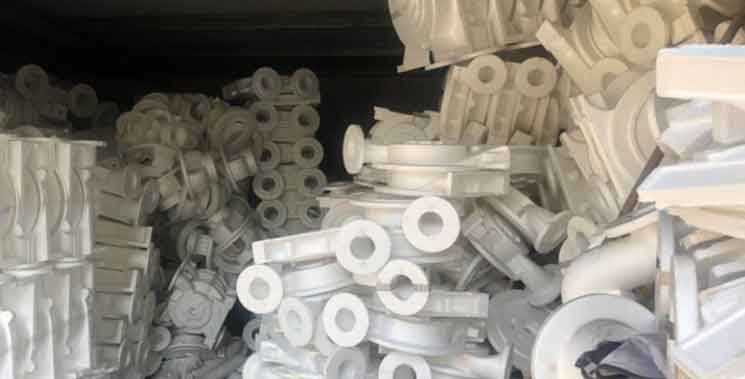
Lost foam casting is a metal fabrication process that offers exceptional design freedom and precision in creating complex metal components. Also known as evaporative pattern casting, this technique utilizes a foam pattern that evaporates when molten metal is poured into the mold, leaving behind a cavity that forms the desired shape of the final product. Let’s explore how lost foam casting unleashes design freedom and precision:
1. Complex Geometries:
Lost foam casting enables the production of intricate and highly complex geometries that may be challenging or even impossible to achieve with other casting methods. The foam patterns can be easily shaped and molded, allowing for intricate details, undercuts, thin walls, and internal features, without the need for separate cores or additional assembly operations.
2. Design Versatility:
With lost foam casting, designers have the freedom to create intricate and innovative designs without the limitations imposed by traditional casting processes. The flexibility of foam patterns allows for the production of components with curved surfaces, intricate textures, and complex shapes, opening up new possibilities for creative and functional designs.
3. Near-Net Shape Casting:
Lost foam casting enables the production of near-net shape components, which require minimal post-casting machining or finishing operations. The foam pattern accurately replicates the desired shape, reducing the need for extensive material removal and machining, resulting in cost and time savings.
4. Dimensional Accuracy:
Lost foam casting offers high dimensional accuracy and repeatability. The foam patterns can be precisely engineered to the desired dimensions, ensuring that the final castings match the intended specifications. This accuracy minimizes the need for post-casting machining or corrective operations, reducing costs and improving overall efficiency.
5. Weight Reduction:
The design flexibility of lost foam casting allows for the production of lightweight components. By creating hollow sections or using foam patterns with internal channels, weight can be significantly reduced while maintaining structural integrity. This makes lost foam casting an attractive option for applications where weight reduction is essential, such as automotive, aerospace, and consumer electronics industries.
6. Material Variety:
Lost foam casting is compatible with a wide range of metal alloys, including aluminum, iron, steel, and their respective alloys. This versatility allows manufacturers to choose the most suitable material for the specific application, considering factors such as strength, corrosion resistance, and thermal properties.
7. Reduced Tooling Costs:
Lost foam casting can offer cost advantages compared to traditional casting methods. Since foam patterns are relatively simple and inexpensive to produce, tooling costs can be lower, especially for smaller production runs or prototype development. This makes lost foam casting a cost-effective option for manufacturers seeking precision and design freedom.
8. Environmentally Friendly:
Lost foam casting can be considered environmentally friendly due to the reduced material waste and energy consumption. The foam patterns used in the process can be recycled and reused, minimizing waste generation. Additionally, the absence of binders or coatings in the pattern reduces the environmental impact associated with other casting methods.
Lost foam casting has revolutionized metal fabrication by unleashing design freedom and precision. Its ability to produce complex shapes, achieve high dimensional accuracy, and offer near-net shape components contributes to increased efficiency, reduced costs, and expanded design possibilities in various industries.