introduction
Precision casting of rail transit brake system components has the characteristics of good chip removal performance, shock absorption and noise reduction, and low cost. It has become a key technology for high-speed railway train brake system.Widely used components in the dynamic unit. With the acceleration of high-speed rail speed and the improvement of safety requirements, the casting defects such as slag inclusion, porosity, shrinkage, and cracking are not allowed in the brake unit of high-speed rail trains. Numerical simulation software can better obtain the distribution of filling speed, filling temperature, solidification and shrinkage during the casting process, predict whether there are defects in the casting in time, and adopt better casting technology to achieve the goal of saving cost and improving casting quality. Using AnyCasting software to perform numerical simulation on the complex cavity casting forming process under different risers, the shrinkage and shrinkage of the complex cavity were predicted, and process improvements were made. Using AnyCasting software to perform numerical simulation on the filling and solidification process of impeller casting,
Value simulation predicts shrinkage defects in the central part of the impeller casting. Based on ProCAST software, the casting process of the butterfly valve body is analyzed.Through numerical simulation, the velocity field, temperature field, and solid fraction distribution of the valve body casting were obtained, and the location of defects in the valve body casting was predicted and the process was optimized. The volume of defects was reduced by more than 95%.
Taking the brake unit box of high-speed trains as the research object, AnyCasting software was used to conduct numerical simulation of the filling, solidification, and shrinkage during the casting process of the box, predict and determine whether there were defects in the casting of the brake unit box of high-speed trains. Based on the numerical analysis results, the casting process was optimized.Improvements are made in the hope of obtaining high-performance brake unit box castings for high-speed trains.
Structure and Model
The brake unit box of high-speed rail is an important supporting component of the high-speed rail brake system. As shown in the figure, the box, together with the clamping lever assembly, brake shoe carrier assembly, and hanger assembly, constitutes a complex parking brake clamping unit, whose performance directly affects the safety of high-speed rail trains. The brake unit box component weighs 14 kg and the casting size is 302 mm × 287 mm × 235 mm. Its structure is complex, as shown in the figure, consisting of three sand cores forming an internal cavity structure. According to the structural characteristics of the brake unit box, a runner is set up in the middle of the disc with a diameter of 50 mm and a height of 60 mm. The lower part of the runner is placed with a filter block, which is used to filter the water and impurities in the melted steel.The size is 50 mm×50 mm×22 mm; the lower part of the filter block is the riser, with a diameter of 75 mm and a height of 90 mm. As shown in the figure, the thick and large parts on both sides of the flange are provided with risers for shrinkage compensation, with a diameter of 60 mm and a height of 90 mm.
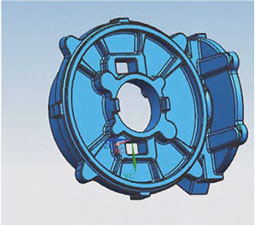
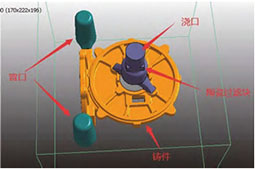
Casting value
The design of the riser and runner for the high-speed rail brake unit box is conducted using AnyCasting analysis software to conduct numerical simulation of the casting formation of the high-speed rail brake unit box, predicting the filling, solidification, and shrinkage distribution of the high-speed rail brake unit box, and evaluating whether there are casting defects in the high-speed rail brake unit box.Defects.
Casting filling
The filling capacity is particularly critical for the casting of high-speed rail brake unit boxes to achieve precise dimensions, clear contours, and complete shapes during the casting process. The mold filling distribution of the brake unit box for the high-speed railway is obtained using the AnyCasting analysis software, as shown in the figure. From the perspective of mold filling speed, during the mold filling process In the process of filling the mold, the molten iron enters the mold cavity at a high speed, as shown in the figure. The casting is at risk of sand flushing, and it is necessary to provide sufficient mold strength to ensure that the sand is not washed away. From the overall filling process, the molten iron flows rapidly, as shown in the figure. When the liquid level rises from the bottom of the casting mold cavity, turbulence occurs. From the perspective of filling temperature, during the filling process, when the molten iron finally fills the mold cavity, the lowest temperature on the surface of the casting is around 1300℃, as shown in the figure. At the end of filling, the temperature of the molten metal is above the solidus line, and the probability of cold shut formation on the casting surface is low. From the analysis of oxide conditions during filling process, as shown in the figure, during pouring process, the first stream of molten iron reacts with air and easily forms oxide slag.
Casting solidification
The casting solidification and shrinkage distribution of the brake unit box of the high-speed railway obtained using the AnyCasting analysis software is shown in the figure. From the perspective of solidification sequence, there are three large isolated liquid-phase regions in the casting during solidification, as shown in the figure, which cannot effectively supplement the molten iron and poses a risk of shrinkage porosity and shrinkage cavity defects. From the perspective of probability defects, as shown in the figure, there are five regions with risks of shrinkage porosity and shrinkage cavity defects in the casting body, with a probability of defects exceeding 60%, which requires improvement from the process perspective.
