Chapter 1: Understanding the Fundamentals of Sand Casting

Sand casting is a fundamental and widely-used manufacturing process in metalworking. Here’s a basic overview of its fundamentals:
What is Sand Casting?
- Definition: Sand casting is a process where molten metal is poured into a mold made of sand to form a metal object. Once the metal cools and solidifies, the sand mold is broken away, leaving the metal part.
Key Components of Sand Casting
- Pattern: A model of the final product; it’s used to create the mold cavity.
- Mold: A cavity in the sand that holds the molten metal to form the desired shape. It’s made of two halves: the cope (top half) and the drag (bottom half).
- Core: A sand shape inserted into the mold to create internal cavities of sand casting.
- Molten Metal: Metals like iron, steel, aluminum, or bronze are melted and poured into the mold.
- Flask: The frame that holds the sand mold.
The Sand Casting Process
- Pattern Making: A pattern of the final product is created, often from wood or metal. This pattern is slightly oversized to account for metal shrinkage during cooling.
- Mold Making: The pattern is placed in a flask and packed with specially prepared sand. The sand around the pattern is compacted and shaped, forming the mold cavity that will be filled with the molten metal.
- Core Making (if needed): If sand casting requires internal voids or shapes, a core is made from sand and placed in the mold.
- Molten Metal Pouring: The molten metal is poured into the mold. The metal flows into the cavity and fills the space, taking the shape of the pattern.
- Cooling: The metal is left to cool and solidify. This can take from several minutes to hours, depending on the size and complexity of sand casting.
- Mold Breakaway: After the metal has solidified, the sand mold is broken away from the cast part. This sand can often be recycled and used again.
- Cleaning and Finishing: The sand casting may have excess material (such as the metal from the pouring channel) which is removed. The part may also require sandblasting, grinding, or machining to achieve the final dimensions and surface finish.
Advantages of Sand Casting
- Flexibility in Size and Shape: Can produce parts of virtually any size and shape.
- Cost-effective for Small Batches: Ideal for small to medium production runs due to low tooling costs.
- Material Versatility: Compatible with a wide variety of metals.
Limitations
- Surface Finish and Tolerance: Generally, sand castings have a rougher surface and less precise tolerances than other casting methods.
- Post-casting Processing: Often require additional machining and finishing processes.
Applications
- Sand casting is used in various industries, including automotive, aerospace, machinery, construction, and decorative arts, for making engine parts, machine components, gears, ornaments, and more.
Understanding these fundamentals of sand casting provides insight into its versatility and widespread use in manufacturing a diverse array of metal parts and components.
Chapter 2: Exploring the Basics of Sand Casting
Sand casting is a fascinating and time-honored method of metal casting, widely used for its simplicity and versatility. Here’s a beginner’s guide to understanding the basics of sand casting:
1. Overview of Sand Casting
- Definition: Sand casting involves creating a mold from a sand mixture and pouring molten metal into the mold. Once the metal solidifies, the sand mold is broken apart to reveal the cast metal object.
- History: It’s one of the oldest casting methods, dating back thousands of years.
- Applications: Used for making a wide range of metal objects, from simple household items to complex machinery parts.
2. Materials Required
- Sand: A mixture of silica sand, clay, and water. The sand must be able to retain its shape when molded.
- Metal: Various metals like iron, steel, aluminum, and bronze can be cast using this method.
- Binding Agents: To help the sand hold its shape.
- Melting Furnace: For melting the metal.
- Mold Tools: Including flasks, rammers, and strikers.
3. Process Steps
- Creating the Pattern: The first step is to create a pattern of the object to be cast. This is typically made from wood, plastic, or metal.
- Preparing the Sand Mold: The pattern is placed in a flask and packed with the sand mixture. The sand is compacted around the pattern to form the mold.
- Removing the Pattern: Once the sand is compacted, the pattern is carefully removed, leaving a cavity in the shape of the object.
- Pouring the Metal: Molten metal is poured into the cavity of the sand mold.
- Cooling and Solidification: The metal is left to cool and solidify in the mold.
- Breaking Open the Mold: After the metal has solidified, the sand mold is broken open to remove the casting.
4. Advantages and Limitations
- Advantages:
- Flexibility in size and shape of the castings.
- Cost-effective for small batch production.
- Simplicity of the process.
- Limitations:
- Rough surface finish.
- Limited dimensional accuracy.
- The process can be labor-intensive.
5. Common Problems and Solutions
- Defects in Casting: Such as porosity, shrinkage, and cracks. Solutions include proper design of the casting, controlling the cooling rate, and ensuring the quality of the sand and metal.
