Abstract
In this study, we conducted a comprehensive optimization of the sand casting process for a QT500-7 fixed base using numerical simulation techniques. The fixed base, designed for industrial robotic applications, required high structural integrity and defect-free casting due to its critical role in load-bearing and stability. By leveraging SolidWorks for 3D modeling and ProCAST for simulation, we analyzed the initial sand casting process, identified defects such as shrinkage porosity in thick sections, and implemented optimized solutions including risers and chill inserts. The revised process eliminated internal defects, achieving a casting yield of 66.2% while adhering to technical specifications. This work demonstrates the efficacy of numerical simulation in enhancing sand casting quality and efficiency.
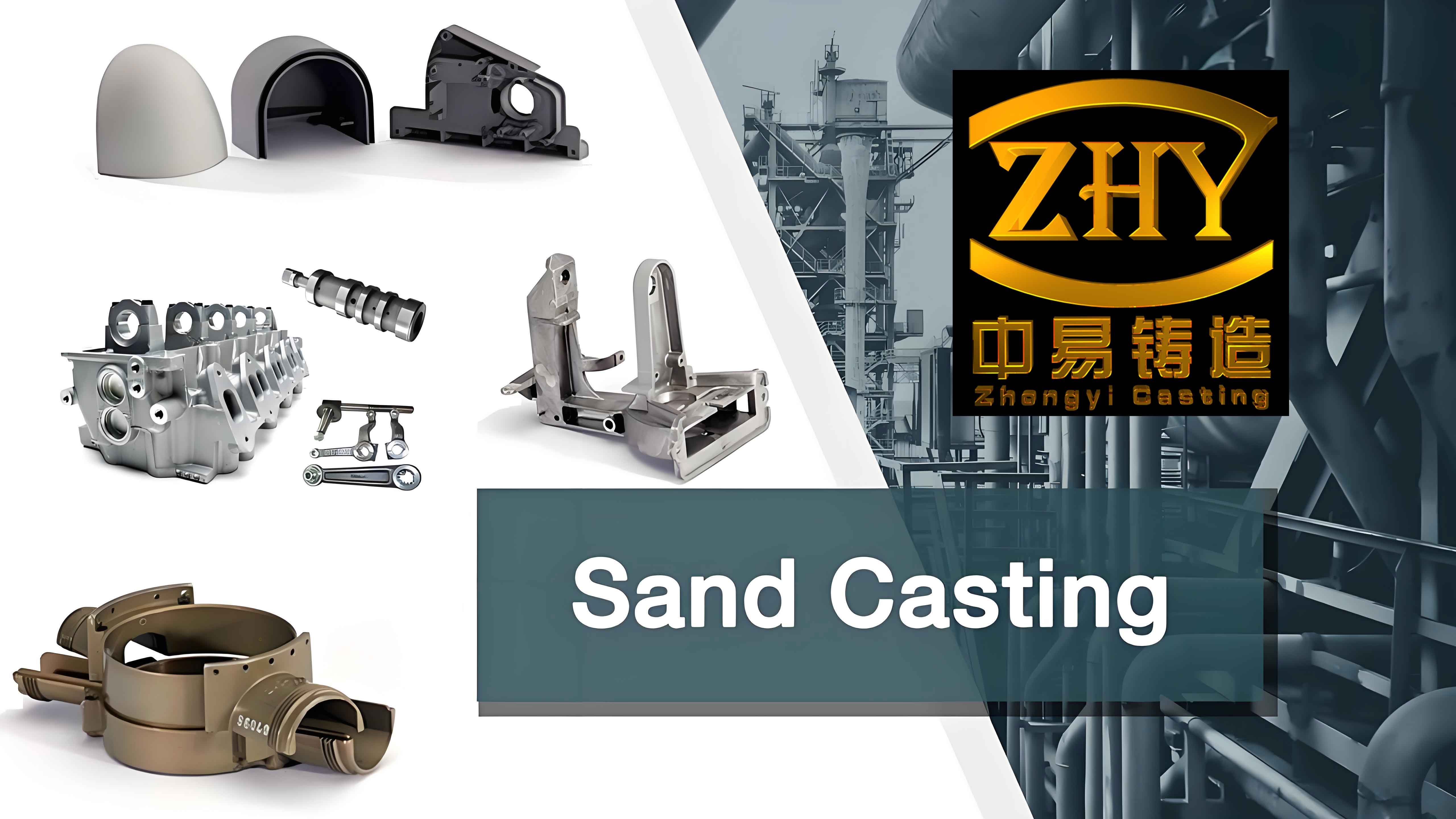
1. Introduction
Sand casting remains a cornerstone of modern manufacturing, particularly for producing complex geometries in ductile iron components like the QT500-7 fixed base. Traditional trial-and-error approaches often lead to prolonged development cycles and increased costs. Numerical simulation, however, enables precise prediction of defects such as shrinkage cavities, porosity, and cold shuts during the early design stages. This study focuses on optimizing the sand casting process for a QT500-7 fixed base through simulation-driven adjustments, emphasizing defect mitigation and process reliability.
