With the increasing requirements of energy saving, environmental protection and reducing the cost of components, large-scale structural casting of aluminum magnesium alloy has become an important development trend, and its manufacturing technology has become the current development hotspot. At present, the main production technologies of large-scale aluminum magnesium alloy structural parts are high-pressure casting, squeeze casting and low-pressure casting. Due to the high production efficiency and good product quality of high-pressure casting has become the main production process. The development of its manufacturing technology mainly focuses on the high-pressure casting process, which is prone to air entrainment and the formation of air holes inside the casting, so the improvement of heat treatment can not be carried out.
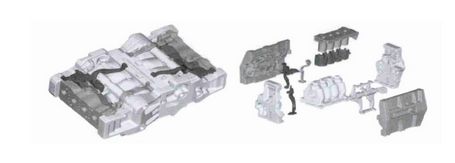
Fulai company of Germany has developed vacuum negative pressure suction casting technology, and the whole process of die casting is carried out in high vacuum state (less than 30 mbar). The metal liquid is sucked in from the furnace by the straw without oxidation through the mould, pressure chamber and straw in the vacuum state, and the steam of the release agent is also discharged by the vacuum system. The main features of the vacuum negative pressure suction casting process are as follows: when the quantitative casting is started, the whole system is in a high vacuum state; during the quantitative casting process, the gas in the mold cavity and the metal melt can be effectively discharged; during the pouring process, the metal melt has no oxidation; during the pouring process, there is no heat loss, and the lower pouring temperature can be used for pouring, Under real-time monitoring, undisturbed laminar flow filling is carried out. The above process has been successfully applied to the mass production of automobile structural castings, providing advanced forming methods and processes for the application of high-quality light alloy castings.
A double circuit vacuum system for the production of structural castings has been developed by Buhler company in Switzerland. The production technology is called the production technology of structural parts, as shown in Figure 5. Using the technology of structural parts production can improve the speed of vacuum pumping, thus obtaining stable production conditions and significantly improving the quality of die casting. As shown in Figure 5, the air extraction port of one circuit in the double circuit vacuum system is set at the upper end of the pressure chamber, which is mainly used for air extraction in the pressure chamber. When the injection punch moves forward to seal the pouring port, it starts and closes at the moment when the punch is about to seal the air extraction port. The other circuit is set up in the same way as the traditional vacuum process, which is mainly used for air extraction in the cavity. At present, the technology has been successfully applied to the manufacturing of aluminum alloy integrated shock absorption tower, door inner panel, body longitudinal beam and other components of passenger cars.