- Mold Failure: This can occur if the sand is not properly prepared or compacted. Using the correct mixture and compacting methods can mitigate this.
6. Safety Considerations
- Always wear protective gear, such as gloves and safety glasses.
- Ensure proper ventilation in the casting area.
- Be cautious with hot metals and molten materials.
7. Learning More
- Books and Online Resources: There are many books and online tutorials that can provide further details and advanced techniques.
- Workshops and Classes: Practical hands-on experience can be very beneficial.
Sand casting can be a rewarding hobby or a valuable skill in various professional settings. As with any craft, practice and experience are key to mastering the technique.
Chapter 3: Challenges and Solutions in Modern Sand Casting Technologies
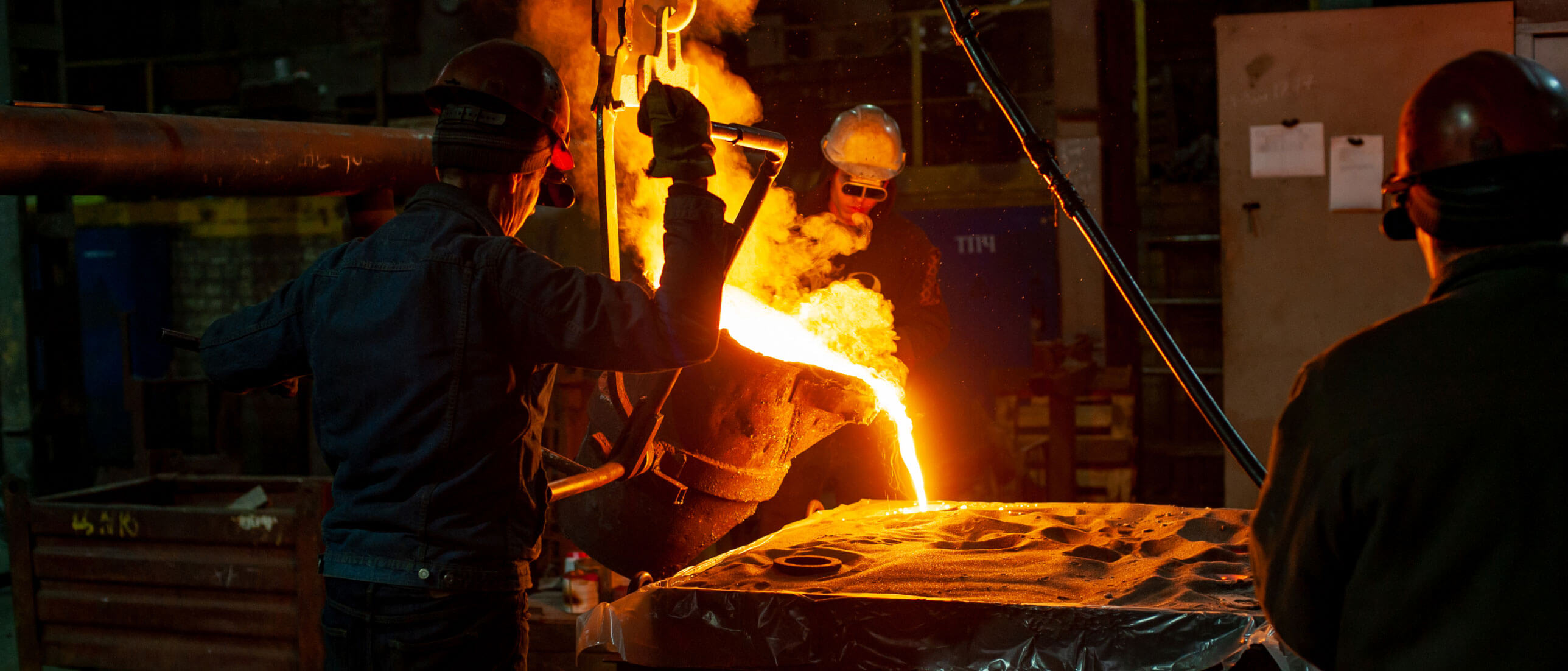
Modern sand casting technologies have evolved to address various challenges inherent in traditional methods. Here’s an overview of these challenges and the innovative solutions being implemented:
Challenges in Modern Sand Casting
- Precision and Accuracy
- Traditional sand casting can struggle with producing parts with tight tolerances or intricate details.
- Surface Finish
- Sand casting typically results in a rougher surface compared to other casting methods, which may not be desirable for some applications.
