Certain copper containing cast steel has high strength and plasticity, as well as good low-temperature impact toughness and weldability. In recent years, it has been widely used in the production and manufacturing of offshore platforms or ship components. The size of marine engineering components and new types of ship components is constantly developing towards larger and larger sizes, and the size and wall thickness of components are also increasing. In order to further explore the mechanical performance potential of a copper containing cast steel material with a yield strength grade of 370 MPa, three different sizes of test blocks were cast using this copper containing cast steel, and heat treatment tests and performance tests were conducted to explore the feasibility of using this material to manufacture larger size and wall thickness components.
1. Ingredient requirements
Copper containing cast steel has high strength, toughness, and good weldability, which is closely related to the composition of the steel grade. The chemical composition requirements for copper containing cast steel with a yield strength grade of 370 MPa are shown in Table 1.
C | Si | Mn | P | S | Ni | Cr | V | Cu |
0.10~0.13 | 0.10~0.50 | 0.40~0.80 | ≤0.020 | ≤0.030 | 1.30~1.60 | ≤0.30 | ≤0.10 | 0.50~0.80 |
C element can play a strong role in interstitial solid solution strengthening in cast steel, which is an economically effective strengthening method for improving the strength of steel materials. However, an increase in C content will reduce the toughness of cast steel, increase carbon equivalent, and make welding difficult. In addition, a higher C content will reduce the corrosion resistance of cast steel in the atmosphere. Therefore, the C content in the copper containing cast steel is controlled between 0.10% and 0.13%.
Si element can play a role in deoxidation and reduction in cast steel. Si can improve the strength of cast steel, but the increase of Si will reduce the plasticity and toughness of cast steel. Therefore, the content of Si in cast steel should not be too high.
Mn element can improve the hardness and strength of ferrite and austenite in cast steel, and can also reduce the critical transformation temperature, playing a role in refining pearlite and indirectly improving the strength of pearlite cast steel. Therefore, it is recommended to set a middle and upper limit for the content of Mn.
Cu element plays a role in solid solution strengthening, fine-grained strengthening, and precipitation strengthening in cast steel. Adding Cu element to cast steel can replace traditional carbon strengthening through Cu precipitation strengthening, ensuring excellent weldability while achieving higher yield strength. However, the melting point temperature of Cu is relatively low, at 1084.87 ℃. In order to reduce oxidation and thermal embrittlement during hot processing, the content of Cu element should not be too high.
Ni element plays a role in strengthening ferrite and refining pearlite in cast steel, which can increase strength without significantly reducing toughness and plasticity. Related studies have shown that Ni can combine with Fe and Cu to form a high melting point solid solution. When the nickel copper ratio is greater than 1, the phenomenon of thermal embrittlement can be eliminated.
Adding Cr to cast steel can improve its strength, hardness, oxidation resistance, wear resistance, and corrosion resistance, but at the same time reduce plasticity and toughness. Adding V to cast steel can refine grain size, improve the strength and low-temperature toughness of cast steel.
2. Test materials and methods
2.1 Test materials
The copper containing cast steel material was melted in an electric arc furnace, and then refined using LF+VD. The melted cast steel liquid was poured into test blocks A, B, and C with wall thicknesses of 300 mm, 400 mm, and 450 mm. The details of each test block are shown in Table 2.
Test block name | Size specifications | Quantity | Number |
Test block A | 300 mm x 300 mm x 500 mm | 4 | A1-A4 |
Test block B | 400 mm x 400 mm x 650 mm | 3 | B1-B3 |
Test block C | 450 mm x 450 mm x 650 mm | 3 | C1-C3 |
2.2 Test methods
Number | Preparation heat treatment | Normalized heat treatment | Tempering heat treatment |
A1 | 660 ℃ x 216 h electric furnace | 920 ℃ x 7 h air-cooled | 620 ℃ x 10 h |
A2 | 660 ℃ x 216 h electric furnace | 920 ℃ x 7 h air-cooled | 620 ℃ x 10 h |
A3 | 660 ℃ × 216 h gas furnace | 920 ℃ x 7 h air-cooled | 620 ℃ x 10 h |
A4 | 660 ℃ × 216 h gas furnace | 920 ℃ x 7 h air-cooled | 620 ℃ x 10 h |
The heat treatment process of the copper containing cast steel material is: preparatory heat treatment → normalizing heat treatment → tempering heat treatment. The purpose of preparing heat treatment is to reduce hydrogen content, avoid material plasticity and impact failure; Using normalizing heat treatment to refine the grain structure and obtain the required metallographic structure; Finally, the mechanical properties of the material meet the requirements for use through appropriate temperature tempering heat treatment.
