The microstructure of grey cast iron samples with three different contents of scrap steel is shown in Fig. 1 and Fig. 2. In 1 # and 2 # samples, due to the addition of a certain amount of return material to the cast iron raw material, the graphite in the return material can not be completely dissolved in the molten iron during the smelting process, which has a certain heritability, which is the main reason for the large amount of block graphite in the cast gray iron samples. At the same time, the long strip type a graphite in 1 # and 2 # samples are mostly flat and large in length, most of which are 250-350 μ m. The graphite grade is grade 3 (Fig. 1 (a), (b)), which accounts for about 70% of the total graphite content. In contrast, 100% scrap steel and carburizing agent were added to 3 sample, without reheating material. At this time, the molten iron from scrap smelting is seriously carbon poor, and the carburizing agent is added into it. On the one hand, there is a large density difference between the carburizing agent and molten iron, resulting in the upward floating of the carburizing agent, that is, the distribution of the carburizing agent particles in the molten iron is uneven; Secondly, the distribution of carbon elements dissolved in molten iron is also uneven, so there are carbon poor and carbon rich regions in molten iron, which provides favorable composition fluctuation conditions for the nucleation and growth of graphite in molten iron. During the casting and solidification of molten iron, the nucleation and growth of graphite in the carbon rich zone have compositional advantages, while the melting and exothermic heat of the carburizer leads to the higher temperature in the carbon rich zone and the lower temperature in the carbon poor zone, and the temperature of each micro zone in the molten iron is uneven, This provides favorable energy conditions for the nucleation and growth of graphite in molten iron. Due to the rapid melting of the carburizer, the structure of C in molten iron is more uniform and stable, which in turn provides favorable structural conditions for the nucleation and growth of graphite in molten iron. Therefore, most of the graphite formed in the 3 sample added with 100% scrap is fine, curved short-film A-type graphite, The length is mostly 150-200 μ M (grade 4 graphite), which accounts for about 50% of the total graphite. Due to different crystallization conditions, cast iron contains a small amount of D-type graphite (Fig. 1 (c)).
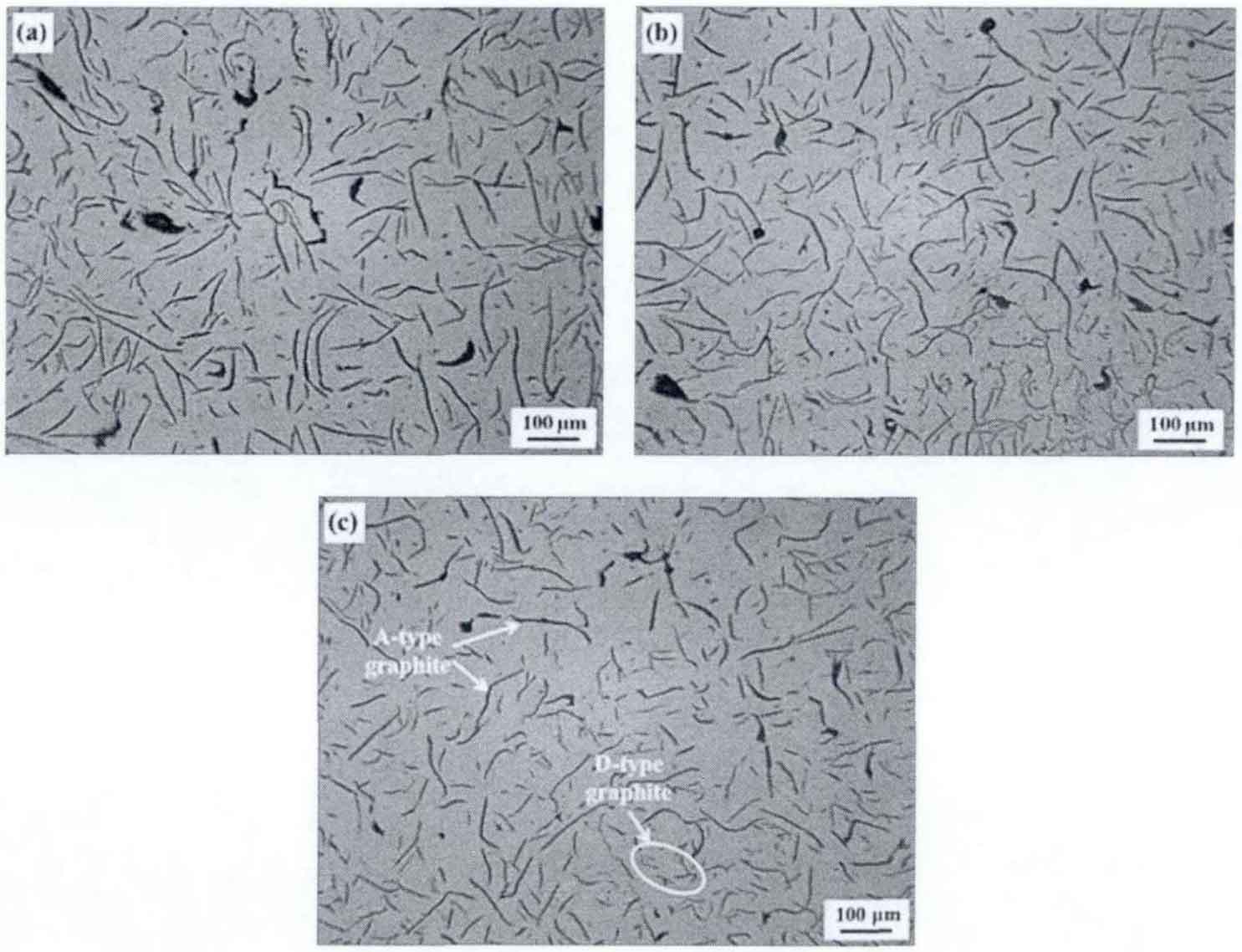
The morphology and distribution of pearlite matrix and hard inclusion phase in gray cast iron with different amount of scrap are obviously different. As shown in Fig. 2 (a) and (b), pearlite in sample 1-2 has coarsening phenomenon to a certain extent, with large lamellar spacing and large white ferrite distributed between them. Although the plasticity and toughness of ferrite structure are good, its strength and hardness are relatively low, and its comprehensive properties are poor. Therefore, the formation of these large ferrites has a very adverse impact on the microstructure uniformity and mechanical properties of gray cast iron. In addition, the number of inclusions (tin, MNS, etc.) in sample 1-2 is relatively large, and the size is slightly larger. They are mostly distributed at the pearlite interface, which will also have an adverse impact on the mechanical properties of gray cast iron.
