Lost foam casting is indeed revolutionizing the casting industry with its unique advantages and capabilities. Here are some ways in which lost foam casting is making a significant impact:
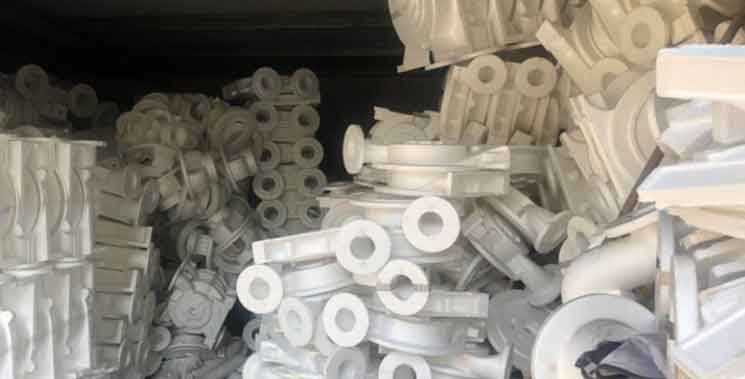
- Design Freedom: Lost foam casting offers exceptional design freedom, allowing the production of highly complex and intricate components. The foam patterns used in the process can be easily shaped and manipulated, enabling the creation of intricate details, undercuts, and complex geometries that are challenging to achieve with other casting methods. This design freedom opens up new possibilities for innovative product designs and enables the manufacturing of components with unique features.
- Near-Net Shape Casting: Lost foam casting produces near-net shape components, reducing the need for extensive post-casting machining or finishing operations. The foam pattern accurately replicates the final shape of the component, minimizing material wastage and saving time and cost associated with material removal. This near-net shape capability improves efficiency and reduces production costs, making lost foam casting an attractive option for cost-conscious industries.
- Complex and Integrated Components: Lost foam casting enables the production of components with complex internal geometries and integrated features. By eliminating the need for cores and parting lines, lost foam casting allows for the creation of seamless components with integrated channels, passageways, and internal structures. This capability is particularly beneficial in industries such as automotive and aerospace, where components with optimized cooling systems, intricate fluid passages, and integrated functionality are in high demand.
- Reduced Manufacturing Steps: Lost foam casting simplifies the casting process by eliminating the need for core-making and core removal steps. This reduces the number of manufacturing steps and eliminates the associated time, cost, and labor required for core-related operations. The simplified process streamlines production and improves overall efficiency.
- Material Flexibility: Lost foam casting can be performed with a wide range of materials, including various metals and alloys. This flexibility allows manufacturers to choose the most suitable material for their specific application, considering factors such as strength, durability, corrosion resistance, and heat resistance. The ability to use different materials further expands the application possibilities of lost foam casting across various industries.
- Reduced Tooling Costs: Lost foam casting offers lower tooling costs compared to traditional casting methods. The foam patterns used in the process can be produced using low-cost molds or even 3D printing techniques. This eliminates the need for complex and expensive molds and cores, making lost foam casting more accessible and cost-effective, particularly for small to medium-scale production runs and prototypes.
- Environmental Sustainability: Lost foam casting is considered a relatively environmentally friendly casting method. The foam patterns used in the process can be recycled or even reused, minimizing waste generation. Additionally, the elimination of cores and the reduced need for binders contribute to lower emissions and environmental impact compared to traditional casting methods.
Lost foam casting is gaining popularity and finding applications in industries such as automotive, aerospace, machinery, and art, where complex designs, integrated components, and near-net shape casting are essential. With its ability to revolutionize the casting process and offer unique advantages, lost foam casting is driving innovation and pushing the boundaries of what is possible in the casting industry.