Number | Preparation heat treatment | Normalized heat treatment | Tempering heat treatment |
B1 | 660 ℃ × 324 h electric furnace | 920 ℃ x 9 h air-cooled | 620 ℃ x 13 h |
B2 | 660 ℃ × 324 h electric furnace | 920 ℃ x 9 h air-cooled | 620 ℃ x 13 h |
B3 | 660 ℃ × 324 h gas furnace | 920 ℃ x 9 h air-cooled | 620 ℃ x 13 h |
According to the wall thickness and size specifications of the test blocks, they are grouped for heat treatment, and the process parameters for each heat treatment process are selected according to the recommended parameters in the process specifications. At the same time, according to different experimental purposes, two methods of hydrogen removal in electric furnace and gas furnace were used for comparison in the preparation heat treatment, and the cooling method after normalizing the test block was also compared using blowing and air cooling. The heat treatment process plans for test blocks A, B, and C are shown in Tables 3-5.
Number | Preparation heat treatment | Normalized heat treatment | Tempering heat treatment |
C1 | 660 ℃ × 324 h electric furnace | 920 ℃ x 10 h air-cooled | 620 ℃ x 15 h |
C2 | 660 ℃ × 324 h electric furnace | 920 ℃ x 10 h air-cooled | 620 ℃ x 15 h |
C3 | 660 ℃ × 324 h gas furnace | 920 ℃ x 10 h air-cooled | 620 ℃ x 15 h |
After the heat treatment is completed, samples are taken from the outside, T/4 wall thickness position, and core position of each test block, with one sample taken from each position Φ 10 mm standard tensile specimens and a set of standard Charpy V-shaped impact specimens, all tensile tests shall be carried out in accordance with GB/T 228, and all impact tests shall be carried out in accordance with GB/T 229. The test results of copper containing cast steel materials shall meet Table 6.
Lower yield strength ReL/MPa | Elongation after fracture A/% | Tensile strength Rm/MPa | Reduction of area Z/% | -40 ℃ shock absorption energy KV2/J |
≥ 370 | ≥ 20 | ≥ 490 | ≥ 40 | ≥ 27 |
3. Test results and analysis
3.1 300 mm wall thickness test block A
A test block with a wall thickness of 300 mm was divided into four groups for orthogonal testing. Test blocks A1 and A2 were subjected to electric furnace dehydrogenation, while test blocks A3 and A4 were subjected to gas furnace dehydrogenation; A1 and A3 test blocks are air-cooled after normalizing, while A2 and A4 test blocks are air-cooled after normalizing. The results of sampling and testing at the outer, T/4, and core positions of the 300 mm wall thickness test block are shown in Table 7.
Test number | Sampling location | Rm/MPa | ReL/MPa | A/% | Z/% | -40 ℃ KV2/J |
A1 | External | 518 | 392 | 30.0 | 76 | 63 |
A1 | T/4 | 516 | 393 | 31.0 | 74 | 86 |
A1 | Core part | 511 | 391 | 30.5 | 74 | 89 |
A2 | External | 521 | 395 | 32.5 | 73 | 69 |
A2 | T/4 | 517 | 394 | 31.5 | 73 | 71 |
A2 | Core part | 514 | 393 | 31.5 | 72 | 86 |
A3 | External | 515 | 392 | 31.5 | 74 | 73 |
A3 | T/4 | 509 | 388 | 32.0 | 72 | 79 |
A3 | Core part | 510 | 389 | 31.5 | 74 | 85 |
A4 | External | 521 | 398 | 31.5 | 75 | 73 |
A4 | T/4 | 515 | 392 | 33.0 | 74 | 82 |
A4 | Core part | 515 | 391 | 32.5 | 73 | 82 |
According to the test data in Table 7, comparing the impact values, elongation after fracture, and cross-sectional shrinkage of A1 and A3, A2 and A4 test blocks, it can be found that under the same conditions of pretreatment and positive tempering process parameters, the plasticity and toughness values after using gas furnace for hydrogen removal are comparable to those of electric furnace for hydrogen removal. This proves that a higher [H] atmosphere in gas furnace does not affect the hydrogen removal effect, and using gas furnace for hydrogen removal in copper containing cast steel can achieve the same effect as electric furnace for hydrogen removal. Comparing the yield strength and tensile strength values of A1 and A2, A3 and A4 specimens, it can be found that within a certain cooling rate range, the normalizing cooling rate has a certain help in improving the strength of copper containing cast steel materials, but the improvement is not significant. Comparing the test results of the external, T/4, and core positions of the test block, it was found that as the sampling depth increased, the strength of the copper containing cast steel material slightly decreased and the toughness slightly improved; The performance results of four test blocks with a wall thickness of 300 mm and three sampling positions all meet the technical requirements.
