The mechanical parameters of the interface include two aspects: elastic parameters and plastic parameters. The young’s modulus of the integrated surface can be obtained from the young’s modulus of each rough surface by using the following classical formula,
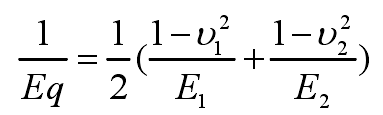
The Poisson’s ratio of two rough surfaces is v = 0.3. The young’s modulus of rough surface 1-a356 is E1 = 97.8-0.16t GPA, and that of rough surface 2-h13 is E2 = 207 GPa. Therefore, the young’s modulus of the interface is a function EQ = EQ (T), where t is the average temperature of the casting die interface.
The yield strength of the interface is determined by the lowest of the two rough surfaces. Therefore, the yield strength of the interface is rep = 18.3 MPa.
Since the length of the sample used to measure the profile of the rough surface is 4 mm, the nominal length of the contact surface is 4 mm. Because the height and curvature radius of the convex vertex of rough surface change with the different convex, the two parameters are taken as variables. According to the classical deformation theory, the deformation of contact surface can be divided into three parts: elastic deformation, elastic-plastic deformation and plastic deformation. The interface spacing “d” is defined as the distance between the smooth rigid surface and the plane z = 0 where the average height of the convex vertices of the rough deformable integrated surface is located, as shown in the figure 1.
Therefore, local contact occurs only when the vertex distance Z of the bulge is greater than the interface distance “d”. The deformation of the bulge is δ = Z – D, as shown in Figure 1.
In order to obtain the resultant force due to contact deformation caused by convex rough surface, the following formula is used for calculation,
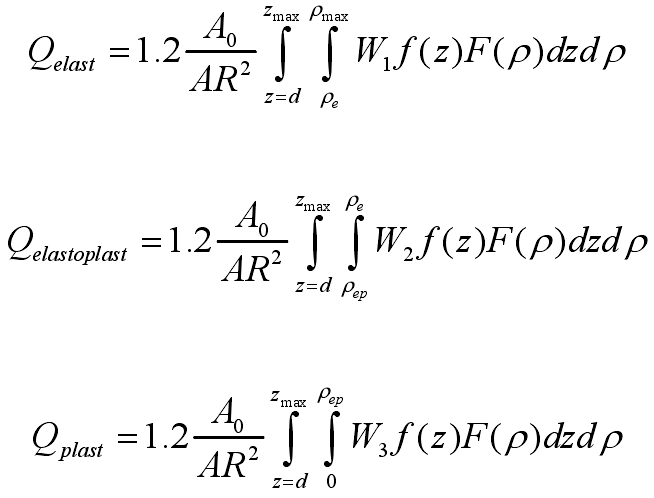
Where,
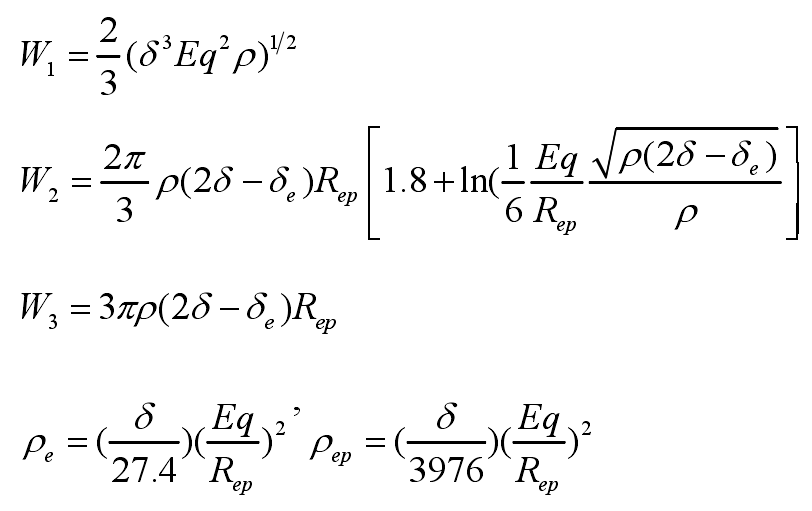
Zmax and ρ Max are the maximum values of the height and curvature radius of the convex vertex in the conformal surface. The total load can be obtained by the following formula,

The interface contact pressure is defined as Q / A0. Because the mechanical parameters of the integrated surface are related to the average temperature of the casting die interface, the relationship between the interface contact pressure and the interface spacing at different temperatures is shown in Figure 2.
