The inheritance of tin in raw and auxiliary materials and the introduction of Ti element will increase the tin particles in gray iron castings, and the influence of tin particles on their microstructure and properties is complex. As a gray cast iron casting, the scorching process and solidification process are two very important processes in material research. Therefore, we need a comprehensive analysis of its growth mechanism and action mechanism.
Nowadays, gray cast iron cylinder bodies are generally low alloy cast iron. In order to improve the structure and properties of the cylinder block, a certain amount of alloy is usually added selectively in the molten iron smelting process. These alloying elements and other elements will have different effects on the melting and solidification of gray cast iron. Referring to the experience of International Foundry Association and actual production, the liquidus temperature (TL) and solidus temperature (TS) of gray cast iron system can be estimated by the following formula:
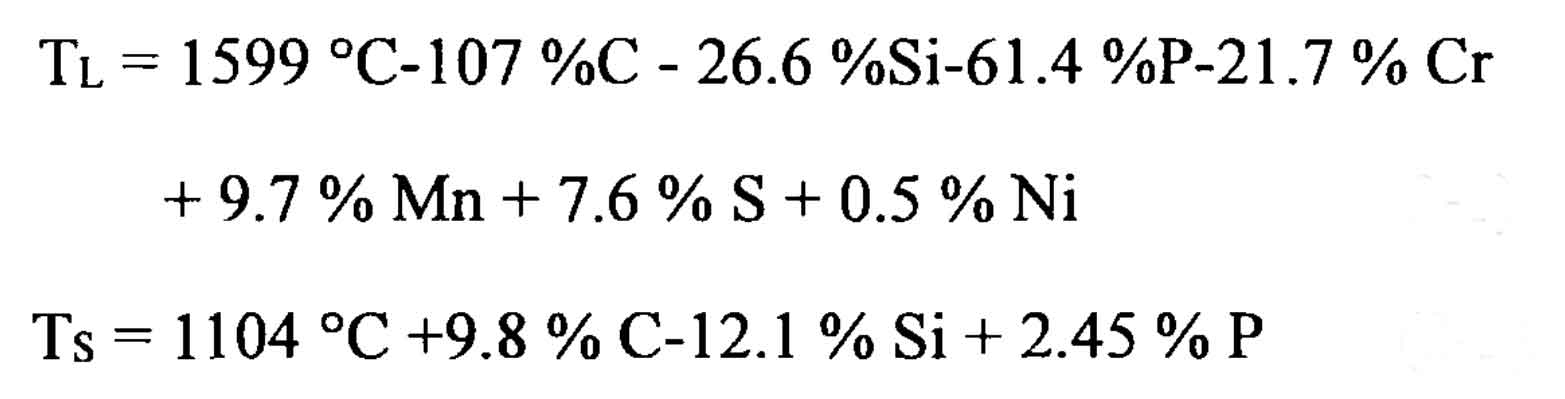
Sample | C | Si | Mn | P | S | Cu | Cr | Ti | Al | Sn | Pb | Fe |
1# | 3.34 | 1.89 | 0.667 | 0.028 | 0.087 | 0.018 | 0.223 | 0.044 | 0.007 | 0.074 | 0.0010 | Other |
2# | 3.36 | 1.81 | 0.665 | 0.026 | 0.090 | 0.026 | 0.193 | 0.049 | 0.007 | 0.077 | 0.0009 | Other |
3# | 3.32 | 1.80 | 0.644 | 0.027 | 0.088 | 0.027 | 0.217 | 0.043 | 0.007 | 0.075 | 0.0006 | Other |
Average | 3.34 | 1.83 | 0.665 | 0.027 | 0.088 | 0.023 | 0.211 | 0.045 | 0.007 | 0.075 | 0.0008 | Other |
In order to analyze the solidification process of grey cast iron, we sampled the melt of grey cast iron in the insulation pouring furnace (before pouring) and tested it through the thermal analyzer and direct reading spectrometer. The solid-liquid phase line temperature, C element and other alloy elements during the solidification process of grey cast iron can be obtained. Molten iron is sampled three times in each furnace. The test data are shown in Table 1. Then, the measured molten iron composition results are respectively brought into the formula, from which the solid-liquid phase line temperature during the solidification process of molten iron in each furnace can be estimated (Table 2). When the thermal analyzer is used to measure the solidification curve, a certain amount of antimony (sb) is usually added to the sample cup. According to the above, we know that the addition of sb will change the composition of the test molten iron, thus changing the solidification and crystallization process of gray cast iron. Therefore, compared with the calculated results, the test results of the thermal analyzer will deviate to a certain extent, but the deviation generally does not exceed ± 13 ° C, meeting the test requirements.
Sample | TL (estimated value) | TS (estimated value) | TL (test value) | TE (test value) |
1# | 1191.9 | 1113.9 | 1210.6 | 1124.8 |
2# | 1192.6 | 1115.1 | 1209.3 | 1125.6 |
3# | 1196.4 | 1114.7 | 1211.7 | 1124.3 |
Average | 1193.6 | 1114.6 | 1210.5 | 1124.9 |