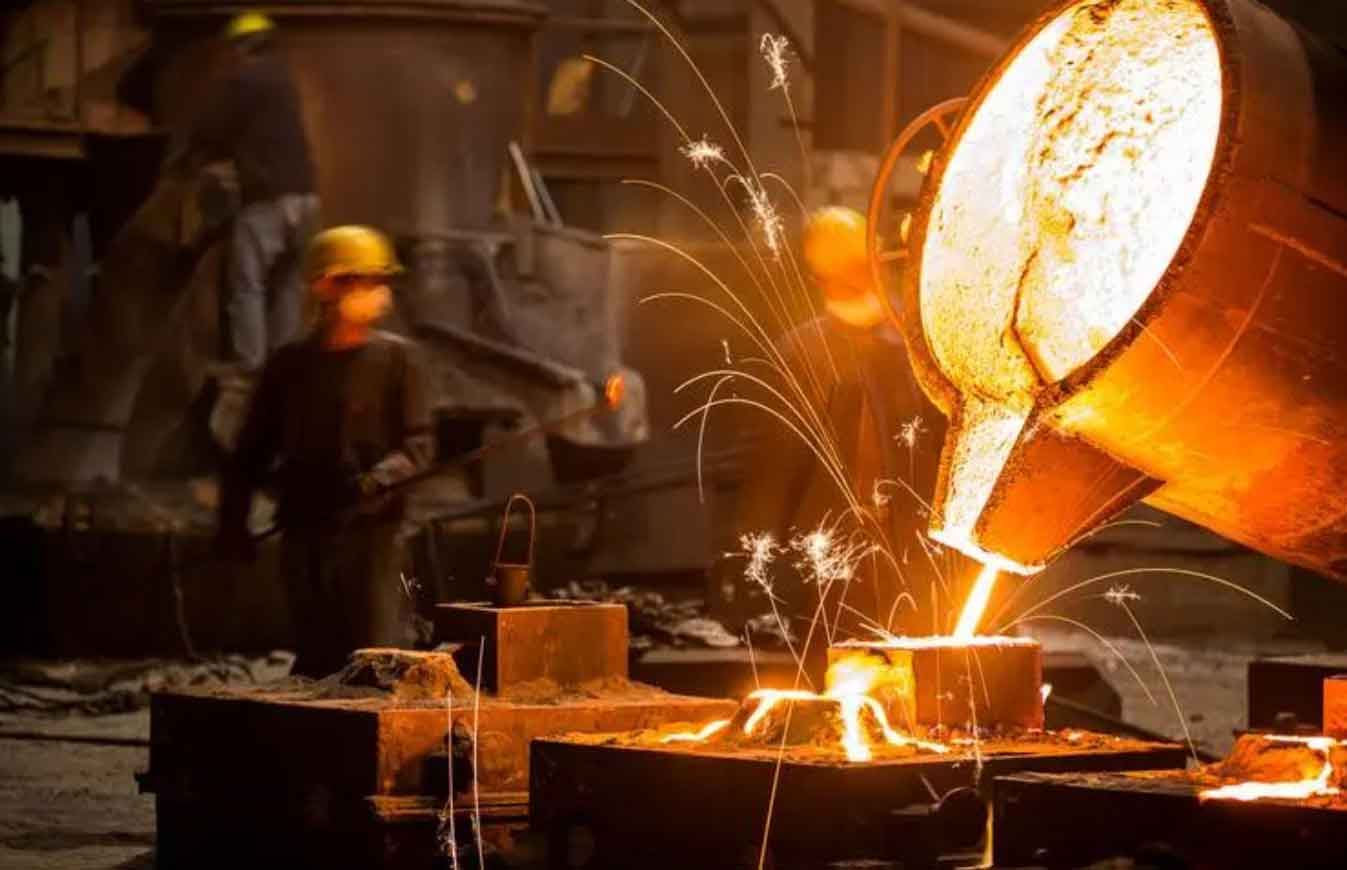
Sand casting is a traditional method of manufacturing that involves creating molds from sand to cast metal parts. This method is popular for its flexibility, affordability, and ability to produce large components. The global landscape of sand casting manufacturers is diverse, with significant activities in various countries and regions. Here are some key insights:
- North America: The United States and Canada are home to numerous manufacturers that specialize in both small-scale and large-scale production. North American companies often focus on high-quality, precision casting for automotive, aerospace, and industrial machinery.
