The front-end box casting structure is complex, with many internal tubes, and the casting process is There are major difficulties in production. The main problems with front-end box castings are It is a defect of gas hole and shrinkage cavity, which affects the quality of the casting. The concession rate of the casting and scrap rate account for the majority, and the complete qualification rate is low. Through process Improvement, mainly to optimize the gas emission of the mud core and the pouring system The early porosity problem has been controlled, and the casting quality has basically stabilized. which meets the requirements of mass production.
Structural characteristics and technical requirements of castings
The casting of the front end box of L21/31 has a rough weight of 2,180 kg, The outline dimension is 1800mm ×1100 mm × 950 mm, The structure of the bottom is very complex, consisting of 27 sand cores in the upper, middle and lower layers There are multiple interrelated internal cavity structures, and the distribution of mold core is shown in the figure 1. The main wall thickness of the L21/31 front cavity casting is 12 mm, the largest The large wall thickness of 125 mm and large wall thickness differences are prone to produce pores, shrinkage cavities, Casting defects such as porosity ultimately lead to casting failure during hydrostatic and pneumatic pressure tests. The leakage was scrapped during the test. The casting material is HT300, and the mechanical properties should be Calculate tensile strength σb ≥300 N/mm2, HB hardness 185~278.
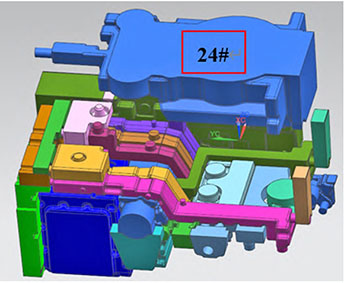
Existing problems and reasons
The L21/31 front-end box has been trial-produced since 2013, There is a phenomenon of “holding breath” on the upper, middle and lower surfaces of the upper, middle and lower layers. The casting “holds breath” The porosity defects caused by “gas” are shown in the figure. The number is not large, but the volume Larger, smooth-walled pores appear on the surface of the casting, often in the shape of a pear oval or round.
There are three main reasons for the formation of porosity defects:
1) From the mechanism of the formation of intrusive pores, the casting is mainly liquid. When the metal enters the sand mold, the casting sand mold or sand core is affected by the high temperature of the molten metal. A large amount of gas will be generated, and the casting will increase with the increase of temperature and gas volume. In addition, the pressure of gas at the metal-mold interface is constantly increasing. When the interface When the pressure of the upper partial gas is higher than the external resistance, the gas will invade Liquid metal forms bubbles on the mould wall. After the formation of bubbles in the casting, they will break away The mold wall floats into the liquid metal in the mold cavity. When the bubble cannot rise in time When the temperature rises, invasive pores will form in the metal.
2) The previous pouring system has always been to arrange the runner on the upper box, The ceramic tube for the runner is directly introduced to the bottom of the casting. Due to the internal runner The height difference is close to 1000 mm, and the molten iron is The straight internal runner obtains a higher flow velocity, which can be maintained when it enters the cavity. When the molten iron flows at high speed, it is very easy to cause the phenomenon of backwinding, which will affect the casting cavity Gases are easily wrapped in molten iron, and complex cavity structures are not It is beneficial to the gas floating, if the gas wrapped in the molten iron in the casting cannot rise in time After floating out, most of them will eventually stop moving on the surface or at the surface layer. The casting uses software to simulate its molten iron filling process, The tracking particle motion state is shown in the figure, and there is obvious turbulence and eddy Phenomena such as gas.
3) Due to the complex structure of the L21 front end box, the mud core in the cavity The number of objects is large, and the arrangement is mainly vertical and horizontal, stacked and distributed. It is beneficial to the air discharge of the mud core, together with the 24# mud core on the upper part of the mold cavity (see Figure 1) large size (horizontal section size is about 1300mm×850mm), In addition to its large gas generation capacity, the mud core itself also This impeded the smooth gas release from the lower mud core and the faster discharge of gas from the mold cavity.
