Casting defects can significantly affect the performance, reliability, and lifespan of a product. As such, overcoming these defects is paramount in enhancing the product’s performance. This article explores common casting defects and how to mitigate them for improved product performance.
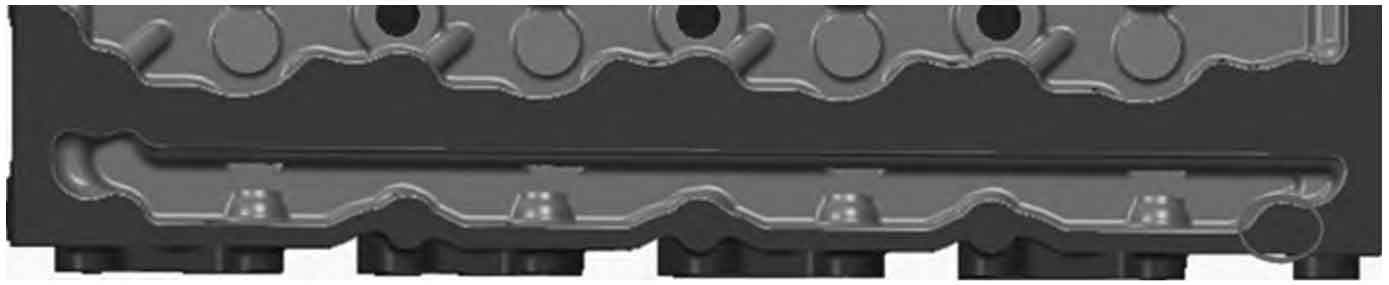
- Porosity: Porosity, which manifests as voids or holes within the cast part, can lead to a reduction in product strength and durability. Addressing porosity involves degassing techniques, improving venting in the mold, and controlling cooling to prevent shrinkage porosity.
- Shrinkage Defects: Shrinkage defects occur when different sections of the casting solidify at different rates, leading to volume reduction and causing voids or cracks. Overcoming this defect involves strategic mold design, ensuring uniform cooling, and the correct placement of risers.
- Gas Defects: Trapped gases can lead to defects within the cast. Efficient venting of the mold, maintaining correct pouring temperatures, and utilizing degassing techniques can help overcome this issue.
- Mold Material Defects: Improper preparation or incompatibility of the mold material can lead to defects in the final product. Using suitable mold materials, ensuring proper preparation, and regular maintenance can help in addressing mold material defects.
- Metallurgical Defects: Metallurgical defects, which result from improper alloy composition or issues during melting and pouring, can lead to compromised product performance. Careful control of the metal composition and casting conditions can prevent these defects.
- Geometric Defects: Geometric defects, such as misruns, cold shuts, or warping, occur when the molten metal does not completely fill the mold or cools unevenly. Overcoming this involves proper mold design, maintaining the correct pouring temperature, and ensuring sufficient fluidity of the molten metal.
The ability to identify and overcome casting defects is key to enhancing the performance of cast products. By investing in improved processes, training, equipment, and quality control measures, foundries can create high-quality products that satisfy customer expectations and withstand the rigors of use. With every defect overcome, a step is taken towards improved product performance, increased customer satisfaction, and the overall success of the foundry operation.