3.2 400 mm wall thickness test block B
Test block B with a wall thickness of 400 mm was divided into three groups for testing. Test blocks B1 and B2 were subjected to hydrogen removal using an electric furnace, while test block B3 was subjected to hydrogen removal using a gas furnace; The B1 test block undergoes two rounds of positive tempering, with the first round using air cooling and the second round using air cooling. The B2 and B3 test blocks undergo one round of positive tempering, with air cooling used for normalization. The results of sampling and testing at the outer, T/4, and core positions of the 400 mm wall thickness test block are shown in Table 8.
Test number | Sampling location | Rm/MPa | ReL/MPa | A/% | Z/% | -40 ℃ KV2/J |
B1 | External | 518 | 397 | 33.5 | 76 | 71 |
B1 | T/4 | 501 | 384 | 33.5 | 75 | 86 |
B1 | Core part | 498 | 378 | 33.5 | 76 | 100 |
B2 | External | 513 | 390 | 33.0 | 77 | 68 |
B2 | T/4 | 496 | 377 | 33.0 | 75 | 81 |
B2 | Core part | 493 | 375 | 32.5 | 76 | 83 |
B3 | External | 512 | 388 | 32.5 | 76 | 69 |
B3 | T/4 | 495 | 376 | 33.5 | 76 | 78 |
B3 | Core part | 491 | 370 | 33.0 | 76 | 84 |
According to the test data in Table 8, comparing the impact value, elongation after fracture, and cross-sectional shrinkage of B2 and B3 test blocks, it can be found that under the same conditions of pre-treatment and positive tempering process parameters, the plasticity and toughness values after gas furnace dehydrogenation are very close to those after electric furnace dehydrogenation. This further proves that using gas furnace dehydrogenation can achieve the same effect as electric furnace dehydrogenation in copper containing cast steel, with higher [H] in gas furnace The atmosphere does not affect the dehydrogenation effect; The performance of the B1 test block after two rounds of normalizing heat treatment is higher than that of the B2 and B3 test blocks after only one round of normalizing heat treatment. The yield strength is increased by 7-9 MPa, the tensile strength is increased by 5-7 MPa, and the impact toughness is also better.
By comparing the test results of the outer, T/4, and core positions of the 400 mm wall thickness test block, it can be observed that the strength gradually decreases from the outside to the inside; The performance of the three sampling positions of the 400mm wall thickness test block meets the technical requirements, but the strength is lower than that of the sampling positions of the 300mm wall thickness test block. It is speculated that the decrease in strength is related to the increase in wall thickness of the test block.
3.3 450 mm wall thickness test block C
Test block C with a wall thickness of 450 mm is divided into three groups for testing. The C1 and C2 test blocks are subjected to hydrogen removal using an electric furnace, while the C3 test block is subjected to hydrogen removal using a gas furnace; After normalizing, C1 and C3 test blocks are cooled by air, while C2 test blocks are cooled by air. The results of sampling and testing at the outer, T/4, and core positions of the 450mm wall thickness test block are shown in Table 9.
