The optimized casting process is shown in Figure 1. The production method of flat casting is adopted, the parting surface is selected on the flange surface of the casting, and the semi closed gating system is adopted. The section ratio of each component is Σ f straight: ∑ f Cross: ∑ f inner =1:2:0.85. In order to make the molten iron cleaner, silicon carbide filter screen is used to reduce the slag hole defects of castings. The pouring temperature is (1390 ± 10) ℃, and the pouring time is 50 s. Compared with the original process, the operation difficulty is greatly reduced, and the sand iron ratio is also reduced. In order to prevent the blowhole defect on the upper box surface, three exhaust strips are added on the upper box surface, and nine overflow slag discharge exhaust risers are placed at the same time. This scheme is simple to operate, and the production efficiency is also improved. However, blowhole defects appear on the upper surface of the casting from time to time (as shown in Figure 2). In order to solve the blowhole on the upper surface of the casting, three parts with a size of 60 mm are made on the upper surface of the casting × (3~5) mm exhaust strips, on which 12 duckbill risers are set, play the role of overflow and exhaust. This process not only has low production rate, but also has low cleaning efficiency, and the defect rate reaches more than 30%.
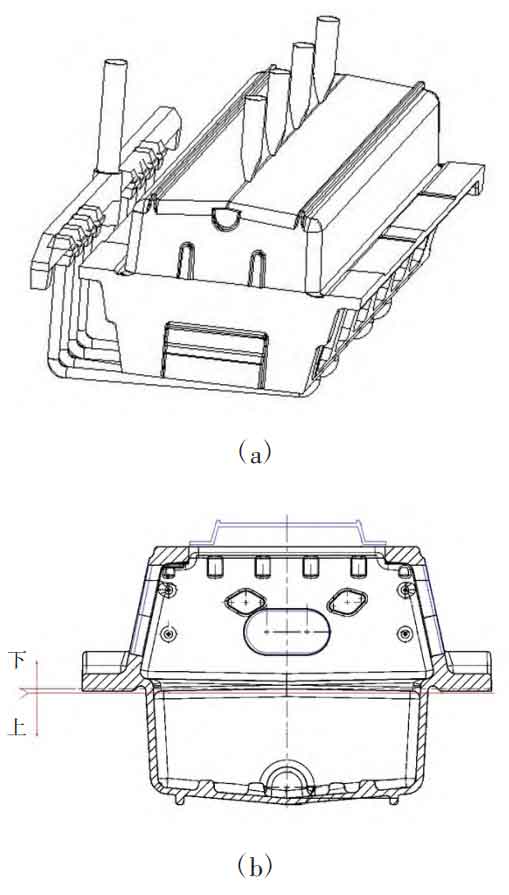
Through analysis, the root cause of this defect lies in the blocked exhaust of the middle large sand core and the drift of the sand core, so it is necessary to strengthen the exhaust of the middle large sand core. In order to prevent the drift of the middle large sand core, fix it in the lower box, and reserve a through hole on the sand core. After the core is lowered, fix the sand core in the lower box, and tie 3 cores in the lower box at the same time φ 50 mm air hole. Add air holes at the corresponding positions of the lower box and the sand core to strengthen the exhaust of the sand core. The sand scraping surface of the sand core must be scraped flat to ensure compactness and prevent the casting from running fire. At the same time, increase the pouring temperature to (1400 ± 10) ℃.
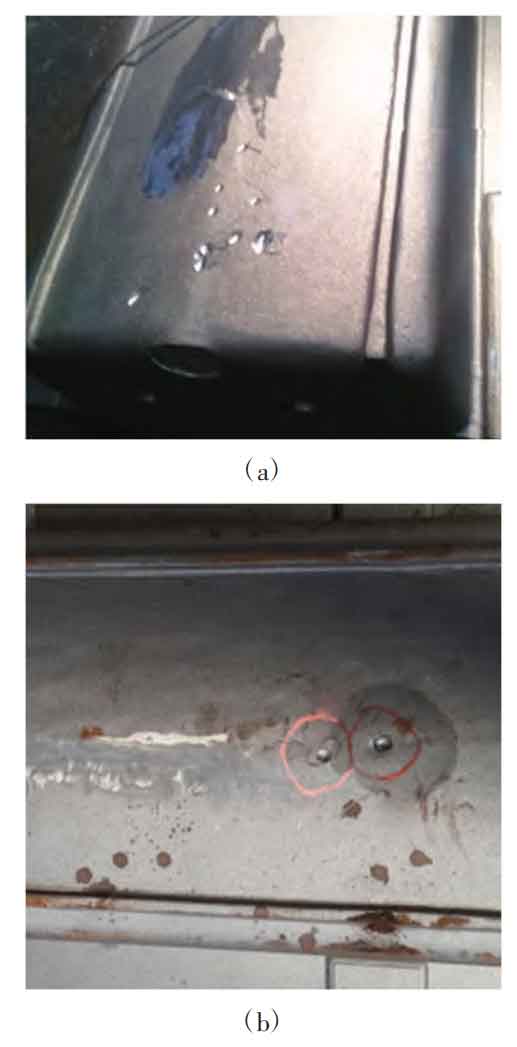
In order to prevent the occurrence of subcutaneous pores, the moisture content of molding sand is controlled at no more than 0.3%, and the permeability of molding sand is improved. Through process improvement, the porosity defects on the upper surface of castings are greatly reduced, and the qualification rate reaches more than 93%. After the pores on the upper surface are eliminated, the overflow riser and slag collecting strip on the upper box surface are optimized to reduce the grinding amount of the subsequent process, and improve the cleaning efficiency of the subsequent process and the process yield of the casting.
Category | Sand iron ratio | Process yield /% | Scrap rate /% |
Original process | 6:1 | 70 | 35 |
Optimize the process | 4.5:1 | 80 | 5 |
The simulation analysis of the filling process of the improved casting process is carried out, as shown in Figure 3. It can be seen that the filling process is stable, and the temperature of the rib plate is high, which is convenient for filling and solves the cold shut and pore defects of the casting.
Figure 4 shows the simulation results of solidification process after process optimization. The change of temperature field is smaller and more uniform than that of horizontal and vertical pouring process. After reducing risers and cold bars, the temperature field on the top surface is more uniform and the probability of defects such as shrinkage porosity, bubbles and cracks is smaller.
The comparison of production before and after process optimization is shown in the table. It can be seen that the process yield is further improved, the scrap rate is reduced from 35% to 5%, and the process optimization effect is good.