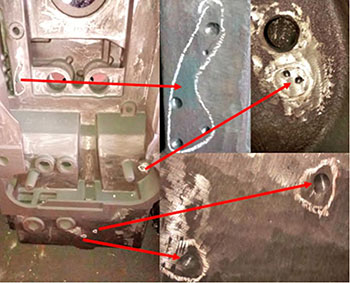
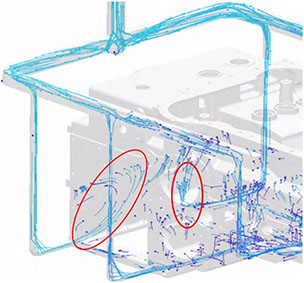
Process improvement direction and process
Based on the above analysis, a solution to the problem of L21 casting front-end box surface Process direction for surface porosity defects: 1) Solve the impact of gas emission from the clay core itself. The gas emission of the casting clay core should be reduced Shorten the time to avoid the temperature drop of molten iron and the filling of molten iron into the mold cavity After that, there was still gas from the mud core itself moving out and invading into the molten iron, which was too late. float and discharge. 2) Solve the problem of flying volume and unstable liquid surface rise during the filling of molten iron for casting The impact. According to the established process improvement direction, carry out casting process improvement Come in.
Core gas emission
The casting mud core has a large gas evolution rate, so in order to ensure that it is not affected by the heat during the process, The gas in the core should be discharged as soon as possible, and the removal of mud core should be minimized gas from the bottom and surrounding areas of the mud core invades into the molten iron, Test and discuss the design, hollow out the center of the top of the casting mud core (ensure The sand consumption around the mud core is not less than 200mm, and the pre-embedded coke is used. The advantage of gas venting from the mud core is that it reduces the risk of the mud core itself Gas volume, which provides gas outlet channels for the discharge of gas in the mud core, but also The gas removed from the casting mud core increases the storage space and improves the quality of the mud core. The tendency of gas to discharge into the cavity, as shown in the figure.
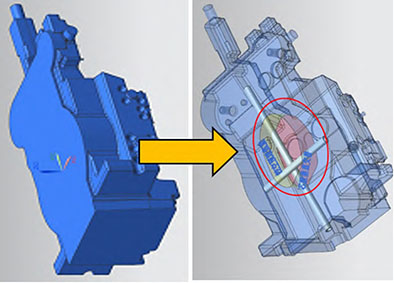
Other mud core gas emission
After experimentation, the method of “drawing out the leather rope + embedding the ventilation rope” The formula is shown in the figure. When molding the casting mud core, place the venting rope along the core bone (root Select φ6mm and φ8mm ventilation ropes according to the size of the mud core), and allocate boxes for the castings After the core is inserted, use leather rope to guide the mud core air outlet from the core head to the sand box In addition, after sand filling, the leather rope should be pulled out. The advantage of doing so is that it can It is made of nylon material, which has certain toughness and strength After the leather rope is extracted, the mud core and the outside world can form a stable air outlet In addition, this method also reduces the safety risks during operation. Full risk, which also has certain prevention effect on the porosity quality defects of castings. The role.
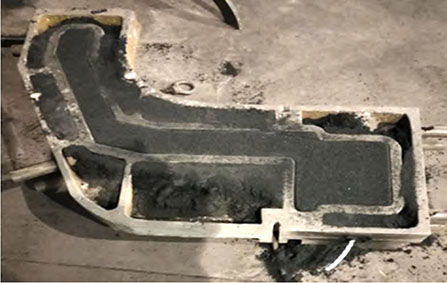
Gas outlet riser setting
The 24# mud core is basically covered on the upper part of the mold cavity. Not conducive to the discharge of gas from the cavity, and the location of gas porosity defects is often large Mostly located at the bottom of the mud core. To allow gas to flow smoothly at the bottom of the mud core from the inside of the cavity, at locations where air hole defects are common (The parts where gas easily accumulates in the cavity), adding vent risers. As shown in the figure, the riser passes through the 24# clay core, allowing gas to flow directly from the upper tank. The gas outlet riser is removed.
