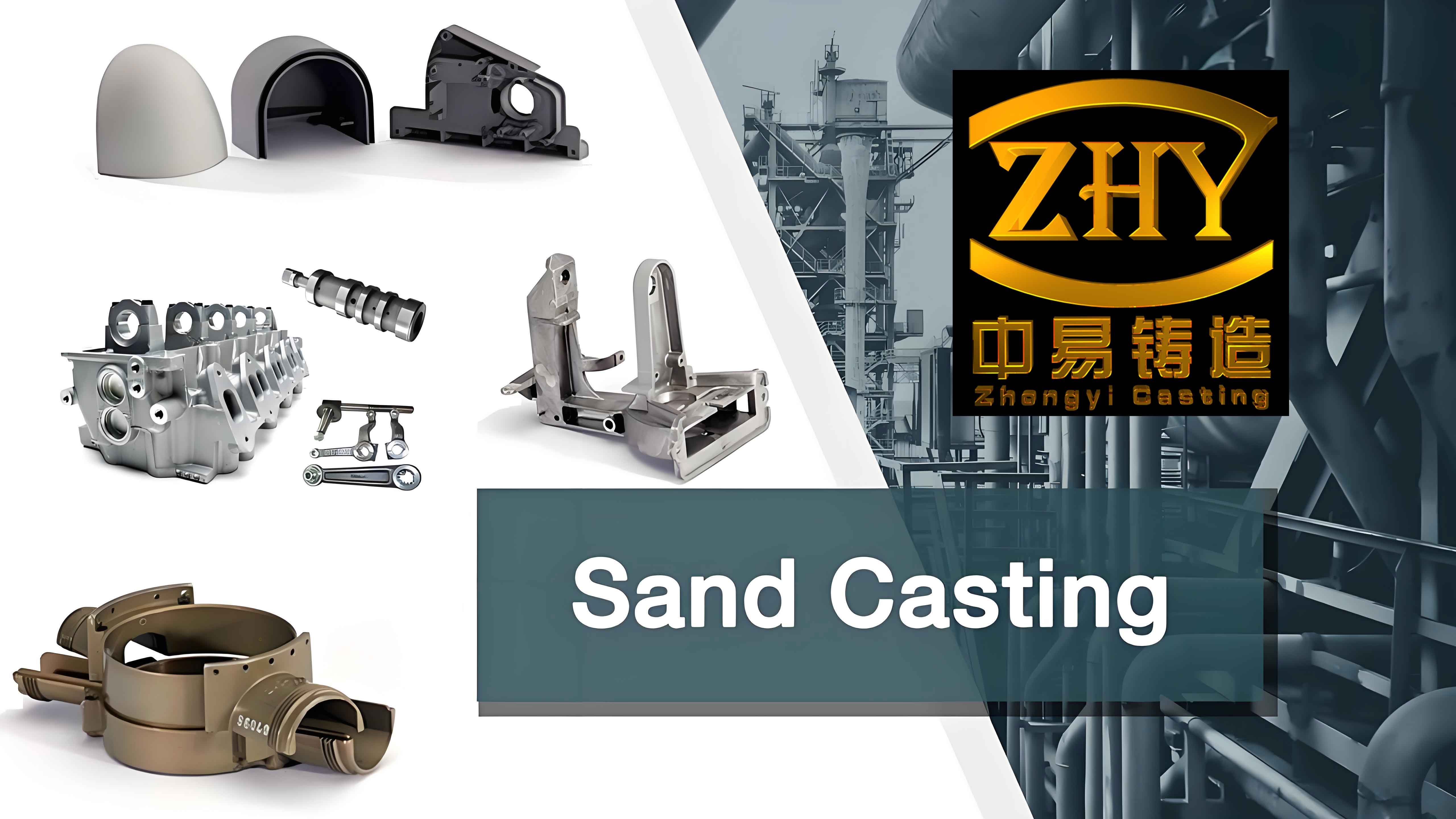
Sand casting is one of the most versatile and widely used methods for casting metals. Despite its many advantages, such as flexibility in design, cost-effectiveness, and the ability to cast large components, sand casting can also present various challenges. One of the most significant challenges in sand casting is the occurrence of casting defects. These defects can affect the quality, functionality, and aesthetics of the final product. This article aims to address some of the most common casting defects in sand casting, exploring their causes and proposing methods to prevent or mitigate them.
