1. Introduction
The metal pressure vessel industry is an important part of the equipment manufacturing industry and reflects a country’s comprehensive national strength. With the development of China’s national economy and the increasing attention and support for the high-end equipment manufacturing industry, the demand for metal pressure vessels in China has been continuously increasing. Low-pressure casting technology has the advantages of good overall structure, high reliability, light weight and low processing cost of castings, so it is suitable for casting parts related to pressure vessels. The aluminum alloy sleeve used for pressure vessels has special working environment and high requirements for hardness, tensile strength and airtightness of the part itself. Therefore, this paper studies the aluminum alloy sleeve used for pressure vessels, uses Flow – 3D Casting software to simulate the casting process, in order to predict and eliminate possible defects in production through simulation, obtain the optimal low-pressure casting process scheme, effectively improve the process yield of parts, and provide a reference for the process design of aluminum alloy casting sleeves.
2. Product Analysis and Process Design
2.1 Product Analysis
The sleeve has a pouring temperature of , uses sand mold low-pressure casting based on dried and scrubbed sand, the initial temperature of the mold is , and the material is A356. A356 is a common die-casting alloy with excellent casting, mechanical and physical properties, but it also has some casting defects such as holes and non-metallic inclusions due to shrinkage during solidification and easy dissolution of hydrogen in the molten state. The three-dimensional model of the sleeve shows that its flange size is , the cylinder body size is , the inner diameter is , and the overall height is . The casting is required to have no casting defects such as pores and shrinkage porosity. After casting, the sleeve will undergo shot blasting treatment, heat treatment and mechanical processing, and then complete the detection of chemical composition, mechanical properties, appearance, material quality and size. Finally, hydraulic pressure test, airtightness test and hydraulic pressure destruction test will be carried out.
2.2 Process Design
The “Ozan” formula is introduced into low-pressure casting to obtain the calculation formula. The cross-sectional area of the inner runner is determined to be . The casting system and chill distribution are designed according to the principle of sequential solidification. The inner runner is designed to be evenly distributed at the thick wall of the casting to ensure uniform cooling and small stress of each part of the casting. Chills are set at the flange and the top of the sleeve to ensure the product quality of the casting. The pressure required for solidification molding is calculated according to a certain formula.
Scheme Number | Filling Time /s | Liquid Rising and Filling Pressure /Pa | Solidification Molding Pressure /Pa |
---|---|---|---|
Scheme 1 | 5 | 10000 | 50000 |
Scheme 2 | 10 | 4000 | 20000 |
Scheme 3 | 15 | 2000 | 20000 |
3. Low Pressure Casting Pressure Curve Design Analysis
Low-pressure casting combines the anti-gravity casting filling principle and the casting crystallization principle under pressure. The low-pressure casting process of cylindrical parts is one of the most common and mature processes in production. The pressure curves of the three schemes are calculated according to the structure parameters of the casting and the actual production situation, and the process parameters of the three schemes are determined as shown in the above table.
4. Process Scheme Optimization
4.1 Process Scheme 1
- Speed Field Simulation Results: The flow velocity of the metal liquid in the inner runner is and respectively, and there is air entrainment, which will affect the physical and mechanical properties of the casting and cause problems such as stress concentration. The flow velocity of the liquid surface is , and there is turbulence and churning, which increases the risk of gas entering the metal liquid.
- Oxidation Slag Distribution Simulation Results: The contact area between the metal liquid and air is small in the early stage, and the oxidation slag is less. In the later stage, the contact area increases, the oxidation film breaks and is involved in the metal liquid, and the content of secondary slag in the metal liquid increases.
- Temperature Field Simulation Results: The metal liquid flows into the mold at a temperature of . The pouring temperature is high, which increases the superheat of the melt, reduces the viscosity, relatively extends the filling and solidification time, and improves the fluidity and filling ability. However, if the pouring temperature is too high, it will increase the total shrinkage of the alloy and the amount of gas absorption, and is prone to casting defects such as shrinkage holes and shrinkage porosity. The temperature distribution at the flange is reasonable, which is conducive to the sequential solidification of the casting and verifies the rationality of the chill distribution position.
