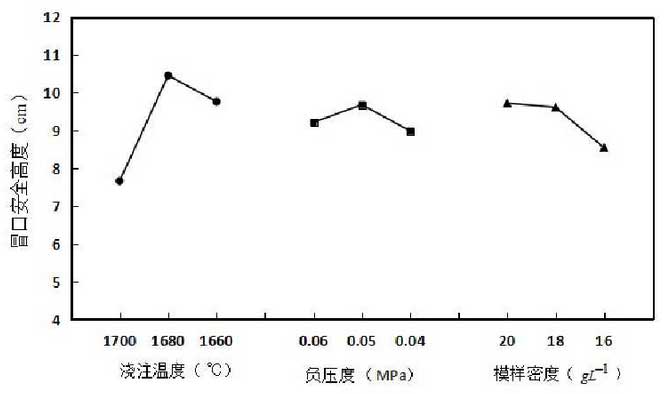
It can be seen from Fig. 1 that when the pouring temperature changes from high to low, the safe height of the riser first increases greatly and then decreases slightly. This shows that when the pouring temperature is too high, the volume shrinkage of molten steel increases, and the amount of feeding liquid in riser also increases. At the same time, because the pouring is side bottom pouring, too high pouring temperature will affect the sequential solidification of castings, resulting in the decrease of feeding effect of risers. When the pouring temperature is too low, due to the absorption and absorption of a large amount of thermal energy from the foam pattern, especially the open top riser away from the gate, the heat loss of the molten metal is too fast, resulting in shorter riser solidification time, which is not conducive to the feeding of the riser.
When the negative pressure changes from high to low, the test results show a trend of first increase and then decrease, but the change range is not large. Negative pressure is conducive to the rapid discharge of the pyrolysis products of foam pattern, reducing the air gap pressure between metal liquid and solid foam, and reducing the soft dynamic force and heat loss of molten metal. Although the negative pressure degree has little effect on the test results, too high or too low negative pressure will affect the filling status and filling speed of molten metal, and then affect the temperature field distribution of castings. Therefore, the range of negative pressure should be appropriate.
The effect of pattern density on the test results is second only to pouring temperature, and the test results show a downward trend with the decrease of pattern density. This shows that when the density of the pattern decreases gradually, the heat consumption of the pattern gasification decreases due to the decrease of pyrolysis products and the acceleration of filling speed. The superheat of molten steel increases, and the shrinkage rate of Afterbody increases, which reduces the feeding effect of riser. At the same time, if the pattern density is too low, the front edge of molten metal will appear turbulent soft state, which will increase the risk probability of carburization and air entrapment, and reduce the internal quality of steel castings. In addition, if the pattern density is too low, the overall strength of the model will decrease and the blank size of the casting will be affected. Therefore, in practice, the foam with low density is generally not used. However, in order to reduce the residue of pyrolysis products and the effect of Carburizing on steel castings, the method of making hollow foam is usually adopted, which not only improves the overall strength of the pattern, but also reduces the average density of the pattern, and also reduces the cost of the sample material.
The purpose of orthogonal test is to make the best feeding effect and the highest safety height of riser, that is, the larger the index value, the better. Through the above range analysis and comparison, the optimal combination is a2b2c1, namely pouring temperature 1680 ℃, negative pressure 0.05Mpa, pattern density 20g / L.
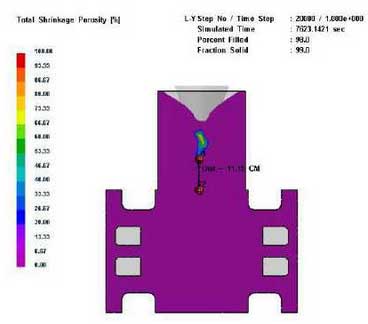
According to the optimal combination of process parameters obtained from the above orthogonal test, the simulation calculation is carried out. The calculation results show that the safe height of riser is 11.15cm, which is 0.63cm higher than that of test No.4 (10.52cm), as shown in Fig.2.