Investment casting is a versatile manufacturing process used to create complex metal parts with high dimensional accuracy and excellent surface finish. While this process is highly regarded for producing intricate components, optimizing it for enhanced durability and cost efficiency remains a key focus for manufacturers. This article explores various strategies and technologies that can be employed to achieve these goals.
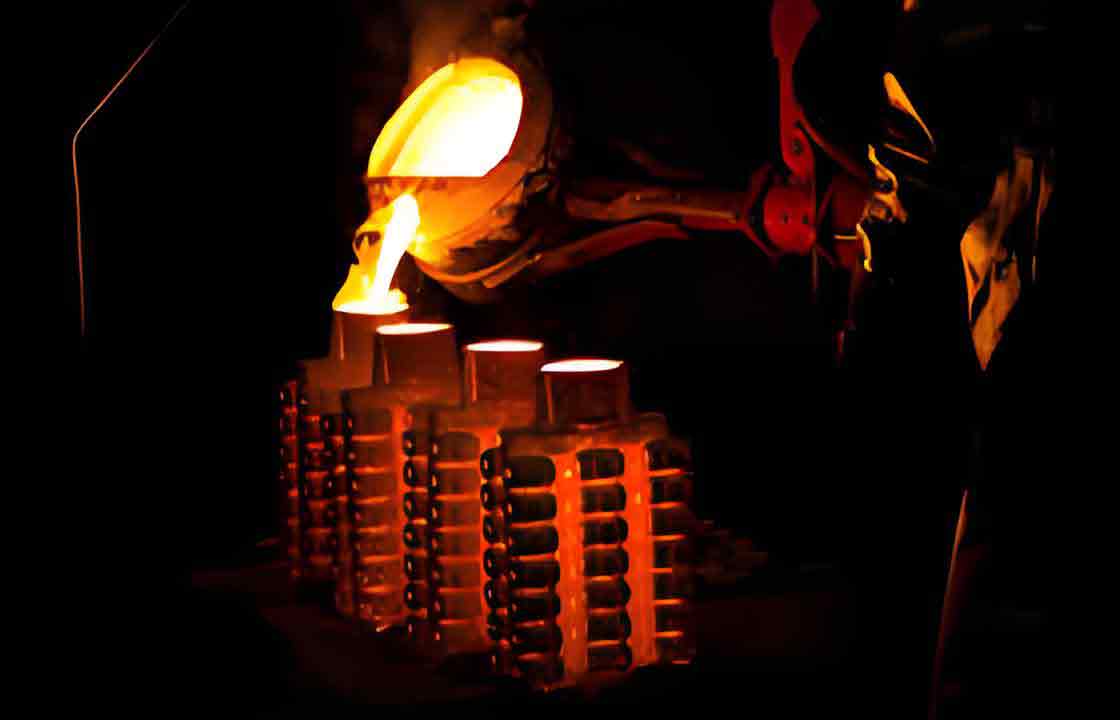
Introduction
Investment casting involves creating a wax pattern, coating it with a ceramic shell, and then melting the wax to leave a cavity for molten metal. This process allows for the production of components with intricate geometries and fine details. However, the challenges of achieving both enhanced durability and cost efficiency require a deep understanding of materials, processes, and technological advancements.
Key Strategies for Optimization
- Material Selection and Alloy Optimization
- Advanced Pattern Making Techniques
- Improved Mold Materials and Coatings
- Process Automation and Control
- Heat Treatment Optimization
- Lean Manufacturing and Waste Reduction
Material Selection and Alloy Optimization
Key Points:
- High-Performance Alloys: Utilizing alloys that offer superior mechanical properties and corrosion resistance.
- Alloy Composition: Optimizing the composition of alloys to enhance durability without significantly increasing costs.
Benefits:
- Increased component lifespan and performance.
- Reduced material costs through efficient use of alloys.
Advanced Pattern Making Techniques
Key Points:
- 3D Printing: Employing 3D printing for creating highly detailed and precise wax patterns.
- Hybrid Methods: Combining traditional and modern pattern-making techniques for better accuracy and efficiency.
Benefits:
- Enhanced precision and complexity in designs.
- Faster turnaround times and reduced prototyping costs.
Improved Mold Materials and Coatings
Key Points:
- High-Temperature Ceramics: Using advanced ceramic materials that can withstand higher temperatures and provide better surface finishes.
- Refractory Coatings: Applying high-quality refractory coatings to improve mold stability and surface integrity.
Benefits:
- Improved mold durability and reduced defects.
- Enhanced surface finish of cast components.
Process Automation and Control
Key Points:
- Robotics and Automation: Integrating robotics for repetitive tasks such as mold handling and metal pouring.
- Real-Time Monitoring: Utilizing IoT and sensor technologies for real-time process monitoring and control.
Benefits:
- Increased production efficiency and consistency.
- Reduced labor costs and human error.
Heat Treatment Optimization
Key Points:
- Controlled Cooling: Implementing precise cooling methods to enhance mechanical properties and reduce residual stresses.
- Advanced Heat Treatments: Using specialized heat treatments to improve toughness, strength, and wear resistance.
Benefits:
- Enhanced durability and performance of cast components.
- Reduced likelihood of defects and failures.
Lean Manufacturing and Waste Reduction
Key Points:
- Lean Principles: Applying lean manufacturing techniques to streamline processes and eliminate waste.