- Mold Strength and Durability
- The sand mold must be strong enough to withstand the pressure and heat of molten metal without deforming or cracking.
- Environmental Concerns
- Traditional sand casting processes can have significant environmental impacts, including dust production and disposal of used sand.
- Production Efficiency and Cost
- While sand casting is generally cost-effective for small batches, the labor-intensive nature of traditional methods can be a drawback for larger-scale production.
Solutions and Technological Advancements
- Improved Sand Quality and Binders
- Using higher quality sands and innovative binders improves the precision and surface finish of sand casting. Binders that strengthen the sand can also enhance mold stability.
- Computer-Aided Design (CAD) and Manufacturing
- CAD allows for more precise design of molds and patterns. It can be integrated with automated molding machines to increase accuracy and efficiency.
- 3D Printing for Patterns and Molds
- 3D printing technology is increasingly being used to create more accurate and complex patterns and molds. This method also allows for rapid prototyping and production.
- Automated Molding and Core Making Machines
- Automation in molding and core making reduces labor costs and improves consistency in production.
- Environmentally Friendly Practices
- Innovations include the use of biodegradable binders and the recycling of used sand to minimize environmental impact.
- Advanced Metallurgical Techniques
- Using refined melting and pouring techniques and advanced metallurgical analysis can improve the quality of the final product.
- Quality Control and Process Monitoring
- Implementing advanced sensors and monitoring systems helps in detecting and correcting defects early in sand casting process.
Future Directions
- Integration with Industry 4.0
- Further integration of IoT, AI, and data analytics in sand casting processes could lead to smarter, more efficient production lines.
- Sustainable and Green Manufacturing Practices
- Continued focus on reducing the environmental footprint of sand casting, including waste reduction and energy efficiency improvements.
- Customization and Flexibility
- Leveraging technologies like 3D printing for more customizable and flexible manufacturing options.
- Material Innovations
- Exploring new types of sand casting materials that offer improved properties or are more environmentally sustainable.
The modernization of sand casting is part of a broader trend in manufacturing towards greater precision, efficiency, and sustainability. These advancements not only enhance the quality and capabilities of sand casting but also ensure its relevance in the evolving landscape of manufacturing technologies.
Chapter 4: How Sand Casting is Transforming Various Industries
Sand casting, with its unique advantages and recent technological advancements, is significantly impacting various industries. Let’s explore how this transformation is unfolding:
1. Automotive Industry
- Component Manufacturing: Sand casting is extensively used for producing engine blocks, cylinder heads, manifolds, and other large, complex parts.
- Customization and Restoration: It allows for the production of custom parts for vintage cars and specialized vehicles.
- Cost-Effectiveness: Ideal for small to medium batch production, which is common in specialty automotive manufacturing.
2. Aerospace Industry
- Engine and Structural Parts: Key components like engine casings and airframe parts are produced using sand casting due to its ability to create complex geometries and large parts.
- Lightweight Alloys: The process is compatible with lightweight, high-performance alloys crucial in aerospace applications.
3. Construction and Infrastructure
- Heavy Machinery Parts: Components for construction equipment, such as housings and large gears, are often made through sand casting.
- Piping and Manholes: The method is also used for creating large, durable iron pipes and manhole covers.
5. Energy Sector
- Wind and Hydro Power: Components like turbine housings and large-scale transmission parts are typically produced using sand casting.
- Oil and Gas Equipment: The method is used for manufacturing heavy-duty parts that can withstand extreme conditions.
6. Marine Industry
- Ship Components: Parts such as propellers, anchors, and engine components for ships and boats are often made using sand casting.
- Corrosion-Resistant Materials: The process is compatible with corrosion-resistant materials, essential in marine environments.
7. Rail Industry
- Train Parts: From wheels to undercarriage components, sand casting is used to produce various heavy-duty and wear-resistant parts for railways.
8. Medical Equipment
- Surgical Instruments and Implants: Some specialized medical equipment and implants require the precision and customizability offered by sand casting.
9. Electronics and Telecommunications
- Heat Sinks and Chassis: Sand casting is utilized for producing large heat sinks and metal chassis that require good heat dissipation and durability.
10. Defense and Military
- Armament and Vehicle Parts: Essential for producing heavy-duty and bespoke components for military equipment and vehicles.
Future Outlook and Continued Innovation
- Advanced Materials: Ongoing research into new alloys and composite materials is expanding the capabilities of sand casting.
- Sustainability Focus: Efforts to make the process more environmentally friendly are ongoing, including the recycling of sand and the use of greener binders.
