1. Introduction
In the field of modern manufacturing, the production of high-quality castings is crucial for various industries. The large stainless steel volute casting is a key component in many applications, such as in certain industrial equipment and machinery. This article focuses on the process design and optimization of such castings to ensure their quality and performance.
1.1 Background
The demand for stainless steel volute castings has been increasing due to their excellent corrosion resistance and mechanical properties. However, the casting process of these complex structures faces many challenges, such as ensuring proper filling, preventing defects like cracks, porosity, and shrinkage, and achieving the required dimensional accuracy and surface finish.
1.2 Objectives
The main objectives of this study are to design an efficient casting process for large stainless steel volute castings, optimize the process parameters to minimize defects, and produce castings that meet the design requirements in terms of mechanical properties, dimensional accuracy, and surface quality.
2. Product Description
2.1 Material and Composition
The large stainless steel volute casting is made of ZG12Cr18Ni9Ti. The chemical composition is carefully controlled to meet the specific requirements of the application. The following table shows the comparison between the sampled composition, the standard (JB/T6405 – 2018), and the internal control limits:
Category | C | Si | Mn | P | S | Cr | Ni | Ti | N |
---|---|---|---|---|---|---|---|---|---|
Sampled Composition | 0.05 | 0.69 | 1.29 | 0.021 | 0.023 | 17.98 | 8.15 | 0.25 | 0.016 |
JB/T6405 – 2018 | ≤0.12 | ≤1.50 | 0.80 ~ 2.00 | 0.03 | ≤0.04 | 17.0 ~ 20.0 | 8.00 ~ 11.00 | 5(C) – 0.03] – 0.80 | |
Internal Control | 0.06 | 0.50 – 0.80 | 1.20 ~ 1.50 | 0.025 | ≤0.025 | 17.8 – 18.5 | 8.10 – 8.20 | 0.20 – 0.35 | ≤0.02 |
2.2 Dimensions and Structure
The casting has a maximum size of 3800 mm and a wall thickness ranging from 20 mm to 30 mm (with some parts having a thickness of 200 mm). It has a complex structure with a 隔断 that forms a heat – affected zone when connected to the upper and lower end faces. The overall structure is such that it is prone to deformation and casting defects when cast as a whole due to the non – uniform wall thickness and complex geometry.
3. Production Process
3.1 Mold Design
3.1.1 General Design
The mold design takes into account the symmetry of the casting’s upper and lower structures and the presence of local control valve flanges and mounting bosses. These parts are made into movable blocks, allowing a single wooden model board to be used for shaping both the upper and lower sand boxes. The sand type used is steel 3 mm with a certain proportion of additives (2.5% and 1.0%) and a thickness of 15 mm. The sand core, estimated to be about 3t based on the density of the 宝珠砂 (2.0 g/cm³), has a symmetric center plane as the parting surface, with sawdust and straw ropes added in the middle to increase the yieldability.
3.1.2 Core Structure
Due to the large span size of the sand core, a core bone structure reinforced by welded steel bars is designed to prevent deformation and drifting during the pouring process. This core bone structure provides additional support to the sand core, ensuring its stability during casting.
3.2 Casting Process Design
3.2.1 Pouring System Design
- Double Ladle Pouring: To shorten the pouring and filling time and reduce defects such as slag and porosity in large thin – walled castings, a double ladle pouring method is adopted. This allows for a more efficient transfer of molten metal into the mold.
- Ceramic Tube for Pouring Channels: To prevent sand from being flushed into the casting during pouring, ceramic tubes are used to arrange the pouring channels. This helps to maintain the integrity of the casting and reduces the risk of inclusions.
- Section Ratio of Pouring System: The pouring system is designed as an open system with a section ratio of ∑S₁ : ∑S₂ : ∑S₃ = 2 : 3 : 4 for the various units. This ratio is determined based on the characteristics of the molten steel and the requirements for proper filling and solidification.
- Inlet and Outlet Design: There are two schemes for the design of the inlet and outlet of the pouring system. Scheme 1 involves using ϕ120 mm and ϕ90 mm pipes, while Scheme 2 uses a 1/2 trapezoidal internal pouring channel. These designs aim to ensure good filling and reduce the temperature difference at the bottom of the casting.
