1. Selection of casting method
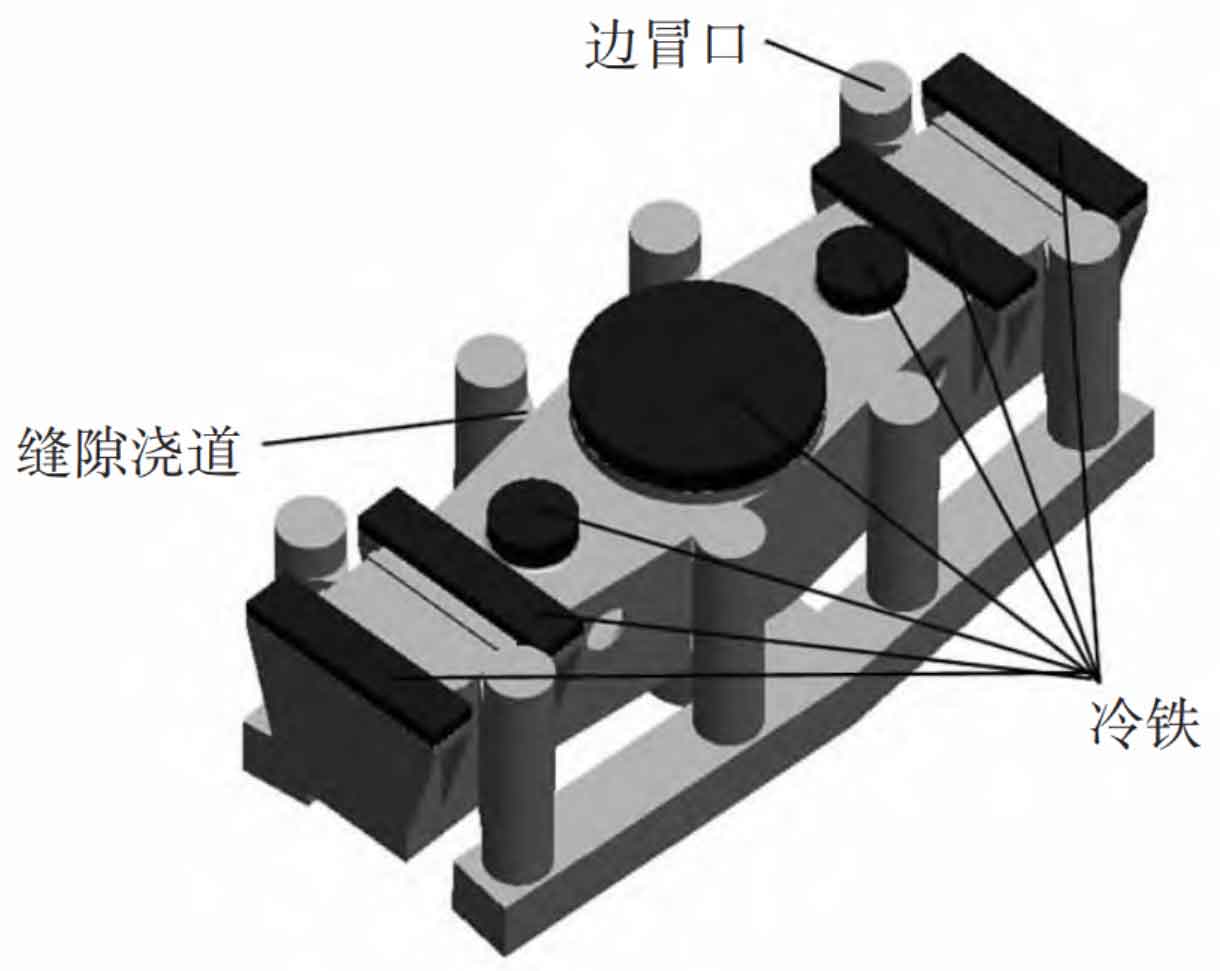
The wall thickness of the casting is thin, the flow resistance of the molten metal is large, and it is difficult to fill the mold. For the thin-walled parts with uniform wall thickness, the temperature difference between the molten metal and the cavity is small, so it is impossible to establish an effective temperature gradient, and it is not easy to realize sequential solidification. Low pressure casting is characterized by stable mold filling through controllable mold filling pressure and time. It has good formability and is conducive to the formation of castings with clear outline and smooth surface, and is more conducive to the formation of large thin-wall castings. Considering the complex structure of the inner cavity of the part, in order to ensure sufficient feeding time before solidification of molten aluminum, low-pressure sand casting is selected. The gate is designed as a gap sprue, which is fed through the side riser, and the cold iron is used to chill the thicker position with machining allowance, so as to realize local sequential solidification and realize overall simultaneous solidification. Figure 1 shows the casting process plan.