- Integration with Digital Technologies: The adoption of 3D printing, AI, and automation is expected to further revolutionize sand casting, improving efficiency and precision.
Sand casting’s adaptability and cost-effectiveness make it a crucial technique in modern manufacturing, impacting numerous industries by providing an optimal balance between quality, flexibility, and cost.
Chapter 5: Advancements in Sand Quality and Its Impact on Sand Casting Efficiency
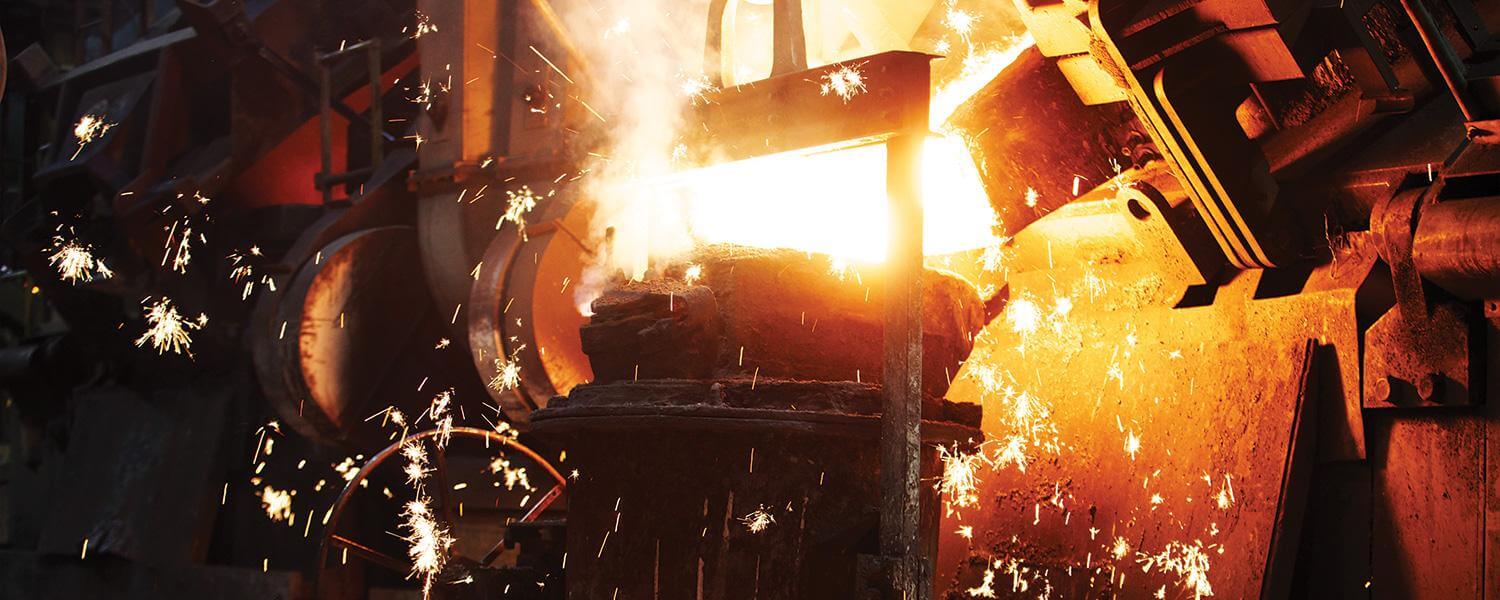
Advancements in sand quality have a profound impact on the efficiency and effectiveness of sand casting processes. High-quality sand can significantly improve the casting’s final outcome, enhancing precision, surface finish, and overall strength. Let’s delve into these advancements and their implications:
Key Advancements in Sand Quality
- Improved Grain Size and Shape Control
- Uniform grain size and shape lead to more predictable molding properties and better surface finish.
- Engineered sand grains offer enhanced moldability and compactibility.
- Advanced Binders
- Newer binder technologies provide stronger molds and cores with better dimensional accuracy.
- Environmentally friendly binders, like organic or water-based options, reduce hazardous emissions.
- Enhanced Sand Additives
- Additives that improve sand’s refractory properties, allowing it to withstand higher temperatures without breaking down.
- Additives that reduce casting defects such as veining or penetration.
- Sand Reclamation Technologies
- Advanced reclamation processes enable the recycling of used sand, reducing costs and environmental impact.
- Improved reclamation quality ensures that reclaimed sand is almost as good as new.
Impact on Sand Casting Efficiency
- Reduced Defects in Castings
- Higher quality sand means fewer casting defects like blowholes, sand fusion, and cold shuts.
