The wall thickness of ductile iron piston varies greatly, the thinnest part is 7.5 mm, the thickest part is 23 mm, the outer contour dimension of piston is 235 mm × 380 mm, and the internal structure is complex. Nodular iron piston is composed of pin hole, cooling chamber, vertical rib and combustion chamber. The piston requires zero defect.
- Combustion chamber
Porosity and shrinkage porosity are the most common defects of ductile iron, and these defects are absolutely not allowed to appear on the surface of piston combustion chamber. When the piston works in the combustion chamber, it needs to withstand the repeated action of high-temperature and high-pressure gas. This defect will cause stress concentration. The thermal effect and mechanical load of high-frequency pulsation will lead to piston damage, which will cause disastrous consequences.
- The ring groove is prone to problems
The wall thickness of the ring groove is thick and easy to appear loose. The ring groove is used to place the piston ring. High temperature leads to poor lubrication conditions at the ring groove. When working, the piston ring moves with the piston at high speed under the action of high temperature and high pressure gas, repeatedly hitting both sides of the ring groove, and all the force on the piston ring is transferred to the piston ring groove, so the piston ring groove is not allowed to have any loose defects.
- Easy to have problems at the vertical reinforcement
The wall thickness of the joint between the piston rib and the pin hole is large, which is easy to loose. Due to the complex structure and irregular shape of the vertical bar, it is not convenient to place cold iron.
- The pin hole is easy to have problems
The piston pin hole is prone to slag inclusion and porosity. The piston pin is installed in the pin hole to connect the piston and connecting rod, and transmit the force borne by the piston to the connecting rod. The piston pin bears a large periodic impact load at high temperature. The piston pin transfers the impact load to the piston pin hole. Once there is slag inclusion, it will become the stress concentration point, resulting in cracks at the piston pin hole. If the crack expands seriously, the pin hole is damaged, the connecting rod is separated from the piston, and the connecting rod moves at high speed in the cylinder block, the cylinder block will be damaged and the whole diesel engine set will lose its working ability. Cold iron cannot be placed at the pin hole, which is easy to cause slag inclusion.
5. Casting process design
The casting process is designed by sequential solidification. During Eutectic Transformation of ductile iron, the precipitation of graphite will cause volume expansion, but its tendency of shrinkage porosity is much greater than that of gray cast iron. Because the graphite core of spheroidal graphite cast iron is surrounded by austenite, the volume expansion produced by the growth of graphite ball is affected by the expansion of austenite. Only a small part of the expansion is transferred to the liquid between dendrites, while most of it acts on the adjacent eutectic group or primary austenite skeleton, which leads to the production of ductile iron The tendency of expansion before shrinkage is much greater than that of gray cast iron. In addition, the nodular cast iron is “mushy solidified”. During the whole solidification period, the firmness of its shell is far less than that of gray cast iron. If the rigidity of cast iron is not enough, most of the volume expansion caused by graphitization will be consumed by shell expansion. As a result, the liquid shrinkage and solidification shrinkage of the internal liquid between dendrites or eutectic groups can not be compensated. At the same time, due to the fine and many graphite eutectic clusters precipitated during solidification of nodular cast iron, even if the riser is used for feeding, the effect is not ideal when the riser efficiency is not high, the liquid holding time is not long enough or the pressure is not large enough.
The vertical rib of pin hole is the thickest area of piston. It is not convenient to place cold iron in the mold cavity, so the inner riser must be used for feeding. Due to the limitation of location and space, only 50 mm insulation riser can be placed. After calculation, the feeding amount is insufficient, so it is necessary to heighten the riser and splice two risers into one riser to increase the filling amount.
According to the above requirements, the casting process as shown in Figure 1 is adopted, and the mold is sodium silicate sand.
① The outer mold, core box, pouring system, bottom and cover box are made of nodular iron and aluminum alloy respectively. The core of clay is made of Atalanta resin sand, the outer mold cavity is made of sodium silicate sand, and the coating is alcohol based graphite coating.
② The first baking temperature of the clay core is 430 ℃± 10 ℃, and then it is put out of the kiln and painted after 30 min. After the core is put into the kiln and then baked, the baking temperature is 360 ℃± 10 ℃ and kept for 3 h, and the external mold is baked at 250 ℃ and kept for 5 h, then the concrete can be poured in a box.
③ Molten iron is melted in 500 kg acidic medium frequency furnace. The charge is made of Q10 pig iron, scrap steel, nickel, chromium, molybdenum, etc. according to the chemical composition of piston.
④ In the middle and later stage of pouring, three Y-shaped samples were injected for physical and chemical property testing. The samples and pistons of the same furnace were heat treated in the furnace.
⑤ The residual sand, flash, burr and fleshy parts shall be completely removed.
- Difficulty solving
In view of the above difficulties, special solutions are adopted respectively.
(1) Combustion chamber defects. In view of the possible loose defects on the surface of the combustion chamber, the shape following cold iron is placed in the combustion chamber, which can accelerate the cooling of the combustion chamber, refine the structure of the combustion chamber and eliminate the loose defects in the combustion chamber.
(2) The ring groove is defective. The wall thickness of the ring groove is thick and easy to appear loose. As with the combustion chamber, the way of cold iron quenching is adopted to accelerate the cooling, refine the structure and eliminate the porosity defects.
(3) There are defects in the vertical reinforcement. The wall thickness of the joint between the piston rib and the pin hole is large, which is easy to loose. Due to the complex structure and irregular shape of the vertical reinforcement, it is not convenient to place the cold iron. Therefore, a riser is placed at the joint of the pin hole and the vertical reinforcement, and one hidden riser is placed at each of the two vertical bars, and the concealed riser is placed inside the main clay core. The riser is feeding the opposite reinforcement to eliminate the shrinkage porosity at the vertical reinforcement.
(4) Defect at pin hole. Inclusions and shrinkage porosity are easy to appear in the piston pin hole. Cold iron can not be used to eliminate shrinkage porosity at the pin hole, which is easy to cause inclusions, and no inclusion is allowed at the pin hole. Therefore, the riser is used to feed, which can not only eliminate the shrinkage porosity, but also transfer the inclusions into the riser. Because the pin hole is connected with the vertical bar, the pin hole and the vertical bar adopt the same riser.
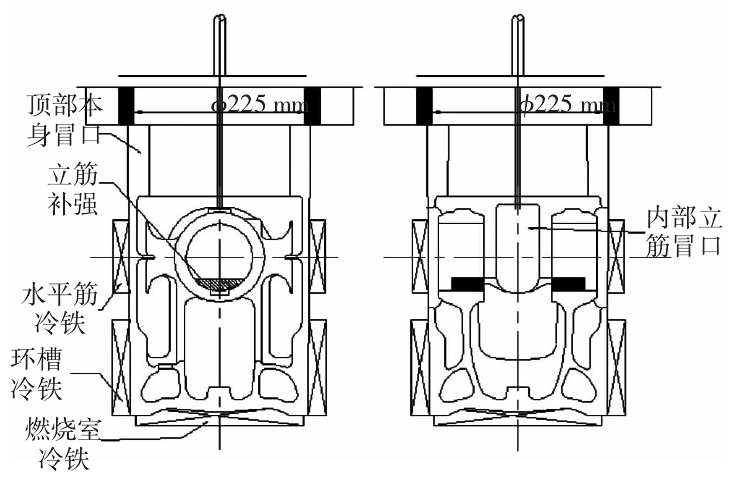