3.2.2 Process Simulation and Optimization
- Simulation Parameters: The CAE software is used for numerical simulation of the casting and solidification process. The cast type material is selected as resin sand, with a heat transfer coefficient between the casting and the sand box of 700 W/(m²·K). The pouring temperature is set at 1600℃, and the initial sand type temperature is 20℃. The heat transfer conditions at the interface are considered to be convection and radiation, along with the permeability of the sand type.
- Defect Analysis: Through simulation, the distribution of solid phase rate field during solidification and the location of shrinkage defects are analyzed for both Scheme 1 and Scheme 2. For example, in Scheme 1, certain defects are observed in the 6 – 9 regions, while in Scheme 2, the defects are analyzed in the 10 – 13 regions. Based on these results, the process is optimized to eliminate or reduce defects.
- Optimization Measures: To optimize the process, measures such as increasing the feeding ability of the riser, adding local external and internal cold irons, and arranging chromium ore sand are taken. These measures help to increase the density of the casting, prevent cracks and shrinkage holes, and improve the overall quality of the casting.
3.3 Steel Melting and Composition Control
- Melting Process: The steel melting process involves using 2 – 3 min for melting and then immediately pouring. The temperature of the molten steel is controlled between 1590 – 1620℃, and the pouring is carried out after 48 h of holding. During melting, the addition ratio of stainless steel pouring and riser return materials is controlled to reduce the nitrogen content in the molten steel.
- Composition Control: When melting titanium – containing stainless steel, due to the reactivity of titanium, the yield rate is 40% – 50%. To prevent defects such as slag formation on the surface of TiN, the addition proportion of stainless steel pouring and riser return materials is reduced, and prior to adding titanium iron, silicon iron and manganese – silicon – calcium are used for deoxidation.
4. Production Verification
4.1 Casting Quality Inspection
The castings are produced using the alkali phenolic resin 宝珠砂 for molding and core making. The pouring temperature of the mold sand is set between 1600 – 1610℃. After the casting is formed, the pouring and riser are removed. Through inspection, it is found that there are no cracks, pores, shrinkage holes, or slag inclusions inside the casting that affect the product quality.
4.2 Mechanical Property Testing
Tensile specimens are taken from the test bars along with the furnace to test their mechanical properties. The measured tensile strength is 490 MPa, and the yield strength is 215 MPa. The elongation percentage is between 28% – 35%. These results indicate that the casting process is effective and can meet the requirements for mass production.
5. Conclusion
In conclusion, through the design of an open pouring system, the use of ceramic tubes for pouring channels, and the optimization of process parameters such as risers, cold irons, chromium ore sand, pouring temperature, and filling speed, it is possible to produce large stainless steel volute castings with complete shapes and qualities that meet the design requirements. This study provides a valuable reference for the production of similar castings in the future, enabling manufacturers to improve their casting processes and produce high – quality products more efficiently.
6. Importance of Process Optimization in Stainless Steel Volute Casting
6.1 Impact on Quality
The optimization of the casting process has a direct and significant impact on the quality of the stainless steel volute casting. By carefully controlling parameters such as the pouring system, temperature, and use of additives like cold irons and chromium ore sand, defects such as porosity, cracks, and shrinkage can be minimized. This results in a casting with better mechanical properties, dimensional accuracy, and surface finish. For example, the proper design of the pouring system ensures a smooth and complete filling of the mold, reducing the likelihood of air pockets and inclusions. The use of cold irons helps to control the solidification rate, preventing the formation of shrinkage cavities.
6.2 Cost and Efficiency Considerations
Process optimization also plays a crucial role in cost reduction and improving production efficiency. By reducing the occurrence of defects, the amount of rework and scrap is decreased, saving both material and labor costs. Additionally, an optimized process allows for a faster production cycle. For instance, a well-designed pouring system can shorten the pouring and filling time, enabling more castings to be produced in a given time period. This not only increases productivity but also reduces the overall production cost per unit.
