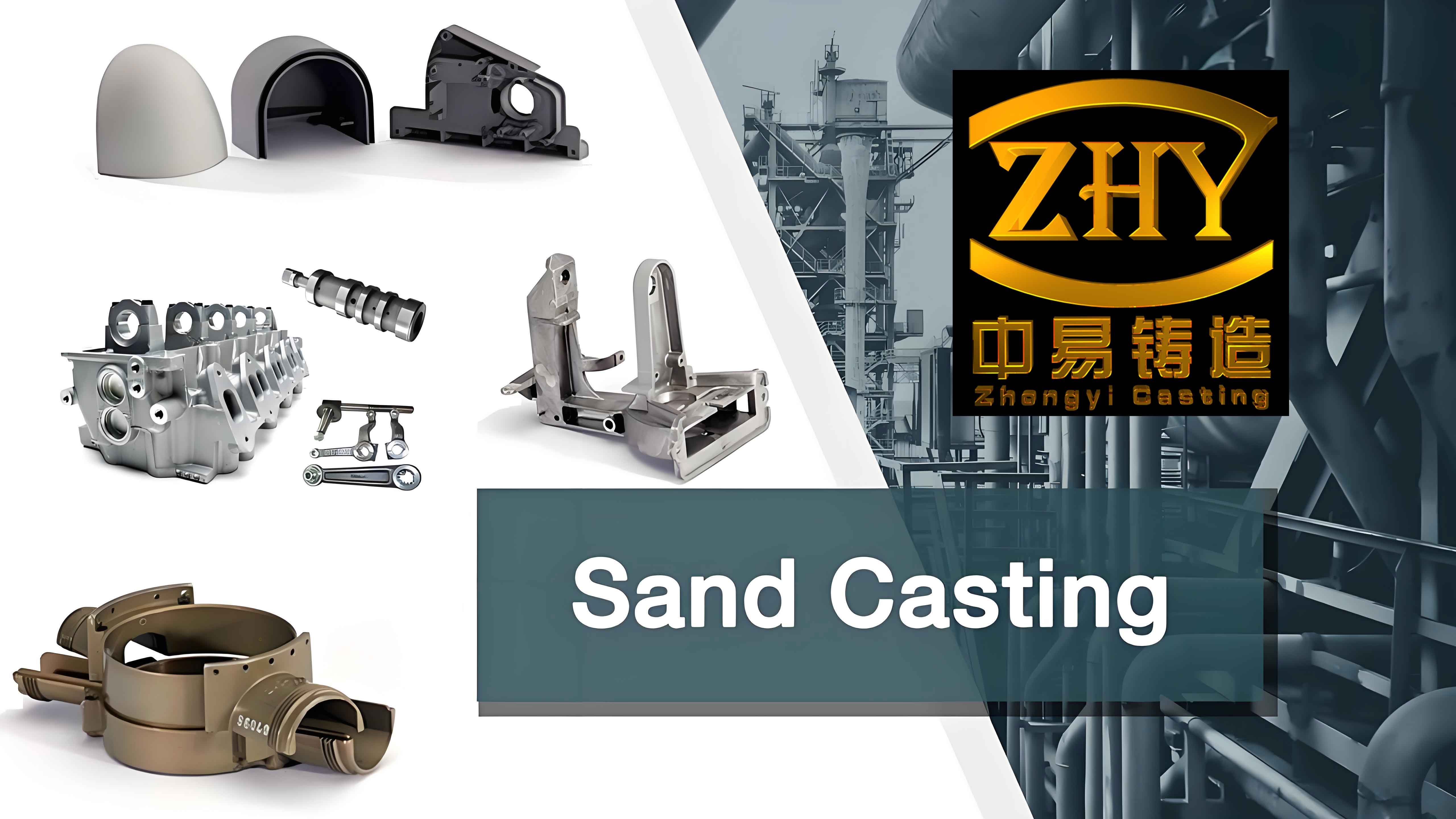
In sand casting processes, coating application on mold/core surfaces prevents direct contact between molten metal and sand particles, significantly reducing casting defects. This study investigates the critical relationship between coating thickness, Baumé concentration, and brushing frequency in alcohol-based coatings through systematic experimentation.