- This results in reduced waste and higher yield.
- Improved Surface Finish and Detail
- Finer and more uniform sand grains allow for capturing intricate details in the mold, leading to better surface finishes.
- This can reduce the need for secondary finishing processes.
- Increased Mold Stability and Durability
- Advanced binders and additives enhance mold and core strength, reducing the chances of mold collapse or distortion.
- Stronger molds are especially important for large or complex castings.
- Enhanced Precision and Dimensional Accuracy
- Improved sand quality leads to tighter tolerances and better dimensional control in the final product.
- Essential for industries requiring high precision, such as aerospace and automotive.
- Cost Efficiency
- The ability to recycle sand effectively reduces raw material costs.
- Reduction in casting defects and secondary processing also contributes to cost savings.
- Environmental Impact
- Environmentally friendly binders and effective sand reclamation practices reduce the ecological footprint of the sand casting process.
- This is increasingly important as industries move towards more sustainable practices.
Future Directions
- Continued Material Innovation
- Ongoing research into new sand compositions, binders, and additives to further enhance casting quality and efficiency.
- Integration with Digital Technologies
- Using data analytics and predictive modeling to optimize sand mixtures and casting parameters for specific applications.
- Sustainable Practices
- A focus on developing more sustainable materials and processes to minimize the environmental impact of sand casting.
In summary, advancements in sand quality are crucial in enhancing the efficiency, precision, and sustainability of sand casting processes. These improvements not only benefit manufacturers in terms of reduced costs and higher-quality outputs but also contribute positively to environmental conservation efforts in the industry.
Chapter 6:The Comprehensive Process of Sand Casting
Sand casting is a versatile and widely used process in metal casting, involving several key steps. Here’s a comprehensive breakdown of the entire process:
1. Designing the Pattern
- Creation: A pattern, which is a replica of the final cast product, is designed and created. Materials like wood, plastic, or metal are used.
- Considerations: Patterns must account for the metal’s shrinkage during cooling and other variances.
2. Preparing the Sand Mold
- Mixing Sand: Sand is mixed with a binder and sometimes other additives to enhance its properties.
- Molding: The pattern is placed into a box (flask), and the sand mixture is compacted around it. This is done in two halves – the cope (top) and drag (bottom).
- Creating the Cavity: After the sand hardens, the pattern is removed, leaving a cavity that will form the cast part.
3. Creating Cores (If Necessary)
- Cores: For creating internal cavities or undercuts, sand cores made from a similar sand mixture are placed in the mold cavity.
4. Assembling the Mold
- Positioning Cores: Cores are inserted into the mold if internal geometries are required.
- Closing the Mold: The cope and drag are precisely aligned and closed.
5. Pouring the Molten Metal
- Melting the Metal: The metal (aluminum, iron, steel, bronze, etc.) is melted in a furnace to the required temperature.
- Pouring: Molten metal is carefully poured into the mold through a pouring cup and down a system of runners and gates to reach the cavity.
6. Cooling and Solidification
- Waiting Period: The metal is allowed to cool and solidify in the mold. The time depends on the metal’s thickness and composition.
7. Mold Breakaway
- Removing the Casting: Once solidified, the sand mold is broken apart (often vibratory or mechanical methods are used), and the casting is removed.
8. Cleaning and Finishing
- Trimming: Excess material, such as gates and runners, is cut off or ground down.
- Cleaning: The casting may require sandblasting, grinding, or polishing to remove any residual sand or scale and to improve surface finish.
9. Inspection and Quality Control
- Testing: Castings are inspected for defects, dimensional accuracy, and material properties, often using non-destructive methods like x-ray or ultrasound.
10. Post-processing (If Required)
- Heat Treatment: Some castings undergo heat treatment to achieve desired mechanical properties.
- Machining: Additional machining may be required for precision areas or where tighter tolerances are needed.
11. Final Inspection and Dispatch
- Final Check: A final quality check is done before the parts are shipped to the customer.
Factors Affecting the Process
- Mold Material and Type: The choice of sand and binder significantly affects the mold’s properties.
- Metal Type and Temperature: Different metals and alloys have specific melting points and behaviors in the mold.
- Design Complexity: Complex shapes might require specialized cores or advanced molding techniques.
Conclusion
Sand casting is a multi-step process involving precise design, careful preparation of molds, accurate pouring, and detailed finishing. Despite its age-old roots, it remains a fundamental method in modern manufacturing due to its flexibility, cost-effectiveness, and adaptability to a wide range of metals and complex geometries.
