The quality of the finished camshaft casting is affected both by a combination of multiple casting process parameters and by environmental noise The effect of fluctuations in the error generated by the factors. Based on this, the concept of signal-to-noise ratio in the Taguchi method and the TOSIS in multi-objective decision-making were used It is applied to the optimization of process parameters in the camshaft casting process to achieve the robust design of casting quality. Combined with the computer numerical simulation technology of the casting process, the optimal combination of process parameters with strong anti-interference ability was obtained from the simulation test scheme. The test results show that the combination of casting process parameters of casting temperature of 35 °C, pouring time of 12 s and pouring temperature of 1 446 °C makes the quality of camshaft castings reliable and robust, which provides an idea for the optimization method of casting process parameters in actual production.
As an important part of the engine valve mechanism, the quality of the camshaft directly determines the quality of the engine, which in turn affects the performance and market competitiveness of the car. The traditional camshaft casting process design process can only control the formation process of castings based on experience and general theory”Production” is only a qualitative analysis, and it takes repeated trial production to determine the process and achieve the expected process goals to a certain extent. This is easy to cause a lot of waste of resources, and it is also difficult to analyze the causes of casting defects, and it is impossible to truly eliminate defects from the mechanism level. The application of numerical simulation method in the casting process can greatly discover the defect forms and areas that may occur in the production process of camshafts, and can visually show the dynamic solidification process of camshaft casting molten metal, which is of great benefit to improving the quality of castings. In addition, the final quality of the product is directly determined by the production process parameters, and if the process parameters are not set properly, it is difficult to obtain a satisfactory product even if the optimal casting process design scheme is adopted. Abík et al. revealed the potential causes of defects in castings through numerical simulation, and studied the influence of adjusting the pouring process parameters on the quality of ENGJS-500-7 ductile iron castings. The results show that the optimization of the pouring time from 3.168 s to 3.460 s is conducive to eliminating the defects of cold insulation and insufficient pouring of castings, and the mechanical properties of the optimized castings also reach the corresponding standards. Wei Donghai et al. [3] studied the casting technology of high-precision retentionable QT600-3 beams from the aspects of finite element analysis of beam structural stiffness and numerical simulation of casting deformation The amount and composite alloy composition ratio are beneficial to improve the tensile strength and elastic modulus of castings and reduce the residual stress. Therefore, the optimal design of multiple casting process parameter combinations in the camshaft casting process can greatly improve the mechanical properties of castings and improve the quality and efficiency of casting. Because the influence of various unstable factors on the machining quality of castings in the casting process of camshafts must be fully considered, in order to obtain the best process parameter design scheme with strong anti-interference ability, it is necessary to carry out the robust design of casting process parameters. In the actual production process, it is often necessary to comprehensively consider the advantages and disadvantages of multiple quality characteristic indicators of castings to determine whether the current combination of process parameters is reasonable or optimal, that is, it is necessary to carry out the multi-objective robustness design of camshaft casting process parameters.
1 Optimize the design method
1.1 Signal-to-noise ratio
The quality control method based on signal-to-noise ratio proposed by Dr. Kenichi Taguchi can improve the stability of the quality of the finished product under external interference. The size of the signal-to-noise ratio factor (S/N) is an indicator to measure the robustness of product quality, and the larger the signal-to-noise ratio, the more robust the product quality. According to the characteristics of the quality of the product The signal-to-noise ratio function has three different static characteristics, namely, the signal-to-noise ratio (SNR) characteristic, the signal-to-noise ratio (SNR) feature, the signal-to-noise ratio (SNR) function, the signal-to-noise ratio (SNR) function, and the signal-to-noise ratio (SNR) function. For the quality index of castings, the severity of various defects is often considered, so it is believed at this time The noise ratio function has the property of looking small, that is, the value of the defect index of the desired casting The smaller, the better. The corresponding signal-to-noise ratio is defined as:

where: ηj is the signal-to-noise ratio value under the design scheme of group j process parameters; n is the number of trials corresponding to each group; Yi is the quality characteristic corresponding to the ith test of each group Sex metric response value. From the calculation formula of the signal-to-noise ratio, it can be seen that the higher the signal-to-noise ratio value The larger, the higher the average quality of the casting.