Test number | Sampling location | Rm/MPa | ReL/MPa | A/% | Z/% | -40 ℃ KV2/J |
C1 | External | 499 | 382 | 34.0 | 76 | 69 |
C1 | T/4 | 488 | 368 | 34.5 | 76 | 70 |
C1 | Core part | 487 | 367 | 35.0 | 74 | 86 |
C2 | External | 492 | 368 | 34.0 | 76 | 70 |
C2 | T/4 | 483 | 359 | 33.5 | 76 | 79 |
C2 | Core part | 480 | 358 | 34.5 | 75 | 82 |
C3 | External | 496 | 375 | 34.0 | 74 | 70 |
C3 | T/4 | 484 | 365 | 33.5 | 75 | 78 |
C3 | Core part | 483 | 364 | 34.5 | 74 | 79 |
According to the test data in Table 9, comparing the impact value, elongation after fracture, and cross-sectional shrinkage of C1 and C3 test blocks, it can be found that under the same pre-treatment and tempering process parameters, the plasticity and toughness values after gas furnace dehydrogenation are very close to those after electric furnace dehydrogenation. This once again proves that using gas furnace dehydrogenation can achieve the same effect as electric furnace dehydrogenation in copper containing cast steel; Comparing the yield strength and tensile strength values of C1 and C2 specimens, it can be found that within a certain cooling rate range, the normalizing cooling rate has a certain help in improving the strength of copper containing cast steel materials, but the improvement is not very significant. Comparing the test results of different sampling positions on the outside, T/4, and core of the 450 mm wall thickness test block, it can be found that for copper containing cast steel test blocks with larger wall thickness, the strength of the three positions of the test block shows a more obvious trend of gradually decreasing from the outside to the inside. External sampling can meet the technical requirements, but the results of T/4 and core sampling positions are already lower than the technical requirements. Comparing the performance of 300 mm and 400 mm wall thickness test blocks, after the selection of heat treatment process parameters is limited, the strength index of copper containing cast steel test blocks continuously decreases as the wall thickness of the test blocks further increases. How to achieve the mechanical performance indicators of 310 mm wall thickness test blocks for copper containing steel castings with larger wall thickness needs to be explored from the aspects of optimizing material composition or casting performance.
4. Metallographic testing
Test number | Sampling location | Metallographic structure | Grain size |
A1 | External | Ferrite+Pearlite | 7 |
A1 | T/4 | Ferrite+Pearlite | 7 |
A1 | Core part | Ferrite+Pearlite | 7 |
A2 | External | Ferrite+Pearlite | 7 |
A2 | T/4 | Ferrite+Pearlite | 7 |
A2 | Core part | Ferrite+Pearlite | 6.5 |
A3 | External | Ferrite+Pearlite | 7 |
A3 | T/4 | Ferrite+Pearlite | 7 |
A3 | Core part | Ferrite+Pearlite | 7 |
A4 | External | Ferrite+Pearlite | 7 |
A4 | T/4 | Ferrite+Pearlite | 6.5 |
A4 | Core part | Ferrite+Pearlite | 6.5 |
After the mechanical performance test, the microstructure was inspected using impact residual samples from the outer, T/4, and central parts of 300mm, 400mm, and 450mm wall thickness test blocks, and the grain size was evaluated. The metallographic examination and grain size rating results of the external, T/4, and central positions of three different size specifications of test blocks are shown in Table 10-12. The metallographic and microstructural photos of some test blocks are shown in Figure.