- Europe: European countries, particularly Germany, Italy, and the UK, are known for their engineering expertise in sand casting manufacturers. European manufacturers often emphasize advanced technologies, environmental sustainability, and high-quality outputs. They serve industries like automotive, aerospace, and defense.
- Asia: Asia is a major player in the sand casting manufacturers. China and India, in particular, boast a large number of manufacturers due to their vast industrial bases and availability of skilled labor. These manufacturers typically offer cost-effective solutions and are major suppliers to both domestic and international markets.
- Emerging Markets: Countries like Brazil, Turkey, and South Africa are emerging as significant contributors to the global sand casting manufacturers. These regions benefit from growing industrialization and investment in manufacturing capabilities.
The industry is also influenced by trends such as digitalization, automation, and the use of environmentally friendly materials. Manufacturers globally are adopting new technologies such as 3D printing for creating sand molds, which allows for greater precision and reduced waste.
Overall, the global sand casting manufacturers are characterized by its extensive reach and adaptation to new technological and environmental standards, making it a crucial part of the manufacturing sector worldwide.As we continue to explore the global landscape of sand casting manufacturers, there are several additional points worth noting:
- Technology Integration: Increasingly, sand casting manufacturers are integrating advanced technologies to enhance their processes. For instance, simulation software is being used to predict casting defects and optimize mold designs before actual production. This not only saves time and costs but also improves the overall quality of sand casting manufacturers.
- Customization and Specialization: Many manufacturers are moving towards offering specialized and customized casting solutions tailored to specific industry needs. For example, specialized sand casts for high-performance applications in the aerospace industry require precise alloy compositions and exacting manufacturing standards.
- Supply Chain and Logistics: Effective supply chain management is crucial for sand casting manufacturers, especially those serving international markets. Manufacturers are optimizing their supply chains to ensure timely delivery of finished products and to mitigate the risks associated with raw material supply fluctuations.
- Environmental Considerations: Environmental sustainability is becoming increasingly important in the sand casting manufacturers. Manufacturers are exploring ways to minimize waste and recycle used materials. For instance, some are using reclaimed sand or developing processes to reduce emissions and energy consumption during casting.
- Market Challenges: Despite the robust growth, sand casting manufacturers face challenges such as competition from alternative manufacturing methods like die casting and injection molding, which can offer quicker turnaround times and finer detail in certain applications. Additionally, fluctuations in metal prices and economic downturns can impact production costs and demand.
- Future Outlook: Looking ahead, the sand casting manufacturers is poised for further evolution. The ongoing development of new materials, combined with advancements in manufacturing technology, suggests that sand casting will remain a vital manufacturing technique. Moreover, as industries such as renewable energy and electric vehicles continue to grow, there will be new opportunities for sand casting manufacturers to expand their offerings and enter new markets.
In conclusion, the global landscape of sand casting manufacturers is marked by diversity, innovation, and adaptation to changing technological and environmental standards. With its deep roots in traditional manufacturing and its eye on future advancements, the sand casting manufacturers continues to be an integral part of the global manufacturing ecosystem. As the sand casting manufacturers continues to evolve, several additional trends and innovations are shaping its future:
- Educational and Training Initiatives: There is a growing emphasis on education and training within the sand casting sector. Manufacturers are collaborating with educational institutions to develop specialized courses and training programs that focus on sand casting manufacturers, material science, and process optimization. This not only helps in bridging the skills gap but also ensures a steady pipeline of qualified professionals who can drive innovation and maintain high standards of production.
