Based on the analysis of simulation results and actual defect locations of steering knuckle steel castings, it can be seen that the irregular structural constraints of the product and the unreasonable design of the gating system jointly lead to casting defects such as shrinkage holes and sand inclusions in the steering knuckle steel castings. The optimized casting process plan is as follows:
(1) Reduce the arc above the parting surface from R85 mm to R65 mm (see Figure 1), reducing hot spots and reducing processing costs.
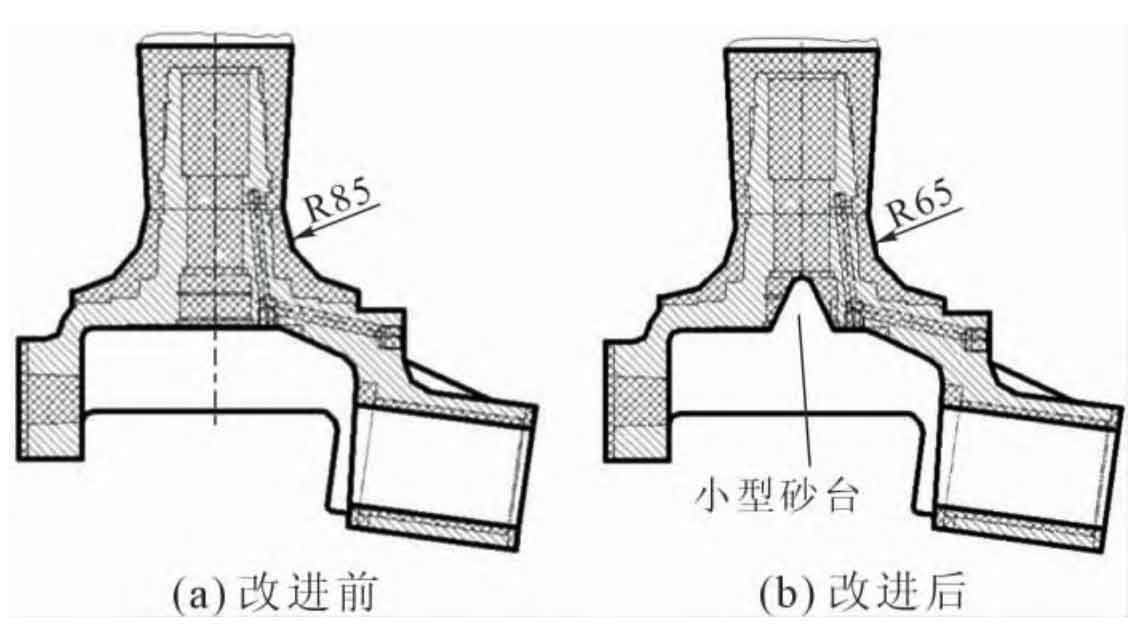
(2) Add a graphic design for the lower sand mold φ 60 mm × A 55 mm small sand table (Figure 1) is beneficial for accelerating heat dissipation, reducing impurity accumulation, and reducing processing costs.
(3) The intermediate pouring adjustment pouring system is optimized to a bottom pouring pouring system to form a bottom-up sequential solidification of molten steel. The optimized runner bypasses the outer contour of the NO. 3 sand core in the lower model, without affecting the normal core lowering operation of the NO. 3 sand core (Figure 2). Before the No. 3 sand core is lowered into the core, the surrounding of the inner runner shall be evenly coated with two coats of alcohol based zircon powder paint to avoid long-term erosion of high temperature steel liquid into the sand mold and introduction of non-metallic inclusions.
To verify the above process optimization effect, ProCAST was used to set the same numerical simulation parameters before process optimization. By meshing the 3D solid casting process model, as shown in Figure 3, the non important part of the grid size riser was set to 28 mm, the other important parts were set to 6 mm, the number of surface grids was 165 928, and the number of volume grids was 627 892.
From Figure 4, after optimizing the steering knuckle steel casting process, it can be seen that during the mold filling process, the steel liquid enters the bottom of the mold cavity through the inner runner. As the mold filling continues, the steel liquid smoothly fills the mold from bottom to top, and finally completely solidifies.

From the temperature field change diagram of the steering knuckle steel casting after process optimization in Figure 5, it can be seen that the liquid phase red high-temperature steel liquid moves upward in accordance with the overall solidification sequence, achieving the effect of first solidification at the position away from the thick and large riser during the solidification process, and finally solidification at the riser position. In the sectional view of the temperature field change diagram, it can be seen that the thick parts of the steering knuckle steel casting eliminate the isolated liquid phase zone during solidification, and the riser is the highest temperature part to ensure the smooth floating of non-metallic inclusions into the riser.
