1. Preface
1.1 Background
As an important component of the engine, the appearance of the cylinder block with sand sticking directly affects the performance and appearance quality of the engine. Improving the appearance of castings with sand sticking, improving product quality, reducing waste defects, and fully utilizing material properties are one of the effective ways to improve enterprise efficiency.
Taking the appearance of HD15 engine cast iron cylinder block produced by ZHY Casting as an example, this paper analyzes it, takes a series of preventive measures and implements verification, tracks and statistically analyzes the verification results, determines the effectiveness of the measures, and finally solidifies the effective measures, in order to reduce the sand sticking defects of cylinder products and improve product quality. This article is only applicable to the production situation of ZHY CastingHD15 products. Please do not apply it mechanically, for reference only.
1.2 Wet sand process
The production of cylinder castings using wet sand molding technology has many characteristics: strong adaptability to molding methods; Can adapt to various types of raw sand; Has unique strength performance; Low cost; But the liquidity is poor and the filling effect is not good.
ZHY Casting adopts the German HWS static pressure molding line, with an upper molding compaction pressure of 45MPa and a lower molding compaction pressure of 50Mpa; The old sand in the sand system is about 350 tons, with a continuous production cycle of about 15 hours; Adopting belt with water (summer) and double disc cooling; Using a 3-ton sand mixer to mix 2.3 tons of molding sand; Online detection of mixed sand properties; The auxiliary materials for molding sand are bentonite, coal powder, and necessary ash powder, and the lower mold is sprayed with an alcohol based coating with a Baume degree of 30.
The cylinder block casting adopts the horizontal pouring method, with two the first mock examination. The material grade of the cylinder block casting is HT250, the weight of molding sand is 630Kg, the weight of sand core is 68Kg, the weight of molten iron is 120Kg, and the pouring temperature is 1410-1450 ℃.
2. Reasons for the formation of sand sticking
ZHY Casting is a professional casting factory that produces engine cylinder blocks. In the early stages of the establishment of the molding line, there was no sand sticking defect. With the continuous circulation of the old sand system and the aging of the equipment, the sand sticking defect becomes more and more obvious, especially for some products with complex appearance and large weight. The newly built sand treatment system has a good dust removal effect, resulting in insufficient amounts of fine sand and fine powder, low mud content, and high permeability; As the weight of the production cylinder increases, more sand cores need to be added during production, and the original sand for the sand cores is 50/100 sand, resulting in an AFS value of around 50-53 for molding sand and a coarser particle size; As the cycle period increases, there is an increasing amount of dead clay in the old sand system. Due to these reasons, product sand sticking is becoming increasingly prominent.
At the same time, all of our cylinder bodies adopt bottom injection water inlet. During the casting process, molten iron enters the mold from the inner gate and continuously washes the sand near the gate. The surface of the sand mold is easily damaged, making it easier for molten iron to immerse into it; The temperature of molten iron near the gate is the highest, the liquid state is maintained for a long time, and it is higher from the gate cup, bearing a larger dynamic and static pressure head. These are also the causes of sand sticking.
Most of the sticky sand in casting production belongs to mechanical sticky sand. The appearance of sticky sand in green sand belongs to mechanical sticky sand, which means that the metal liquid infiltrates into the gaps between the sand particles, sinters with the sand particles, and adheres to the surface of the casting. Slightly, it is only a thin layer that can be removed by rough polishing with the first surface treatment, and in severe cases, it can reach a layer several millimeters thick. This type of sand needs to be removed by fine polishing with the second or multiple surface treatments.
The reasons for mechanical sand sticking can be roughly divided into three situations. The first is that static pressure causes the metal liquid to penetrate between the sand particles. The second is that the dynamic pressure during the flow of the metal liquid causes the metal liquid to penetrate between the sand particles. The third is that during pouring, explosions or choking occur inside the mold, resulting in dynamic pressure causing the metal liquid to penetrate between the sand particles.
The third case is mainly discussed here. Since the air pressure in the mold cavity is too high, resulting in sand sticking on the appearance of the casting, where does the air pressure in the mold cavity come from? It mainly comes from three aspects: the gas generation of resin and coating in the sand core, the gas generation of coal powder and water in the sand mold, and the gas in the mold itself.
