As the connection between the wheel and suspension system, the steering knuckle in the automobile chassis parts bears the load under various conditions, and is a key component required by the suspension system, wheel hub, steering system and braking system, so it is required to have high comprehensive mechanical performance. However, the number of automobile steering knuckle is large, the internal quality is high, and the shape structure is complex, the thickness and section are uneven, and there are many curved surfaces, so it is difficult to form. The common structure of this product is a claw or claw structure with irregular space, which has multiple hot spot areas and is prone to shrinkage defects. The shrinkage defects will seriously affect the strength and elongation of ductile iron castings, thus causing a large number of unqualified ductile iron castings.
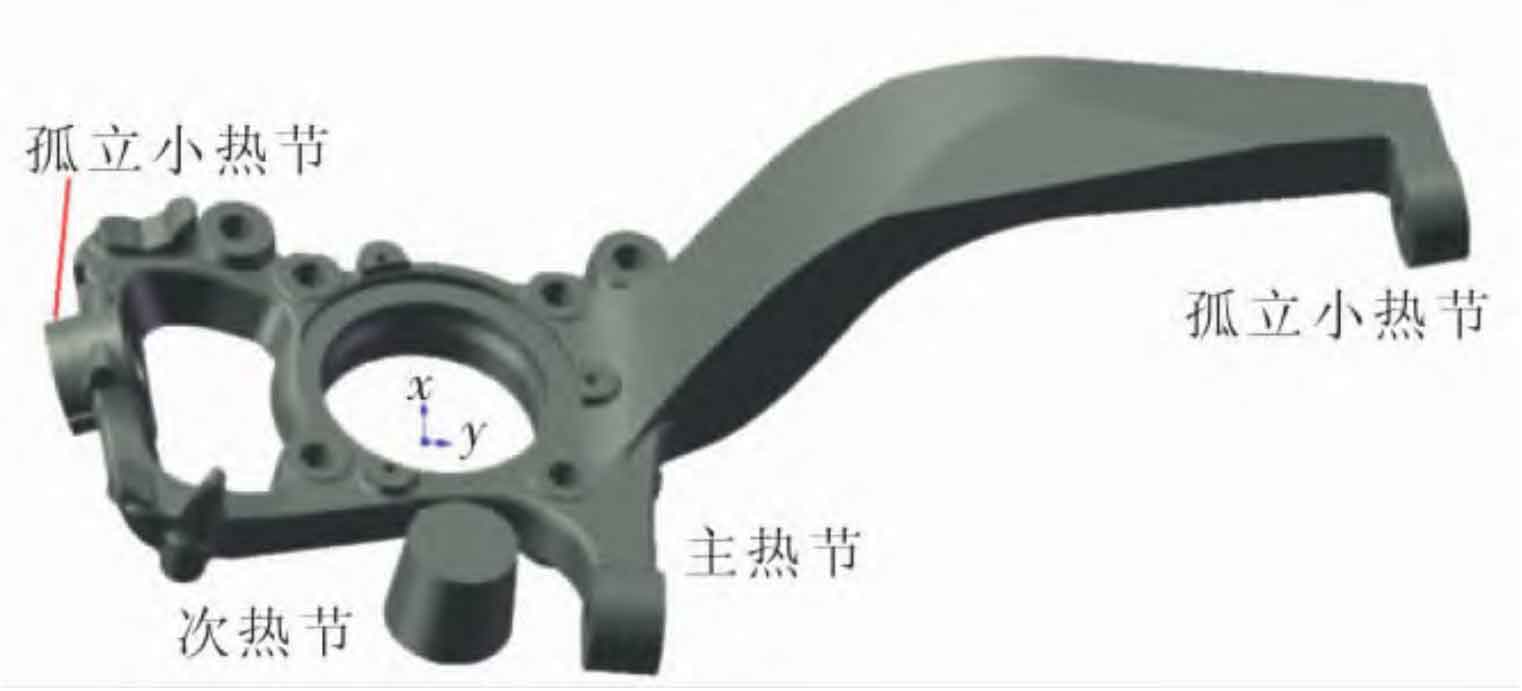
(1) When producing ductile iron castings of automobile ductile iron castings steering knuckle with multiple hot spots, the eutectic degree of molten iron is adjusted to close to 1 through fine control of chemical composition, and the eutectic undercooling of solidification temperature curve is adjusted to close to zero, and the shrinkage porosity of ductile iron castings is significantly reduced.
(2) Based on the analysis of thermal analysis curve, the combination of silicon carbide pretreatment, wire feeding inoculation, floating silicon inoculation, ladle inoculation, and flow inoculation is used to strengthen the inoculation, so that the number of graphite spheres is increased, the self-expansion ability is strengthened, and shrinkage porosity is eliminated. Without the use of risers and chills, excellent ductile iron castings with multiple heat joints and no shrinkage porosity are produced for automobile steering knuckle. The tensile strength and yield strength are increased by 8.4% and 9.7% respectively, and the elongation is increased by 58%, The hardness is increased by 8%, significantly improving the yield.
At present, the solution is generally to increase its feeding capacity by adding a blind riser, or to increase the cooling rate by covering the iron mold with sand, but the above methods increase the complexity and workload of the process. The use of melt quality control can reduce or eliminate the riser and significantly increase the process yield. Compared with the iron mold coated with sand, it reduces the difficulty of mold design and saves costs. Therefore, this paper mainly studies the preparation of a sound non-shrinkage ductile iron castings automobile steering knuckle through melt quality control.