According to the analysis of the casting process defects of the coal mining machine rocker arm shell by the casting products manufacturers, it can be seen that the rocker arm shell cast by the casting products manufacturers using the bottom injection process still has defects, and the pouring system still has shortcomings. It is necessary to optimize and improve the structure and condition parameters of the pouring system.
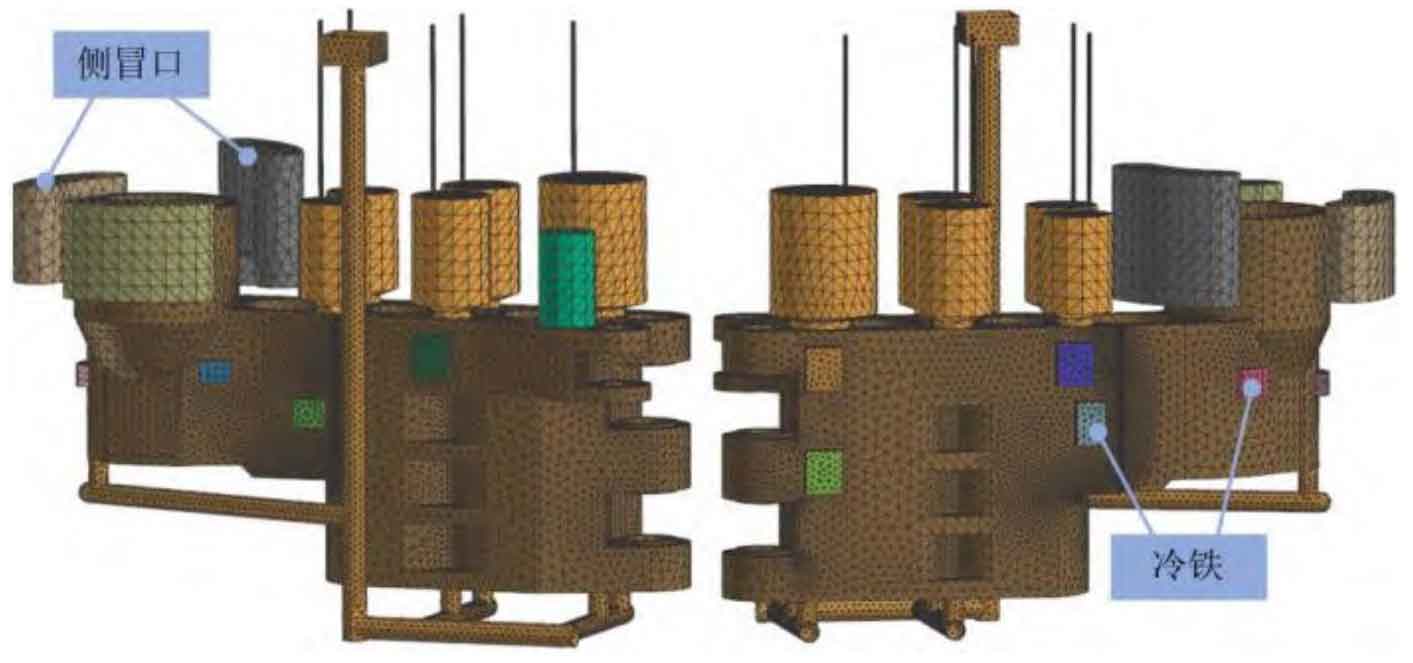
Casting products manufacturers have improved the riser structure and size based on the bottom injection process plan: increasing the riser size at the shell and body pin shaft holes; Change the riser at the output end drum position to a side riser form to effectively supplement the slower solidification parts with molten metal; To reduce the occurrence of casting defects caused by different solidification rates, an external cold iron is added to increase the solidification rate in local areas, ensuring that all parts of the casting solidify almost simultaneously; Raise the preheating temperature of the mold to 300 ℃, slow down the cooling rate of the casting, and ensure that the temperature of each part of the coal mining machine rocker arm shell casting is uniform by the casting products manufacturers, reducing the generation of thermal stress. The optimized pouring system model is shown in Figure 1.