1.2 Orthogonal test
The orthogonal test design is mainly based on the use of formal orthogonal test tables
When designing a protocol of experiments, to determine the best combination between multiple parameters. These combinations have the characteristics of “evenly dispersed, neatly comparable”, so that:Only a small number of tests are needed to meet the requirements of the investigation, which is very large to improve design efficiency. Shuhua used the orthogonal test to find the optimal process parameters of ZL201 aluminum alloy lost foam casting under the comprehensive optimization process goal of filling speed, casting density, tensile strength and elongation performance. Wang Xiansheng et al. used orthogonal test method and quantitative metallographic analysis to study the effect of squeeze casting process parameters on the microstructure of Al-4.80%Cu-0.44%Mn alloy, and the results showed that under the conditions of pouring temperature of 730 °C, mold temperature of 200 °C, pressure of 75MPa, and holding time of about 30 s, the microstructure of squeeze casting could be obtained by squeeze casting. Therefore, orthogonal testing is widely used in the production field for quality control of products.
1.3 TOPSIS
TOPSIS(Technique for Order Preference by
Similarity to Ideal Solution) is an evaluation method based on the reference frame and measures the advantages and disadvantages of the scheme by analyzing the relationship between the alternative and the reference frame. Among them, “positive ideal solution” and “negative ideal solution” are its two basic concepts. The “positive ideal solution” is the hypothetical optimal solution, and its property values reach the best values among the alternatives. The “negative ideal solution” is the worst solution that is conceived, and the values of each attribute reach the worst value of the alternatives. Then, the distance between an evaluation scheme and the positive and negative ideal solutions is compared, so as to calculate the degree of fit between the evaluation scheme and the positive and negative ideal solutions, and the schemes are ranked accordingly, and the scheme with the closest distance from the positive ideal solution and the farthest distance from the negative ideal solution is the optimal scheme.
In order to reduce the degree of air entrapment and the density of surface defects in the casting, Papanikolaou et al. designed the most suitable casting and pouring system by using the TOPSIS method. Cao Feihong et al. used MATLAB and TOPSIS to conduct comprehensive evaluation and analysis, and optimized the parameters of the rack and pinion steering gear, which provides an important method for this kind of optimization design. Therefore, TOPSIS has the advantages of strong practicability, simple calculation, etc., and is widely used.
2 Robustness test
2.1 Camshaft casting quality evaluation
The object of this study is a certain type of QT600-3 camshaft, and its casting three
The Vitu is shown in Figure 1. The process scheme is two boxes of molding, one type of four pieces, using sand gravity casting process, in order to take into account the stability and filling rate of metal liquid filling, the use of intermediate injection gating system. The three-dimensional solid drawings of the mould and casting are shown in Figure 2 and Figure 3, respectively.