- Collaborative Efforts and Partnerships: Manufacturers are increasingly engaging in partnerships and collaborative projects with other companies and research institutions. These collaborations often aim to develop new materials, improve casting processes, or create more sustainable manufacturing practices. Such partnerships can also extend to cross-industry collaborations, where sand casting firms work with companies from other sectors to develop new applications for sand casting products.
- Regulatory Impact: Regulatory changes are also impacting the sand casting manufacturers, especially in terms of environmental compliance and safety standards. Manufacturers need to stay agile and compliant with changing regulations to avoid penalties and ensure their operations are sustainable. This includes adhering to international standards and local laws regarding emissions, waste management, and worker safety.
- Digital Marketing and Sales Channels: The digital transformation has not left the sand casting manufacturers untouched. Manufacturers are leveraging online platforms and digital marketing strategies to reach a broader audience. E-commerce for industrial products, including cast parts, is slowly becoming more prevalent, allowing manufacturers to reduce their reliance on traditional sales methods and expand their market reach globally.
- Innovation in Materials: There is ongoing research and development into new materials that can be used in sand casting manufacturers to improve the properties of the final products. Innovations such as high-performance alloys and composites are being tested for their ability to withstand extreme conditions, offer lighter weights, or provide better durability. These advancements could open new applications in sectors such as transportation, construction, and energy.
- Adaptation to Global Economic Shifts: As global economic dynamics shift, sand casting manufacturers must adapt to changing demand patterns. The rise of emerging markets, the reshoring of manufacturing activities to developed countries, and changes in global trade policies all influence where and how manufacturers operate. This requires strategic planning and flexibility to shift production as needed to take advantage of new opportunities.
In summary, the global sand casting manufacturers is not just about maintaining traditional manufacturing practices; it’s about advancing them through education, collaboration, compliance, digital transformation, and material innovation. These efforts are crucial for staying competitive in a rapidly changing industrial landscape and will determine the future direction of sand casting manufacturers on a global scale. Continuing with the evolving dynamics of the sand casting industry, here are further aspects that highlight its ongoing adaptation and innovation:
- Automation and Robotics: Automation is increasingly becoming integral to sand casting manufacturers. Robotics and automated machinery are used for tasks such as sand mixing, mold making, and casting pouring. This not only improves efficiency and consistency in production but also reduces the physical strain on workers, leading to safer work environments. As technology advances, we can expect even greater integration of robotics, potentially automating the entire sand casting manufacturers from start to finish.
- Quality Control Technologies: Advanced quality control technologies are being employed to ensure the integrity and precision of sand cast products. Techniques such as X-ray imaging, 3D scanning, and real-time monitoring sensors are used to detect defects and inconsistencies that could affect the performance of the final product. These technologies allow for immediate corrections during the manufacturing process, thereby reducing waste and increasing the reliability of the output.
- Sustainability Initiatives: The push towards sustainability is driving sand casting manufacturers to explore more eco-friendly practices. This includes the use of biodegradable binders in sand molds, the recovery and recycling of used sand, and the optimization of energy consumption within sand casting manufacturers. Additionally, some companies are looking into ways to offset their carbon footprint by investing in renewable energy sources and carbon capture technologies.
- Global Supply Chain Optimization: The global nature of the sand casting manufacturers requires an efficient and resilient supply chain. Manufacturers are focusing on optimizing their logistics to handle disruptions more effectively, such as those experienced during global events like the COVID-19 pandemic. This involves diversifying suppliers, investing in local resources to reduce dependence on distant markets, and utilizing digital tools to manage supply chain risks.