2. Numerical simulation analysis of casting process scheme
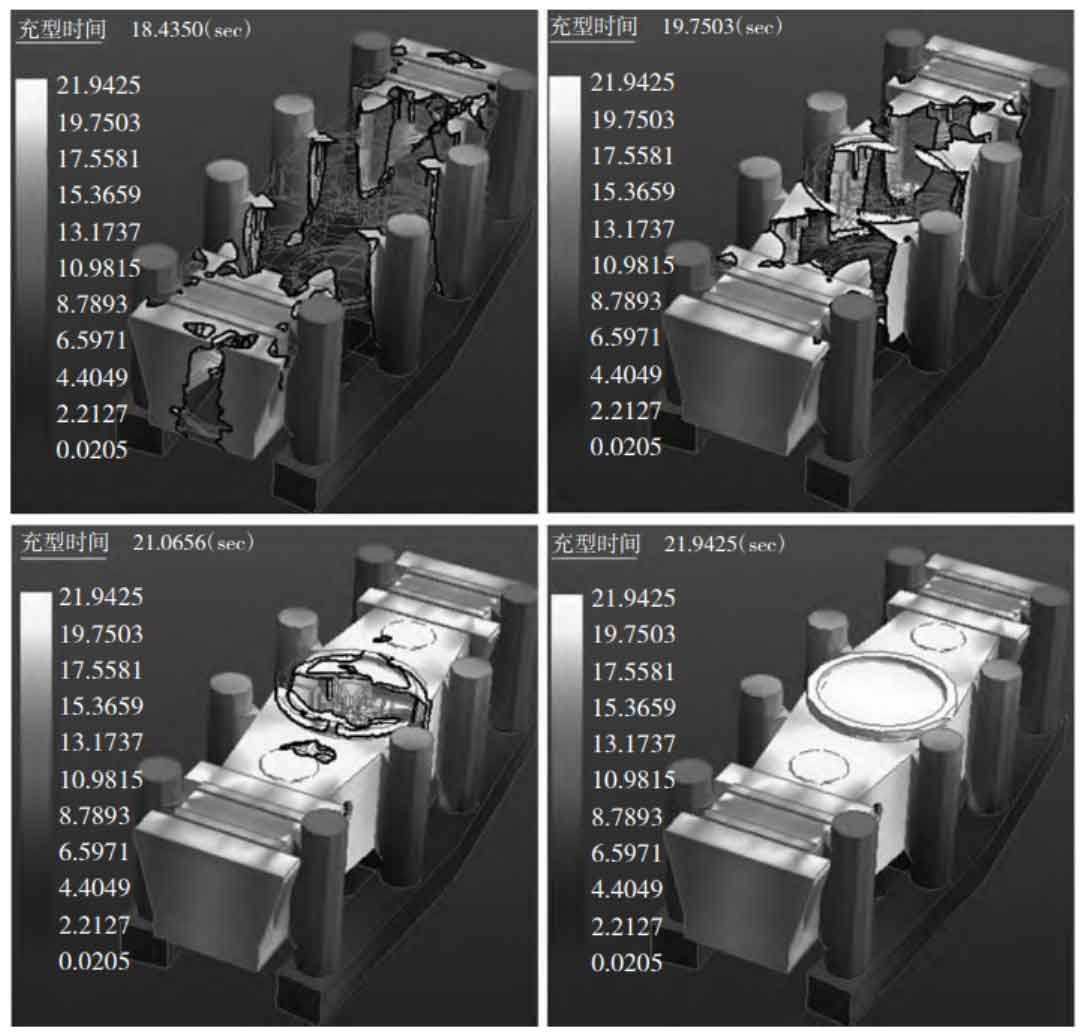
The final simulation results are shown in Figure 2. It can be seen from the filling simulation results that the molten metal enters the mold cavity smoothly through the gap sprue, and no vortex entrainment phenomenon is found. It can be observed from the solidification simulation results that the solidification sequence of the casting is ideal, the part of the casting away from the gap between the sprue and riser solidifies first, and the upper and lower parts of the casting solidify at the same time; The solidification of the area near each gap runner of the casting is later than that of the middle part of the gap runner, the gap runner is later than that of the casting body, and the solidification of the riser and lower transverse runner is later than that of the gap runner. The overall temperature distribution and feeding sequence of the casting are basically reasonable, and the casting is in a good state of overall simultaneous solidification and local sequential solidification.
