The microhardness of the middle part of the rim and the inner rim near the spinning wheel area (upper) and near the core mold area (lower) in different forming schemes were tested. Randomly select multiple values from the above three areas. After removing the maximum and minimum values, calculate the average microhardness of each area.
The average Vickers hardness of the inner flange under different forming schemes is shown in the figure. A356 aluminum alloy α- Al is softer than eutectic silicon particles. If the sampling point is in different phases, the hardness will change. The microhardness distribution in the near spinning wheel area (upper), middle (middle) and near core mold area (lower) reflects the deformation uniformity. Sha et al. pointed out that the solution treatment made the irregular eutectic silicon particles spheroidized, dissolved Mg2Si to form a uniform supersaturated solid solution. During the subsequent aging treatment, the hardness of the Mg-Si precipitated phase precipitated in the A356 matrix increased rapidly. The average microhardness decreases with the increase of the refinement of eutectic silicon phase caused by plastic strain, and the reduction of silicon size helps to improve the mechanical properties of the alloy.
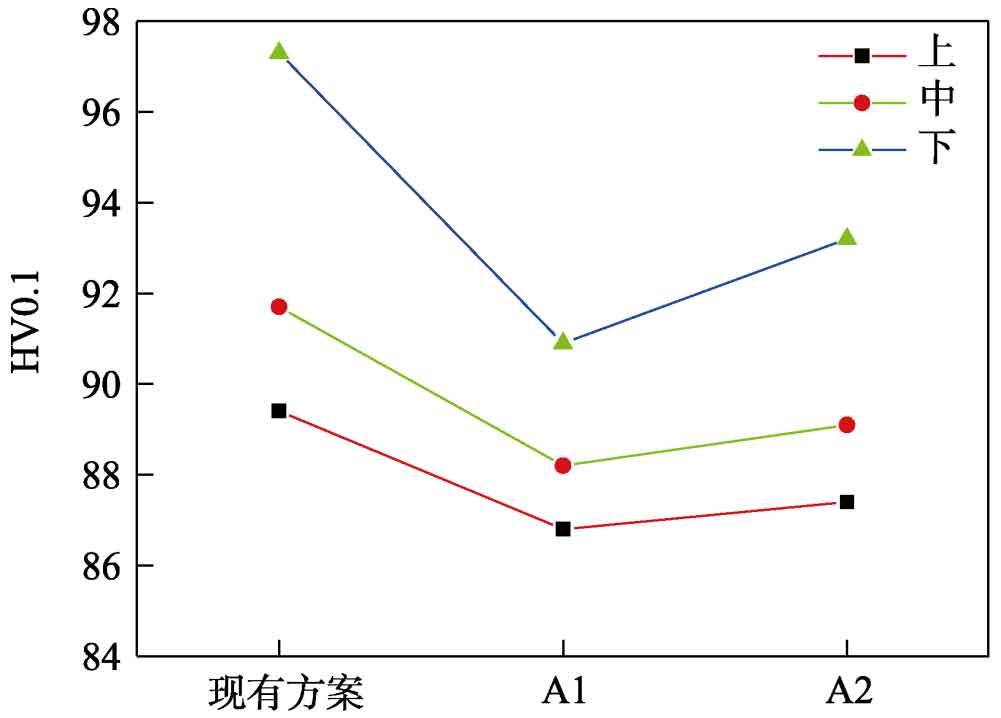
It can be seen from the figure that the microhardness of the lower region is the largest, followed by the central region, and the upper region is the smallest. This means that the tissue streamline near the upper part of the spinning wheel is obvious, and the silicon dispersion is better. The data shows that the hardness difference between the three layers of the inner flange under the forming scheme A1 is the smallest, so the forming scheme A1 can obtain more uniform deformation.