Key challenges included:
- Ensuring complete mold filling without turbulence.
- Eliminating shrinkage defects in thick sections.
- Balancing economic feasibility with technical requirements.
2. Component Analysis and Technical Requirements
The QT500-7 fixed base, with dimensions 760 mm × 760 mm × 270 mm and a weight of 174.31 kg, features heterogeneous wall thicknesses (20–40 mm) and critical functional surfaces. Its structural complexity arises from:
- Central and lateral through-holes for assembly.
- Reinforced support plates and lateral protrusions.
- Thin-to-thick transitions prone to thermal stress.
Technical specifications mandated:
- No cracks, cold shuts, shrinkage defects, or slag inclusions.
- Surface roughness conforming to GB/T 6414-2017 (DCTG13 grade).
- Chemical composition within the range specified in Table 1.
Table 1: Chemical composition of QT500-7 (wt%)
C | Si | Mn | P | S |
---|---|---|---|---|
3.5–3.8 | 2.5–2.8 | <0.3 | <0.07 | <0.02 |
3. Sand Casting Process Design
3.1 Gating System Design
An open-top gating system was selected to ensure smooth filling and effective slag trapping. The cross-sectional ratios of the gating channels followed the criteria for ductile iron:∑Asprue:∑Arunner:∑Aingate=3:2.5:1∑Asprue:∑Arunner:∑Aingate=3:2.5:1
Key parameters included:
- Sprue: 1 channel, 11.88 cm² cross-section.
- Runner: 1 channel, 29.69 cm² cross-section.
- Ingates: 4 channels, total 35.63 cm².
A short, wide ingate design minimized turbulence, while ceramic filters at the sprue entrance reduced oxide inclusions.
3.2 Mold and Core Design
Given the low production volume, manual sand molding with wooden patterns was employed. Two cores were designed:
- Core 1: For lateral rectangular through-holes.
- Core 2: For side protrusions, optimized with chill inserts.
The parting line was positioned at the maximum cross-section to simplify mold assembly and reduce misalignment risks.
4. Numerical Simulation Setup
4.1 Meshing and Boundary Conditions
The 3D model was discretized into 178,308 tetrahedral elements. Critical simulation parameters included:
- Pouring temperature: 1360°C (above QT500-7 liquidus of 1168°C).
- Heat transfer coefficients:
- Solidification time: 19.6 s (calculated based on Chvorinov’s rule).
4.2 Initial Simulation Results
The initial sand casting process showed complete filling without cold shuts but exhibited shrinkage porosity in thick sections (Figure 1). Key observations:
- Turbulent flow at the ingates caused air entrapment.
- Slow solidification in support plate corners led to macroshrinkage.
5. Process Optimization
5.1 Riser Design
Cylindrical blind risers were added to the four corners of the support plate to feed shrinkage. The riser dimensions were calculated using the modulus method:Mriser=1.2×McastingMriser=1.2×Mcasting
where M=VAM=AV (volume-to-surface area ratio). Final riser dimensions:
- Height: 120 mm
- Diameter: 80 mm
5.2 Chill Insert Application
Gray iron chill plates (130 mm × 130 mm × 10 mm) were embedded near side protrusions to accelerate cooling. The chill size satisfied:Dchill≥0.5×Dhot spotDchill≥0.5×Dhot spot
This ensured directional solidification, transferring defects to risers.
6. Optimized Simulation Results
Post-optimization simulations confirmed:
- Uniform filling with reduced turbulence (velocity gradient < 0.5 m/s).
- No shrinkage defects in the casting; all porosity concentrated in risers.
- Improved yield: 66.2% (vs. 58% in the initial design).
Table 2: Comparison of Initial and Optimized Processes
Parameter | Initial Design | Optimized Design |
---|---|---|
Shrinkage Defects | Present | Eliminated |
Casting Yield (%) | 58 | 66.2 |
Pouring Time (s) | 19.6 | 19.6 |
7. Conclusion
Through numerical simulation, we successfully optimized the sand casting process for the QT500-7 fixed base. Key achievements include:
- Elimination of shrinkage defects via risers and chill inserts.
- Enhanced casting yield (66.2%) without compromising structural integrity.
- Validation of simulation-driven design for sand casting applications.
This approach underscores the value of integrating computational tools into traditional sand casting workflows, enabling cost-effective and defect-free production of complex ductile iron components.