3. Production verification
During the production first article verification and X-ray flaw detection, it is found that the casting has slag inclusion and insufficient pouring. The main influencing factors are analyzed and the solutions are put forward as follows.
The slag inclusion is uniformly diffused and distributed. The main reason is that the quality of molten aluminum is unqualified. First, control the use amount of returned material, and the general standard is not more than 30%; Secondly, degassing and slag removing refining treatment shall be carried out for the aluminum liquid. After the completion, spectral analysis and density detection shall be carried out in time. After passing the detection, the aluminum liquid shall be used in a short time to prevent the quality of the aluminum liquid from declining after a long time of storage. Generally, it is required not to exceed 1h in actual production. Under the condition of ensuring the quality of molten aluminum, the pouring temperature of molten aluminum should be increased as much as possible. The pouring temperature range of thin-walled castings discussed in this paper is 725~735 ℃.
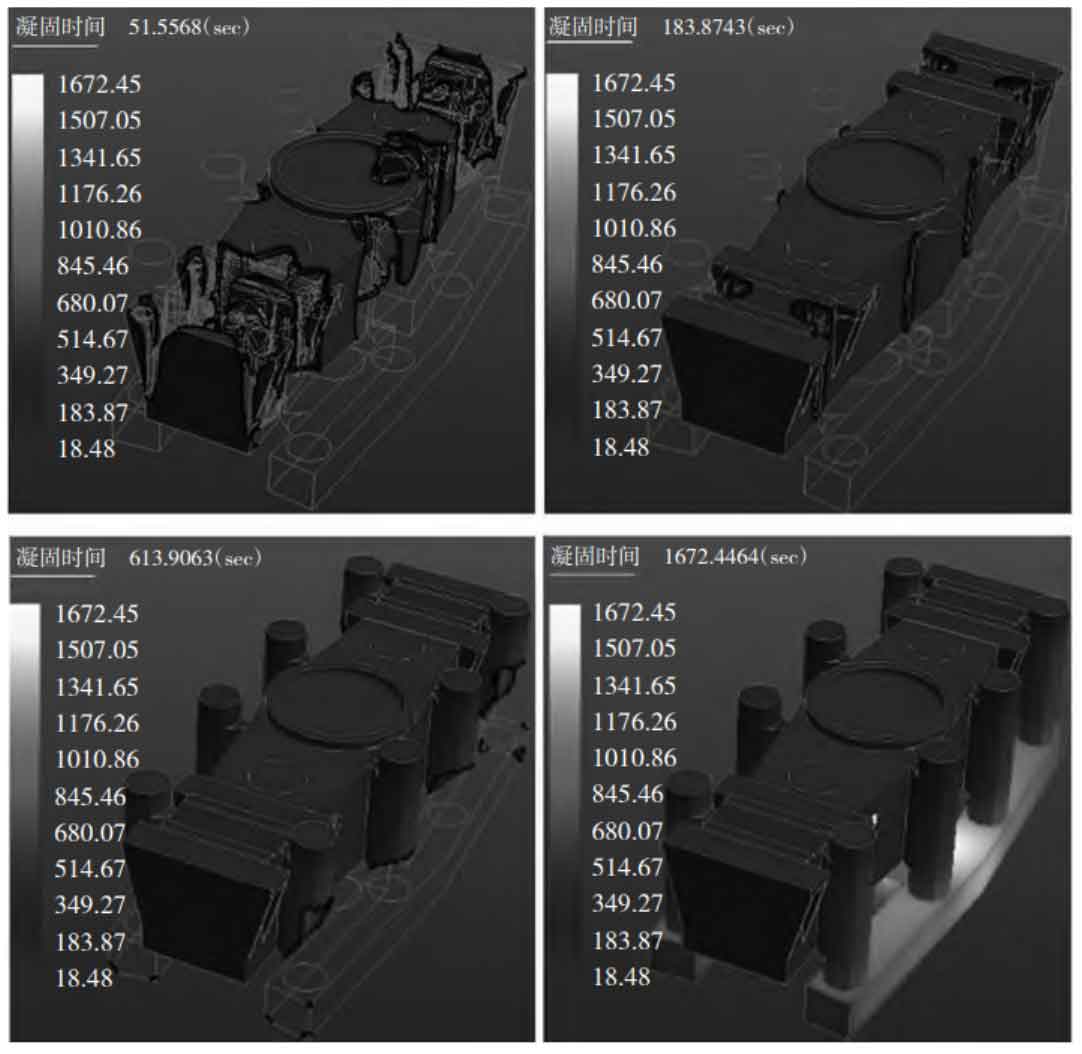
After adjustment and small batch verification, the casting defect position has been qualified, as shown in Figure 4.
