I. Introduction
In the automotive industry, the demand for high-performance and lightweight components is constantly increasing. Aluminum alloys, with their excellent properties such as low density, high strength-to-weight ratio, and good corrosion resistance, have become widely used materials in the production of automobile parts. Among them, the ADC12 aluminum alloy is particularly favored due to its strong bearing capacity, high mechanical properties, and good machinability.
The engine support is a crucial component in an automobile, as it is responsible for fixing the engine to the vehicle frame and withstanding the vibrations and loads generated during engine operation. Therefore, ensuring the high mechanical properties of the engine support is of great significance for the safety and performance of the vehicle.
Squeezing casting is a near-net-shape forming process that combines the advantages of casting and forging. By applying a mechanical static pressure to the molten metal during solidification, it can produce castings with dense microstructure, high dimensional accuracy, and excellent mechanical properties. In recent years, squeezing casting has been increasingly used in the production of high-quality aluminum alloy components.
In this study, we focus on optimizing the squeezing casting process parameters for an aluminum alloy automobile support part. By using numerical simulation and experimental methods, we aim to investigate the effects of key process parameters such as casting temperature and holding pressure on the shrinkage porosity, mechanical properties, and microstructure of the ADC12 aluminum alloy castings. The results of this study will provide valuable guidance for the industrial production of high-quality aluminum alloy automobile support parts.
II. Numerical Simulation
A. Control Equations
The flow of molten metal during the indirect squeezing casting filling process is a free surface flow of non-isothermal fluid, which follows the laws of fluid mechanics and can be regarded as an unsteady flow of incompressible Newtonian fluid. The governing equations include the volume function equation, the continuity equation, the Navier-Stokes momentum equation, and the Fourier heat conduction differential equation.
B. Preprocessing
The three-dimensional model of the automobile support part and the inner gate were drawn using UG software. Then, a virtual sand box was constructed in ProCAST, and the mesh was divided. The size of the mold mesh was set to 10 mm, while the mesh sizes of the casting, the molten metal in the pressure chamber, and the pressure chamber punch were set to 2 mm. A total of 128,764 surface meshes and 2,948,240 volume meshes were generated.
C. Process Parameters
The ADC12 aluminum alloy was selected as the material for the casting, and the H13 steel was used for the mold. The chemical compositions and thermophysical properties of the two materials are shown in Tables 1-3. The key process parameters optimized in this study were the casting temperature and the holding pressure. The casting temperature was varied from 620 to 700 °C, and the holding pressure was set from 110 to 150 MPa. The other process parameters were kept constant, including the filling speed of 0.1 m/s, the holding time of 13 s, and the mold temperature of 250 °C.
D. Boundary Conditions
The boundary conditions included the velocity and pressure of the mold punch, as well as the heat transfer conditions between the mold, the casting, and the air. The velocity of the mold punch was set to -0.1 m/s along the Z-axis, and a pressure boundary condition that varied with time was applied at the contact surface between the punch and the molten metal. The outer surface of the mold in contact with the air was set to air cooling. The heat transfer coefficient between the casting and the mold was set as a curve that varied with time, corresponding to the pressure change during the casting filling and holding solidification processes.
E. Simulation Results and Analysis
The numerical simulation results showed that the defect volume first decreased and then increased with the increase of the casting temperature, reaching the minimum at 680 °C. This was because when the casting temperature was too low, the fluidity of the molten metal was poor, and the solidification time was short, resulting in a thick solidification shell that prevented the effective transfer of pressure to the internal molten metal during the holding solidification stage, leading to poor feeding. On the other hand, when the casting temperature was too high, the shrinkage of the liquid metal increased, and the solidification time was long, resulting in the formation of isolated liquid phase regions in the casting, which were prone to shrinkage porosity during free solidification.
The defect volume generally decreased with the increase of the holding pressure, and the change became relatively flat after reaching 140 MPa. The essence of the holding pressure feeding in squeezing casting is that the punch applies an external force to cause the plastic deformation of the solidification shell outside the molten metal, and at the same time, the molten metal flows to achieve forced feeding. When the pressure was low, the feeding effect was poor, resulting in the formation of shrinkage porosity in the hot spot area of the casting.
III. Experimental Procedure
A. Casting Production
Based on the numerical simulation results, several groups of castings were produced under different process conditions. The casting process was carried out using an indirect squeezing casting machine.
B. Mechanical Property Testing
Tensile tests were performed on the castings using a WDW100 electronic universal testing machine. Three specimens were tested for each group, and the average values were taken. The hardness of the castings was measured using an HBS3000V visual Brinell hardness tester. The diameter of the indenter was ϕ10 mm, the test load was 4900 N, and the holding time was 10 s. Three points were selected for each specimen, and the average value was taken.
C. Microstructure Observation
Small samples were taken from the core and the outer part of the castings, polished, and corroded with an aluminum alloy etchant (5% HNO₃ + 5% HCl + 5% HF) for about 10 s. Then, the microstructure was observed using a Leica6000M metallographic microscope.
