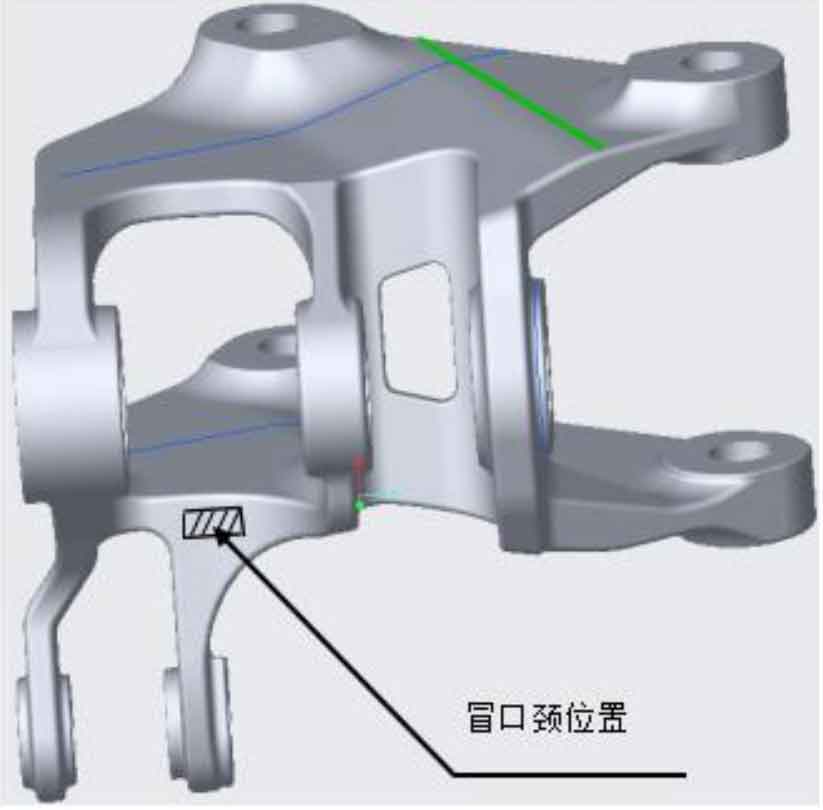
When discussing the original process design of nodular iron castings, it is considered that there is a large hot spot here, and the product feeding is not easy. Instead of using an ordinary riser, 80/110 heating riser sleeve is used for feeding, so that the feeding volume of the riser is increased from about 10% to about 50%, which is embedded in the side ear core, and the riser neck is formed by the clay core to realize the feeding function of nodular iron castings (Fig. 1).
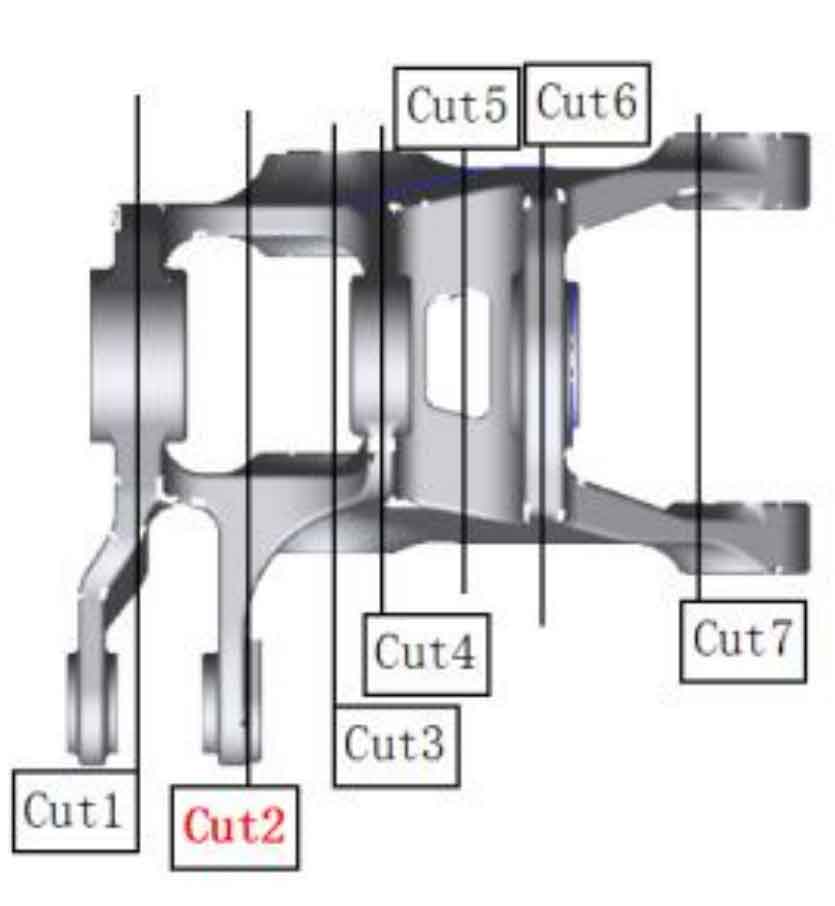
After the product development preparation is completed, the product trial production evaluation is carried out, and the internal casting defects of nodular iron castings are checked and confirmed according to the product evaluation anatomy scheme (Figure 2). There are shrinkage casting defects at the “cut2” position, and even small shrinkage cavities are formed. The area of