- Customer-Centric Approaches: As markets become more competitive, manufacturers are adopting more customer-centric approaches to differentiate themselves. This includes offering end-to-end services from design and prototyping to final production and even aftermarket support. By engaging closely with customers and understanding their specific needs, manufacturers can develop more tailored products and forge stronger relationships, which can lead to repeat business and long-term loyalty.
- Future Challenges and Opportunities: The sand casting manufacturers faces several challenges, including the need for continuous technological upgrades, managing environmental impacts, and navigating complex global trade environments. However, these challenges also present opportunities for innovation and growth. As industries such as electric vehicles, aerospace, and renewable energy continue to expand, there will be new demands for complex, high-quality cast components, driving further evolution in sand casting technologies and practices.
In essence, Sand casting manufacturers are at a crossroads of tradition and innovation. While it relies on age-old techniques, it is also at the forefront of industrial technology and environmental practices. Its ability to adapt and evolve will continue to play a critical role in its sustainability and relevance in the modern manufacturing landscape.
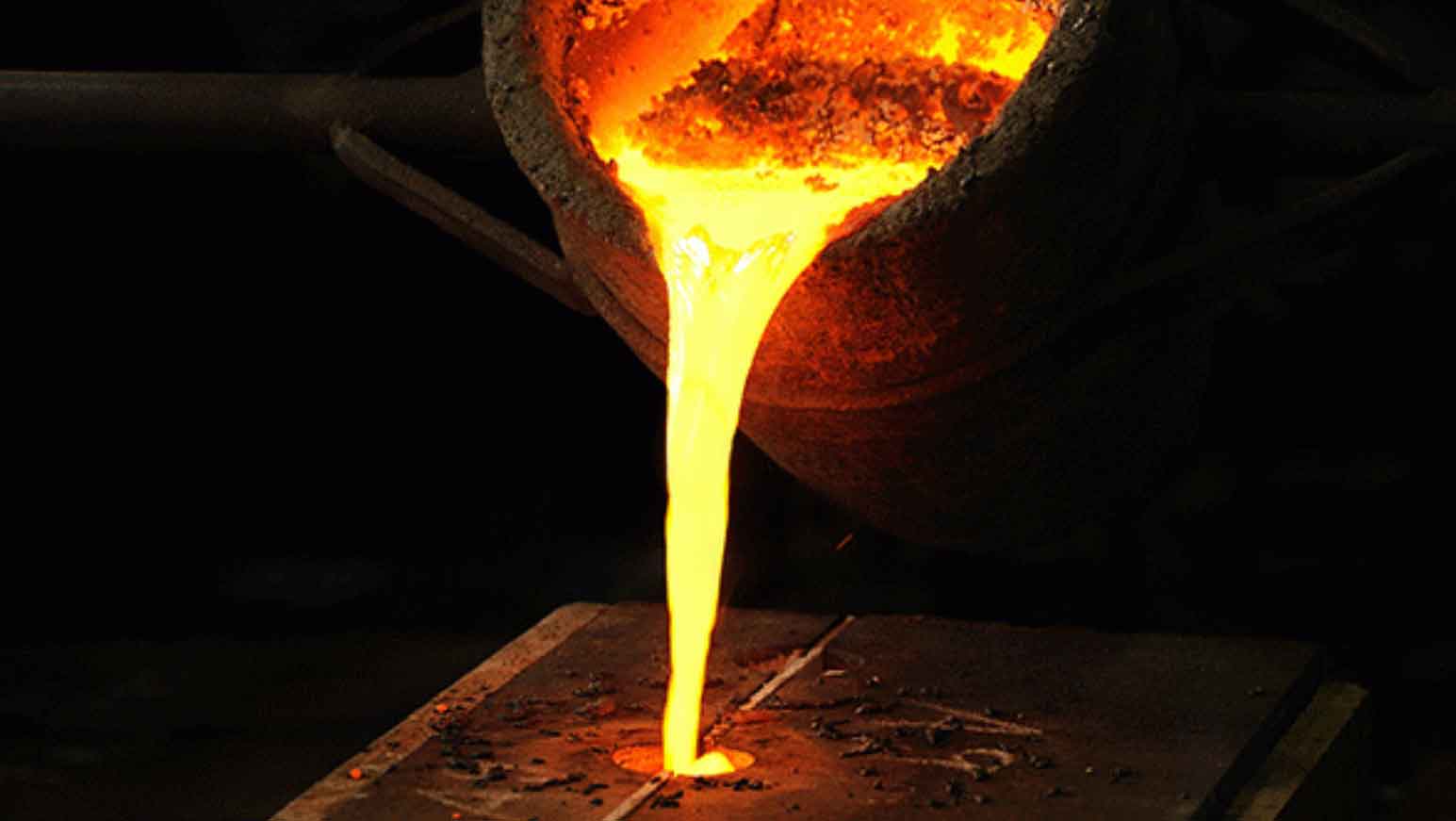
As we further delve into the future prospects and ongoing developments within the sand casting manufacturers, several additional strategic areas come into focus:
- Interdisciplinary Collaborations: The sand casting manufacturers is increasingly engaging in interdisciplinary collaborations that combine expertise from different fields such as materials science, engineering, and digital technology. These collaborations aim to push the boundaries of what can be achieved with sand casting manufacturers, from developing new alloy compositions to integrating IoT (Internet of Things) technologies for smarter production lines. Such synergistic partnerships can accelerate innovation and lead to breakthroughs that enhance both product quality and manufacturing efficiency.
- Custom Tooling and Machinery Development: As product specifications become more complex, there is a growing demand for custom tooling and machinery tailored to specific sand casting manufacturers. Manufacturers are investing in the development of specialized equipment that can handle unique alloys, intricate mold designs, and precise casting requirements. This not only boosts their capability to produce high-quality parts but also positions them as leaders in niche markets.