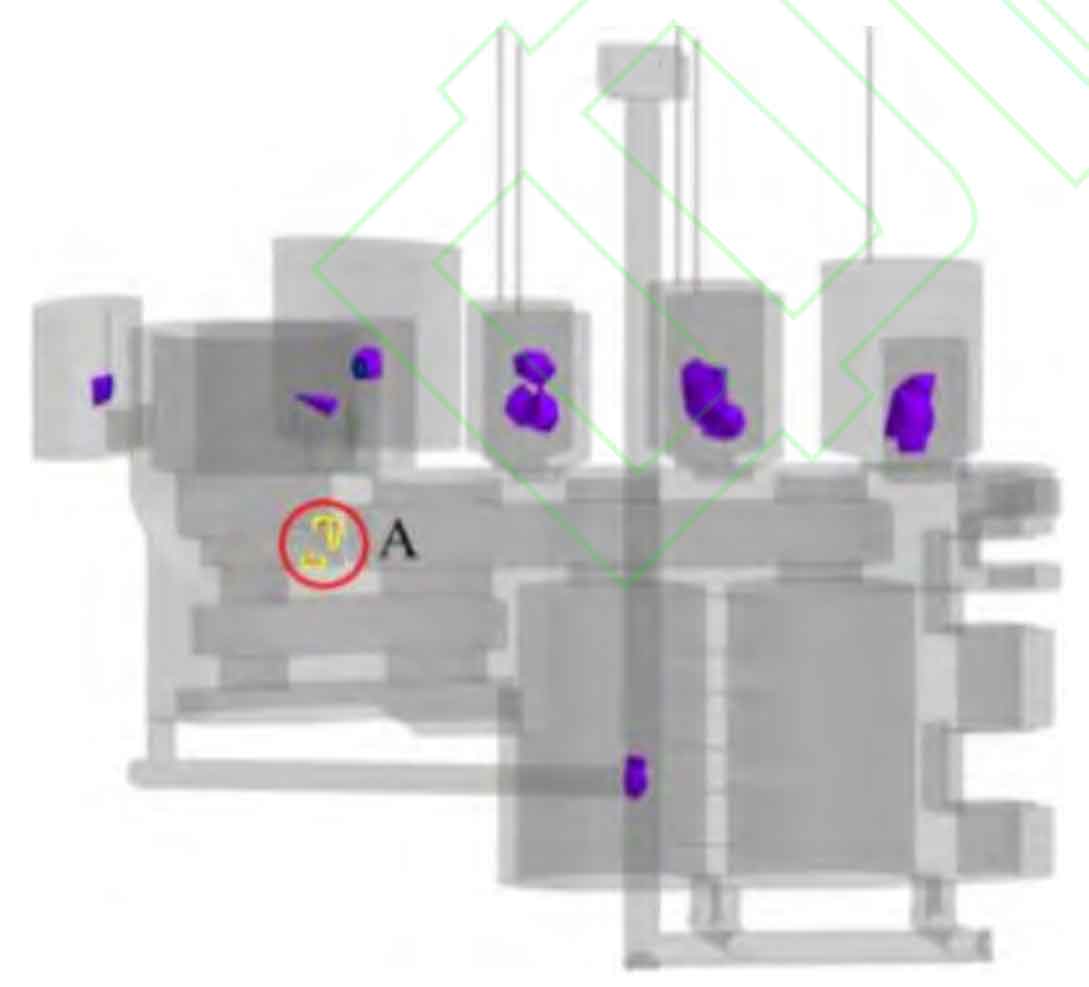
The casting products manufacturers conducted simulation tests on the optimized bottom injection process plan and obtained defect distribution results as shown in Figure 2. According to the Niyama criterion, only a small amount of shrinkage cavities exist at the casting A of the rocker arm housing. The shrinkage volume is 9.01 cm3, with a reduction rate of 93.3% compared to before optimization, accounting for 0.0049% of the volume of the rocker arm shell. The casting products manufacturers have significantly reduced the casting defects of the shearer rocker arm shell castings.
