Casting shrinkage is a common challenge faced in the casting process, particularly in high-precision applications where dimensional accuracy and surface finish are critical. Shrinkage defects can compromise the functionality, reliability, and aesthetics of cast components. This article explores various strategies and techniques to mitigate casting shrinkage defects specifically in high-precision applications.
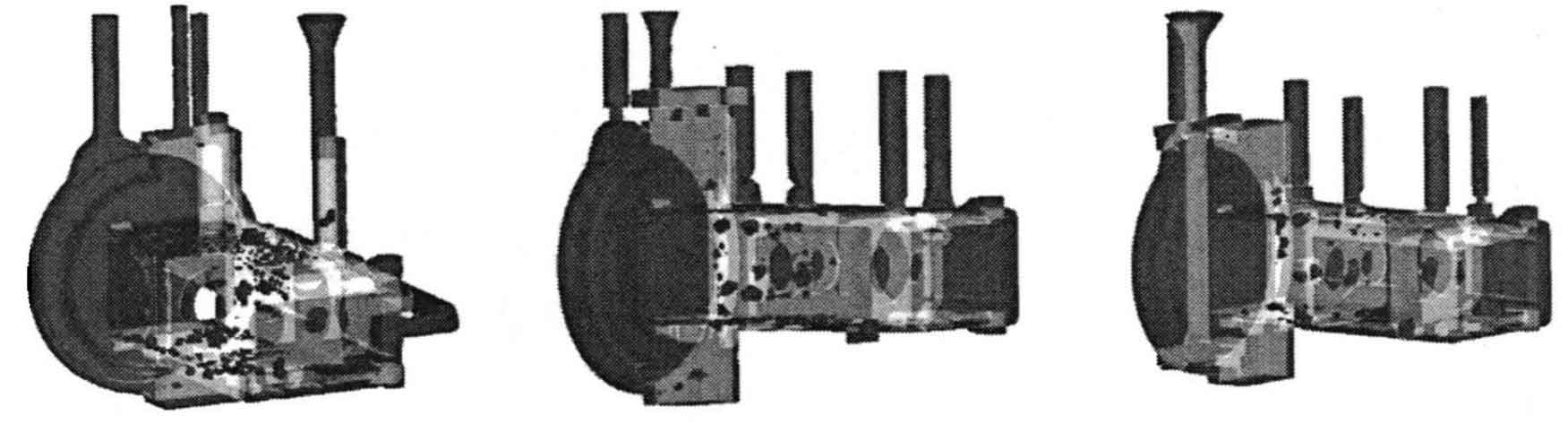
- Optimized Design and Mold Preparation: Careful consideration of the component’s design and mold preparation is crucial in minimizing shrinkage defects. Factors such as proper gating and riser design, appropriate wall thickness, and effective use of chill plates or insulating materials can help control the cooling rate and reduce shrinkage tendencies.
- Mold Material Selection: The choice of mold material can significantly impact shrinkage control. Using materials with low thermal conductivity can slow down the cooling rate and allow for more controlled solidification, reducing the risk of shrinkage defects. Additionally, the mold material should have good dimensional stability to prevent distortion during solidification.
- Rigorous Process Monitoring and Control: Implementing robust process monitoring and control systems is essential to detect and address shrinkage defects in real-time. Temperature sensors, thermal imaging, and other monitoring techniques can provide valuable insights into the cooling and solidification process, allowing for prompt adjustments to minimize shrinkage defects.
- Optimized Pouring and Solidification Parameters: Proper control of pouring temperature, pouring rate, and solidification time is crucial in mitigating shrinkage defects. These parameters should be optimized to ensure a balanced feeding system, sufficient molten metal flow, and controlled solidification, reducing the likelihood of shrinkage defects.
- Use of Shrinkage-Compensating Materials: Some advanced casting materials, such as alloys with self-compensating properties, can help mitigate shrinkage defects. These materials are formulated to undergo controlled expansion during solidification, compensating for the volumetric shrinkage and reducing the occurrence of defects.
- Heat Treatment and Stress Relief: Post-casting heat treatment processes, such as stress relief annealing, can help alleviate residual stresses and reduce the risk of shrinkage defects. Controlled heat treatment can improve the material’s microstructure and mechanical properties, enhancing its resistance to shrinkage.
- Advanced Simulation and Modeling: Utilizing computer-aided casting simulation software can provide valuable insights into the solidification process and predict the occurrence of shrinkage defects. By simulating different process parameters and analyzing the results, foundries can optimize the casting process to minimize shrinkage defects in high-precision applications.
- Non-Destructive Testing: Incorporating non-destructive testing techniques, such as X-ray or ultrasonic inspection, can detect internal shrinkage defects that may not be visible on the surface. Early detection allows for timely remedial actions, preventing further propagation of defects and ensuring the integrity of the cast components.
- Continuous Improvement and Knowledge Sharing: Foundries should promote a culture of continuous improvement and knowledge sharing. Lessons learned from past experiences, customer feedback, and collaboration with industry experts can help identify areas for improvement, develop best practices, and enhance shrinkage control in high-precision casting applications.
In conclusion, mitigating casting shrinkage defects in high-precision applications requires a holistic approach encompassing design optimization, process control, material selection, and advanced simulation techniques. By implementing these strategies and continuously improving casting processes, foundries can achieve superior dimensional accuracy, surface finish, and overall quality in high-precision cast components. This, in turn, ensures the reliability and performance of the components in demanding applications.