- Recycling and Reuse: Implementing systems for recycling and reusing materials to reduce costs.
Benefits:
- Lower production costs and environmental impact.
- Increased efficiency and productivity.
Comparative Table: Traditional vs. Optimized Investment Casting
Aspect | Traditional Investment Casting | Optimized Investment Casting |
---|---|---|
Material Selection | Standard alloys | High-performance, optimized alloys |
Pattern Making | Manual or basic methods | Advanced 3D printing and hybrid techniques |
Mold Materials | Conventional ceramics | High-temperature ceramics and advanced coatings |
Process Control | Manual monitoring | Automated with real-time monitoring |
Heat Treatment | Standard methods | Optimized and controlled cooling/heat treatments |
Waste Management | Basic waste disposal | Lean manufacturing and recycling |
Detailed Analysis
Material Selection and Alloy Optimization
Choosing the right materials is crucial for enhancing the durability and cost efficiency of investment casting. High-performance alloys such as superalloys, titanium, and stainless steels offer excellent mechanical properties and corrosion resistance. By optimizing alloy compositions, manufacturers can achieve the desired properties while minimizing material costs. Research into new alloy formulations can also provide significant performance improvements.
Advanced Pattern Making Techniques
The use of 3D printing in pattern making allows for the creation of highly detailed and precise wax models. This technology enables complex geometries and fine details that are difficult to achieve with traditional methods. Combining 3D printing with conventional techniques can further enhance accuracy and efficiency, reducing the time and cost of prototyping.
Improved Mold Materials and Coatings
Advancements in mold materials and coatings play a significant role in improving the quality and durability of cast components. High-temperature ceramics can withstand the intense heat of molten metal, reducing the risk of mold failure. High-quality refractory coatings ensure that the mold surface remains intact, resulting in a smoother finish and fewer defects in the final product.
Process Automation and Control
Automation and real-time process control are essential for achieving consistent quality and high efficiency in investment casting. Robotics can handle repetitive and hazardous tasks, reducing the risk of human error and increasing production speed. IoT and sensor technologies provide real-time data on various process parameters, enabling immediate adjustments and ensuring optimal conditions.
Heat Treatment Optimization
Optimized heat treatment processes are vital for enhancing the mechanical properties of cast components. Controlled cooling methods help to minimize residual stresses and improve toughness and strength. Advanced heat treatments, such as vacuum heat treating and cryogenic treatments, can significantly enhance the durability and performance of the final product.
Lean Manufacturing and Waste Reduction
Applying lean manufacturing principles helps to streamline production processes and eliminate waste. Techniques such as just-in-time (JIT) production, value stream mapping, and continuous improvement can increase efficiency and reduce costs. Implementing recycling systems for wax, ceramic materials, and scrap metal further reduces waste and lowers production costs.
Practical Applications and Case Studies
Aerospace Industry
In the aerospace industry, investment casting is used to produce high-performance components such as turbine blades and structural parts. Optimizing the casting process has led to significant improvements in the durability and efficiency of these parts.
Case Study:
- Turbine Blades: By using high-performance alloys and advanced heat treatments, manufacturers have produced turbine blades with superior strength and thermal resistance, extending their service life and reducing maintenance costs.
Automotive Industry
Investment casting is widely used in the automotive industry for producing complex components like engine parts and transmission housings. Process optimization has resulted in cost savings and improved part performance.
Case Study:
- Engine Components: The integration of 3D printing for pattern making and automated process control has led to the production of highly precise and durable engine components, reducing manufacturing costs and improving fuel efficiency.
Medical Devices
The medical device industry relies on investment casting for producing precision parts such as implants and surgical instruments. Enhancing the casting process has improved the quality and reliability of these critical components.
Case Study:
- Surgical Instruments: By implementing real-time process monitoring and using advanced materials, manufacturers have produced surgical instruments with improved durability and precision, enhancing patient safety and outcomes.
Future Trends and Research
- Artificial Intelligence (AI) Integration
- Advanced Materials Development
- Sustainable Casting Practices
- Digital Twin Technology
Artificial Intelligence (AI) Integration
Trend:
- AI and machine learning algorithms are being developed to predict casting defects and optimize process parameters in real-time.
Impact:
- Enhanced process control and reduced defect rates.
- Continuous improvement and innovation in casting techniques.
Advanced Materials Development
Trend:
- Ongoing research into new alloys and ceramic materials that offer better performance and lower costs.
Impact:
- Improved material properties and expanded application range.
- Cost-effective production of high-performance components.
Sustainable Casting Practices
Trend:
- Increasing focus on sustainability through the use of eco-friendly materials and energy-efficient processes.
Impact:
- Reduced environmental impact and compliance with regulations.
- Enhanced brand reputation and customer satisfaction.
Digital Twin Technology
Trend:
- The development of digital twins for investment casting processes, enabling virtual simulations and optimizations.
Impact:
- Greater predictability and control over casting outcomes.
- Faster development cycles and reduced time-to-market.
Conclusion
Optimizing investment casting processes for enhanced durability and cost efficiency involves a multifaceted approach that includes material selection, advanced pattern making, improved mold materials, process automation, heat treatment optimization, and lean manufacturing techniques. By embracing these strategies and staying abreast of emerging trends and technologies, manufacturers can produce high-quality components more efficiently and cost-effectively. The future of investment casting looks promising, with ongoing innovations poised to further elevate the capabilities and applications of this versatile manufacturing process.