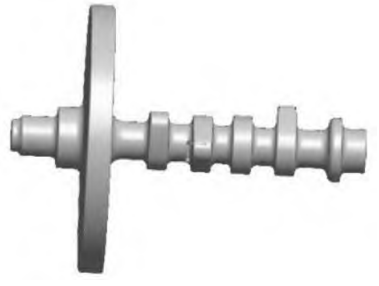
Fig.1. Three-dimensional view of the camshaft
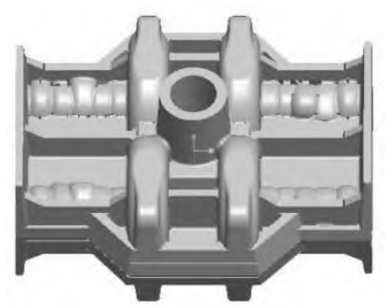
Fig.2. Three-dimensional view of the casting mold

Fig.3. Three-dimensional drawing of casting
Import the above castings and casting molds into the casting simulation software, and compare the models Meshing and generation. According to the damage that occurred during the inspection,
Intersection and volume overlap and other problems are adjusted to the model, and finally the surface is divided into planes The number of meshes is 74 793, and the number of body meshes is 459 525, and the mesh generation is shown in Figure 4. The cooling method of the casting mold is air cooling, the sand mold material is resin sand, and the heat transfer coefficient between the casting and the sand mold is 500 W/(m2· K), the heat transfer coefficient between the casting and the cold iron is 2 000 W/(m2· K)。
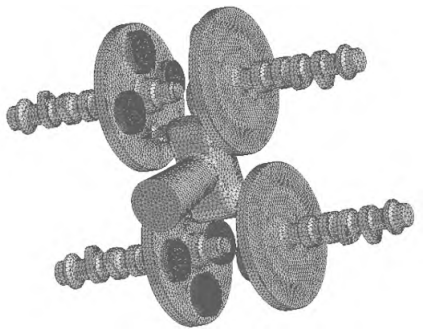
Fig.4. Meshing of castings with the addition of chilled iron
The volume of shrinkage porosity inside the camshaft casting is the same as that of the casting
The density after the shape is the two most critical qualities that reflect the quality of the camshaft
Characteristic indicators. The volume of shrinkage porosity can reflect the specificity of the defect in the casting shrinkage size; The density, on the other hand, reflects the overall shrinkage of the defect
Degree. Since the former is looking at small data, while the latter is looking at large data,Here, in order to unify the data types, the density is expressed as the average shrinkage This paper is used as a quality evaluation standard for camshaft castings. The filling and solidification process of the casting was simulated and analyzed by using the numerical simulation software of the casting process, and the shrinkage and porosity volume and average shrinkage rate of the castings in each simulation test scheme were obtained according to the distribution of shrinkage defects simulated numerically in Figure 5.
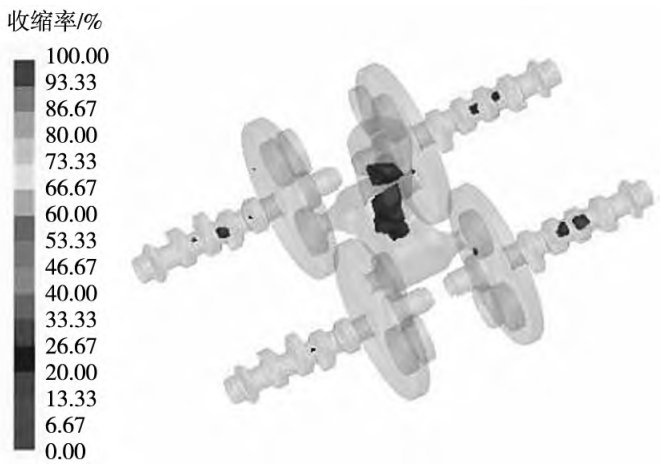
Fig.5. Distribution of shrinkage defects in castings
2.2 Build a regression model
According to the characteristics of the camshaft casting process, the controllable process parameters are selected
The numbers are the mold temperature T1, the pouring time t and the pouring temperature T2. Based on the influence of various factors in the actual casting production, the casting temperature is controlled
20~40 °C, when the molding line is working, the casting temperature is monitored and controlled by the sensing equipment; The pouring time range is 6~14 s, which is converted from the actual pouring work. The pouring temperature was 1 434~1 450 °C, and the molten metal was measured and controlled by a thermometer, as shown in Table 1. Figure 5 simulates the initial process using a mould temperature of 20 °C, a pouring time of 10 s, and a pouring temperature of 1 440 °C.