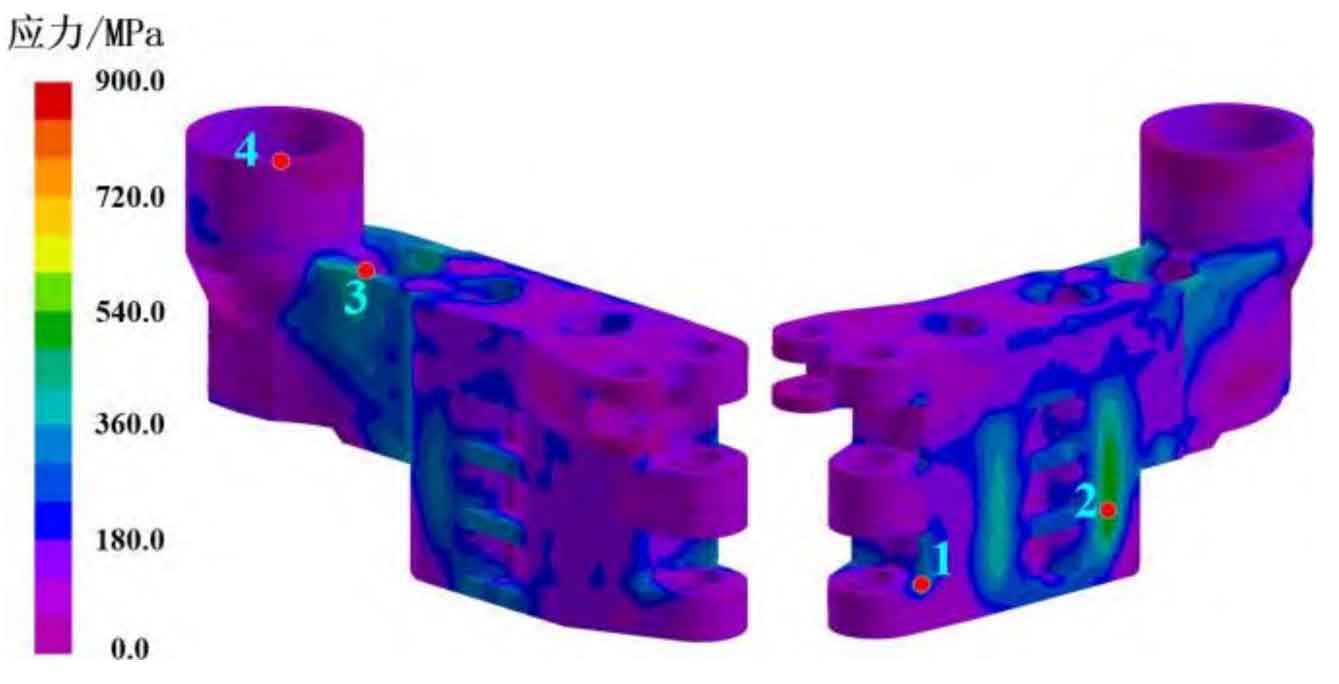
When the casting products manufacturers solidifies and cools the coal mining machine rocker arm shell casting to 50000 s, the stress distribution of the rocker arm shell casting is shown in Figure 3. The optimized stress distribution of castings by casting products manufacturers is mainly between 60~360 MPa, which is significantly reduced compared to the stress distribution before optimization. The stress variation curves of each monitoring point over time are shown in Figure 4. The stress value of monitoring point 2 at the end of the motor hole is 523 MPa, the stress value of monitoring point 1 at the pin shaft hole of the shell and the body is 351 MPa, the stress value of monitoring point 3 at the idler shaft hole on the rear side of the output end of the shell is 449 MPa, and the stress value of monitoring point 4 at the output end hole of the shell is 56.4 MPa. The change pattern of the curve can be seen, The stress changes at each monitoring point gradually flatten with the increase of cooling time.