Chapter 7: Analyzing the Economic Benefits of Sand Casting in Manufacturing
Sand casting, one of the oldest and most versatile manufacturing processes, offers several economic benefits that make it a preferred choice in various industries. Here’s an analysis of its economic advantages:
1. Low Cost of Tooling
- Initial Setup: The cost to create sand molds and patterns is significantly lower compared to more complex and permanent mold-making processes.
- Modifications: Altering or modifying sand molds is relatively inexpensive, making it ideal for prototypes and small runs.
2. Flexibility in Materials and Sizes
- Material Options: Sand casting can accommodate a wide range of metals, including iron, steel, aluminum, bronze, and more, without significant changes in tooling.
- Size Adaptability: It’s suitable for casting parts of almost any size – from small components to large machinery parts, offering versatility in production.
3. Cost-Effectiveness for Small to Medium Batches
- Production Scale: Especially economical for small to medium batch production, where the cost of expensive mold tooling wouldn’t be justified.
- Prototype Development: Ideal for developing and testing prototypes without substantial investment.
4. Reduced Waste through Reusability
- Sand Reclamation: Modern sand casting practices allow for the recycling and reuse of sand, which can significantly cut material costs.
- Resource Efficiency: This process reduces waste, as excess metal from sand casting process can also be melted down and reused.
5. Lower Energy Requirements
- Energy Consumption: Sand casting generally requires less energy compared to high-temperature and high-pressure casting processes, leading to lower manufacturing costs.
6. Simpler Machinery and Maintenance
- Equipment Investment: The machinery required for sand casting is less complex and costly compared to other casting methods.
- Maintenance and Upkeep: Lower maintenance requirements translate into reduced operational costs.
7. Reduced Labor Costs
- Skill Level: The process can often be performed with less skilled labor compared to other manufacturing processes, although skilled workers are essential for quality control and complex molds.
- Labor Efficiency: Automation in sand mixing, mold making, and sand casting processes further reduces labor costs.
8. Customization and Design Flexibility
- Design Changes: Making design changes in sand casting is not as costly as in other processes, encouraging innovation and customization.
9. Minimized Lead Times
- Rapid Production: Quick setup and turnaround times, particularly for small batches, can reduce overall lead times.
Conclusion
Sand casting offers a unique combination of low cost, flexibility, and material versatility, making it economically beneficial, especially for small to medium-scale production and complex, customized parts. While it might not always match the precision and finish of other casting methods, its cost-effectiveness and adaptability continue to make it a valuable tool in the manufacturing sector.
Chapter 8: Enhancing Precision in Sand Casting
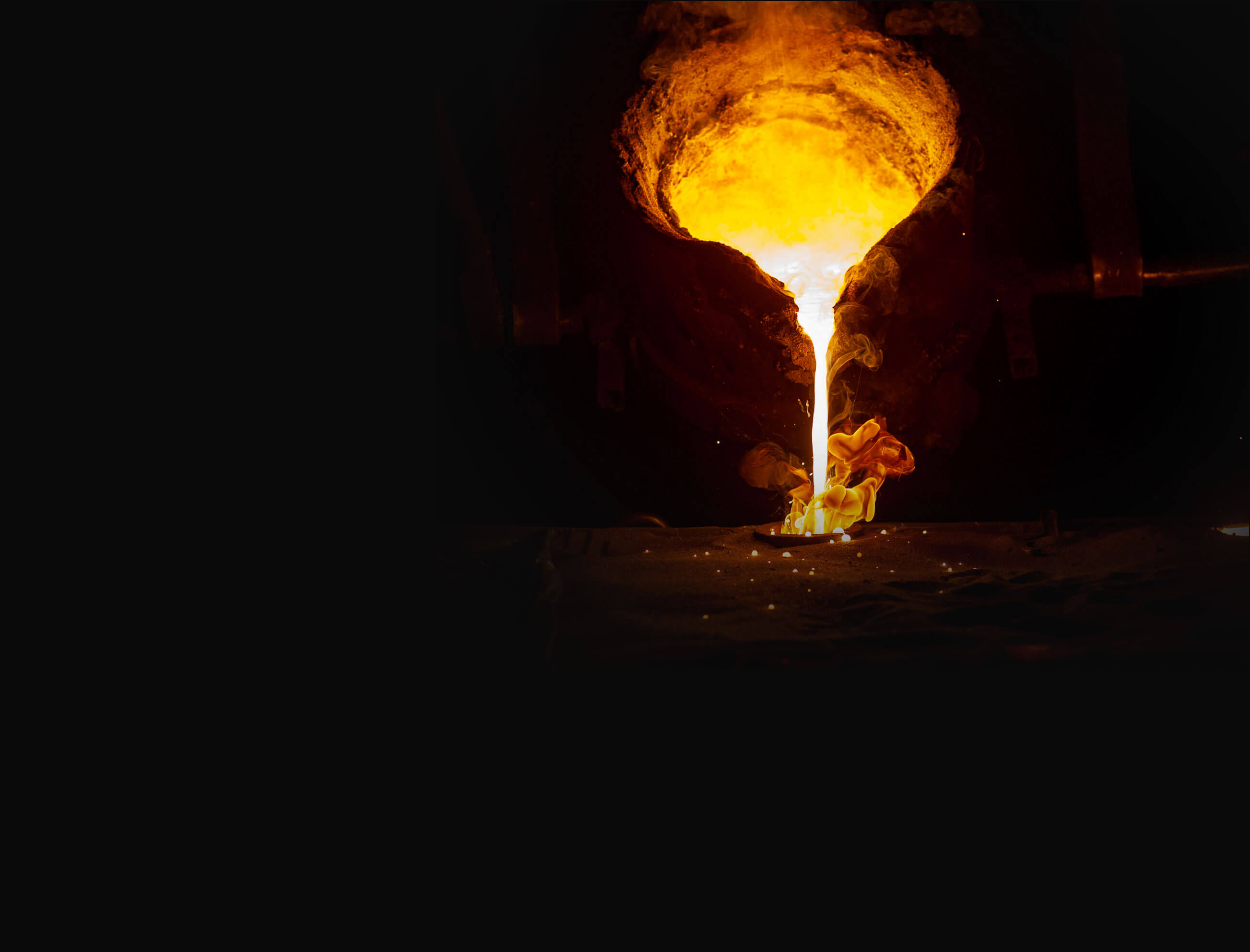