4.2 Process Scheme 2
- Speed Field Simulation Results: Compared with Scheme 1, the velocity distribution gradient of Scheme 2 becomes smaller. The flow velocity of the metal liquid in the inner runner is , and there is still air entrainment. The flow velocity of the liquid surface is , and there is turbulence. When the metal liquid flows through the flange, the flow is blocked and the flow velocity is still large.
- Oxidation Slag Distribution Simulation Results: The contact area between the metal liquid and air is small in the early stage, and the oxidation slag is less. In the later stage, the contact area increases, and the oxidation slag is more than that of Scheme 1. The turbulence of the metal liquid is weakened, and the contact opportunity between the metal liquid and air is less. The oxidation slag distribution is reasonable.
- Temperature Field Simulation Results: The metal liquid temperature distribution is , which is the same as that of Scheme 1. The temperature distribution at the flange is , the temperature distribution gradient is large, and a too low pouring temperature may cause cold shut and insufficient pouring.
4.3 Process Scheme 3
- Speed Field Simulation Results: The filling pressure of Scheme 3 is further reduced. The flow velocity of the metal liquid in the inner runner is and respectively, and the air entrainment disappears. The flow velocity of the liquid surface is , and the turbulence duration is shortened.
- Oxidation Slag Distribution Simulation Results: The flow velocity of the metal liquid is slow, and the contact time with air is long, so the surface oxidation slag production increases. In the later stage, the contact area between the metal liquid and air increases, but the liquid surface is stable, there is no air entrainment and turbulence, and the oxidation slag production decreases.
- Temperature Field Simulation Results: The metal liquid temperature distribution is , which is the same as that of the previous two schemes. The temperature distribution at the flange is , the temperature distribution gradient is reduced, and it is conducive to sequential solidification.
5. Conclusion
Through the analysis of the sleeve structure and production requirements, the casting system is designed, three casting process schemes are proposed and the pressure curves of each scheme are calculated. The three process schemes are simulated respectively, and the following conclusions are obtained after comparison and research:
(1) Analyzing the flow state of the metal liquid in different process schemes, it is found that air entrainment and turbulence and other casting defects are prone to occur in the inner runner and flange position of the sleeve. The reason is that the filling pressure is large and the flow velocity of the metal liquid is too fast.
(2) In the filling process of Scheme 3, the air entrainment disappears, the turbulence is weakened, the liquid surface rises stably, the oxidation slag production is reduced, the temperature distribution gradient is small, and the solidification sequence of the casting is reasonable. It is the optimal scheme and can effectively reduce the possible casting defects in the actual production process.
In conclusion, the optimization of the low-pressure casting process for aluminum alloy sleeves is of great significance for improving the quality of castings and meeting the production requirements of pressure vessels. Through the use of simulation software and the comparison of different process schemes, the optimal process scheme can be determined, which provides a reference for the actual production of aluminum alloy sleeves.
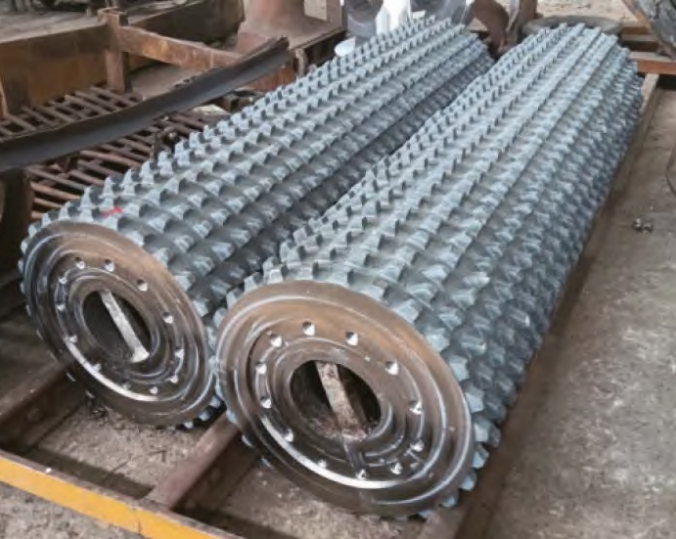