Grey cast iron is a widely used material in the casting industry, valued for its excellent castability, thermal conductivity, and damping properties. However, its machinability presents several challenges that must be addressed to optimize manufacturing processes and product quality. This article explores the machinability of grey cast iron, identifying key challenges and presenting solutions that enhance its performance in casting engineering.
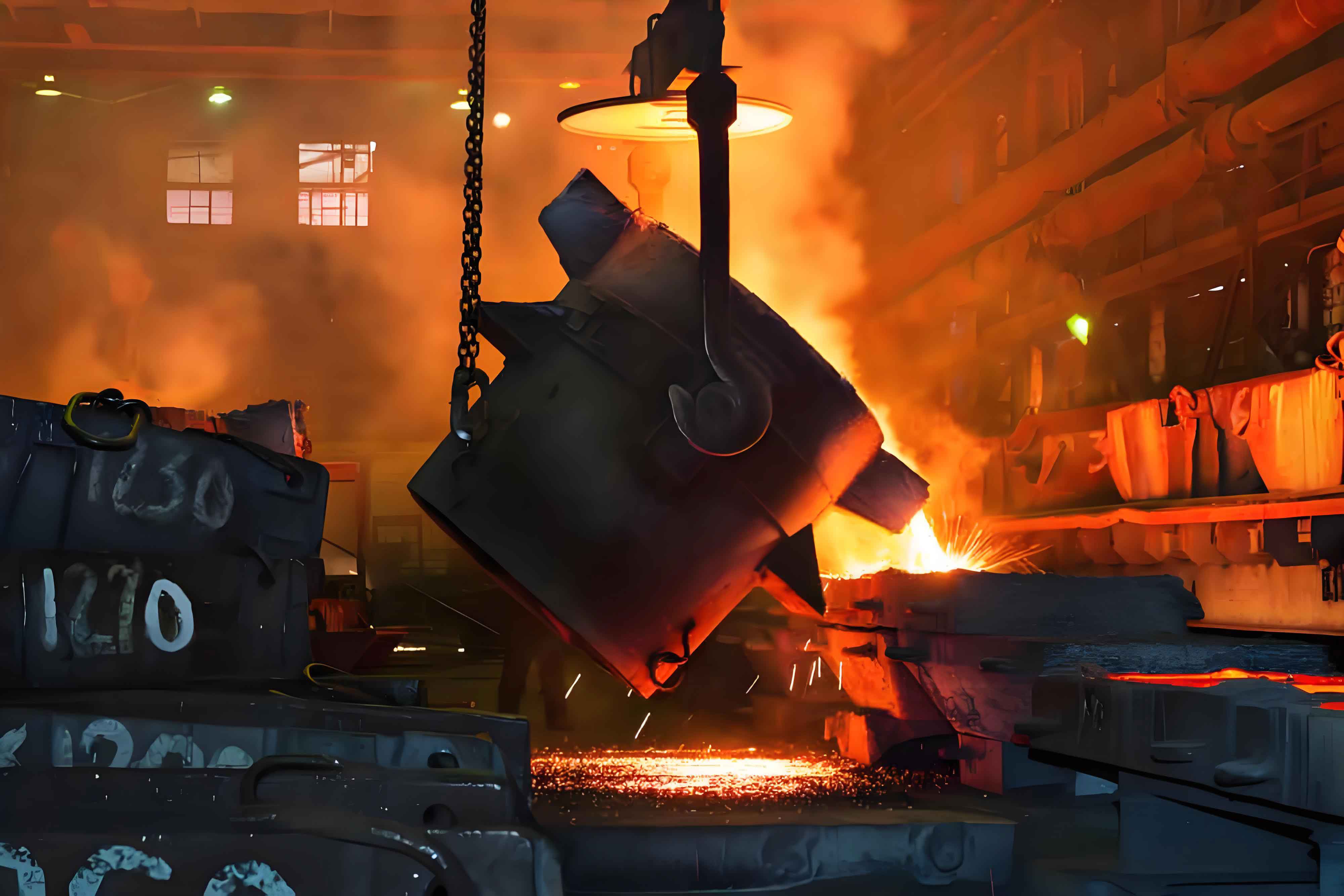
Introduction
Grey cast iron, characterized by its graphite flake microstructure, is a material of choice for various industrial applications. Despite its favorable properties, machinability remains a critical factor influencing its overall utility. Machinability refers to the ease with which a material can be cut, shaped, or finished using machine tools. This article examines the machinability of grey cast iron, explores the associated challenges, and discusses solutions that can improve machining efficiency and quality.
