Casting defects in manufacturing can pose significant challenges to product quality and production efficiency. Employing best practices for defect prevention is crucial to ensure high-quality castings. Here are some common challenges associated with casting defects and the corresponding best practices for their prevention:
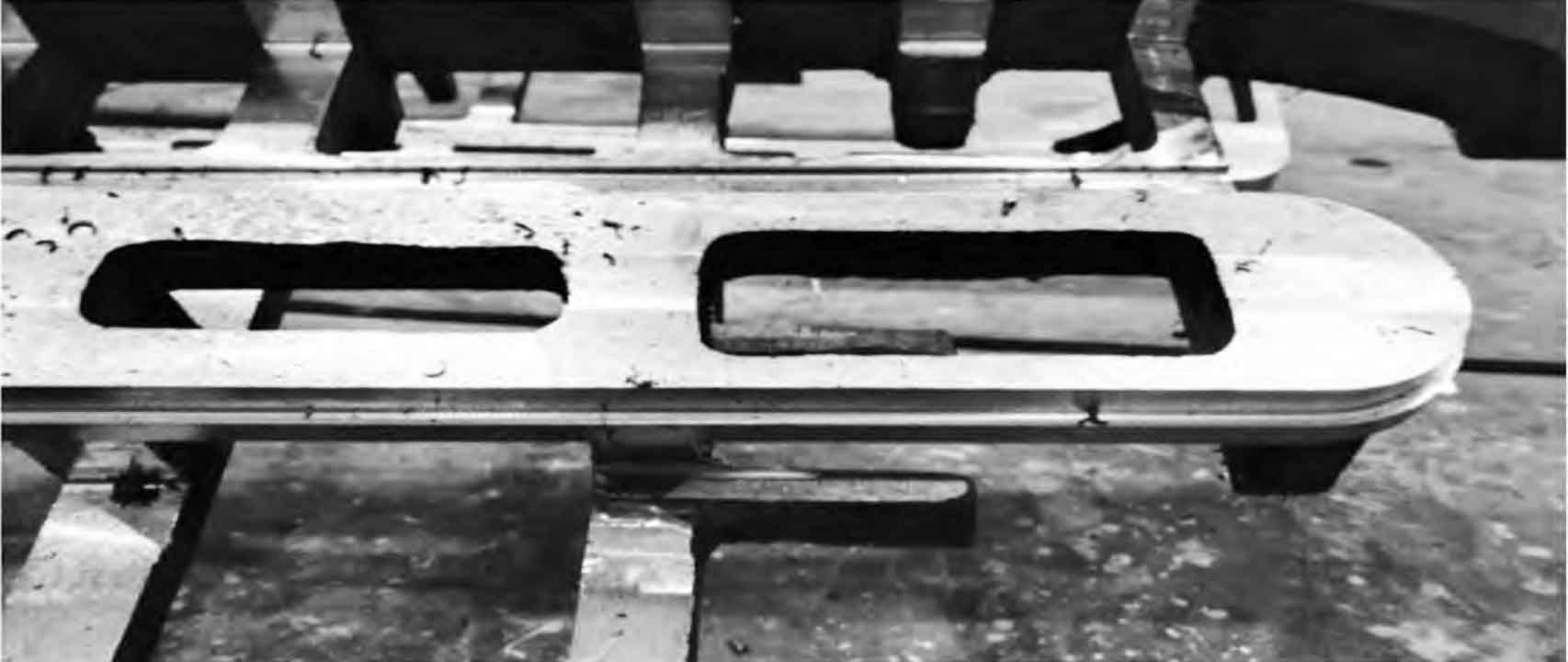
- Lack of Process Control:
- Challenge: Inadequate process control can lead to variations in casting parameters, such as temperature, pouring rate, mold preparation, or solidification time.
- Best Practices: Implement robust process controls, including standardized operating procedures, documented work instructions, and regular training for operators. Monitor and control critical process parameters to ensure consistency and repeatability.
- Inadequate Design Considerations:
- Challenge: Insufficient consideration of casting-specific design requirements can result in improper gating and riser design, uneven cooling, or insufficient material flow.
- Best Practices: Involve casting engineers early in the design phase to optimize part geometry, wall thickness, fillets, and draft angles. Design efficient gating systems, risers, and cooling channels to facilitate proper metal flow, minimize defects, and ensure uniform solidification.
- Poor Mold Preparation:
- Challenge: Improper mold preparation, such as inadequate mold coating, insufficient mold drying, or inadequate venting, can lead to defects like surface roughness, metal/mold interaction, or gas porosity.
- Best Practices: Implement rigorous mold preparation procedures, including proper cleaning, coating, and drying techniques. Ensure adequate venting to allow for gas escape. Regularly inspect and maintain molds to prevent erosion or degradation.
- Material and Process Quality Control:
- Challenge: Inconsistent material quality, variations in alloy composition, or inadequate quality control during the casting process can contribute to defects.
- Best Practices: Establish strict material specifications, work with reputable suppliers, and perform regular material testing. Implement quality control measures, including inspection and testing protocols, to identify potential material issues and process deviations.
- Inadequate Inspection and Testing:
- Challenge: Insufficient or ineffective inspection and testing procedures may result in undetected defects, leading to compromised product quality.
- Best Practices: Implement a comprehensive inspection and testing plan, including visual inspection, non-destructive testing (NDT), and dimensional analysis. Utilize advanced techniques like CT scanning, ultrasonic testing, or 3D scanning for more accurate defect detection. Regularly review and update inspection procedures to ensure effectiveness.
- Lack of Continuous Improvement:
- Challenge: Failing to identify and address root causes of defects can hinder ongoing quality improvement efforts.
- Best Practices: Foster a culture of continuous improvement by establishing cross-functional teams, conducting regular defect analysis, and implementing corrective and preventive actions (CAPA). Utilize tools such as root cause analysis (RCA), Six Sigma, or lean manufacturing techniques to drive defect prevention and process optimization.
- Collaboration with Suppliers:
- Challenge: Insufficient collaboration and communication with material suppliers, tooling manufacturers, or casting service providers can lead to quality issues.
- Best Practices: Foster strong relationships with suppliers, ensure clear communication of quality requirements, and provide feedback on material or tooling performance. Collaborate closely with casting service providers, sharing best practices and participating in joint problem-solving efforts.
Implementing these best practices requires a proactive approach, consistent monitoring, and a commitment to quality throughout the casting process. Regular audits, process performance metrics, and feedback loops should be established to ensure continuous quality improvement and defect prevention.