shrinkage casting defects is 37.0 × 20.0mm, maximum shrinkage: 8.0 × 3.0mm, (Figure 3), the internal casting defects are very serious, which can not meet the quality requirements of users’ products.
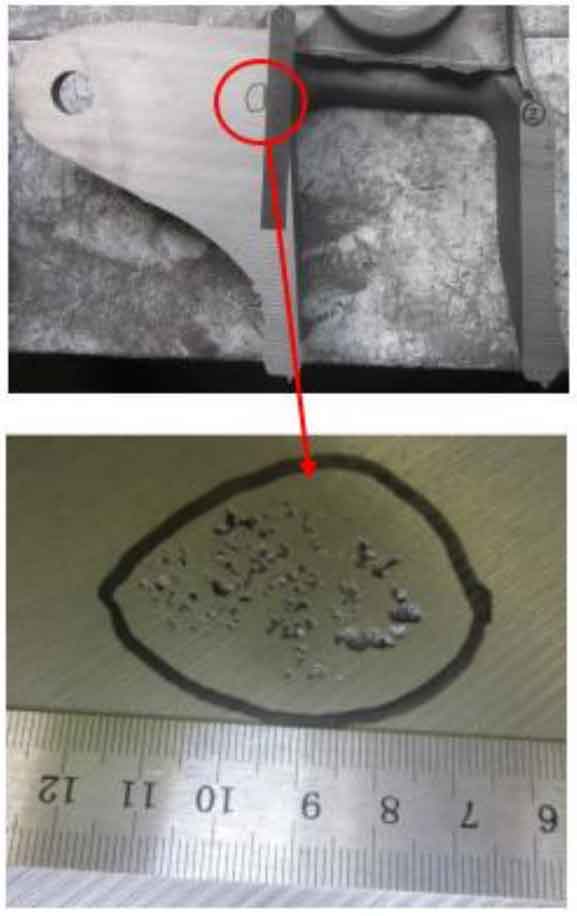
Due to the shrinkage casting defect of the product, the delivery cannot be realized. Through the analysis of the casting defect, it is considered that the feeding effect of the riser is insufficient. We also reduce the shrinkage tendency of molten iron by increasing the cold iron, and 75% is used here × fifty × 15, embedded on the main core (Figure 4). After trial production and verification, the internal casting defects of nodular iron castings were checked and confirmed according to the product evaluation anatomy scheme again. The internal casting defects of nodular iron castings were significantly reduced, and the shrinkage area was 13.0 × 5.0mm, maximum shrinkage: 1.0 × 3.0mm (Figure 5).
