Resin sand casting foundries play a significant role in advancing casting techniques and pushing the boundaries of metal fabrication. These foundries leverage modern technologies, expertise, and innovation to achieve higher precision, efficiency, and quality in the casting process. Here are some ways resin sand casting foundries lead the way in advanced casting techniques:
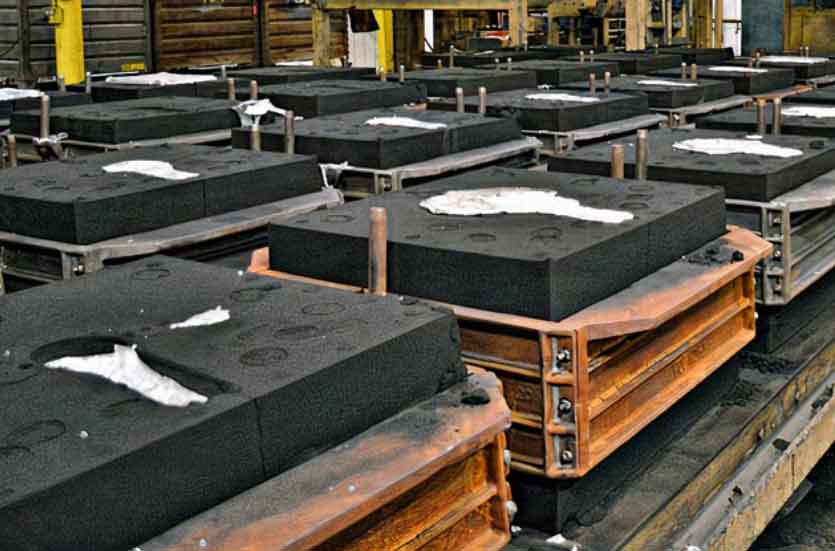
- Computer-Aided Design (CAD) and Simulation: Resin sand casting foundries use CAD software to create detailed digital models of the desired metal components. These digital models are then used to simulate the casting process, allowing foundries to identify potential issues, optimize designs, and predict casting outcomes. This approach minimizes the need for physical prototypes and reduces trial and error, resulting in faster and more reliable production.
- 3D Printing for Tooling: Some resin sand casting foundries utilize 3D printing technology to create complex and custom tooling for casting molds. 3D-printed tooling enables greater design freedom and allows foundries to produce intricate castings that were previously challenging to achieve with traditional methods.
- Automated and Robotic Systems: Resin sand casting foundries adopt automated and robotic systems for tasks such as mold preparation, pouring, and post-casting processes. Automation improves consistency, reduces human errors, and enhances overall production efficiency.
- Real-Time Process Monitoring: Foundries employ advanced sensors and monitoring systems to collect real-time data during the casting process. This data helps ensure casting quality, identify deviations, and make adjustments promptly, leading to higher yields and reduced scrap.
- High-Quality Materials and Alloys: Resin sand casting foundries stay up-to-date with the latest advancements in metallurgy and materials science. They have access to a wide range of high-quality materials and alloys, allowing them to cater to the unique requirements of diverse industries and applications.
- Lean Manufacturing Principles: Leading resin sand casting foundries embrace lean manufacturing principles to streamline their processes, reduce waste, and optimize production flow. By eliminating non-value-added steps, these foundries enhance their efficiency and cost-effectiveness.
- Sustainability Initiatives: Resin sand casting foundries are increasingly adopting sustainable practices to reduce their environmental impact. This includes recycling sand and materials, optimizing energy consumption, and implementing waste reduction strategies.
- Continuous Training and Skill Development: Skilled technicians and engineers are essential for the success of advanced casting techniques. Resin sand casting foundries invest in continuous training and skill development to ensure their workforce is proficient in the latest technologies and methodologies.
- Collaboration with Designers: Leading foundries actively collaborate with designers, engineers, and customers to understand their specific needs and challenges. This collaborative approach helps ensure that the casting process is tailored to meet the unique requirements of each project.
- Research and Development: Resin sand casting foundries invest in research and development to explore new materials, techniques, and processes. This dedication to innovation allows them to stay at the forefront of the industry and deliver cutting-edge solutions to their customers.
Resin sand casting foundries that lead the way in advanced casting techniques combine their expertise, state-of-the-art technologies, and commitment to innovation to produce high-quality, complex, and sustainable castings for a wide range of industries and applications.