Enhancing precision in sand casting is crucial for meeting the increasing demands for quality and complexity in various industries. Advancements and techniques in this area focus on improving the accuracy of molds and the quality of cast parts. Here’s an overview of strategies used to enhance precision in sand casting:
1. Improved Pattern Making
- 3D Printing: Utilizing 3D printing technology for creating precise and complex patterns.
- CNC Machining: CNC machining of patterns for higher accuracy compared to traditional manual methods.
2. Quality of Sand and Binders
- High-Grade Sand: Using sand with consistent grain size and shape to reduce flaws in the casting.
- Advanced Binders: Employing stronger and more stable binders to maintain mold integrity and dimensional accuracy.
3. Mold Making Techniques
- Precision Molding: Employing automated molding machines that ensure consistent and precise mold production.
- Core Making: Improving core making processes for better dimensional control of internal features of castings.
4. Controlled Pouring Techniques
- Automated Pouring: Implementing automated pouring systems to control the rate and volume of molten metal, reducing turbulence and the risk of defects.
- Temperature Control: Precisely controlling the temperature of molten metal to ensure consistent flow and solidification.
5. Mold Design Improvements
- Simulation Software: Using computer simulations to predict and correct potential issues in mold design, such as shrinkage and gas traps.
- Venting and Gating Systems: Optimizing gating and venting systems to ensure proper metal flow and gas escape.
6. Post-Casting Processes
- Heat Treatment: Applying heat treatment to relieve internal stresses and improve dimensional stability.
- Machining and Finishing: Additional machining and finishing processes to achieve desired tolerances and surface finishes.
7. Quality Control Measures
- Inspection and Testing: Implementing stringent inspection and testing procedures, including X-ray, ultrasound, and dimensional checks.
- Continuous Monitoring: Ongoing monitoring and control of casting parameters to maintain consistent quality.
8. Research and Development
- Material Science: Exploring new materials for molds and cores that can withstand higher temperatures and pressures.
- Process Innovation: Continual research into improving every aspect of the sand casting process for greater precision.
Conclusion
Enhancing precision in sand casting involves a combination of advanced technology, quality materials, precise equipment, and stringent quality control measures. These improvements are crucial for industries where precision and reliability are paramount, such as aerospace, automotive, and medical devices. As technology continues to advance, we can expect even further improvements in the precision and capabilities of sand casting.
Chapter 9: The Environmental Impact of Sand Casting
Sand casting, while a versatile and cost-effective manufacturing process, poses certain environmental challenges. However, with growing awareness and technological advancements, the industry is actively seeking solutions to mitigate these impacts. Here’s an overview of the environmental challenges and the solutions being implemented:
Environmental Challenges of Sand Casting
- Sand Waste
- Traditional sand casting generates a significant amount of used sand, which often ends up in landfills, posing disposal issues.