1. Experimental Methodology
Manual brushing tests were conducted using steel sand molds with alcohol-based coatings. The experimental matrix included:
- Baumé concentrations: 75°Bé, 78°Bé, 80°Bé, 82°Bé
- Brushing cycles: 1-5 applications
- Measurement method: Dry coating thickness post-ignition drying
The coating thickness accumulation can be modeled using:
$$ h_n = h_1 + \sum_{i=2}^{n} \Delta h_i $$
Where \( h_n \) = total thickness after n applications, \( h_1 \) = initial penetration thickness, \( \Delta h_i \) = incremental thickness per application.
Baumé (°Bé) | 1st Layer (mm) | 2nd Layer (mm) | 3rd Layer (mm) | 4th Layer (mm) | 5th Layer (mm) |
---|---|---|---|---|---|
75 | 0.17 ± 0.02 | 0.24 ± 0.01 | 0.51 ± 0.03 | 0.79 ± 0.05 | 0.91 ± 0.07 |
78 | 0.15 ± 0.03 | 0.26 ± 0.02 | 0.53 ± 0.04 | 0.82 ± 0.06 | 1.02 ± 0.08 |
80 | 0.16 ± 0.02 | 0.25 ± 0.01 | 0.55 ± 0.05 | 0.85 ± 0.07 | 1.15 ± 0.09 |
82 | 0.18 ± 0.03 | 0.27 ± 0.02 | 0.58 ± 0.04 | 0.89 ± 0.06 | 1.23 ± 0.10 |
2. Coating Thickness Dynamics
The interaction between Baumé concentration (B) and brushing cycles (n) follows:
$$ h = 0.021B + 0.186n – 0.004Bn + \epsilon $$
Where \( \epsilon \) represents measurement error (±0.05 mm). This model demonstrates:
- Initial penetration depth decreases with higher Baumé: \( \frac{\partial h_1}{\partial B} = -0.15 \, \text{mm/°Bé} \)
- Thickness accumulation rate increases with Baumé: \( \frac{\partial \Delta h}{\partial B} = 0.023 \, \text{mm/°Bé-cycle} \)
3. Process Optimization
For typical sand casting requirements (0.4-1.0 mm):
Coating Target (mm) | Recommended Cycles | Baumé Range (°Bé) |
---|---|---|
0.4-0.6 | 2-3 | 75-78 |
0.7-1.0 | 3-4 | 80-82 |
>1.0 | 4-5 | 82+ |
4. Industrial Implementation
In high-volume sand casting production, the coating efficiency can be calculated as:
$$ \eta = \frac{A_c}{A_t} \times 100\% $$
Where \( A_c \) = properly coated area, \( A_t \) = total mold surface area. Field tests show manual brushing achieves 85-92% coating efficiency versus 93-97% for automated systems.
5. Quality Control Parameters
Critical factors for sand casting coating integrity:
- Viscosity-Penetration Ratio: \( VR = \frac{\mu}{P} \times 10^3 \) (Optimal range: 1.2-1.8)
- Drying Rate Coefficient: \( D = \frac{t_{20\%}}{t_{80\%}} \) (Ideal value: 0.45-0.55)
- Adhesion Strength: \( \sigma_a \geq 0.15 \, \text{MPa} \)
6. Future Developments
Emerging trends in sand casting coatings include:
$$ \text{Smart Coatings} = f(\text{Thermochromic Additives}, \text{Nano-reinforcements}, \text{Self-healing Polymers}) $$
Current research focuses on coatings with temperature-responsive viscosity modulation:
$$ \mu(T) = \mu_0 e^{k(T-T_0)} $$
Where \( \mu_0 \) = base viscosity at \( T_0 \) (25°C), k = temperature coefficient (0.02-0.04°C⁻¹).
This comprehensive analysis provides a scientific foundation for optimizing alcohol-based coating processes in sand casting operations, balancing technical requirements with production efficiency.