1. Orthogonal test design
In sand mold casting, pouring temperature and pouring speed are two important parameters in sand mold casting process. In order to obtain more reasonable pouring temperature and pouring speed, orthogonal test is carried out on the basis of the third process plan. The level table of virtual orthogonal test factors designed is shown in Table 1.
Horizontal | Pouring temperature/℃ | Pouring speed/(m · s ^- 1) |
1 | 1 530 | 1.3 |
2 | 1 560 | 1.6 |
3 | 1 590 | 1.9 |
2. Range analysis
The range analysis results of this test are shown in Table 2.
Group No. | Pouring temperature/℃ | Pouring speed/(m · s ^- 1) | Pore volume/cm^3 |
1 | 1 530 | 1,3 | 2.368 |
2 | 1 530 | 1.6 | 2.201 |
3 | 1 530 | 1.9 | 2.503 |
4 | 1 560 | 1,3 | 1.553 |
5 | 1 560 | 1.6 | 1.416 |
6 | 1 560 | 1.9 | 1.818 |
7 | 1 590 | 1,3 | 1.984 |
8 | 1 590 | 1.6 | 2.066 |
9 | 1 590 | 1.9 | 2.206 |
From Table 2, we can see the extreme difference of various factors on defect pore volume. The extreme difference corresponding to pouring temperature is 2.290, which is greater than the extreme difference corresponding to pouring speed 0.844, indicating that pouring temperature has a greater impact on pore volume; With the increase of pouring temperature, the pore volume first decreases and then increases, while with the increase of pouring speed, the pore volume first decreases and then increases. According to the range analysis, the order of influence of two factors on the quality of sand casting shell is: pouring temperature>pouring speed. The optimum combination parameters are pouring temperature 1560 ℃ and pouring speed 1.6m/s. As shown in the pore distribution diagram, the pore defect volume of sand casting shell is 1.416cm3, which is smaller than that of the first and second schemes.
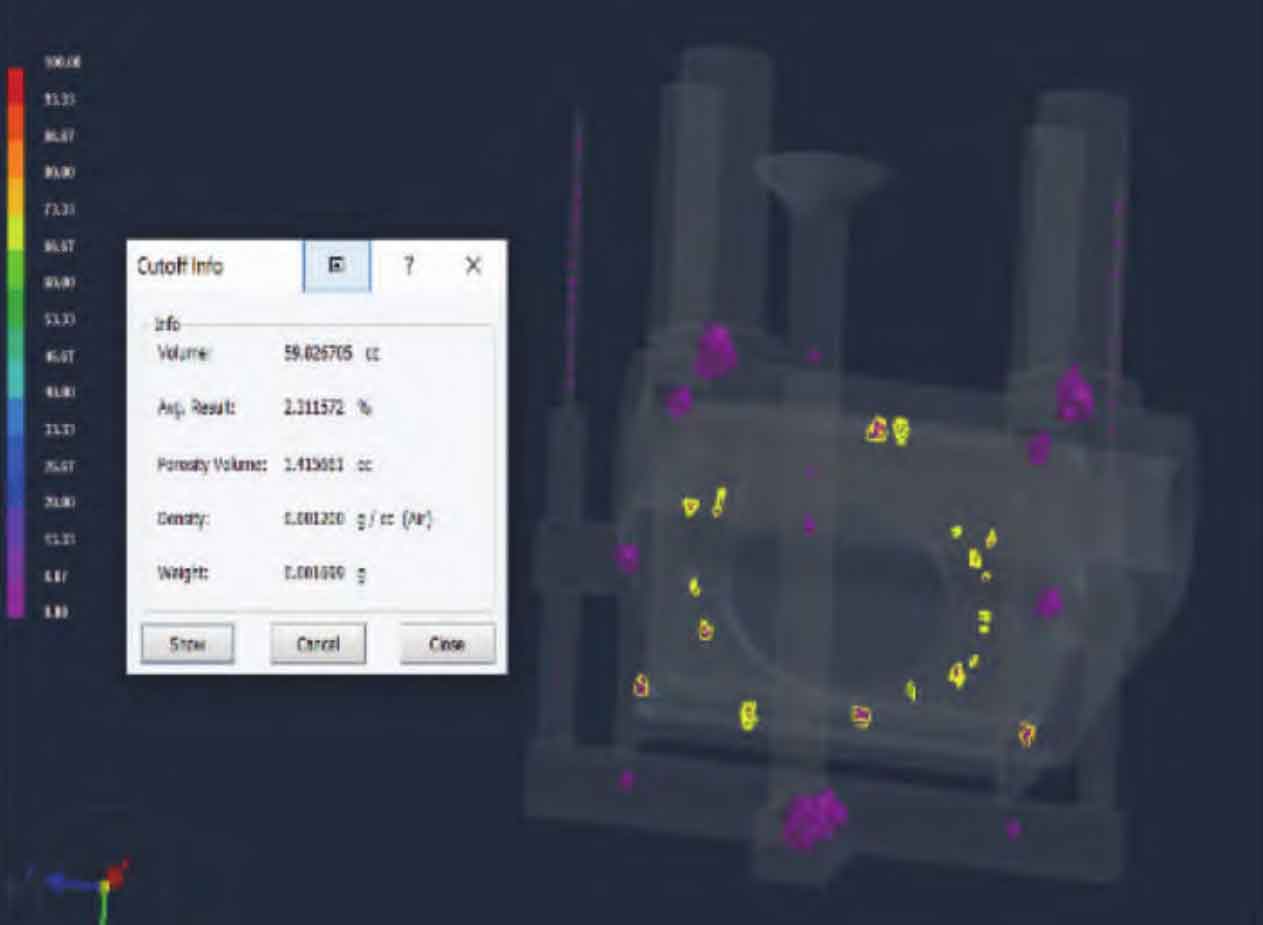
After the process improvement, the qualified rate of sand castings increased from 81% to 96%, and the process yield was 66%.