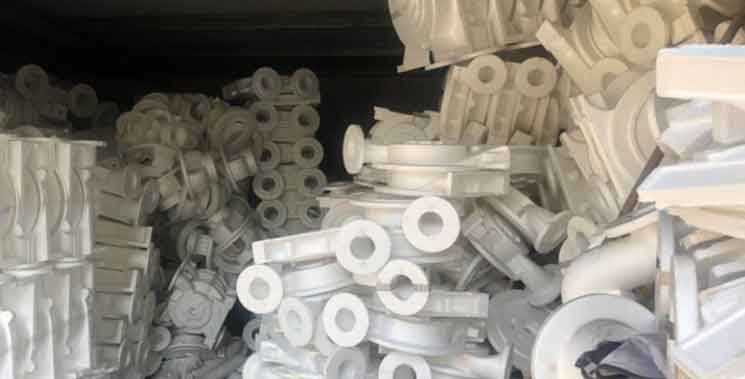
Lost foam casting, also known as evaporative pattern casting, is a modern and innovative casting technique that has unlocked significant potential in the manufacturing industry. It offers several advantages over traditional casting methods and has gained popularity in various applications, ranging from automotive to aerospace industries. Let’s explore the process, benefits, and applications of lost foam casting.
Lost foam casting involves creating a foam pattern in the shape of the desired final product. This foam pattern is then coated with a refractory material to create a shell. The coated pattern is embedded in a casting flask, and molten metal is poured into the flask, causing the foam pattern to vaporize. The vaporized foam creates a void that is filled by the molten metal, resulting in a solid metal casting with intricate details.
One of the primary advantages of lost foam casting is its ability to produce complex and intricate designs with high accuracy. The foam patterns can be easily shaped and manipulated to achieve intricate geometries and fine details that would be challenging or even impossible with traditional casting methods. This technique allows for the creation of complex internal features, undercuts, and thin-walled sections without the need for additional cores or complex tooling.
Another benefit of lost foam casting is the elimination of parting lines and draft angles that are common in other casting methods. Since the foam pattern is vaporized during the process, there are no seams or joints in the final casting. This results in a smooth and seamless surface finish, reducing the need for additional machining or finishing operations.
Lost foam casting also offers improved material utilization and cost efficiency. The foam patterns are made from expanded polystyrene (EPS) or similar materials, which are relatively inexpensive. These patterns can be easily molded, duplicated, and replaced if necessary. Additionally, the absence of cores and the elimination of core removal operations reduce material waste and labor costs associated with core production and removal.
The versatility of lost foam casting extends to a wide range of materials. It can be used with various metals, including aluminum, iron, steel, and even exotic alloys. This flexibility makes it suitable for diverse industries, such as automotive, aerospace, marine, and energy sectors.
In the automotive industry, lost foam casting has found applications in the production of engine blocks, cylinder heads, intake manifolds, and other components. The ability to integrate complex features and reduce weight while maintaining structural integrity makes it an ideal choice for lightweight automotive designs.
In the aerospace industry, lost foam casting is utilized for manufacturing turbine blades, vanes, and other critical components. The technique allows for the creation of intricate cooling passages and advanced airfoil designs that enhance engine performance.
Lost foam casting is also gaining popularity in the art and sculpture industry, as it enables the production of complex and detailed metal artworks.
Despite its advantages, lost foam casting does have some limitations. It requires careful control of the casting process parameters, such as pouring temperature, cooling rate, and mold density, to ensure successful castings. The use of refractory coatings and the potential for gas and vapor entrapment during the casting process also pose challenges that need to be addressed.
Lost foam casting is a modern casting technique that has unlocked tremendous potential in terms of design freedom, accuracy, and cost efficiency. Its ability to produce complex geometries, eliminate parting lines, and reduce the need for additional machining make it an attractive choice for various industries. With ongoing advancements in materials and process control, lost foam casting is likely to continue pushing the boundaries of what is possible in the world of casting.