- Chemical Binders
- Some binders used in sand molds release volatile organic compounds (VOCs) and other harmful emissions when the metal is poured.
- Energy Consumption
- The melting of metals requires high levels of energy, contributing to carbon emissions, especially if the energy is sourced from fossil fuels.
- Resource Depletion
- The extraction of high-quality silica sand for casting can lead to environmental degradation, including soil erosion and habitat disruption.
Solutions and Sustainable Practices
- Sand Reclamation
- Implementing sand reclamation processes where used sand is cleaned, conditioned, and reused, significantly reducing waste and the need for new sand.
- Eco-friendly Binders
- Developing and using binders that are less harmful to the environment. Biodegradable and water-based binders are examples of more sustainable options.
- Energy Efficiency
- Adopting more energy-efficient melting technologies.
- Utilizing renewable energy sources for powering sand casting processes.
- Improved Process Efficiency
- Optimizing sand casting processes to reduce waste and improve yield, thus lowering the overall environmental footprint.
- Implementing advanced technologies like 3D printing for making patterns and cores can reduce material waste.
- Emissions Control
- Installing systems to capture and treat emissions from foundries, including filtering systems for particulate matter and scrubbers for gaseous pollutants.
- Recycling of Metals
- Encouraging the recycling of scrap and excess metal from sand casting process, reducing the need for new metal production.
- Research and Development
- Investing in R&D to find more sustainable materials and processes, including alternative sands and reusable mold materials.
- Regulatory Compliance and Best Practices
- Adhering to environmental regulations and industry standards for sustainable operations.
- Promoting best practices within the industry for environmental management.
Conclusion
The environmental impact of sand casting presents considerable challenges, but the industry is responding with innovative solutions and sustainable practices. By focusing on waste reduction, emissions control, and energy efficiency, sand casting can continue to be a vital part of the manufacturing world while minimizing its ecological footprint. This balance is crucial for the industry’s long-term viability and for meeting the global demand for more environmentally responsible manufacturing practices.
Chapter 10: Exploring the History and Evolution of Sand Casting Methods
Sand casting, one of the oldest and most fundamental metal forming techniques, has a rich history that dates back thousands of years. Its evolution is a testament to human ingenuity and the continuous pursuit of efficiency and precision in metalworking. Let’s explore this fascinating journey:
Ancient Origins
- Early Beginnings: Sand casting is believed to have been used as early as 3000 B.C. The oldest known casting is a copper frog from 3200 B.C. in Mesopotamia.
- Bronze Age: The technique became more prevalent during the Bronze Age, where it was used for weapons, tools, and jewelry.
Medieval and Renaissance Developments
- Widespread Use: In medieval Europe, sand casting was employed for bells, cannons, and statuary.
- Advancements: The Renaissance period saw further refinement in sand casting methods, including the development of more intricate molds and patterns.
Industrial Revolution
- Mass Production: The Industrial Revolution marked a significant turning point. Sand casting was integral in producing parts for the first machines and steam engines.
- Innovation in Materials: This era also saw the introduction of new metals and alloys, expanding the possibilities in casting.
20th Century Advancements
- Technological Integration: The advent of electricity and automation brought about electric melting furnaces, more precise control, and mass production capabilities.
- Patternmaking Evolution: The use of new materials like plastics and improved wood types for patterns enhanced the quality and detail of castings.
Late 20th to 21st Century
- Computer-Aided Design (CAD): CAD revolutionized pattern making and mold design, allowing for more complex and precise castings.
- Environmental Considerations: Increasing awareness of environmental impacts led to the development of more sustainable practices in sand casting.
Modern Era Innovations
- 3D Printing: The introduction of 3D printing technology, especially for making molds and cores, has significantly enhanced the precision and complexity of sand castings.
- Advanced Materials: The continuous development of new casting materials and binders has improved the strength and quality of castings.
- Quality Control Technologies: Modern inspection and quality control techniques, including X-ray and computer tomography, ensure higher accuracy and integrity in cast products.
Conclusion
The evolution of sand casting reflects a journey of continuous improvement and adaptation. From ancient craftsmen to modern manufacturers, the method has consistently been refined to meet the growing demands of precision, efficiency, and environmental responsibility. Today, sand casting remains a vital manufacturing process, adaptable to diverse industries and capable of producing a wide range of products. Its historical journey underscores the enduring importance of this foundational manufacturing technique.