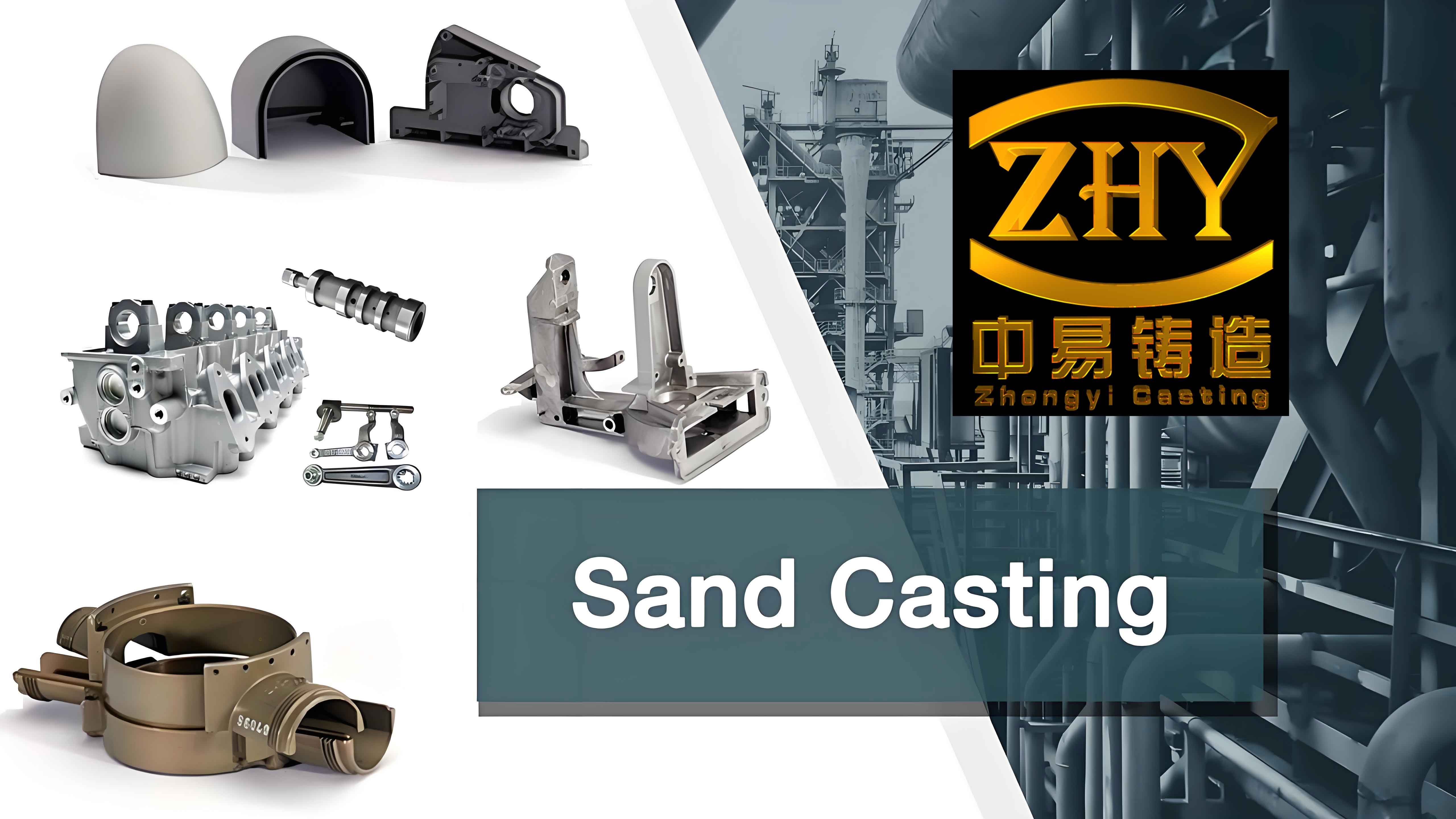
Sand casting is a time-honored method for producing metal components, known for its versatility and ability to create complex shapes. However, the cost of sand casting can be significant, and optimizing cost efficiency is a top priority for sand casting manufacturers. By implementing strategic improvements and leveraging modern technologies, sand casting manufacturers can reduce expenses, increase productivity, and maintain high-quality standards. This article explores various strategies for optimizing cost efficiency in sand casting manufacturing processes.
