In the process of casting simulation, the pouring system, grid division and calculation conditions are the same as the above, the casting material is still QT500-7, the pouring temperature is 1370 ℃, and the pouring time is 3.19s.
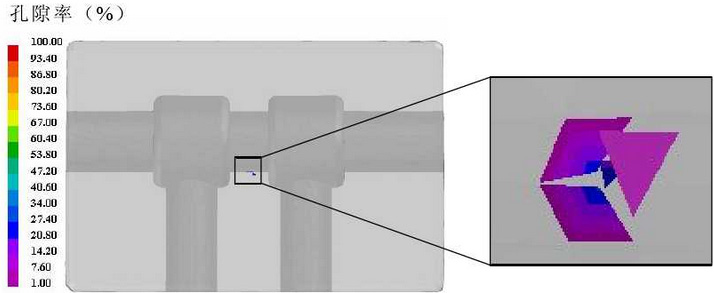
The distribution of shrinkage defects in the improved valve body is as shown in the figure. The shrinkage defects are mainly distributed in the middle of two countersunk grooves of the valve body, with irregular shape and the maximum porosity of 31.4%. Compared with the valve body before the improvement, the improved valve body has fewer shrinkage defects, and the porosity is reduced by 2.9 times. The main reason is that in the improved valve body, there is a gradual transition between the valve hole, the countersunk groove and the oil outlet, so as to reduce the casting shrinkage resistance and the shrinkage defects.