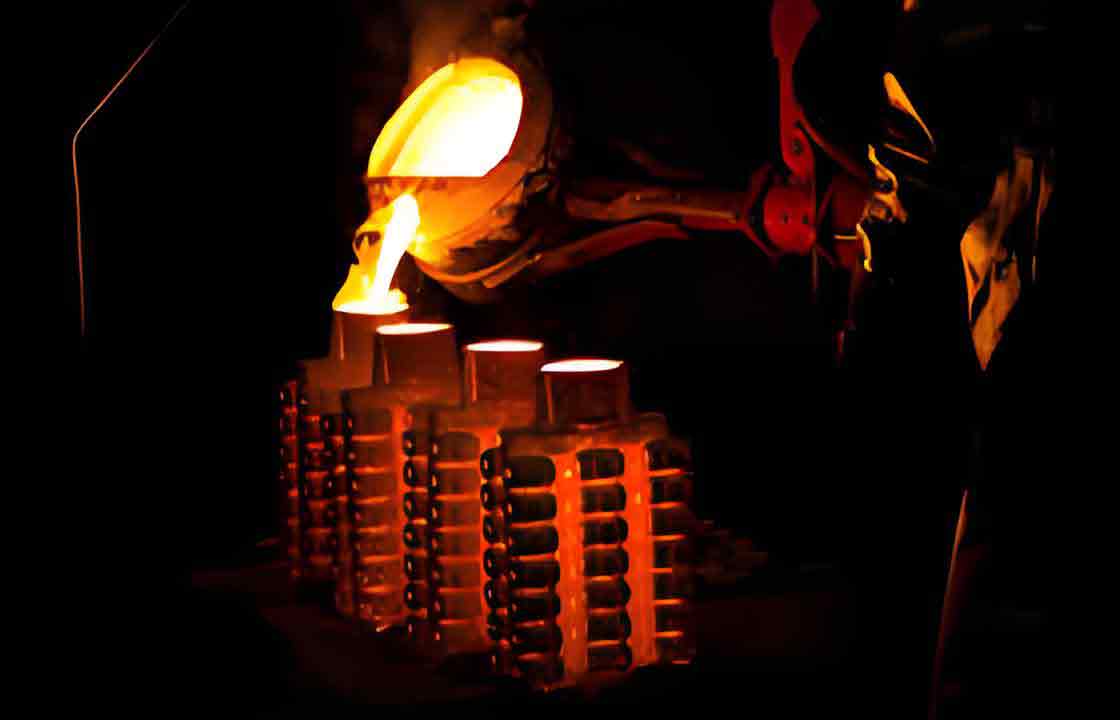
Lost wax casting is manufacturing process widely used for creating intricate and high-precision metal components. One of the critical factors determining the success of this process is the selection of appropriate materials and the development of suitable alloys. The right choice of materials not only ensures the desired mechanical properties and performance but also enhances the overall efficiency and cost-effectiveness of the casting process. This article delves into the considerations for material selection and alloy development in lost wax casting, highlighting key factors, common materials, and advancements in alloy technology.
Introduction to Lost Wax Casting
Lost wax casting involves creating a wax model of the desired part, which is then coated with a ceramic shell. The wax is melted out, leaving a cavity that is filled with molten metal. Once the metal solidifies, the ceramic shell is removed to reveal the metal casting. This process is particularly advantageous for producing components with complex geometries and fine details.
Key Steps in Lost Wax Casting
- Pattern Creation: A wax model of the desired part is created using injection molding or hand carving.
- Assembly: Multiple wax models can be assembled onto a wax tree to create multiple parts in a single batch.
- Shell Building: The wax assembly is repeatedly dipped into a ceramic slurry and coated with fine sand to build a ceramic shell.
- Dewaxing: The ceramic shell is heated to remove the wax, leaving a hollow cavity.
- Metal Pouring: Molten metal is poured into the ceramic mold.
- Shell Removal: Once the metal has solidified, the ceramic shell is broken away to reveal the casting.
- Finishing: The casting is cleaned, and any excess material is removed to achieve the final product.
Importance of Material Selection in Lost Wax Casting
Material selection is critical in lost wax casting as it directly impacts the mechanical properties, performance, and cost of the final product. The choice of material affects the casting’s strength, hardness, ductility, corrosion resistance, and thermal stability. Additionally, the compatibility of the material with the casting process and its ease of casting also play significant roles.
Key Considerations for Material Selection
- Mechanical Properties: Desired properties such as tensile strength, hardness, and ductility.
- Thermal Properties: Ability to withstand high temperatures without deformation or degradation.
- Corrosion Resistance: Suitability for the intended environmental conditions and exposure.
- Castability: Ease of pouring, fluidity, and ability to fill intricate mold details.
- Cost: Material cost and overall cost-effectiveness of the casting process.