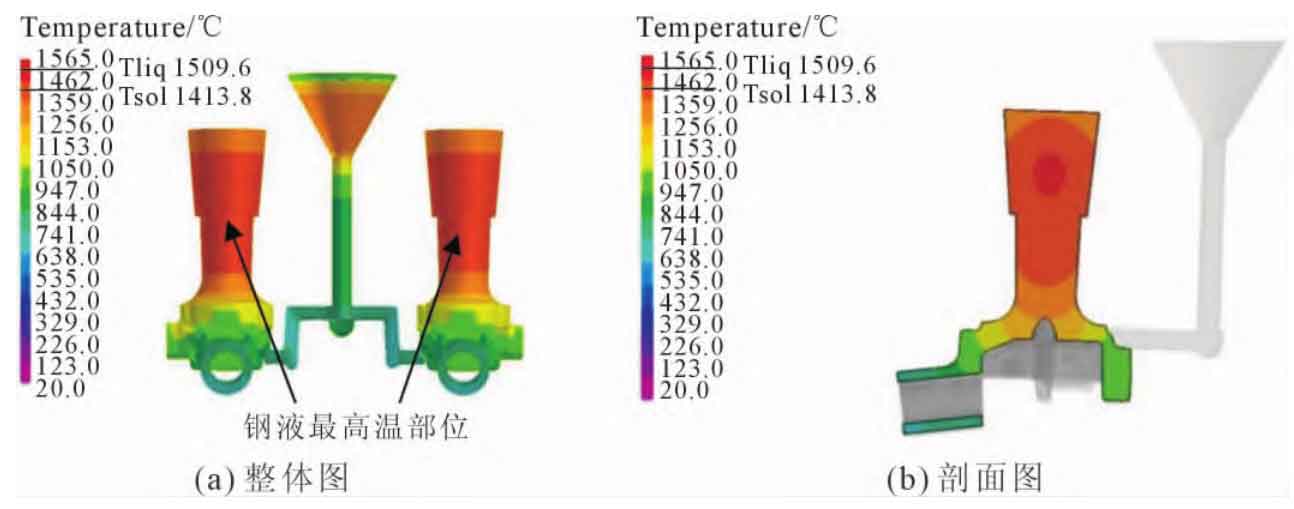
Figure 6 shows the distribution of shrinkage defects after process optimization. The distribution of overall shrinkage casting defects in the steering knuckle steel casting after process optimization shows that there are no casting defects in the neck region with an arc of R65 mm, indicating that the process improvement plan is reasonable. In addition, according to the analysis of simulation results, in the actual production process, the tail boss position is set φ 20 mm × 135 mm inner chill and an appropriate amount of special sand with a thickness of ≥ 25 mm, set at the middle support platform φ 20 mm × An appropriate amount of special sand with a thickness of ≥ 25 mm and an inner chill of 90 mm was found without shrinkage casting defects after trial processing, with good results.
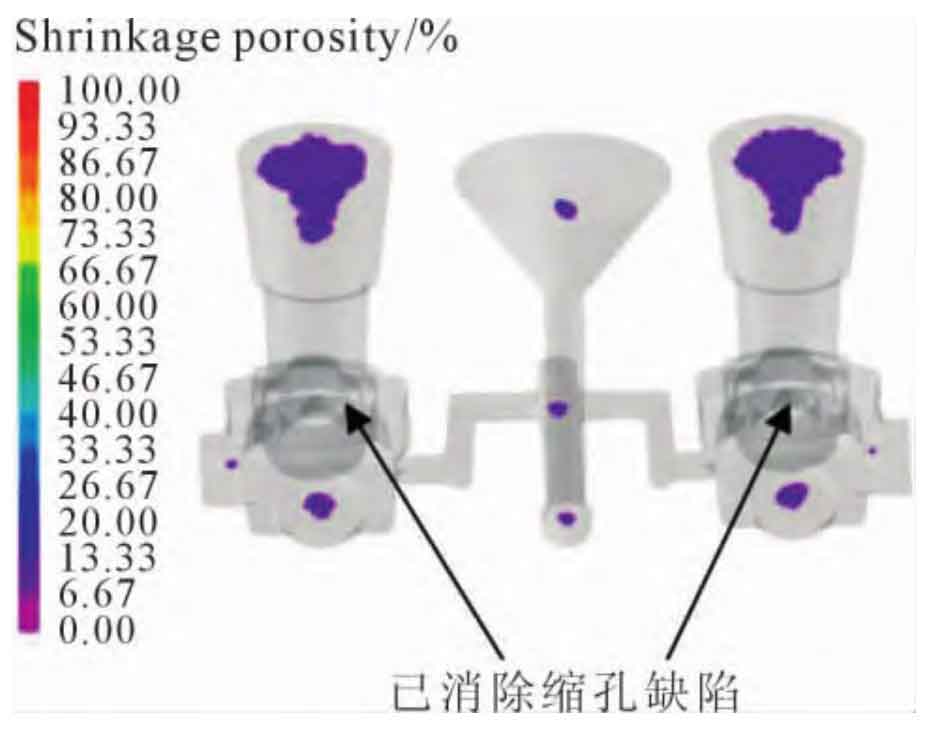