The method of preventing sand sticking in green sand mainly relies on adding coal powder or graphite powder, which will burn violently during the pouring of molten iron and produce a large amount of gas; The moisture contained in green sand suddenly expands in volume under the action of high-temperature metal liquid, and the water changes from liquid to superheated water vapor at 1360 ℃, producing a large amount of gas. The large amount of gas generated instantly by these two causes a sudden increase in the pressure inside the mold cavity. If the exhaust is not smooth and the combustion is not sufficient, choking and explosion phenomena will occur, which is one of the fundamental reasons for sand sticking.
2.1 Defect Description
During pouring, high-temperature molten iron is poured into the mold cavity, producing a large amount of gas. As the amount of molten iron poured increases, the air pressure inside the mold cavity increases. When the pouring of the iron filling riser is about to end, the air pressure reaches its maximum, and at this time, the space inside the mold cavity is the smallest and the air pressure is the highest. The gas will not completely burn, resulting in choking or explosion phenomena, as shown in Figure 1.
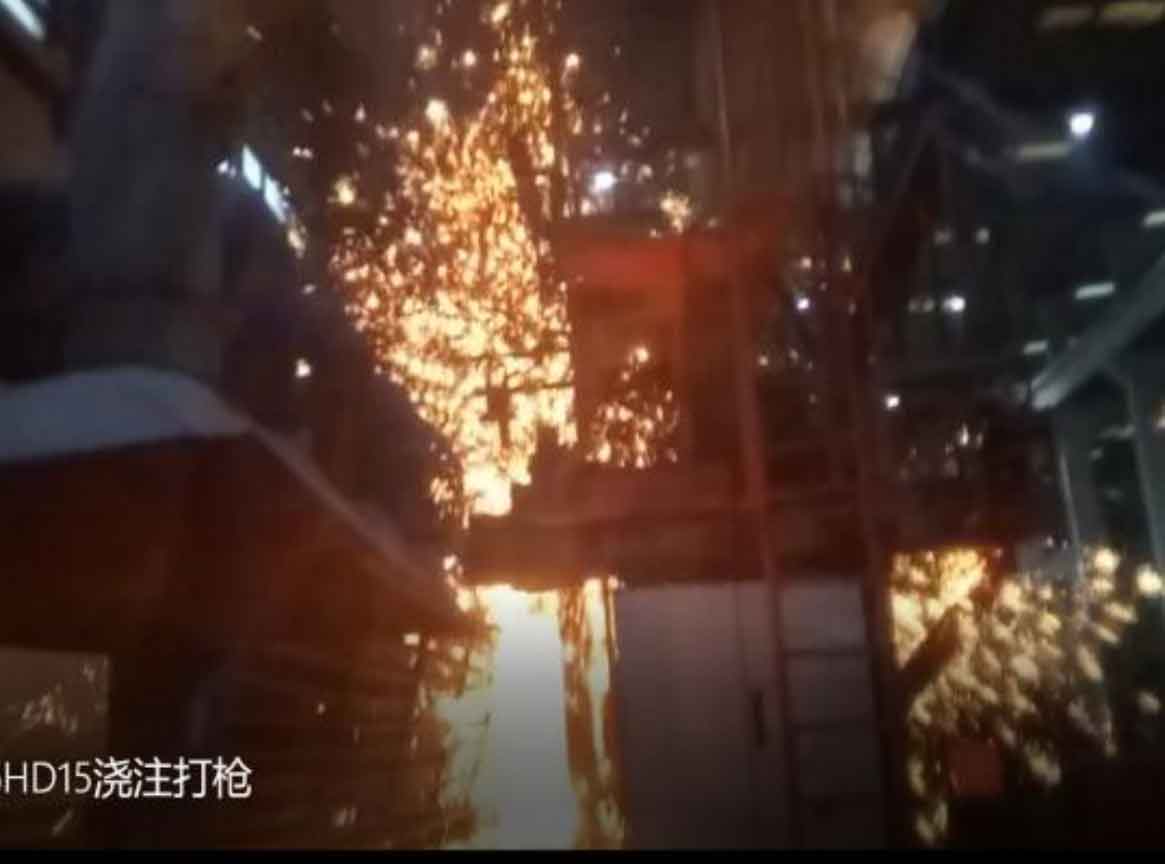
During the pouring process, a large amount of gas is produced by the molding sand, especially the gas produced by the lower mold of the mold, which will be discharged along with the metal liquid to the riser or parting surface. The more gas is produced, the more intense the molten iron will churn. At this time, the lower mold of the mold will bear greater iron extrusion pressure and iron brushing force. Our company’s wet compression strength of green sand is between 0.14 and 0.19 Mpa, and the strength of green sand molds is not very high, especially in some concave areas where the strength is very low. It cannot withstand such a large extrusion pressure and scouring force, and the molten iron will easily penetrate into the sand mold, so it is easy to produce sand sticking. When the pouring is about to fill the mold cavity, the upper part of the mold will be washed away by molten iron, and an explosion phenomenon will occur. The upper part of the mold will be hit by splashing molten iron, and the upper sand will have a crushing phenomenon, so it is easy to produce sand sticking, and even accompanied by sand hole defects. After the first surface treatment and rough polishing, there is a thick layer of sand sticking on both the upper and lower surfaces of the casting, especially at the complex concave pits, as shown in Figure 2.