Common Casting Defects in Sand Casting
1. Porosity
Causes:
- Gas entrapment during the pouring process.
- High moisture content in the sand.
- Inadequate venting.
Prevention:
- Ensure proper sand preparation with controlled moisture content.
- Use vents and risers to allow gases to escape.
- Maintain appropriate pouring temperature.
Factor | Solution |
---|---|
High moisture content | Use drier sand |
Inadequate venting | Add more vents |
Gas entrapment | Adjust pouring speed and temperature |
2. Shrinkage
Causes:
- Improper cooling rates.
- Inadequate feeding of molten metal.
- Poor design of the gating system.
Prevention:
- Optimize cooling rates by using chills or insulating sleeves.
- Design a proper gating system to ensure uniform metal flow.
- Use risers to compensate for shrinkage.
Factor | Solution |
---|---|
Improper cooling rates | Use chills or insulating sleeves |
Inadequate feeding | Employ risers and feeders |
Poor gating system design | Redesign gating system |
3. Cold Shut
Causes:
- Low pouring temperature.
- Slow pouring speed.
- Incorrect design of the gating system.
Prevention:
- Increase the pouring temperature to ensure complete fusion.
- Maintain a steady and appropriate pouring speed.
- Design the gating system to minimize turbulence.
Factor | Solution |
---|---|
Low pouring temperature | Increase pouring temperature |
Slow pouring speed | Adjust pouring speed |
Gating system design | Optimize for minimal turbulence |
4. Misruns
Causes:
- Low metal temperature.
- Insufficient metal flow.
- Poor gating system design.
Prevention:
- Ensure the metal is at the correct pouring temperature.
- Design a gating system that allows adequate metal flow.
- Avoid complex shapes that are difficult to fill.
Factor | Solution |
---|---|
Low metal temperature | Ensure proper melting temperature |
Insufficient metal flow | Design better gating system |
Complex shapes | Simplify design or improve flow |
5. Sand Inclusion
Causes:
- Loose sand particles entering the mold cavity.
- Inadequate compaction of sand mold.
- Excessive turbulence during pouring.
Prevention:
- Properly compact the sand mold to ensure stability.
- Maintain smooth pouring to reduce turbulence.
- Inspect and clean mold cavities before pouring.
Factor | Solution |
---|---|
Loose sand particles | Compact sand mold properly |
Inadequate compaction | Ensure thorough compaction |
Excessive turbulence | Control pouring speed |
6. Hot Tears
Causes:
- Restrained contraction of the casting during solidification.
- Poor mold design.
- Inappropriate alloy composition.
Prevention:
- Design the mold to allow free contraction of the metal.
- Use materials with lower thermal expansion coefficients.
- Modify the alloy composition if necessary.
Factor | Solution |
---|---|
Restrained contraction | Design for free contraction |
Poor mold design | Redesign mold |
Alloy composition | Adjust alloy materials |
7. Mold Shift
Causes:
- Misalignment of mold halves.
- Insufficient clamping of the mold.
- Inaccurate pattern placement.
Prevention:
- Ensure proper alignment of mold halves.
- Use adequate clamping pressure to secure the mold.
- Check pattern placement before pouring.
Factor | Solution |
---|---|
Misalignment of mold halves | Align molds accurately |
Insufficient clamping | Apply adequate clamping pressure |
Inaccurate pattern placement | Verify pattern placement |
Conclusion
Casting defects in sand casting can significantly impact the quality and performance of cast components. By understanding the causes of these defects and implementing the appropriate preventive measures, manufacturers can improve the reliability and quality of their castings. Proper sand preparation, gating system design, and control of pouring parameters are crucial in addressing common casting defects. By continually monitoring and optimizing the casting process, it is possible to minimize defects and produce high-quality castings consistently.