Common Materials Used in Lost Wax Casting
A variety of metals and alloys are used in lost wax casting, each offering distinct advantages and properties. The following table summarizes some common materials and their typical applications.
Material | Properties | Applications |
---|---|---|
Carbon Steel | High strength, low cost | Structural components, industrial machinery |
Stainless Steel | Corrosion resistance, strength | Medical devices, food processing equipment |
Aluminum Alloys | Lightweight, good thermal properties | Aerospace, automotive, electronics |
Copper Alloys | High conductivity, corrosion resistance | Electrical components, plumbing fittings |
Nickel Alloys | High temperature resistance, strength | Aerospace, chemical processing |
Titanium Alloys | High strength-to-weight ratio, biocompatibility | Medical implants, aerospace |
Cobalt Alloys | Wear resistance, strength | Cutting tools, wear-resistant components |
Example Applications
- Aerospace Components: Nickel and titanium alloys for high strength and temperature resistance.
- Medical Implants: Stainless steel and titanium alloys for biocompatibility and corrosion resistance.
- Automotive Parts: Aluminum alloys for lightweight and good thermal properties.
Alloy Development for Lost Wax Casting
The development of specialized alloys is crucial for enhancing the performance of lost wax cast components. Alloy development involves adjusting the composition of base metals by adding various alloying elements to achieve specific properties. These alloying elements can improve mechanical strength, corrosion resistance, wear resistance, and other desired characteristics.
Key Alloying Elements and Their Effects
- Carbon (C): Increases hardness and strength in steels but can reduce ductility.
- Chromium (Cr): Enhances corrosion resistance, especially in stainless steels.
- Nickel (Ni): Improves toughness, corrosion resistance, and high-temperature stability.
- Molybdenum (Mo): Increases strength and hardness, particularly at high temperatures.
- Titanium (Ti): Enhances strength-to-weight ratio, corrosion resistance, and biocompatibility.
- Cobalt (Co): Increases wear resistance and strength, especially in high-temperature applications.
Advanced Alloys for Lost Wax Casting
Advanced alloys are developed to meet the stringent requirements of modern industries. These alloys often incorporate multiple alloying elements to achieve a balance of properties suitable for specific applications.
Superalloys
Superalloys, primarily based on nickel, cobalt, and iron, are designed to withstand extreme temperatures and mechanical stresses. They are commonly used in aerospace, power generation, and chemical processing.
- Example: Nickel-based superalloys with chromium, molybdenum, and titanium additions for high-temperature strength and corrosion resistance.
Titanium Alloys
Titanium alloys are favored for their high strength-to-weight ratio, corrosion resistance, and biocompatibility, making them ideal for aerospace and medical applications.
- Example: Ti-6Al-4V (Titanium-Aluminum-Vanadium) alloy used in aircraft components and medical implants.
Challenges and Solutions in Alloy Development
Developing new alloys for lost wax casting involves addressing several challenges, including achieving uniform composition, avoiding casting defects, and ensuring compatibility with the casting process. Advanced techniques and technologies are employed to overcome these challenges.
Challenges
- Segregation: Uneven distribution of alloying elements can lead to variations in properties.
- Casting Defects: Issues such as porosity, inclusions, and cracking can compromise the quality of the casting.
- Compatibility: Ensuring that the developed alloy is compatible with the lost wax casting process.
Solutions
- Advanced Melting Techniques: Using vacuum induction melting or electron beam melting to achieve uniform alloy composition.
- Process Optimization: Optimizing pouring temperature, mold design, and cooling rates to minimize casting defects.
- Quality Control: Implementing stringent quality control measures, including non-destructive testing and automated inspection.
Case Studies: Successful Alloy Development in Lost Wax Casting
Case Study 1: Aerospace Turbine Blades
A leading aerospace manufacturer developed a nickel-based superalloy for turbine blades using lost wax casting. The alloy, with additions of chromium, cobalt, and aluminum, exhibited excellent high-temperature strength and oxidation resistance, significantly improving the performance and lifespan of the turbine blades.
Case Study 2: Medical Hip Implants
A medical device company developed a titanium alloy for hip implants using lost wax casting. The Ti-6Al-4V alloy provided the necessary biocompatibility, strength, and corrosion resistance, resulting in highly reliable and long-lasting implants.
Case Study 3: High-Performance Automotive Parts
An automotive manufacturer developed an aluminum-silicon alloy for high-performance engine components using lost wax casting. The alloy offered a combination of lightweight, thermal conductivity, and wear resistance, enhancing engine efficiency and durability.
Conclusion
Material selection and alloy development are critical aspects of lost wax casting that significantly impact the quality and performance of the final products. By understanding the properties and applications of different materials, and by developing advanced alloys tailored to specific requirements, manufacturers can optimize their casting processes and produce components that meet stringent industry standards. Continuous advancements in alloy technology and casting techniques ensure that lost wax casting remains a vital and versatile manufacturing process for a wide range of applications.
4o