7. Future Trends in Stainless Steel Volute Casting
7.1 Advanced Simulation and Modeling Techniques
With the continuous development of computer technology, more advanced simulation and modeling techniques are expected to be applied in the casting process of stainless steel volute castings. These techniques will enable more accurate prediction of casting defects and optimization of process parameters. For example, finite element analysis (FEA) and computational fluid dynamics (CFD) can be used to simulate the flow of molten metal and the heat transfer during solidification in more detail. This will allow manufacturers to make more informed decisions and further improve the quality of the castings.
7.2 Use of New Materials and Additives
The exploration and use of new materials and additives is another trend in the future of stainless steel volute casting. For example, the development of new types of refractory materials with higher temperature resistance and better mechanical properties can improve the performance of the mold. Additionally, the use of nano-sized additives may enhance the microstructure of the casting, resulting in improved mechanical properties. These new materials and additives have the potential to further optimize the casting process and improve the quality of the final product.
7.3 Automation and Industry 4.0 Integration
Automation and integration with Industry 4.0 concepts are becoming increasingly important in the manufacturing industry, including the casting of stainless steel volute castings. Automated pouring systems, robotic handling of molds and castings, and real-time monitoring of the casting process using sensors are some of the applications that can be expected in the future. This will not only improve production efficiency but also ensure more consistent quality control. For example, sensors can monitor the temperature and pressure during the casting process and provide real-time feedback for adjustment, reducing the risk of defects.
8. Case Studies of Successful Stainless Steel Volute Casting Projects
8.1 Case Study 1: A Large Industrial Equipment Manufacturer
A large industrial equipment manufacturer was facing challenges in producing high-quality stainless steel volute castings for their critical machinery components. The initial casting process resulted in a high percentage of defective castings due to issues such as porosity and shrinkage. By implementing a comprehensive process optimization strategy, including redesigning the pouring system, using appropriate cold irons, and optimizing the melting process, they were able to significantly reduce the defect rate. The final castings met the required mechanical properties and dimensional accuracy, enabling them to improve the performance of their machinery and gain a competitive edge in the market.
8.2 Case Study 2: A Specialty Casting Company
A specialty casting company was tasked with producing a complex stainless steel volute casting with a unique design. Through the use of advanced simulation techniques to predict and address potential defects, along with careful selection of materials and additives, they were able to produce a high-quality casting that exceeded the client’s expectations. The casting had excellent surface finish and mechanical properties, demonstrating the effectiveness of a well-planned and executed casting process.
9. Challenges and Solutions in Stainless Steel Volute Casting
9.1 Challenges
- Complex Geometry: The complex geometry of the stainless steel volute casting makes it difficult to ensure proper filling of the mold and uniform solidification. This can lead to defects such as porosity and shrinkage in different regions of the casting.
- Material Properties: The properties of stainless steel, such as its high melting point and reactivity of certain elements (e.g., titanium), pose challenges in the melting and casting process. Controlling the composition and ensuring the proper formation of alloys is crucial to avoid defects.
- Quality Control: Maintaining consistent quality control throughout the casting process is a challenge. Small variations in process parameters can lead to significant differences in the quality of the final casting.
9.2 Solutions
- Advanced Design and Simulation Tools: The use of advanced design and simulation tools, such as CAD/CAM and CAE software, can help in designing the mold and predicting potential defects. This allows for early intervention and optimization of the process.
- Process Optimization: As discussed earlier, optimizing process parameters such as pouring temperature, use of cold irons, and addition of chromium ore sand can address many of the quality issues related to the casting.
- Quality Assurance Systems: Implementing a robust quality assurance system, including regular inspection and testing of raw materials, intermediate products, and final castings, can ensure consistent quality control. This system should also include procedures for corrective actions in case of non-compliance.
10. Conclusion
In summary, the casting process of large stainless steel volute castings is a complex but crucial aspect of modern manufacturing. Through process optimization, the use of advanced techniques and materials, and addressing challenges through appropriate solutions, it is possible to produce high-quality castings that meet the requirements of various industries. The future trends in this field, such as advanced simulation, new materials, and automation, offer further opportunities for improvement. By continuously learning from successful case studies and implementing best practices, manufacturers can stay competitive and produce reliable and high-quality stainless steel volute castings.