- Expansion into New Markets: Sand casting manufacturers are exploring opportunities to expand into new geographic and sectoral markets. For example, as renewable energy solutions like wind turbines gain popularity, there is a higher demand for large, durable metal components that can be efficiently produced using sand casting. Sand casting manufacturers are also looking at industries such as medical technology and consumer electronics, where precision and material integrity are crucial.
- Workforce Development and Retention: With the technical complexity of modern sand casting manufacturers, there is a critical need for skilled labor. Manufacturers are focusing on workforce development through continuous training programs and attractive retention strategies. This includes fostering a culture of innovation, offering competitive benefits, and providing opportunities for career advancement within the company.
- Adapting to Regulatory Changes: As environmental and safety regulations continue to tighten, sand casting manufacturers must stay proactive in adapting to these changes. This involves not only compliance but also actively participating in regulatory discussions to ensure that new policies are feasible and that they reflect industry capabilities and constraints. Staying ahead of regulatory changes can prevent operational disruptions and maintain market competitiveness.
- Enhanced Customer Engagement: In an era of digital connectivity, enhancing customer engagement through digital platforms is becoming essential. Manufacturers are using technologies like AR (Augmented Reality) and VR (Virtual Reality) to provide virtual tours of their facilities, simulate sand casting manufacturers, and showcase product testing. This level of transparency and interactive customer service can significantly enhance client satisfaction and trust.
- Long-Term Sustainability Goals: Finally, aligning with global sustainability goals is crucial for the future viability of sand casting manufacturers. This means setting long-term objectives to reduce environmental impact, such as achieving net-zero emissions, minimizing waste through circular economy practices, and ensuring sustainable resource use. These goals not only comply with global standards but also resonate with environmentally conscious customers and stakeholders.
The sand casting manufacturers, thus, is a blend of maintaining robust traditional practices and embracing cutting-edge innovations. By focusing on technological advancements, customer needs, and sustainability, the industry is well-positioned to meet the challenges of the future while continuing to serve as a foundational manufacturing process in numerous sectors.