The raw materials of cast iron, mainly the returned materials, the Ti impurities contained in the auxiliary materials and the ferromanganese added as auxiliary materials are the main sources of tin, MNS and other inclusion phases in gray cast iron. A certain amount of recycled materials are added to the ingredients of 1-2 samples. These hard inclusion phases in the recycled materials cannot be completely melted during the remelting process. Due to their heredity, it is possible to form large-scale hard phases. This will not only reduce the mechanical properties of the casting, but also aggravate the tool wear of the machined surface of the casting during machining.
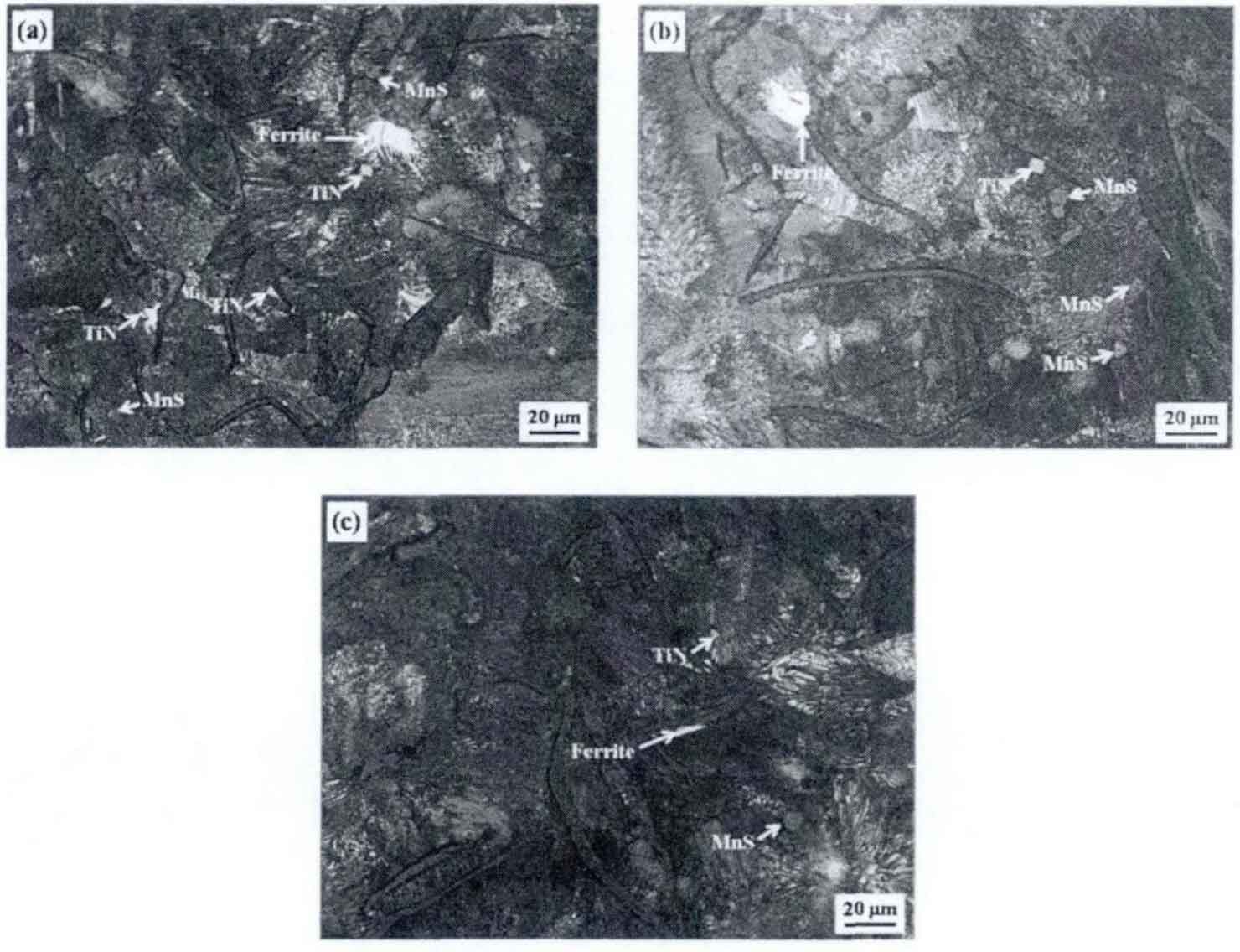
In comparison, the pearlite structure in sample 3 has been significantly refined, the content has also increased, the number of large ferrite is small, and the content of hard inclusion phase is significantly reduced, and the size is relatively small (Fig. 2 (c)). In a word, the solidification process of molten iron becomes more favorable due to the improvement of raw material composition in the 3 sample with 100% scrap added, so its microstructure has been significantly improved.