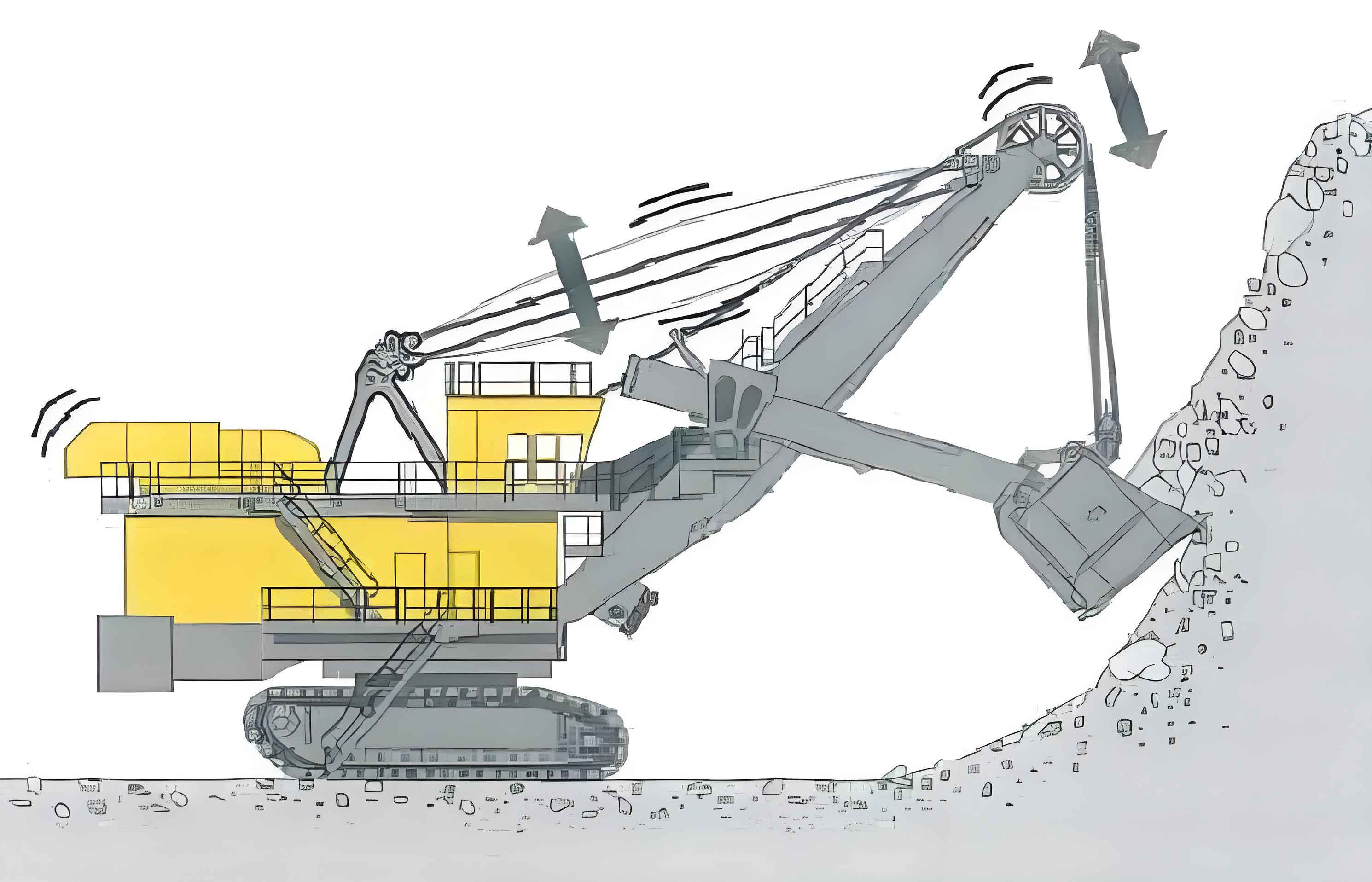