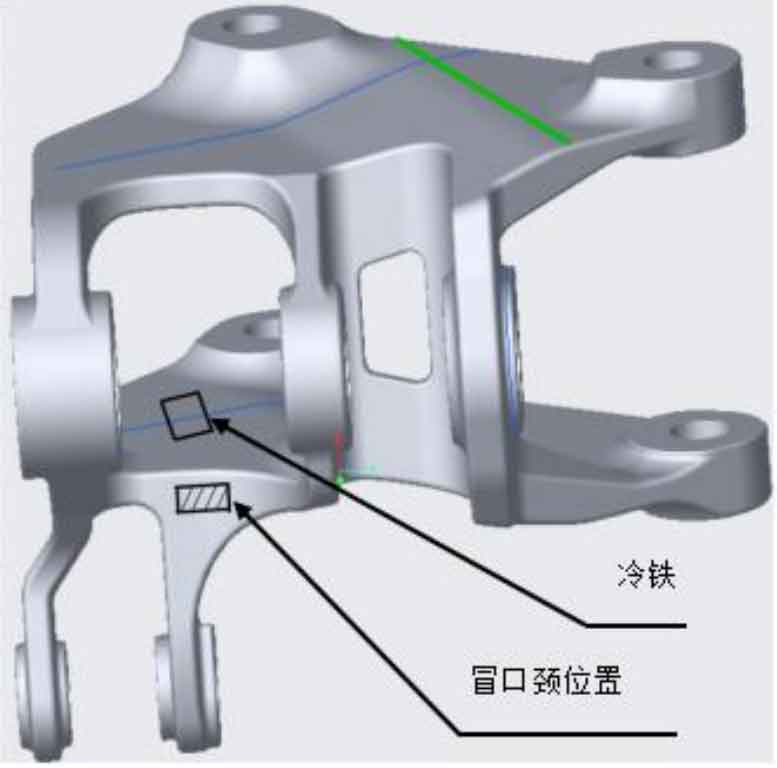
However, it can not meet the quality standard requirements of customers with internal casting defects of nodular iron castings above grade 2, and further improvement is needed.
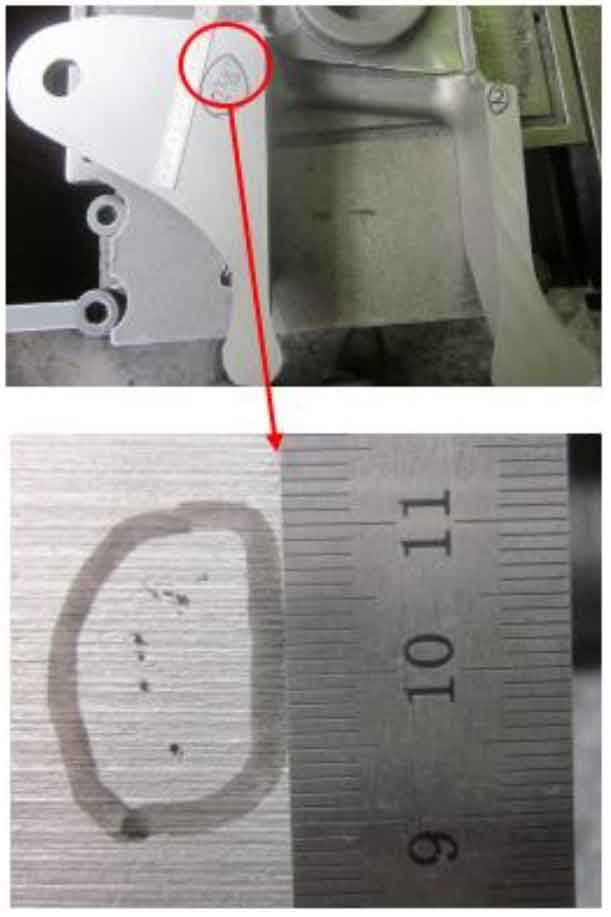