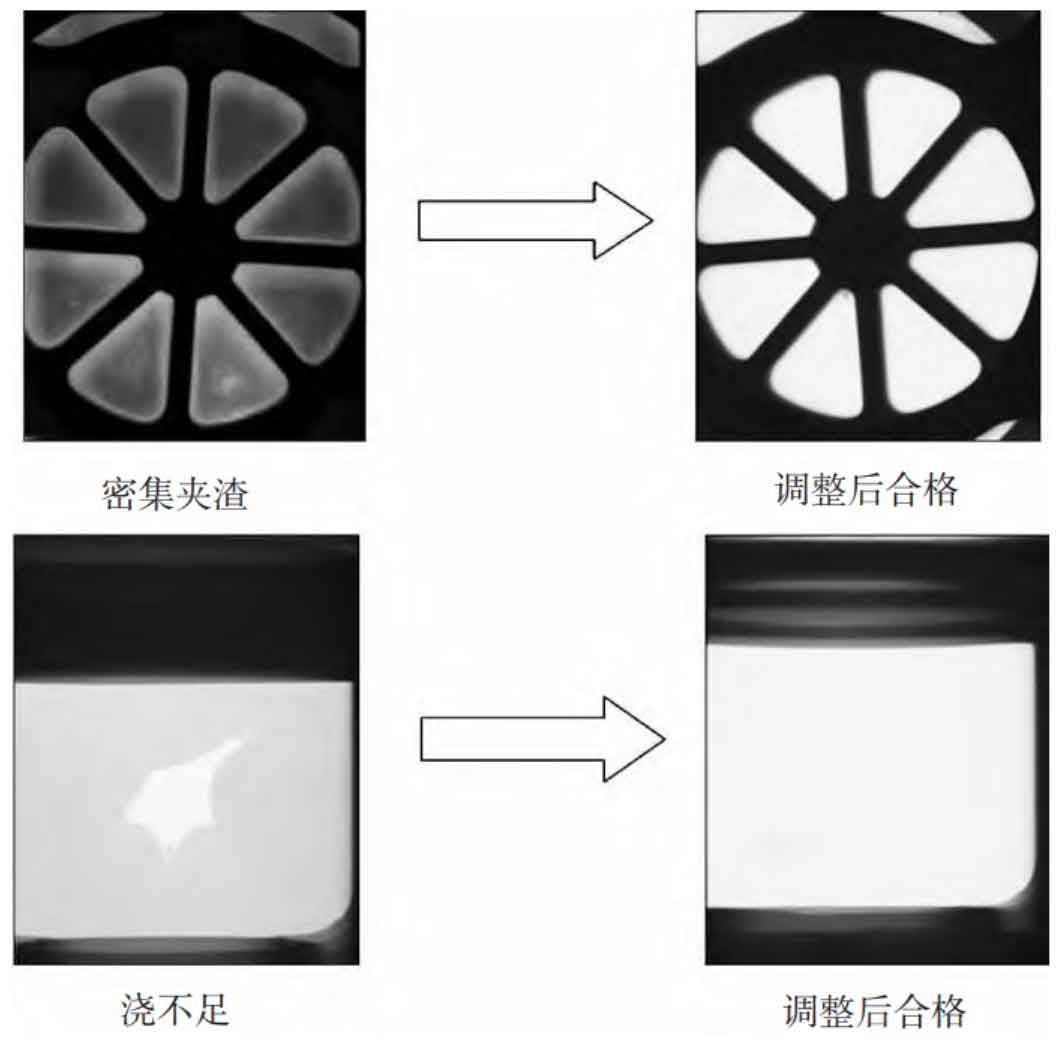