Because of the non-uniformity of rough surface, the size of contact area and non-contact area need to be distinguished by the real contact area. Through the classical deformation theory, the area of the real contact part can be determined according to the deformation and stress. The calculation formula is as follows,
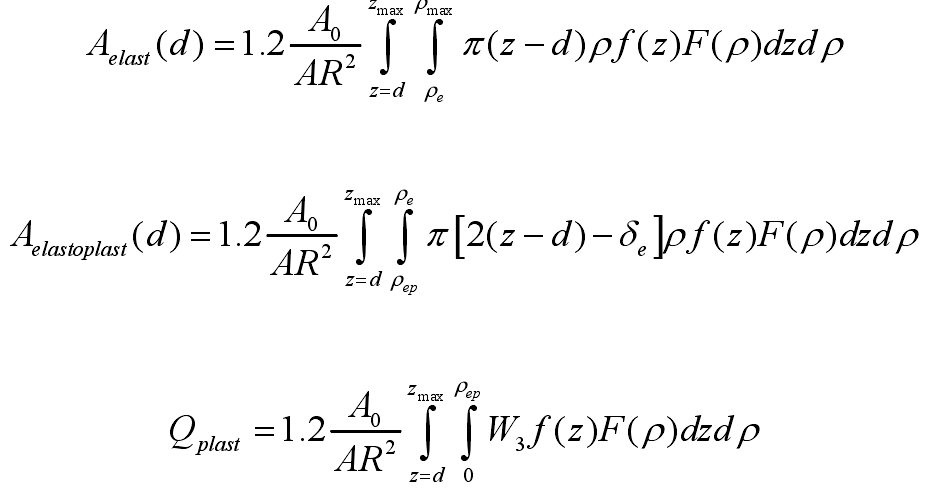
Therefore, the real contact area is as follows,

Figure 3 shows the relationship between the ratio of real contact area to nominal contact area and the interface spacing.
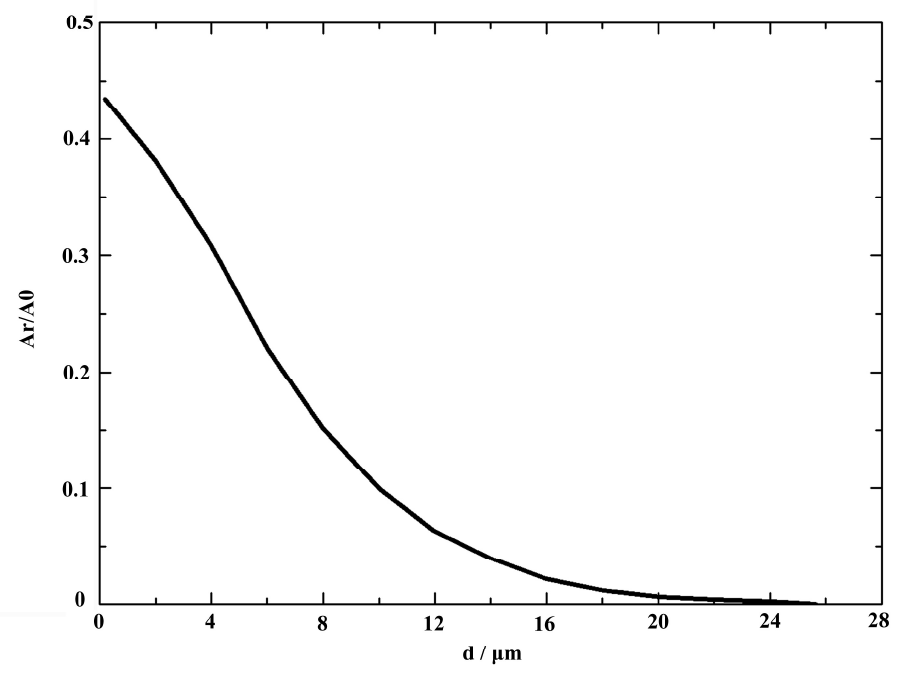