IV. Results and Discussion
A. Mechanical Properties
The results of the mechanical property tests showed that when the casting temperature was 680 °C, the tensile strength, elongation, and hardness of the castings reached the best values. However, as the casting temperature further increased, the mechanical properties began to decline. With the increase of the holding pressure from 110 to 130 MPa, the mechanical properties of the castings significantly improved, and the improvement became less significant after reaching 130 MPa. Considering the production efficiency and the quality of the castings, a holding pressure of 150 MPa was selected as the optimal value.
B. Microstructure
The microstructure of the castings mainly consisted of α-Al phase and Al-Si eutectic phase. The increase of the holding pressure had a significant effect on the microstructure of the ADC12 aluminum alloy castings. It promoted the nucleation of the alloy, refined the grains, and changed the morphology of the grains from dendritic to spherical. At the same time, it also reduced the size and quantity of the eutectic Si phase, which improved the mechanical properties of the castings.
C. Relationship between Process Parameters, Defects, Microstructure, and Mechanical Properties
The casting defect volume, microstructure, and mechanical properties were closely related. The increase of the holding pressure could effectively reduce the defect volume, refine the grains, and improve the mechanical properties. When the casting temperature was 680 °C and the holding pressure was 150 MPa, the casting had the smallest defect volume, the most refined microstructure, and the best mechanical properties.
V. Conclusion
In this study, the optimization of the squeezing casting process parameters for an aluminum alloy automobile support part was carried out. The following conclusions were obtained:
- The casting defect volume, microstructure, and mechanical properties showed consistent variation trends with the change of the process parameters.
- The optimal process parameters were determined as a casting temperature of 680 °C and a holding pressure of 150 MPa, which resulted in the smallest defect volume, the most refined microstructure, and the best mechanical properties of the castings.
- The holding pressure played a dominant role in eliminating defects, refining the microstructure, and improving the mechanical properties within the studied process parameter range.
The results of this study provide a theoretical basis and practical guidance for the industrial production of high-quality aluminum alloy automobile support parts. Future research can focus on further optimizing the process parameters and exploring the effects of other factors on the casting quality.
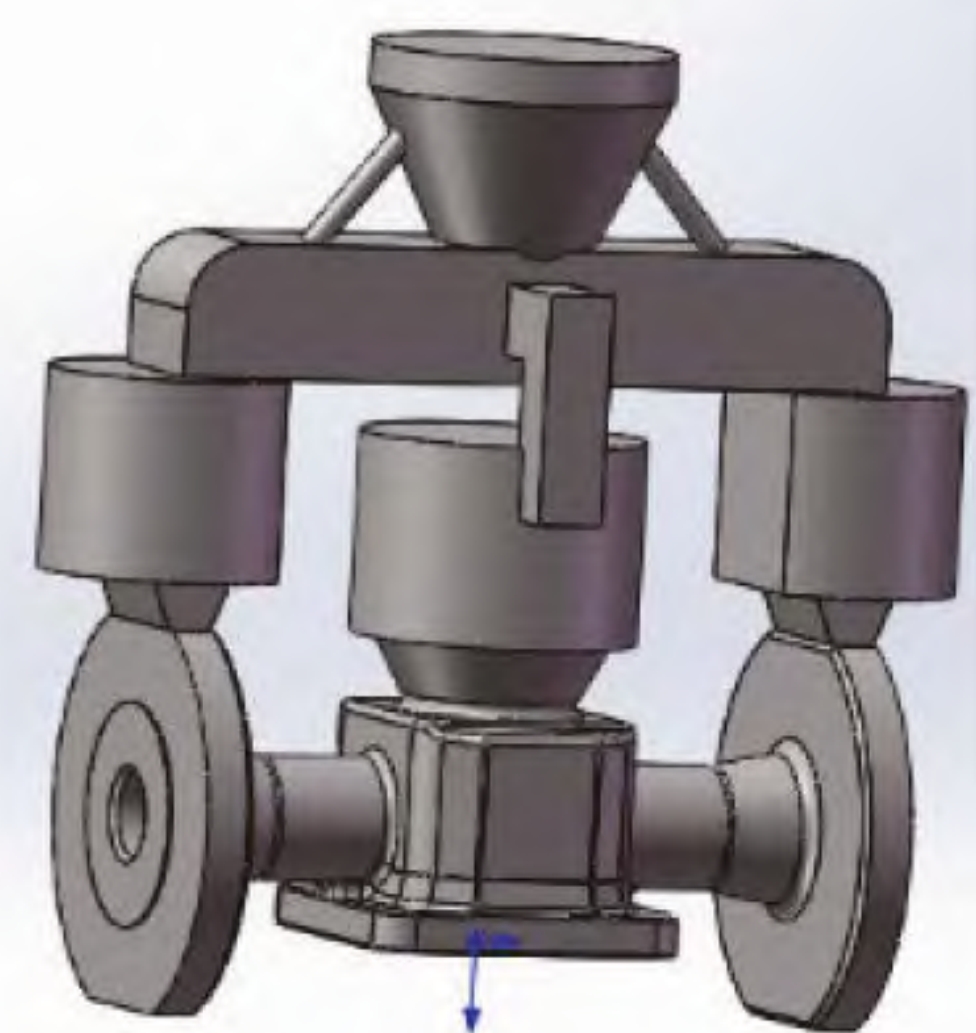