In the steel casting industry, achieving a balance between product quality and production efficiency is of utmost importance. This article delves into the critical task of optimizing casting parameters for steel casting processes. By carefully controlling and adjusting various parameters, manufacturers can strike the ideal balance between high-quality castings and improved productivity.
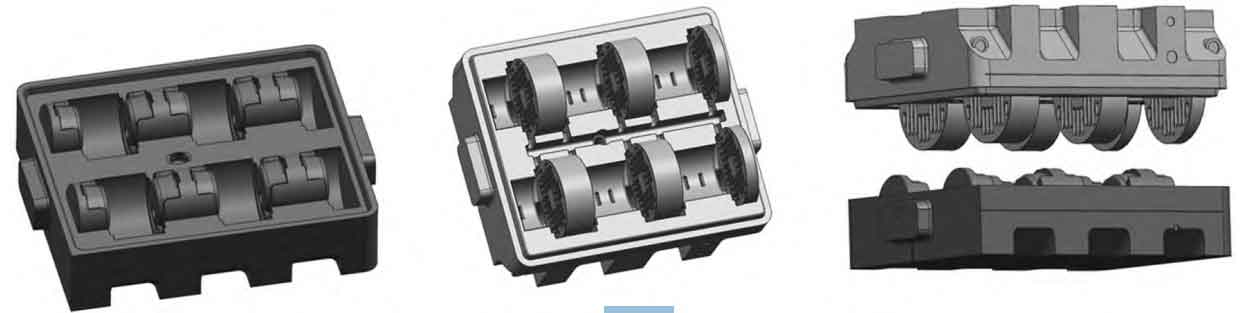
- Alloy Selection for Desired Properties: The choice of alloy plays a crucial role in achieving the desired properties of steel castings. By carefully selecting the appropriate alloy composition, manufacturers can optimize strength, corrosion resistance, heat resistance, and other essential characteristics. Alloy selection must be based on the specific application and performance requirements of the castings.
- Mold Design and Preparation: The design and preparation of molds significantly impact casting quality. Proper mold design ensures precise filling, uniform cooling, and minimal defects. Factors such as mold material, gating system design, riser placement, and venting influence the solidification process and the formation of defects like porosity and shrinkage. Optimizing mold design and preparation enhances the overall quality of steel castings.
- Melting and Pouring Parameters: The melting and pouring parameters directly affect the integrity and microstructure of steel castings. Factors such as melting temperature, holding time, and pouring temperature must be carefully controlled to ensure the desired chemical composition and prevent issues like overheating or underheating. Optimization of melting and pouring parameters is critical for achieving uniformity and avoiding casting defects.
- Solidification and Cooling Control: Proper control of solidification and cooling rates is essential to prevent defects and ensure the desired mechanical properties. This can be achieved through the strategic placement of chills, the use of insulating materials, and the implementation of directional solidification techniques. Optimizing solidification and cooling control leads to improved grain structure, reduced residual stresses, and enhanced mechanical integrity.
- Quality Assurance through Non-Destructive Testing: Non-destructive testing (NDT) techniques play a vital role in optimizing casting parameters. NDT methods such as X-ray, ultrasonic testing, and magnetic particle inspection help detect internal and surface defects without causing damage to the castings. Implementing robust NDT processes ensures the identification and rectification of casting flaws, leading to enhanced product quality.
- Continuous Process Monitoring and Optimization: To achieve consistent quality and productivity, continuous process monitoring and optimization are essential. Real-time monitoring of process variables, such as temperature, pressure, and flow rates, enables prompt adjustments and corrective actions. Utilizing statistical process control techniques and data analysis tools helps identify trends, predict deviations, and optimize casting parameters for ongoing process improvement.
Optimizing casting parameters for steel casting is a critical aspect of achieving the desired balance between quality and productivity. By carefully considering alloy selection, mold design, melting and pouring parameters, solidification control, and implementing effective quality assurance measures, manufacturers can produce high-quality steel castings while maximizing production efficiency. Continuous process monitoring and optimization ensure ongoing improvements and drive the industry towards enhanced performance, customer satisfaction, and long-term success.