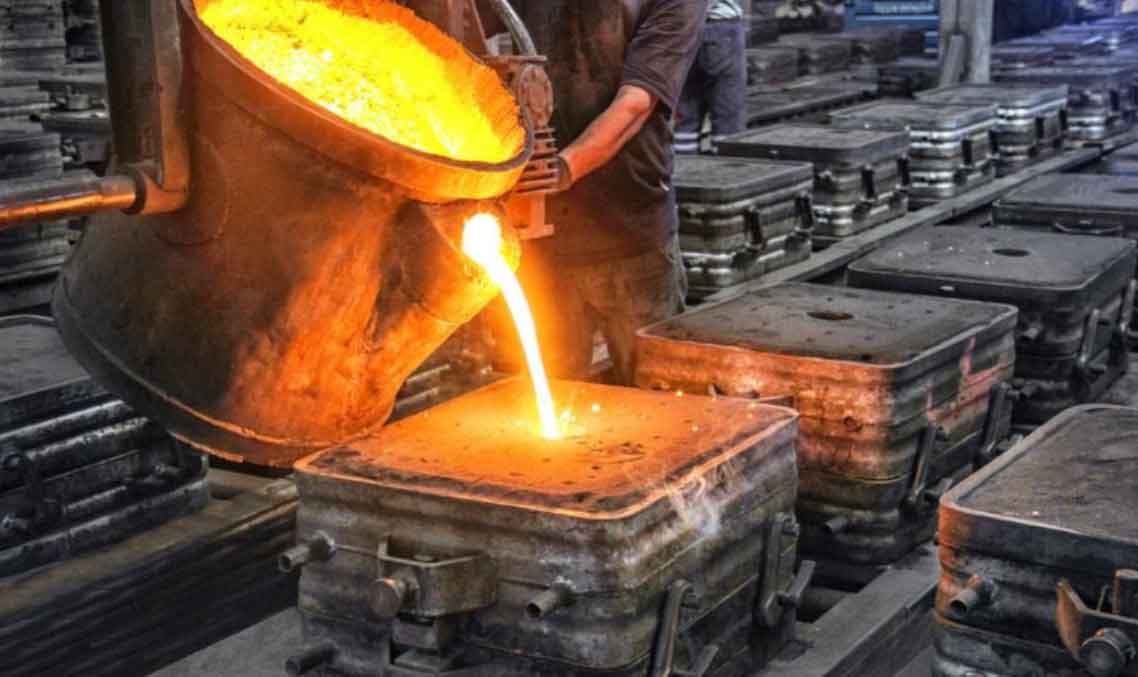
Meeting tight deadlines in sand casting manufacturing requires efficient planning, streamlined processes, and effective coordination among various stakeholders. While expedited production can pose challenges, implementing the right strategies can help manufacturers deliver high-quality castings on time. Here are some strategies for expedited sand casting manufacturing:
1. Collaborative Design and Engineering:
- Involve design engineers, casting experts, and the sand casting manufacturer in collaborative design and engineering from the outset. This ensures that the design is optimized for manufacturability, reducing the need for extensive iterations.
2. Rapid Prototyping:
- Utilize rapid prototyping techniques, such as 3D printing, to quickly produce and evaluate patterns. This allows for design validation and iterations without the need for traditional pattern-making lead times.
3. Prepared Tooling and Patterns:
- Maintain a library of pre-made tooling and patterns for common components or frequently requested parts. This reduces lead times and allows for rapid production when orders are received.
4. Automation and Robotics:
- Leverage automation and robotics for pattern-making, mold assembly, and material handling. Automated processes can significantly reduce the time required for these tasks, improving overall production efficiency.
5. Efficient Sand Preparation:
- Implement efficient sand preparation and conditioning processes to ensure the availability of high-quality sand for molding without delays.
6. Streamlined Gating and Risering Design:
- Optimize gating and risering designs using casting simulation software. This ensures that the casting process is efficient and minimizes the risk of defects, reducing the need for rework and saving time.
7. Effective Scheduling and Planning:
- Develop a well-structured production schedule and plan to allocate resources effectively and meet specific milestones. Regularly review and adjust the plan as needed to address any unforeseen challenges.
8. Material Availability:
- Ensure a reliable supply of materials, such as metal alloys and additives, to avoid production delays. Collaborate closely with suppliers to manage material lead times effectively.
9. Parallel Processing:
- Where possible, implement parallel processing to handle multiple casting tasks simultaneously. For example, prepare molds for one casting while pouring another, reducing the overall production time.
10. Skilled Workforce:
- Employ a skilled and experienced workforce familiar with sand casting processes and equipment. Proper training and cross-training can ensure that tasks are performed efficiently.
11. Real-Time Monitoring and Communication:
- Implement real-time monitoring of the casting process to identify any potential issues early. Maintain clear communication channels between the design team, the casting manufacturer, and any other stakeholders to address concerns promptly.
12. Quality Control and Inspection:
- While working under tight deadlines, maintain stringent quality control measures to ensure that the produced castings meet the required specifications.
By combining these strategies, sand casting manufacturers can expedite production while maintaining the quality and integrity of the castings. Effective collaboration, streamlined processes, and a focus on efficiency are essential for meeting tight deadlines without compromising on the final product’s quality.