Table 1 Controllable factors and their value ranges
符号 | 工艺参数 | 单位 | 取值范围 |
T1(A) | 铸型温度 | ℃ | 20~40 |
t(B) | 浇注时间 | s | 6~14 |
T2(C) | 浇注温度 | ℃ | 1434~1450 |
The signal-to-noise ratio of the evaluation index was obtained through the design of internal and external tests Appear. The inner table is used to reflect the specified combination of process parameters and is noise-free The ideal quality condition under the influence of sound, i.e., the total test sample set. Appearance is reversed The castings are affected by various noises when they are tested at each sample point on the inner surface and the actual quality of the situation.
2.3 Interior and exterior test
According to the above analysis, the robustness optimization design involves three controllable factors, circuit fluctuations and rings that may occur in the actual casting process Error factors such as ambient temperature and manual operation will cause controllable process parameters fluctuations, i.e., three corresponding noise factors are generated. Combined with reality, noise The factors will cause the mold temperature to fluctuate by about 5 °C, the pouring time to fluctuate by about 1 s, and the pouring temperature to fluctuate by about 5 °C.
2.4 Signal-to-noise ratio calculation
According to the signal-to-noise ratio calculation formula (1), 1 article can be obtained in the test group
Under the piece, the signal-to-noise ratios of the shrinkage porosity volume and the average shrinkage rate of the casting are respectively is ηVs=20.743, ηAs=1.774. In the same way, the signal-to-noise ratio values of the quality index characteristics of castings in all test groups with and without noise factor interference can be obtained, as shown in Table 8. Since the porosity volume and average shrinkage ratio are different aspects of the quality effect of castings, in order to eliminate the influence of different dimensions and orders of magnitude of these two quality characteristic indicators, it is necessary to standardize them.
3 Multi-objective decision-making
3.1 Weighted canonical signal-to-noise ratio
Multi-objective decision-making problems need to be integrated into single-objective decision-making problems. According to the number and variety of product quality characteristic indicators, the hierarchy can be used Methods such as analysis or expert experience to determine the weight of each quality characteristic index Heavy. The coefficient of variation method is based on the direct use of the information contained in each quality index Objective weighting method to determine its weight, the greater the difference in values, It can better reflect the gap in the indicator and is given a larger weight. Here, according to the quality index data without noise in Table 8, the coefficient of variation method is used to determine the weights.
3.2 TOPSIS Evaluation
The positive ideal solution is the optimal value of each decision objective attribute, and the negative ideal solution is The attribute of each decision target is the worst.
4 Results and Analysis
4.1 Casting process analysis
According to the equilibrium matching properties of the orthogonal test, the comparison of the average closeness of each parameter at different process levels has nothing to do with other parameters, and only reflects the influence of the parameter on multiple process objectives at different process levels.
4.2 Optimal process scheme
The regression prediction statistics of the optimization scheme (A3B3C3) were carried out according to equation (2) and equation (3) with or without noise factor interference, and calculated
The signal-to-noise ratio value of its quality characteristic index. The optimization scheme is then compared to Table 10 The medium group with the highest fit (3 groups, the fit degree was 0.883, and the process parameter combination was A1B3C3) was compared and verified.
4.3 Validation Analysis
The optimal process parameters were numerically simulated and analyzed, and the filling was carried out
and the solidification process and the final shrinkage defects are shown in Fig. 6 and 7, respectively. The casting filling is stable, the solidification is reasonable, and the shrinkage defects are small, so the process scheme is feasible. It is worth noting that the optimization design method considers the noise influencing factors in the actual casting process, and the results have statistical characteristics, that is, the casting has the strongest anti-environmental interference ability under the combination of optimization schemes. Therefore, the best solution obtained is to withstand the noise factor. As shown in Figure 8, the actual finished castings presented under the guidance of the optimization scheme are of good quality and there are basically no shrinkage defects.
