Because sand casting is a special process, with many hidden links and collective operation mode, some processes cannot be directly observed and tested, such as the inside of the cavity of the box distribution link. Moreover, there are many uncontrollable factors in the process, and the manufacturing and equipment supervision work are difficult. In the past projects, sand mold casting defects often occurred in key parts of the crankcase, such as cracks in the water jacket and pores in the key hole system, which led to product scrapping. Even some defects can be found when the machining is nearly completed, resulting in product scrapping, which not only affects the delivery schedule, but also brings great losses to the factory.
Therefore, attention should be paid to the defects of sand casting in the supervision of diesel engine crankcase. After summary and analysis, it is found that the problems causing product scrapping are relatively single, such as the air holes and cracks described above, and basically exist in fixed positions. In view of this situation, targeted methods should be adopted for manufacturing supervision. First, key processes and key points in the manufacturing process should be identified, and key supervision should be carried out to ensure no problems. Secondly, in order to ensure the comprehensiveness of problem finding, risk thinking can be adopted to collect the problems of similar products in the same workshop and conduct preventive supervision.
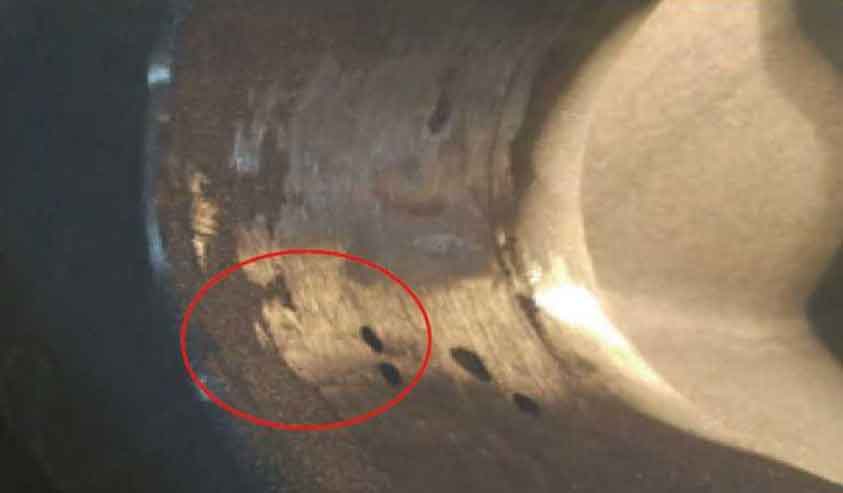
In order to ensure the comprehensiveness of problem identification, the problems existing in similar sand casting products of previous projects in the production workshop were also collected. The reasons leading to the scrapping of the crankcase sand casting are mainly collected, including the internal defects of the cylinder bore, the air hole defects in the camshaft bore, and the subcutaneous defects on the top of the engine body, among which the most air holes are in the camshaft bore. See Fig. 1 and Fig. 2.
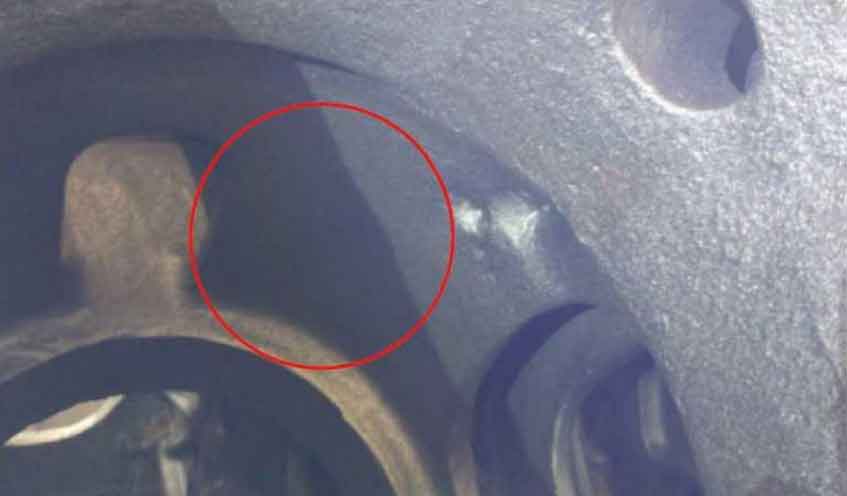