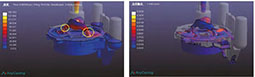
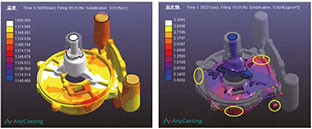
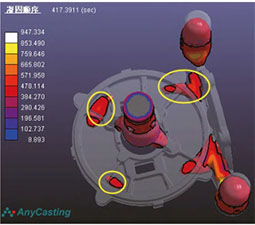
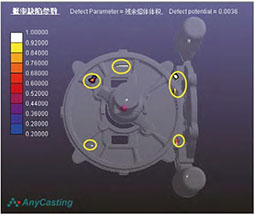
Casting process
It was found that there were certain defects in the casting of the high-speed rail brake unit box, which required improvement from a process perspective. The improvement plan is shown in the figure. Considering reducing sand and oxide, the pouring system was improved to reduce the turbulence of the molten iron and the impact speed of the molten iron on the casting cavity. The intermediate risers were replaced with heating risers (using Shengquan Group FT500-M50×75 heating riser sleeve), and the outer side was connected with two risers to increase the feeding effect of the two risers at the flange. The increased cross-sectional area of the runner was ϕ35 mm, and the size of the filter block at the lower part of the straight runner was 50 mm×50 mm×22 mm. The increased cross-sectional area of the runner connecting with the riser was 25 mm×35 mm. The increased cross-sectional area of the runner connecting with the riser was 50 mm×7 mm. At the same time, the subsidy of the riser neck at the flange was increased, and the size of the subsidy was increased to be 20 mm long and 15 mm wide, and the feeding channel of the riser was increased.
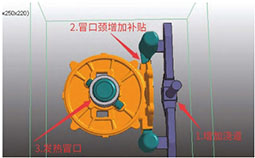
Casting samples and performance test results
According to the improved process plan for the high-speed rail brake unit box, the high-speed rail brake unit box was poured, and the resulting sample is shown in the figure. In order to To detect the defects of the high-speed rail brake unit box, the sample was dissected every 5-10 mm and subjected to dye penetrant testing. The results showed that no shrinkage or shrinkage defects were found inside the high-speed rail brake unit box.
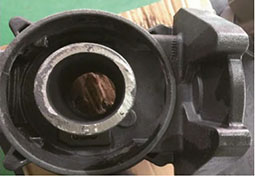
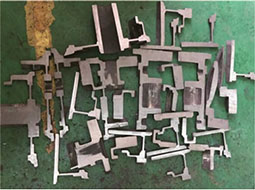
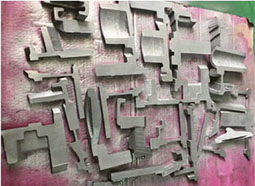
Properties of cast test sample
The testing equipment conducted mechanical property tests on the casting samples of the high-speed rail brake unit box, and the results obtained were as follows: the nodularity and pearlite content, metallographic structure, as shown in the figure, the nodularity was 85%, and the pearlite content was 45%. It can be seen that the tensile strength, yield strength, elongation, hardness, and nodularity of the casting samples of the high-speed rail brake unit box meet the requirements for use.
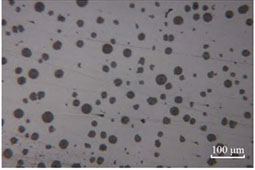
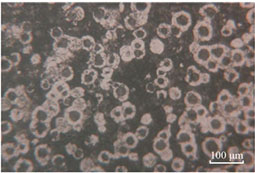
conclusion
(1) The filling, solidification, and shrinkage of the casting process of the high-speed rail brake unit box casting sample can be obtained using AnyCasting numerical simulation software.Predict and judge the forming condition of the box casting.
(2) Through numerical simulation of the casting process of the high-speed rail brake unit box in the original process, the filling speed, filling temperature, oxides, solidification,Based on the shrinkage distribution, it is predicted that shrinkage porosity and shrinkage cavity defects will occur in the box casting, and process improvements are needed.
(3) By improving the pouring system, reducing the turbulence of the molten iron and the impact speed of the molten iron on the casting cavity, the intermediate risers are replaced by heating risers, and the outer risers are increased.Adding a sprue connects two risers, increasing the feeding effect of the two risers at the flange; at the same time, increasing the subsidy of the flange neck and adding process improvement measures such as riser feeding channels. Using AnyCasting numerical simulation software to analyze its filling, solidification, and shrinkage again, the prediction results show that there are no defects in the box casting.
(4) The anatomical and dye penetrant inspection of the casting test sample of the high-speed rail brake unit box obtained showed no internal defects, which is consistent with the improved process parameters.The simulation results are consistent. In addition, the performance testing of the casting samples has shown that the tensile strength, yield strength, elongation, hardness, and nodularization rate meet the customer’s standard requirements. The combination of theoretical calculations and simulation can effectively avoid the occurrence of casting defects, which is beneficial to reducing the casting cost of the high-speed rail brake unit box and improving the casting quality of the box.