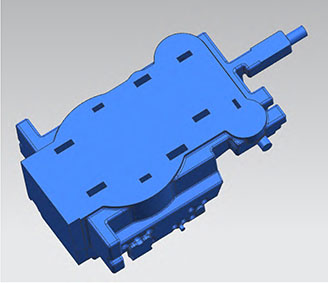
Improvement of the pouring system
The improvement of the casting pouring system mainly reduces the turbulence of molten iron during filling. After technical communication with the user, the runner is placed on the casting. At the bottom, the slow flow effect of the horizontal runner at the bottom reduces the molten iron The filling speed at the inner gate. 3.2.2 Based on the actual situation, the casting design completely bottom-gating pouring system As shown in the figure, the runner is located at the bottom of the casting, buffer the liquid to reduce the filling speed. During the trial production, As a result, based on this basic process, many small-scale improvements have been made. After trial production, the runner is placed at the bottom, resulting in porosity defects in the casting. The number has decreased significantly, but it has not been completely eliminated.
According to the analysis of the first test results, it is believed that the improved mud core The gas discharge method is relatively reasonable, and the filling speed of molten iron has slowed down. However, judging from the quality results of the production castings, the porosity defects have not been eliminated. Except, there is still room for process improvement. After discussing with the engineer Communication, believing that the pouring design of full bottom injection is helpful for improving project objectives, and that further reducing turbulence and backwinding of molten iron can be achieved by It can maintain a stable rise in the liquid level of the mold cavity, which determines the application of filtration technology. Add filter plates to the gate, which can improve the filling speed and It can play a role in preventing slag. The picture shows the filtration plate casting system scheme Intentions.
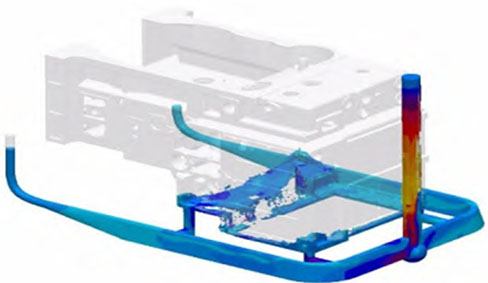
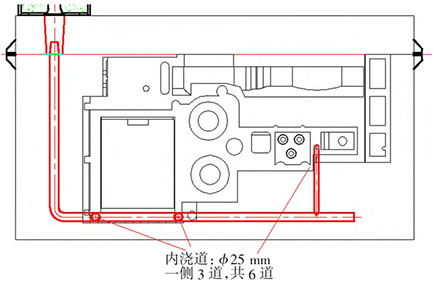
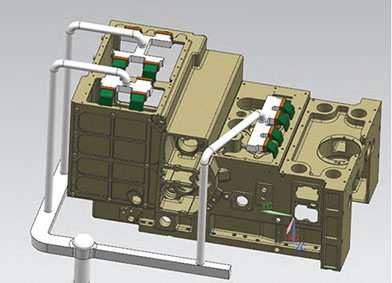
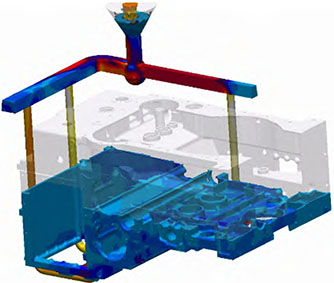
Conclusion
1) For titanium alloy centrifugal pump parts, change the flange to a round shape Shaped structure and straightening of the inlet neck are beneficial to eliminating gas shrinkage holes in the pump body Defects. 2) The pouring method was changed from top pouring to side pouring, which was beneficial to reducing casting defects. The flow mark, cold pox, and folding phenomenon on the surface of the casting make the surface quality and achieved significant improvement. 3) The structural characteristics of the casting and the gating system determine the filling of the casting The stability of the filling process and the rationality of the filling sequence of the molten metal have a significant impact on the internal and external quality of the casting.