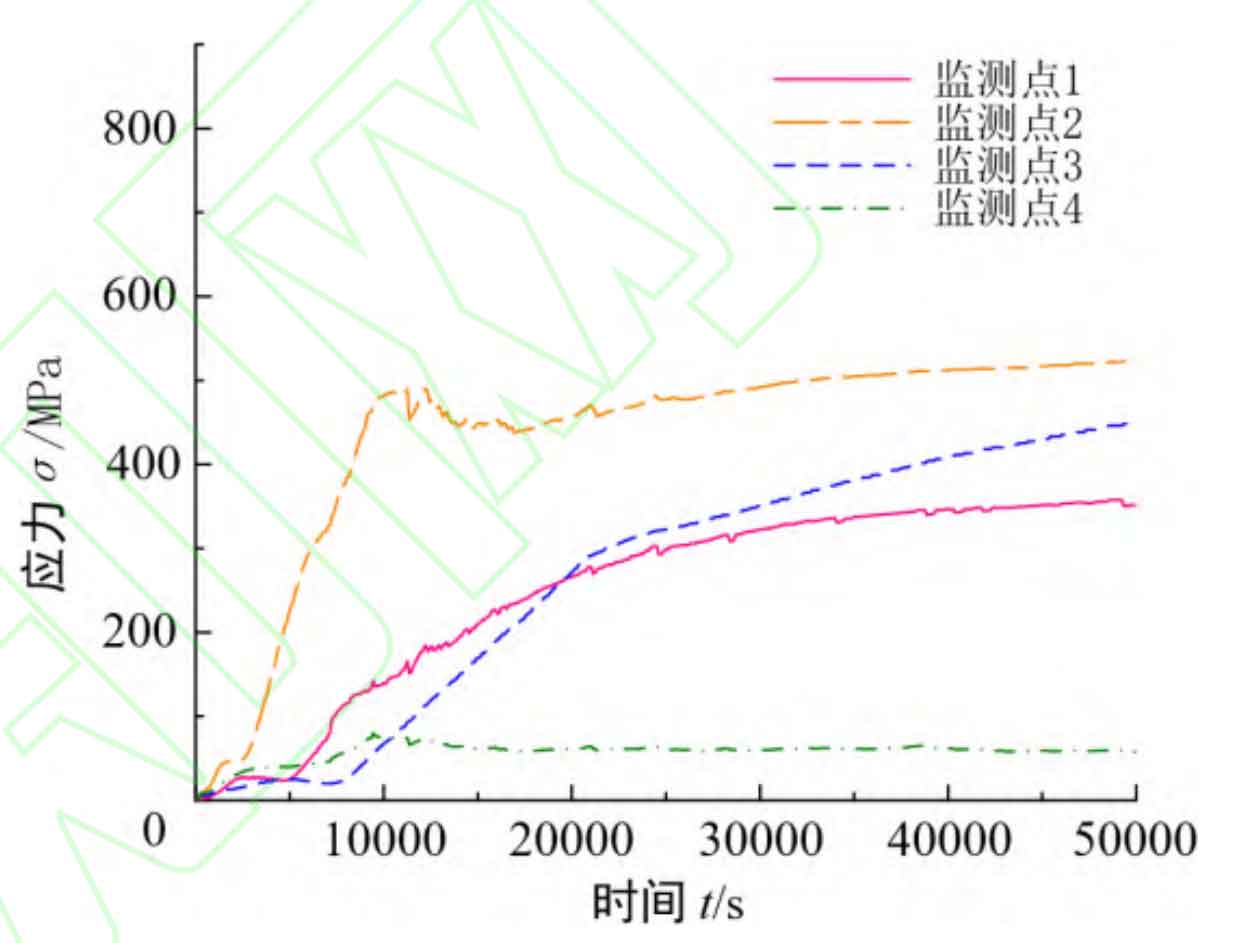
The comparison of stress changes at various monitoring points before and after optimization by the casting products manufacturers is shown in the table. It can be seen that after optimizing the process plan, the stress distribution of the castings is more uniform, and the stress magnitude of some structural connection parts is reduced. The optimization amount at the pin hole of the shell and the body is 49.57%, and the optimization amount at the output end hole of the shell is 91.08%.
Monitoring points | Before optimization/MPa | Optimized/MPa | Optimization amount/% |
1 | 696 | 351 | 49.57 |
2 | 850 | 523 | 38.47 |
3 | 625 | 449 | 28.16 |
4 | 632 | 56.4 | 91.08 |