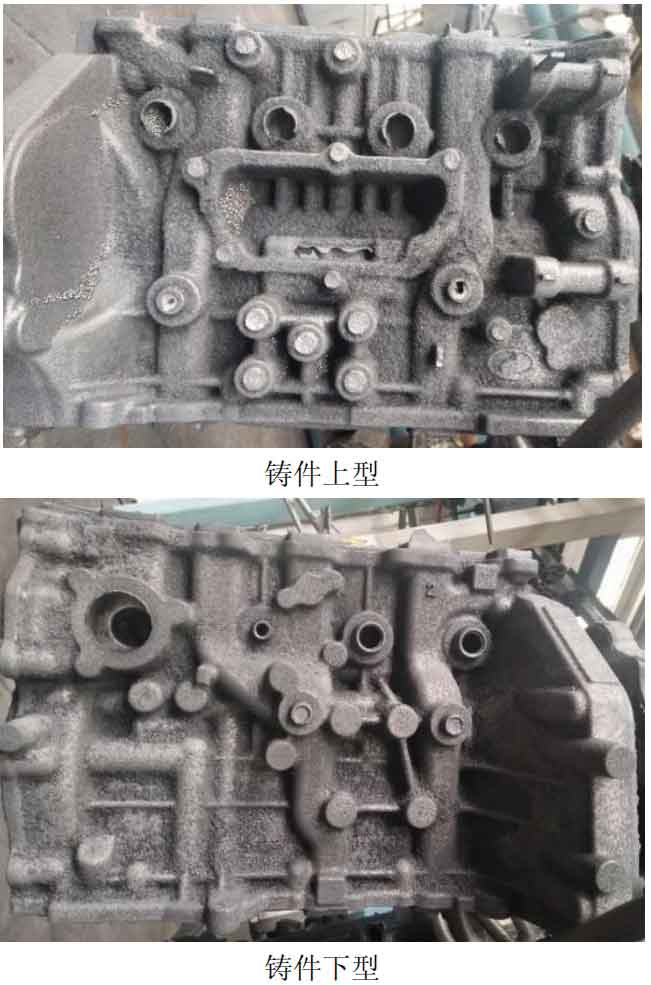
Under normal circumstances, there is generally no sand sticking on the upper part of the mold. However, in cases where the mold produces a large amount of gas, the sand sticking on the upper part of the mold is even more severe than that on the lower part. This type of sand sticking is called gas explosion sand sticking, which can only be cleaned up through a second or multiple surface treatments and polishing, or cannot be cleaned up even after multiple polishing, which will waste more human and material resources.
2.2 Analysis of causes of sand sticking defects
Based on the sand sticking situation in the lower and upper molds of the casting, combined with the phenomenon of choking and gas explosion during the pouring process, the moisture content and gas generation of the sand are generally between 2.9-3.1%, with a gas generation rate of 25-28ml/g. The moisture and gas generation of the sand are both high. Through these signs, it can be analyzed that the production of gas explosion sand sticking is caused by the high moisture and gas generation of the sand at the same time.
