1. Introduction
In the field of modern industrial manufacturing, the quality and performance of components play a crucial role. The plunger pump is an essential part of the hydraulic system in aircraft engines, responsible for providing the necessary flow and power. The aluminum alloy plunger pump shell, as a key component, has strict requirements for casting processes and quality. However, during the production process, casting defects such as shrinkage porosity and porosity often occur, which seriously affect the performance and service life of the component. Therefore, it is of great significance to analyze and optimize the casting defects of the aluminum alloy plunger pump shell to improve the quality and reliability of the product.
This article focuses on the casting defects of the aluminum alloy plunger pump shell, conducts in-depth research and analysis, and proposes corresponding optimization measures. Through a combination of theoretical analysis, numerical simulation, and experimental verification, the causes of defects are explored, and an improved casting process plan is developed. The results show that the optimized process can effectively solve the casting defects and meet the quality requirements of the product.
2. Casting Process and Defect Analysis of the Plunger Pump Shell
2.1 Casting Process of the Plunger Pump Shell
The plunger pump shell is usually cast using a metal mold tilting casting process. This process has the advantages of high production efficiency and good casting quality. The specific process parameters are as follows:
Process Parameter | Value |
---|---|
Casting Temperature | 710 – 730 °C |
Mold Preheating Temperature | 280 – 300 °C |
Pouring Time | 11 s |
In the original casting process, the feeding riser is set at the oil circuit interface end, and a horizontal riser is set on each of the three thick bosses of the bottom flange for feeding. The horizontal riser is coated with thermal insulation paint to improve the feeding efficiency.
2.2 Defect Types and Locations
The main casting defects in the plunger pump shell are shrinkage porosity and porosity. The shrinkage porosity defects are mainly concentrated on the three bosses of the flange surface, and the porosity defects are mainly caused by the turbulent flow of the molten metal during the filling process.
2.3 Causes of Defects
- Shrinkage Porosity Defects: The casting structure of the plunger pump shell is complex, with thick and large parts at both ends and a thin middle part. During solidification, it is difficult to achieve effective feeding, resulting in shrinkage porosity defects. In addition, the solidification time of the boss position is longer than that of the dark riser root, resulting in the early closure of the feeding channel and poor feeding effect.
- Porosity Defects: The small area of the ingate and the large internal cavity of the mold cause the molten metal to flow turbulently during the filling process, resulting in the entrainment of gas and the formation of porosity defects.
3. Optimization of the Casting Process
3.1 Improvement of the Feeding System
To solve the problem of shrinkage porosity defects, the feeding system is optimized. The flange surface of the casting is set upward, and a bright riser is set on the flange. Multiple isolated hot spot circles exist at the thick part of the bottom of the oil circuit interface end, so a dark riser is set in the middle for feeding, and two feeding channels are set on the side cavity walls. The positions that cannot be fed by the middle dark riser are fed by the bright riser.
3.2 Optimization of the Ingate
To reduce porosity defects, the ingate is optimized. The flange surface of the casting is set upward, and a relatively flat cavity surface is selected as the ingate to ensure the smooth filling of the molten metal and avoid the entrainment of gas.
4. Numerical Simulation Analysis
4.1 Simulation Model and Parameters
The AnyCasting simulation software is used to simulate and analyze the optimized casting process. The simulation model is established according to the actual structure of the plunger pump shell, and the relevant process parameters are set as follows:
Parameter | Value |
---|---|
Pouring Temperature | 720 °C |
Mold Preheating Temperature | 280 °C |
Coating Thickness | 500 μm |
Casting Tilting Time | 11 s |
4.2 Simulation Results and Analysis
The simulation results show that the solidification sequence of the casting is more reasonable, and the temperatures of the bright riser and the dark riser are the highest. The shrinkage porosity defects are mainly concentrated in the bright riser and the dark riser, and the shrinkage porosity defects on the casting are eliminated. The final solidification time is 4 minutes.
5. Production Verification
5.1 Production Experiment
According to the optimized casting process, 30 plunger pump shell castings are poured. The real-time imaging inspection is carried out on the three thick bosses of the flange, and no shrinkage porosity defects are found. The surface of the casting is treated by sandblasting, and no porosity defects are found. After mechanical processing, 2 castings are scrapped, and the qualified rate reaches 93.3%.
5.2 Comparison of Results
The production results before and after the optimization are compared as follows:
Process | Production Quantity | Qualified Quantity | Qualification Rate |
---|---|---|---|
Before Optimization | 163 | 54 | 33.1% |
After Optimization | 30 | 28 | 93.3% |
It can be seen that the optimized casting process significantly improves the quality and qualified rate of the castings.
6. Conclusion
In this article, the casting defects of the aluminum alloy plunger pump shell are analyzed and optimized. The following conclusions are drawn:
- By adjusting the sequential solidification of the casting through subsidies and dark risers, the shrinkage porosity defects can be effectively eliminated.
- By reasonably selecting the ingate of the plunger pump shell, the smooth filling of the molten metal can be ensured, and the porosity defects can be effectively reduced.
- In the aluminum alloy metal mold casting process, the horizontal side riser has a limited feeding effect on the isolated hot spots at special positions.
- The dark riser inside the plunger pump shell tank has a good feeding effect because it is located in the center of the casting and is equivalent to a heating dark riser.
The research results of this article provide a reference for improving the casting quality of the aluminum alloy plunger pump shell and have certain guiding significance for the optimization of the casting process of similar components.
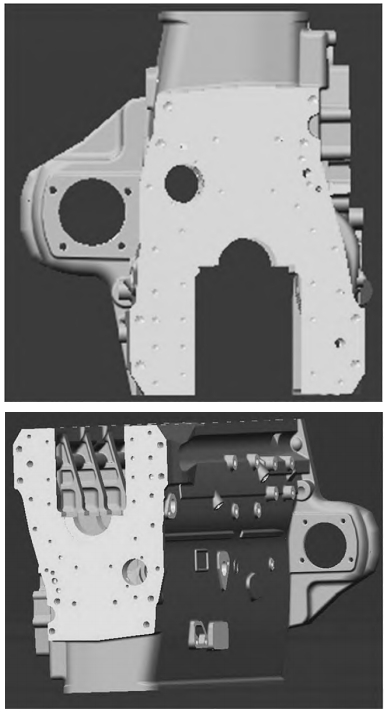