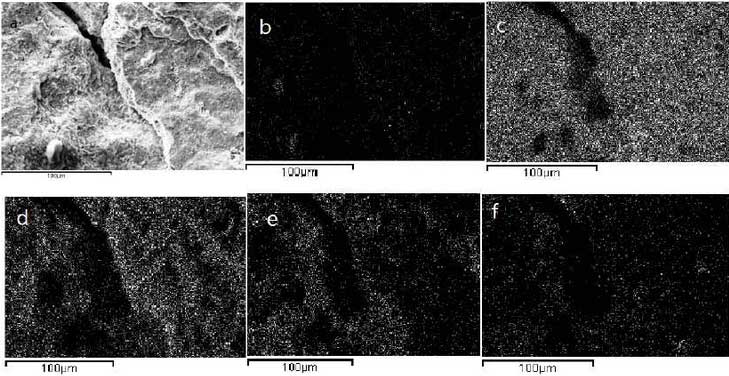
In order to understand the oxidation conditions at the cracks, elemental analyses are carried out on the areas of Fig. 1a and Fig. 2a, respectively, and the results are shown in the B-F diagrams of Fig. 1 and Fig. 2.As can be seen from the observations in Figures 1 and 2, Figures 1b and 2BThe proportion of carbon content in the graphite decreases significantly, mainly due to oxidation, which results in carbon being oxidized to carbon monoxide or carbon dioxide disappearing, resulting in the number of regular spherical graphite significantly less than the average as-cast value; the distribution of oxygen around the crack and spherical graphite is relatively concentrated, so it can be concluded that the formation of cracks can accelerate oxidation, at the same time, the shrinkage of graphite or graphite andThe formation of two-phase gap due to segregated metal-forming compounds around it also accelerates oxidation; the distribution of silicon is relatively uniform and is accompanied by the distribution of oxygen, which indicates that the oxide formed by silicon and oxygen distributes more uniformly and improves the oxidation resistance of the material to a certain extent; the distribution of molybdenum at cracks is relatively concentrated, which indicates the molybdenum carbide formed at the grain boundary as-cast.Because of its irregular shape, stress concentration is easy to occur and cracks are easy to occur here.According to the analysis in Figure 3, the fine and uniform material is Si-Fe-rich oxide.
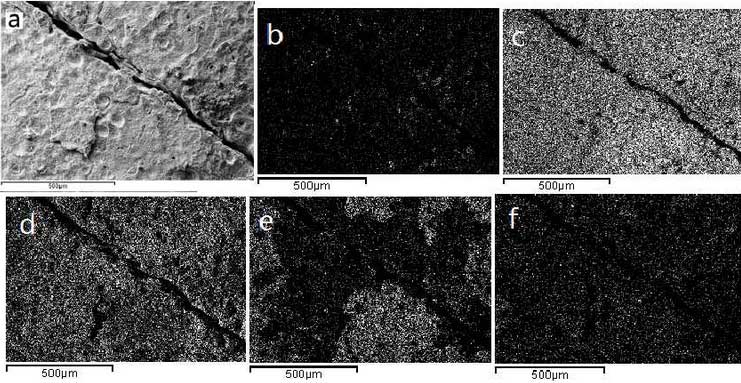
In order to further understand the oxidation process of high silicon molybdenum ductile iron, the samples at the initial stage of oxidation shown in Figure 4A are selected for observation. The results are shown in Figure 4b-4d. Elemental analysis shows that the number of spherical graphite on the surface of the sample begins to decrease and the spherical graphite in parts of the sample has disappeared. The uniform distribution of Si and Fe indicates that Si-Fe-rich graphite forms on the surface of the sample.Oxide protective film to prevent further oxidation.
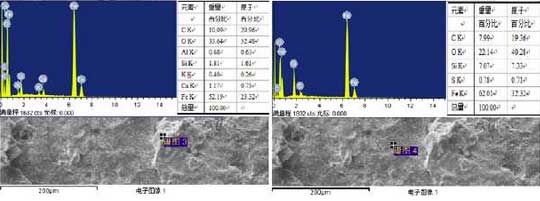
In order to further understand the oxidation process, elemental analysis is carried out at the beginning of crack formation. The test results are shown in Fig. 5.It can be seen from the diagram that at the initial stage of crack formation, the loss of carbon is serious, there is a certain amount on the observed surface only at the spherical graphite, and the rate of decarbonization increases with the increase of operating temperature.According to the research of Yang Shihao’s team, decarbonization of cast iron can protect the oxidation of cast iron to a certain extent, especially at low oxidation rate.
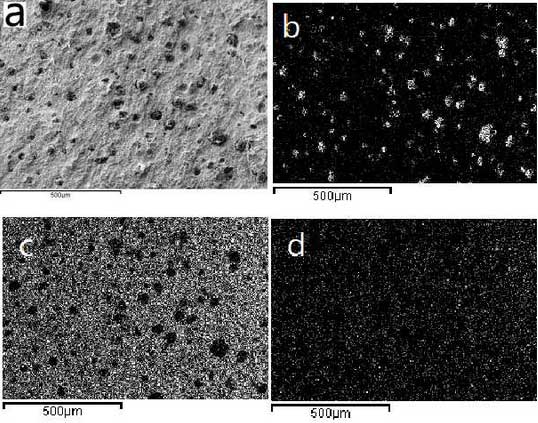
Molybdenum deposits on ferrite grain boundaries mainly as carbide during casting and exists as molybdenum oxide during oxidation.The oxidation of iron and silicon is the main observation surface, which is also consistent with the research of many scholars.
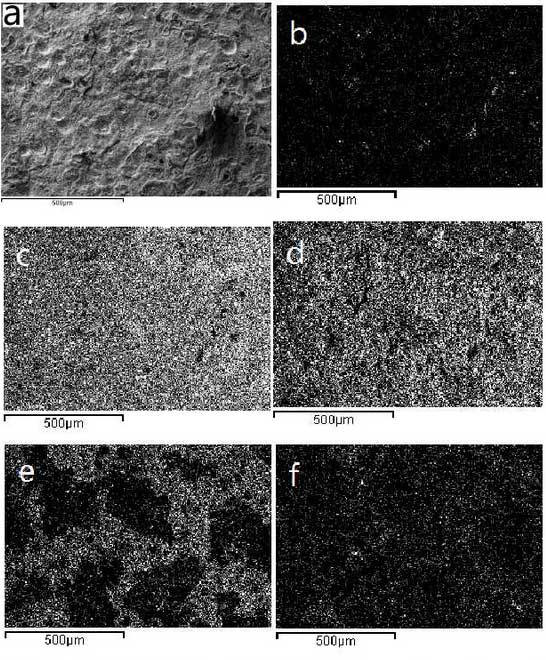