Under normal circumstances, the method of preventing sand sticking in green sand mainly relies on coal powder or graphite powder, which decomposes under high temperature conditions and is then coated with a carbon film on the surface of the sand particles to prevent sand sticking. If the pressure inside the mold cavity is too high, the carbon film will no longer have the desired anti sticking effect. From the perspective of reducing sand sticking defects, the most basic requirement is that the sand is in the most suitable dry and wet state, and the moisture content of the sand is as low as possible. The moisture content of the sand mainly depends on the amount of water absorbing material contained, the amount of mud in the old sand, the type and weight of auxiliary materials added during sand mixing, the sand mixing equipment and sand mixing process.
To achieve a certain strength, a certain amount of bentonite needs to be added to the molding sand; To have a certain ability to prevent sand sticking, a certain amount of coal powder needs to be added; To maintain a certain amount of moisture, a certain amount of ash powder needs to be added. When the ash powder is filled in the gaps between the sand particles, it can also resist the infiltration of high-temperature molten iron into the molding sand, and has a certain ability to prevent sand sticking. These all require a lot of moisture to moisten, which requires both the desired sand performance and the lowest possible moisture content. This requires us to use better raw materials. If the purchased bentonite and coal powder have poor quality, increasing the amount of addition will further cause the sand water to remain high. If the feeding sequence of the sand mixer is poor, the mixing and rolling effect is not strong, the sand scraper is worn, the mixing time is too short, and there are many small clay blocks in the sand that do not have a bonding effect, it will also increase the water content of the sand.
The sand to iron ratio of small products is small, and the burning loss is also small. When switching to small products, it is important to pay attention to the adjustment of the proportion of bentonite, coal powder, and ash powder added. If a higher proportion of bentonite and coal powder is added to the production of small cylinder blocks before the production of large cylinder blocks, gas explosion and sand sticking often occur when switching to large cylinder blocks. Coal powder is an effective component for preventing sand sticking. It decomposes under high temperature conditions and is coated with a carbon film on the surface of the sand particles to prevent sand sticking. At the same time, coal powder is also a hydrocarbon. In a high-temperature molten iron environment, it will burn and produce a large amount of gas, which causes a sudden increase in the pressure of the mold cavity during pouring. The exhaust of the mold cavity is generally achieved through channels such as the sprue system, parting surface, sand mold exhaust holes, and gaps between sand particles. Molten iron is injected into the mold cavity through the sprue, and the main exhaust system is the exposed riser on the mold. If a certain amount of gas is generated in the mold cavity, the more exposed or exhaust holes there are, the better the exhaust effect and the smoother the mold filling.
3. Improvement measures and experimental results
Based on the manifestation and cause analysis of defects, in order to improve gas explosion and sand sticking, it is necessary to reduce the air pressure in the small cavity. This can be improved through two aspects: first, reducing the amount of gas generated by the molding sand; The second is to strengthen the exhaust of the cavity.
3.1 Reduce the gas generation of molding sand
In response to the first point of reducing gas generation, check the moisture content and gas generation of the molding sand. The moisture content is basically between 2.9-3.1%, and the gas generation is 25-28ml/g. The moisture and gas generation of the molding sand are both high. In this situation, it is necessary to reduce the moisture content of the molding sand. While maintaining the necessary molding compactness, try to reduce the mud content of the molding sand. Therefore, the verification measures taken are: 1. Suspend the addition of ash powder and change the addition amount to 0Kg (previously added 2.4Kg); Reduce the amount of bentonite added by half to 12kg (previously added 24kg). 2. Suspend the addition of coal powder and change the amount to 0Kg (previously added 11Kg).
3.2 Strengthening the exhaust of the cavity
Regarding the second point of strengthening exhaust, while maintaining sufficient strength of the sand mold and preventing collapse of the box, it is necessary to increase the exposed riser or exhaust hole appropriately. After inspection of the exhaust system on the mold, it was found that the sand hanging area in the middle of the mold has a large amount of gas generation, but the exhaust effect is not good. Therefore, efforts should be made to strengthen the exhaust of this area. As the surface of this area is of an irregular structure, adding an exposed riser for exhaust will make it difficult to clean the subsequent post-treatment. Therefore, the measure taken is to add two exhaust holes on the back of the sand mold to enhance the gas emission inside the mold.
