Optimizing heat treatment processes for die casting is essential to achieve improved casting quality. Die casting involves injecting molten metal into a mold cavity under high pressure, and heat treatment can address certain issues and enhance the properties of the castings. Here are some ways to optimize heat treatment processes for improved die casting quality:
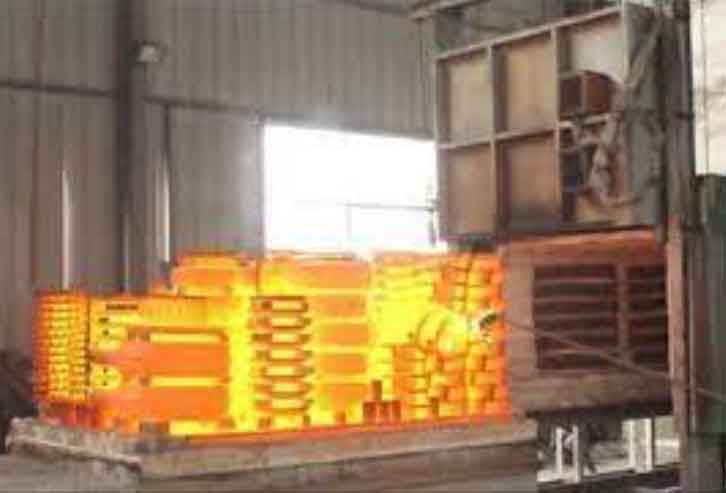
- Understanding the alloy: Different alloys used in die casting, such as aluminum, zinc, or magnesium, have unique metallurgical properties and response to heat treatment. It is crucial to understand the specific alloy composition, including the alloying elements, and their effect on the heat treatment process. This knowledge will help in selecting the appropriate heat treatment techniques and parameters.
- Preheat treatment: Preheating the die before the casting process can help improve the casting quality. Preheating eliminates moisture, reduces thermal shock, and improves the flow of molten metal into the die, resulting in better surface finish and reduced porosity.
- Solution treatment: For certain alloys, such as heat-treatable aluminum alloys, solution treatment is often employed. This involves heating the casting to a specific temperature range to dissolve the alloying elements uniformly. Proper solution treatment promotes homogenization of the microstructure, eliminating any segregation or inclusions present in the castings.
- Quenching: After solution treatment, quenching rapidly cools the casting, freezing the dissolved alloying elements in a supersaturated state. The quenching process determines the final microstructure and mechanical properties of the casting. The quenching media, such as water, oil, or air, should be selected based on the alloy and desired properties.
- Aging: Aging is a post-quenching heat treatment process that allows the precipitation of fine particles within the casting. This step enhances the mechanical properties, such as strength, hardness, and dimensional stability. The aging temperature and time are critical parameters that need to be optimized to achieve the desired properties.
- Stress relief: Die castings can develop internal stresses due to rapid cooling and solidification. Stress relief heat treatment helps in reducing these residual stresses, improving the dimensional stability and minimizing the risk of distortion or cracking.
- Process control and monitoring: To optimize heat treatment processes, it is crucial to have robust process control and monitoring systems in place. This includes accurately measuring and controlling the temperature, time, and atmosphere during each stage of heat treatment. Monitoring techniques like thermocouples, pyrometers, and data logging can ensure consistency and repeatability of the heat treatment process.
- Post-treatment inspections: After heat treatment, thorough inspections, such as visual examination, non-destructive testing, and mechanical testing, should be conducted to verify the quality of the die castings. This helps in identifying any defects or deviations and allows for necessary corrective measures.
By optimizing heat treatment processes for die casting, manufacturers can improve the casting quality, mechanical properties, and dimensional accuracy of the final products. This ultimately leads to enhanced performance, durability, and reliability in various applications where die castings are used.