The particle swarm optimization algorithm is written based on MATLAB program. Set the number of particle population to 30, the number of iterations to 50, the learning factors C1 and C2 to 1.49445, and the inertia weight ω Is 0.8. Specifically, the solution vector value of the process parameter optimization variable is: the number of mold modules Mn ∈ [3,7]; Mold size MS ∈ [600650]; Minimum wall thickness of mold MT ∈ [30120]; Machining allowance Mr ∈ [1.5,5]. The weighting factors of the four optimization objectives take the processing time as 0.4, the carbon emission as 0.3, and the resource consumption and energy consumption as 0.25 according to the priority of the enterprise’s production objectives.
According to the above model parameter settings, the fitness convergence curve of particle swarm optimization algorithm is obtained, as shown in Figure 1. It can be seen from the figure that after about 12 iterations, the fitness curve tends to be stable, and the optimal individual fitness is 0.35597.
To sum up, the final mold process parameters are as follows: the number of mold modules is 6, the mold size is 630mm, the minimum wall thickness of the mold is 65mm, and the machining allowance is 1.8mm. The obtained optimized mold process parameters are applied to the composite mold, and green molding sand is used to fill the empty sand consumption according to the size and specification of the sand box, as shown in Figure 2.
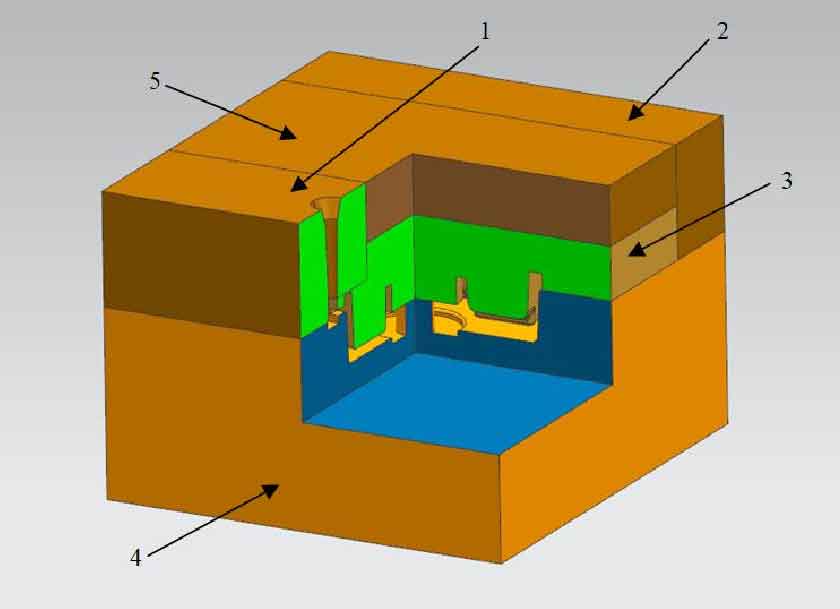
The specific process parameters of casting produced by compound forming method. The casting yield of the optimized composite mold is 85.52%, and the sand filling volume of the remaining part of the sand box is 0.1538m3. In addition, the relevant dimensional parameters of the mold module optimized based on composite forming.