Understanding Machinability in Grey Cast Iron
Machinability encompasses several aspects, including tool wear, surface finish, cutting forces, and material removal rates. The unique microstructure of grey cast iron, with its graphite flakes dispersed in a ferrite or pearlite matrix, impacts these factors in various ways:
- Tool Wear:
- Graphite flakes act as lubricants, reducing tool wear, but the presence of hard carbides can accelerate wear on cutting tools.
- Surface Finish:
- The lubricating effect of graphite improves surface finish, but inconsistent microstructure can lead to variability.
- Cutting Forces:
- Grey cast iron typically requires lower cutting forces due to the presence of graphite, which acts as a chip breaker.
- Material Removal Rates:
- High material removal rates are achievable, but they depend on the specific alloy composition and microstructure.
Comparative Table of Machinability Factors
Machinability Factor | Description | Impact on Machinability |
---|---|---|
Tool Wear | Graphite reduces wear; carbides increase wear | Mixed impact: reduced wear overall but variable |
Surface Finish | Graphite improves finish; inconsistent microstructure affects quality | Generally good finish, potential variability |
Cutting Forces | Lower due to graphite acting as chip breaker | Easier machining with lower forces required |
Material Removal Rates | Dependent on alloy and microstructure | High rates achievable with proper parameters |
Challenges in Machining Grey Cast Iron
- Inconsistent Microstructure:
- Variability in graphite flake size and distribution can lead to inconsistent machining performance and surface quality.
- Tool Wear:
- Despite the lubricating effect of graphite, the presence of hard carbides can cause rapid tool wear, requiring frequent tool changes and increasing costs.
- Heat Generation:
- High-speed machining can generate significant heat, leading to thermal distortion and affecting dimensional accuracy.
- Chip Formation:
- Grey cast iron tends to produce short, brittle chips that can be difficult to manage and remove from the machining area.
Solutions for Enhancing Machinability
- Optimized Alloy Composition:
- Adjusting the composition of grey cast iron to control the size and distribution of graphite flakes and carbides can improve consistency and machinability.
- Advanced Cutting Tools:
- Using cutting tools made from materials such as carbide or ceramic, which are resistant to wear and can withstand high temperatures, can enhance tool life and performance.
- Coolant and Lubrication:
- Employing effective coolant and lubrication systems can reduce heat generation, minimize thermal distortion, and improve surface finish.
- Machining Parameters:
- Optimizing machining parameters, including cutting speed, feed rate, and depth of cut, can help balance material removal rates with tool life and surface quality.
- Surface Treatments:
- Applying surface treatments such as heat treatment or coating can enhance the hardness and wear resistance of grey cast iron, improving its machinability.
Case Studies and Applications
- Automotive Engine Blocks:
- Challenge: Inconsistent surface finish and tool wear during high-speed machining.
- Solution: Use of optimized alloy composition and advanced cutting tools with appropriate coolant systems.
- Outcome: Improved surface finish, reduced tool wear, and enhanced production efficiency.
- Industrial Machinery Components:
- Challenge: Rapid tool wear and heat generation affecting dimensional accuracy.
- Solution: Implementation of ceramic cutting tools and optimized machining parameters.
- Outcome: Extended tool life, better dimensional accuracy, and reduced production costs.
- Brake Discs:
- Challenge: Managing short, brittle chips and achieving consistent material removal rates.
- Solution: Use of advanced chip management systems and tailored cutting speeds.
- Outcome: Improved chip control, consistent material removal, and enhanced surface quality.
Future Trends and Research
- Nanotechnology:
- Research into the incorporation of nanoparticles in grey cast iron alloys aims to enhance its mechanical properties and machinability.
- Additive Manufacturing:
- The development of additive manufacturing techniques for grey cast iron could revolutionize its production, allowing for complex geometries and improved material properties.
- Smart Machining Technologies:
- Integration of smart sensors and real-time monitoring systems in machining processes can provide valuable data for optimizing machining parameters and improving quality control.
- Sustainable Machining Practices:
- Adoption of sustainable machining practices, including the use of biodegradable coolants and energy-efficient equipment, can reduce the environmental impact of machining grey cast iron.
Conclusion
The machinability of grey cast iron presents several challenges that can impact manufacturing efficiency and product quality. However, by understanding the key factors influencing machinability and implementing appropriate solutions, these challenges can be effectively managed. Optimizing alloy composition, using advanced cutting tools, and employing effective coolant and lubrication systems are critical strategies for enhancing the machinability of grey cast iron. As research and technology continue to advance, the future of machining grey cast iron looks promising, with potential for significant improvements in efficiency, quality, and sustainability.