As a metal structural material, the density of magnesium alloy is only 1.74g/cm3, about 2/3 of aluminum and 2/5 of titanium. It has high strength, good casting formability, damping and vibration reduction (30 times higher than aluminum), energy absorption and noise reduction, and strong electromagnetic shielding ability. In recent years, it has ushered in explosive development in the field of aerospace satellites and commercial aerospace. In the aerospace field, magnesium alloy investment castings are mainly used in the cabin frame, seat frame, turboshaft aero-engine casing, aircraft wing skin, etc.; in the aerospace field, they are mainly used in the suction tube, missile cabin section, inner wall plate, electronic instrument and instrument frame, etc. The gearbox housing and cover of some Eurocopter models are made of magnesium alloy investment casting.
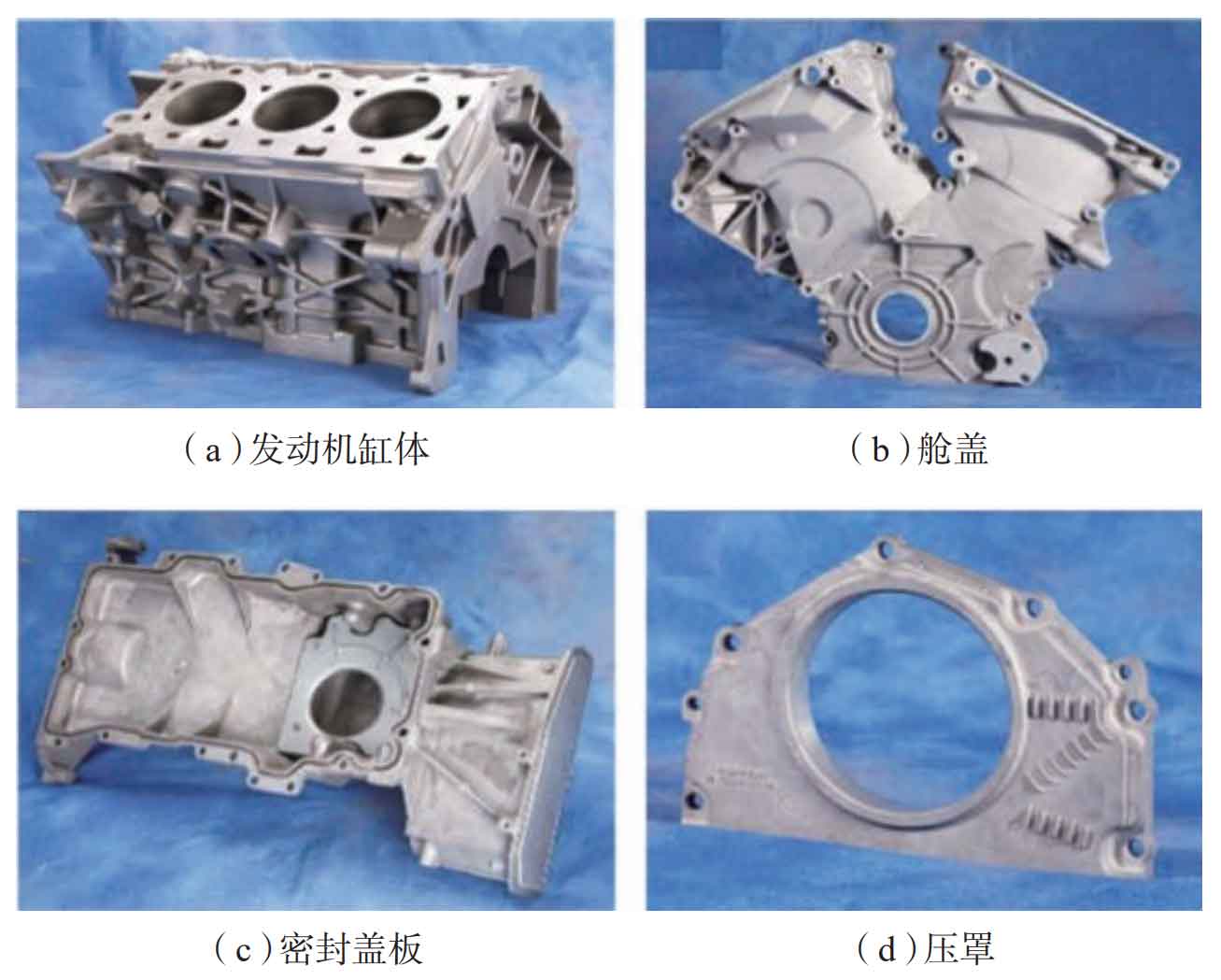
At present, China has formed more than 10 mature commercial rare earth magnesium alloys, which have been widely used in the aerospace field. Among them, the ZM6 magnesium alloy investment casting with Nd element has been applied to the wing rib, slide rail and other structural parts of the fighter series in China. Magnesium alloys can be divided into binary system, ternary system and multicomponent system according to component composition. The commonly used binary system magnesium alloys are mainly Mg – Al, Mg – Zn, Mg – Mn and Mg – Zr. The ternary system magnesium alloys are mostly Mg – Al – Mn and Mg – Al – Si. The common multicomponent system magnesium alloys are Mg – Th – Zn – Zr and Mg – Ag – Th – RE – Zr. Magnesium alloys are more refined by adding Zr elements. According to whether Zr elements are added, they can be divided into magnesium alloys containing Zr, such as Mg – Zn – Zr, Mg – RE – Zr, Mg – Th – Zr and Mg – Ag – Zr. Magnesium alloys without Zr are mostly Mg – Al, Mg – Mn and Mg – Zn. The chemical composition of common cast magnesium alloys.
Die casting is a common production and manufacturing process for magnesium alloy castings at present. When using die casting to manufacture magnesium alloy components with complex shapes, the cost of mold investment is high, the cycle is long, the requirements for equipment and tooling are high, and the parts with complex cavity structure are prone to defects such as shrinkage cavity and insufficient pouring. In contrast, the investment casting process of magnesium alloy is flexible, with high forming dimensional accuracy, high surface finish, and the structural forming dimension can range from a few nanometers to several meters. The figure shows several typical magnesium alloy investment castings.