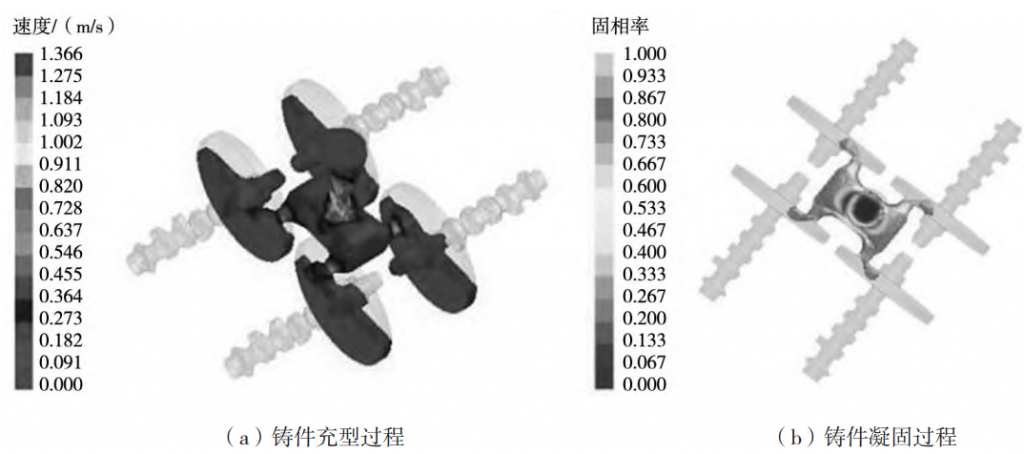
Fig.6. Simulation results of optimal process scheme
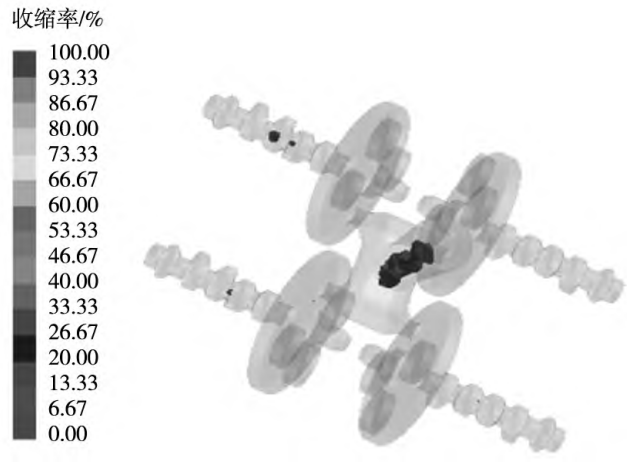
Fig.7. Distribution of shrinkage defects in castings
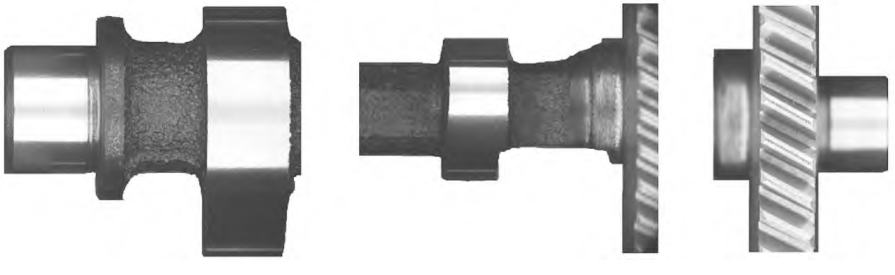
Figure 8 The finished product of the optimized solution
5 Conclusion
(1) This type of camshaft is based on the shrinkage porosity and porosity volume and density of castings
The optimal process parameter scheme for the quality robustness evaluation index is the mold temperature
It was 35 °C, the pouring time was 12 s, and the pouring temperature was 1 446 °C.
(2) Factors affecting the quality and robustness of this type of camshaft casting
The order from large to small is: pouring time, pouring temperature, and mold temperature
Degree.
(3) The combination of signal-to-noise ratio and TOPSIS can be used as a kind of:
Optimize the process parameters to improve the average quality and anti-interference ability of castings
This method provides an idea for the theoretical research and practical production of camshaft casting.