There are exhaust holes at the positions of the upper mold process holes, convex platform joints, and sand core heads. Overall, there are still many places where exhaust can be achieved. However, if the gas generation of the molding sand is particularly large, the pressure inside the mold cavity suddenly increases, and it is still difficult to discharge the gas smoothly in a short period of time. Therefore, increasing the exhaust system as much as possible is also helpful in reducing casting porosity defects, especially increasing the exhaust hole in the middle position of the upper mold.
To strengthen the exhaust of the upper mold, two exhaust holes with a diameter of 18mm have been added to the sand hanging area in the middle of the upper mold, as shown in Figure 3.
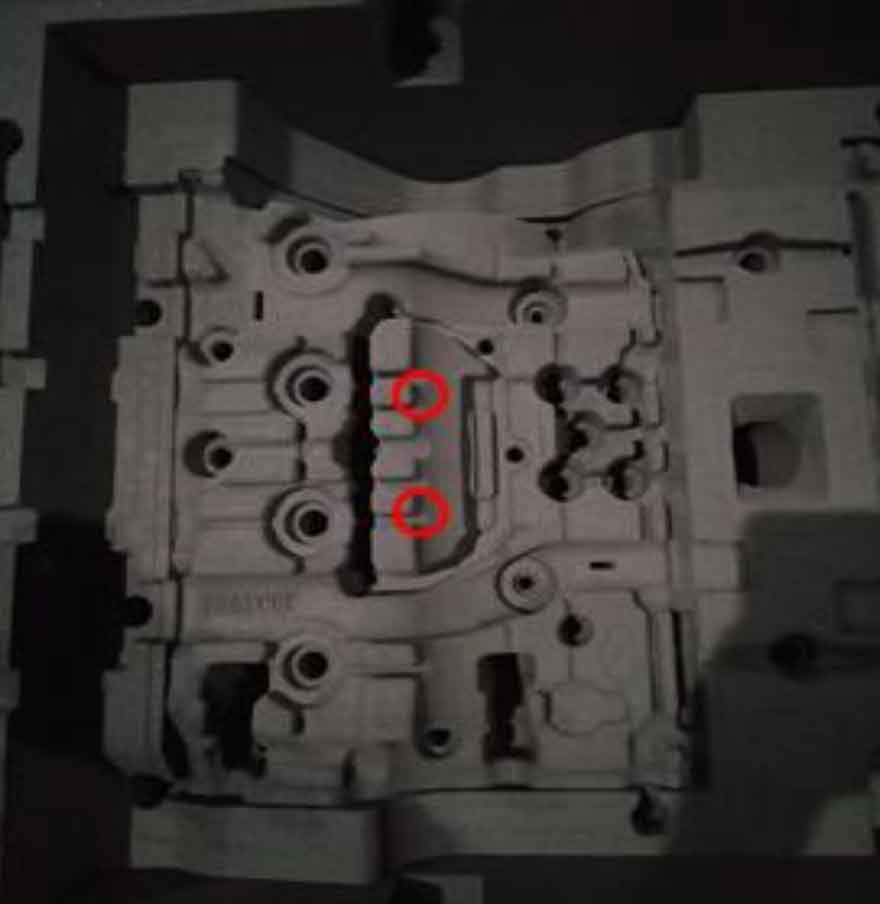
3.3 Product improvement effect
By reducing the mud content of the molding sand, adjusting the amount of coal powder added, and increasing the exhaust hole, there is no longer a choking or explosion phenomenon during casting, and the surface sand sticking situation of the product is immediately and significantly affected.
4. Conclusion
When choking or explosion occurs during the pouring of green sand, it is likely due to high moisture content in the sand, excessive addition of coal powder, or poor exhaust system. At this time, the product often produces gas explosion sand sticking, which is more severe in the upper mold than in the lower mold. To improve this sand sticking defect, it can be rectified through three aspects:
- Reduce the amount of ash powder and bentonite added to reduce the mud content of molding sand, thereby reducing the moisture content of molding sand;
- Reduce the amount of coal powder added;
- Improve the casting exhaust system and increase exhaust holes.
By reducing the gas generation of the mold and improving the exhaust system, the air pressure inside the mold can be lowered to avoid choking or explosion, thereby achieving the goal of improving the appearance of sand sticking defects.