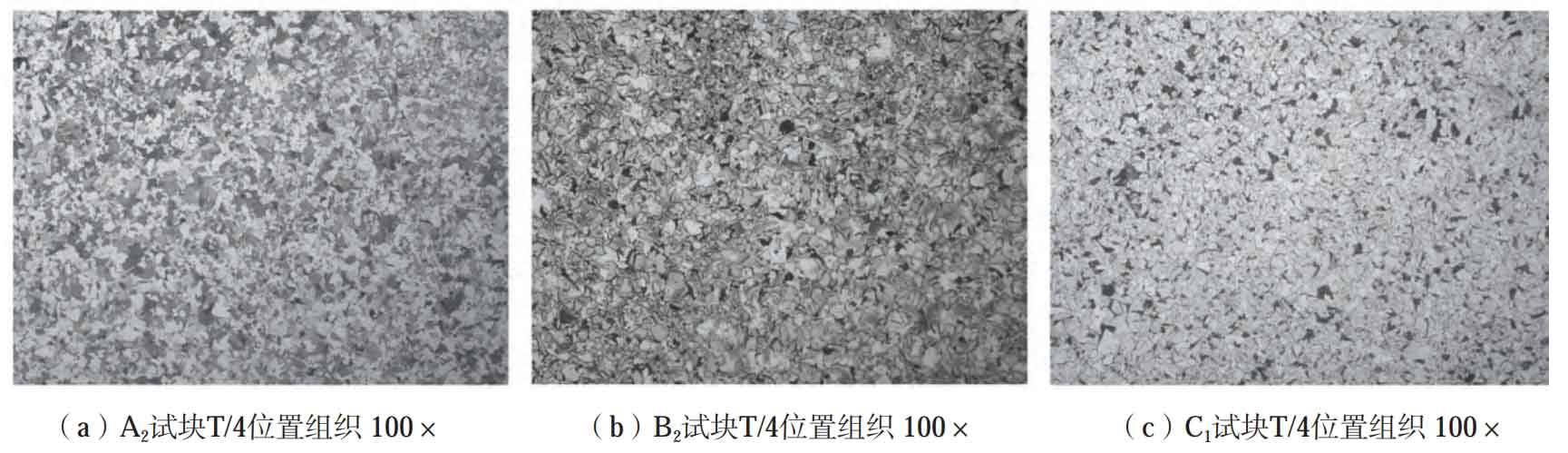
Test number | Sampling location | Metallographic structure | Grain size |
B1 | External | Ferrite+Pearlite | 7.5 |
B1 | T/4 | Ferrite+Pearlite | 7.5 |
B1 | Core part | Ferrite+Pearlite | 7.5 |
B2 | External | Ferrite+Pearlite | 7 |
B2 | T/4 | Ferrite+Pearlite | 6.5 |
B2 | Core part | Ferrite+Pearlite | 6.5 |
B3 | External | Ferrite+Pearlite | 7 |
B3 | T/4 | Ferrite+Pearlite | 6.5 |
B3 | Core part | Ferrite+Pearlite | 6.5 |
The microstructure of three different sized test blocks after heat treatment is ferrite+pearlite structure. There is no significant difference in the grain size grades of the external, T/4, and core positions. The grain size grades are mostly 6.5-7. The B1 test block after two rounds of normalizing heat treatment has finer grains, which are 7.5 levels. By comparing the microstructure photos of the T/4 positions of the 300 mm, 400 mm, and 450 mm wall thickness specimens after normalizing air cooling, it can be found that there is a higher content of pearlite in the metallographic structure of the 300 mm wall thickness specimens, while the content of pearlite in the metallographic structure of the 450 mm wall thickness specimens is lower. The amount of pearlite content affects the strength of the specimens.
Test number | Sampling location | Metallographic structure | Grain size |
C1 | External | Ferrite+Pearlite | 6.5 |
C1 | T/4 | Ferrite+Pearlite | 6.5 |
C1 | Core part | Ferrite+Pearlite | 6.5 |
C2 | External | Ferrite+Pearlite | 6.5 |
C2 | T/4 | Ferrite+Pearlite | 6.5 |
C2 | Core part | Ferrite+Pearlite | 6.5 |
C3 | External | Ferrite+Pearlite | 6.5 |
C3 | T/4 | Ferrite+Pearlite | 6.5 |
C3 | Core part | Ferrite+Pearlite | 6.5 |
5. Conclusion
(1) Under the same conditions of pre-treatment and positive tempering process parameters, the plasticity and toughness of copper containing cast steel materials after hydrogen removal by gas furnace and electric furnace are not significantly different. This proves that a higher hydrogen atmosphere in gas furnace does not affect the hydrogen removal effect. Copper containing cast steel can achieve the same effect of hydrogen removal by electric furnace using gas furnace.
(2) Within a certain cooling rate range, the normalizing cooling rate is helpful in improving the strength of copper containing cast steel materials, but the improvement is not significant.
(3) The comprehensive mechanical properties of copper containing cast steel after two rounds of normalizing heat treatment are better than those after only one round of normalizing heat treatment. Through metallographic examination, it was found that the grains after two rounds of normalizing heat treatment are finer.
(4) The same test block, from the surface to the core, shows a decreasing trend in strength and an increasing trend in toughness as the sampling depth increases.
(5) As the wall thickness of the test block increases, the performance results of the test block after heat treatment gradually decrease. After the wall thickness of the test block exceeds 450 mm, only external sampling can meet the technical requirements, and the results of T/4 and core sampling positions no longer meet the technical requirements.