Introduction to Sand Casting Cost Structure
Understanding the cost structure of sand casting is essential for identifying opportunities for cost optimization. The primary cost components in sand casting manufacturing include:
- Raw Materials:
- Metals (e.g., aluminum, iron, steel)
- Sand and binders for mold making
- Labor Costs:
- Skilled labor for mold making, metal pouring, and finishing
- Maintenance and supervision staff
- Energy Costs:
- Electricity and fuel for melting metals and operating machinery
- Equipment and Maintenance:
- Capital investment in machinery and tools
- Ongoing maintenance and repairs
- Overhead Costs:
- Facility costs (rent, utilities)
- Administrative expenses
Strategies for Optimizing Cost Efficiency
1. Improving Material Utilization
Effective management of raw materials can significantly reduce costs for sand casting manufacturers. Strategies for improving material utilization include:
- Optimized Mold Design: Using computer-aided design (CAD) software to create molds that minimize material waste.
- Recycling Sand: Implementing sand reclamation systems to reuse sand from spent molds, reducing the need for new sand.
- Material Substitution: Exploring alternative materials that offer similar properties at a lower cost.
Material Optimization Strategy | Description | Benefits |
---|---|---|
Optimized Mold Design | Utilizing CAD software for precise mold creation | Reduced material waste, cost savings |
Recycling Sand | Reclaiming and reusing sand from spent molds | Lower raw material costs, sustainability |
Material Substitution | Using alternative, cost-effective materials | Reduced material costs |
2. Enhancing Energy Efficiency
Energy costs are a significant component of sand casting manufacturing. Enhancing energy efficiency can lead to substantial cost savings. Key approaches include:
- Upgrading Equipment: Investing in energy-efficient furnaces and machinery that consume less power.
- Energy Management Systems: Implementing systems to monitor and optimize energy usage throughout the production process.
- Waste Heat Recovery: Capturing and reusing waste heat from furnaces and other equipment to reduce overall energy consumption.
3. Automating Manufacturing Processes
Automation can enhance efficiency and reduce labor costs in sand casting manufacturing. Key areas for automation include:
- Mold Making: Automated mold-making machines can create precise molds faster and with less manual labor.
- Metal Pouring: Automated pouring systems ensure consistent and accurate pouring, reducing waste and defects.
- Finishing Processes: Automated finishing systems can handle grinding, trimming, and polishing tasks more efficiently than manual labor.
Automation Area | Description | Benefits |
---|---|---|
Mold Making | Automated machines for creating precise molds | Faster production, reduced labor costs |
Metal Pouring | Automated systems for consistent metal pouring | Reduced waste, improved quality |
Finishing Processes | Automated grinding, trimming, and polishing | Increased efficiency, lower labor costs |
4. Implementing Lean Manufacturing Practices
Lean manufacturing focuses on eliminating waste and improving efficiency in production processes. For sand casting manufacturers, lean practices can include:
- Value Stream Mapping: Analyzing production processes to identify and eliminate non-value-added activities.
- Just-in-Time (JIT) Inventory: Reducing inventory levels to minimize carrying costs and avoid overproduction.
- Continuous Improvement: Encouraging a culture of ongoing improvement to optimize processes and reduce waste.
Leveraging Technology for Cost Efficiency
1. Advanced Data Analytics
Using advanced data analytics, sand casting manufacturers can gain insights into their production processes and identify opportunities for cost savings. Key applications include:
- Predictive Maintenance: Analyzing equipment data to predict and prevent breakdowns, reducing downtime and maintenance costs.
- Process Optimization: Identifying inefficiencies in the production process and implementing data-driven improvements.
- Quality Control: Using data analytics to monitor and improve product quality, reducing the cost of defects and rework.
2. Internet of Things (IoT)
IoT devices can enhance visibility and control over the manufacturing process. Applications of IoT in sand casting manufacturing include:
- Real-Time Monitoring: Tracking the condition and performance of equipment in real-time to optimize operations.
- Supply Chain Management: Monitoring the movement of materials and products to improve supply chain efficiency.
- Environmental Monitoring: Ensuring compliance with environmental regulations and reducing energy consumption.
Technology | Description | Benefits |
---|---|---|
Advanced Data Analytics | Utilizing data to optimize processes and maintenance | Reduced downtime, cost savings |
IoT | Real-time monitoring and control of manufacturing processes | Improved efficiency, enhanced supply chain |
Conclusion
Optimizing cost efficiency in sand casting manufacturing processes is crucial for maintaining competitiveness and profitability in a challenging market. By improving material utilization, enhancing energy efficiency, automating manufacturing processes, and implementing lean manufacturing practices, sand casting manufacturers can achieve significant cost savings. Additionally, leveraging advanced technologies such as data analytics and IoT can further enhance efficiency and drive continuous improvement.
As the industry continues to evolve, staying ahead of cost challenges will require ongoing innovation and strategic management. Sand casting manufacturers that embrace these strategies will be well-positioned to thrive in the dynamic manufacturing landscape of 2024 and beyond.