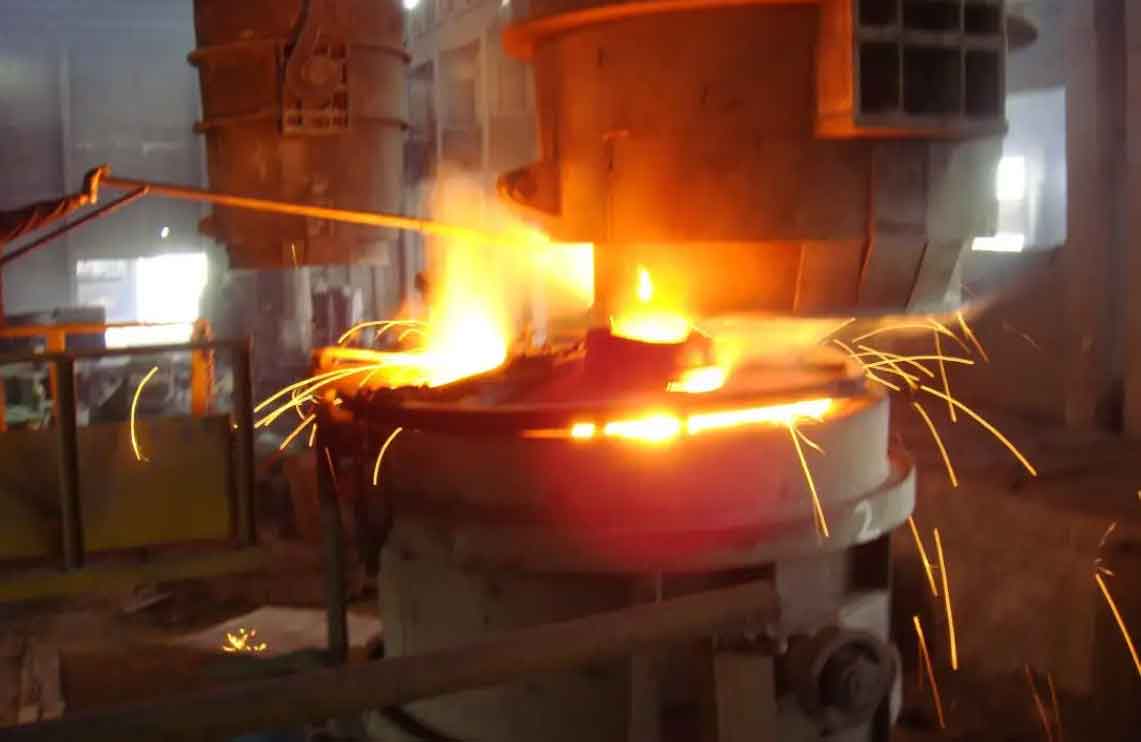
Industrial rotary kilns are widely used in cement, metallurgical pellets, active lime, chemical and other industries. The supporting roller is one of its core parts. It bears the weight of the whole kiln body through the opposite rolling movement with the kiln tyre, and is in the working environment of high temperature and high load alternating stress for a long time. Therefore, the requirements for its internal quality are very strict.
The supporting roller is generally made of cast steel, and no obvious sand casting defects are allowed. The technical requirements are that ultrasonic flaw detection shall be performed according to Level 2 in GB/T 7233.1-2009, and magnetic particle flaw detection shall be performed according to Level 2 in GB/T 9444-2007.
With the rapid development of modern industry, and according to the guidelines of national industrial policies, the specifications of rotary kilns are gradually increasing. Taking cement kilns as an example, the daily output has generally reached more than 5000 tons, and 10000 ton kilns are also being built. The size of the supporting roller also increases ϕ Jump to within 1.8 m ϕ Above 2m, the largest supporting roller has reached ϕ 3.3 m, gross weight more than 80 t. According to the actual production situation, the author will ϕ The idlers above 2m are temporarily large idlers.
After the optimization measures were taken, the quality of hundreds of large idlers was significantly improved, the repair cost was reduced, the repair cycle was shortened, and the economic benefits were significant.
(1) Reasonable pouring speed control and gas outlet measures can avoid defects such as air holding and sand inclusion.
(2) During the structural design of large supporting rollers, the groove depth shall be controlled within 150 mm as far as possible, and the maximum depth shall not exceed 200 mm. If the sand casting enterprise is unable to change the original design size, the process patch can be added appropriately according to the actual conditions to meet the requirements of the feeding channel, and then removed by processing to meet the drawing size.
(3) With the increase of the size of the supporting roller, the thickness of the cylindrical chill should also be increased to further improve its chilling effect, strengthen the temperature gradient in the end zone, and improve the feeding conditions.
(4) When placing the gating system, properly extend the length of the inner gate, and increase the distance between the runner and the supporting roller body, so as to reduce the influence of the overheating of the molten steel flowing in the runner for a long time during the pouring process on the supporting roller body.
(5) When cutting large risers, the cutting position shall be changed for many times to avoid stress concentration in the same direction. At the same time, the cutting shall be completed at one time. After cutting, it shall be timely tempered in the furnace to remove the stress.