1. Introduction
In the automotive engine manufacturing industry, the continuous improvement of engine performance has led to more complex inner cavity structures of cylinder heads. These complex structures bring challenges to the casting process, especially in terms of cavity cleanliness and the occurrence of sintering defects. This article focuses on a specific cylinder head with a complex inner cavity structure in Yuchai Foundry and how casting CAE sand shooting simulation is used to address the sintering casting defects.
1.1 Background of Engine Cylinder Head Casting
With the upgrading of automotive engines and the increasing demand for comprehensive performance, higher requirements are imposed on the cleanliness of the inner cavities of engine cylinder blocks and heads. The complex inner cavity structures of cylinder heads, such as integrated injector sleeves, valve guides, middle baffle structures, and double-layer water jacket structures, enhance the overall water flow field and cooling effect. However, these changes also increase the casting difficulty and demand for more advanced casting process technology and quality control.
1.2 Problem of Sintering Defects in the Cylinder Head
The cylinder head in question has a complex inner cavity structure. The water jacket sand core is produced using the cold box resin sand process. The sintering defect ratio in the casting is as high as 20% or more, mainly occurring in the area around the injector holes of the cylinder head. The corresponding sand core structure is slender, with a minimum width of 3 – 4 mm. The sintering defects not only affect the cleanliness of the inner cavity of the cylinder head but also may lead to engine reliability reduction and casting scrap, causing significant hidden dangers and cost losses in product quality and manufacturing.
1.3 Significance of Using CAE Simulation
Casting CAE sand shooting simulation software provides a powerful tool for analyzing and solving casting problems. By simulating the sand shooting process, it is possible to identify the areas with insufficient sand density and non-compactness in the sand core, understand the flow behavior of the core sand, and evaluate the effects of different process parameters and mold designs. This helps to optimize the mold design, improve the quality of the sand core, and ultimately solve the sintering defect problem without increasing production costs significantly.
2. Sand Shooting Simulation Process
2.1 Sand Shooting Parameter Settings
The water jacket sand core is exported as a process model for sand shooting simulation calculation according to the actual specifications and quantities of the nozzles and exhaust plugs on the mold. The STL format file is then imported into the geometric model processing interface of the sand shooting simulation software. After adjusting the direction, defining the material groups of each element, and ensuring that there are no missing elements, the process enters the finite element mesh generation interface.
Parameter | Setting Value |
---|---|
Sand Shooting Pressure | [Actual Value] |
Sand Shooting Time | [Actual Value] |
Exhaust Area | [Calculated Value] |
Sand Core Material | [Specified Material] |
2.2 Sand Shooting Simulation Calculation and Problem Analysis
After setting the sand shooting parameters according to the actual production situation, the sand shooting simulation calculation is carried out. The analysis of the sand density in different regions of the water jacket sand core shows that the sand density in the area corresponding to the injector holes of the cylinder head is relatively low, only 1.39 g/cm³, which does not meet the requirement of 1.48 g/cm³ after sand shooting. This indicates that there is insufficient or non-compact sand shooting in this area, which is the main cause of the sintering problem in the casting cavity.
Region | Sand Density (g/cm³) | Problem Description |
---|---|---|
Injector Hole Region | 1.39 | Low sand density, non-compact |
Other Regions | [Higher Values] | Relatively better sand density |
The analysis of the sand shooting simulation results also reveals that the 不合理 arrangement of the nozzles in the injector hole area leads to uneven sand shooting volume and turbulent flow of the core sand, which is not conducive to the filling of the core sand. In addition, the inappropriate selection of the nozzle specifications results in either too small or too large sand volume, further contributing to the low sand density in the injector hole area.
Nozzle Problem | Impact |
---|---|
Uneven Arrangement | Uneven sand shooting volume |
Inappropriate Specification | Too small or large sand volume |
2.3 Process Optimization and Sand Shooting Simulation Calculation
2.3.1 Optimization of Nozzle Arrangement and Specification
Based on the structure and shape of the sand core, the injector hole area of the water jacket sand core is divided into different parts according to the structure weight. By analyzing the empirical relationship between the nozzle specification and the effective sand shooting weight, the nozzle specifications in different positions are optimized to improve the compactness and density of the sand core after sand shooting.
Region | Original Nozzle Specification | Optimized Nozzle Specification |
---|---|---|
Injector Hole Region 1 | [Old Size] | [New Size] |
Injector Hole Region 2 | [Old Size] | [New Size] |
2.3.2 Optimization of Exhaust Plug Arrangement and Specification
The exhaust plug plays a crucial role in the sand shooting process. The appropriate selection and arrangement of the exhaust plug can ensure the smooth discharge of gas during sand shooting and the full curing of the core sand. Based on the analysis of the relationship between the exhaust area and the inlet area, and considering the characteristics of the cold box process, the exhaust plug specifications in the injector hole area are optimized.
Region | Original Exhaust Plug Specification | Optimized Exhaust Plug Specification |
---|---|---|
Injector Hole Region 1 | [Old Type and Size] | [New Type and Size] |
Injector Hole Region 2 | [Old Type and Size] | [New Type and Size] |
2.3.3 Effect of Optimized Sand Shooting Simulation Calculation
After optimizing the nozzle and exhaust plug settings, the sand shooting simulation calculation is carried out again. The results show that the sand density in the sintering corresponding area of the injector hole is increased to 1.44 g/cm³, and the compactness and density of the sand core are improved. The sand shooting volume of each nozzle is more balanced, and the exhaust effect is also enhanced.
Parameter | Before Optimization | After Optimization |
---|---|---|
Sand Density in Injector Hole Region (g/cm³) | 1.39 | 1.44 |
Compactness of Sand Core | Low | Improved |
Sand Shooting Volume Balance | Poor | Good |
3. Production Verification
After the optimization of the nozzle and exhaust plug settings on the mold, the sand shooting effect is verified. The sand core in the injector hole sintering corresponding area is formed completely, with a smooth surface and compact structure. The casting cavity has no sand sticking, and the injector hole area has no sintering and is easy to clean, indicating that the optimization measures are effective.
Verification Item | Result |
---|---|
Sand Core Quality | Good |
Casting Cavity Cleanliness | No Sand Sticking |
Injector Hole Area | No Sintering |
4. Conclusion and Outlook
4.1 Summary of Achievements
In this study, casting CAE sand shooting simulation was successfully applied to solve the sintering casting defects of the complex inner cavity structure cylinder head. By analyzing the sand shooting simulation results, optimizing the nozzle and exhaust plug settings, and conducting production verification, the sand density and compactness of the sand core in the injector hole area were effectively improved, and the sintering and sand sticking problems in the casting cavity were solved.
4.2 Significance and Value
This research not only provides a practical solution for improving the casting quality of cylinder heads but also forms an experience method and process design specification for solving casting cavity cleanliness problems. It can effectively guide the actual production process and help solve similar quality problems caused by loose sand cores and insufficient compactness.
4.3 Future Research Directions
In the future, further research can be carried out in the following aspects: exploring more accurate simulation models and algorithms to improve the accuracy of simulation results; studying the influence of different core sand materials and additives on the sand shooting process and casting quality; and applying advanced manufacturing technologies and materials to optimize the design and manufacturing process of cylinder head molds.
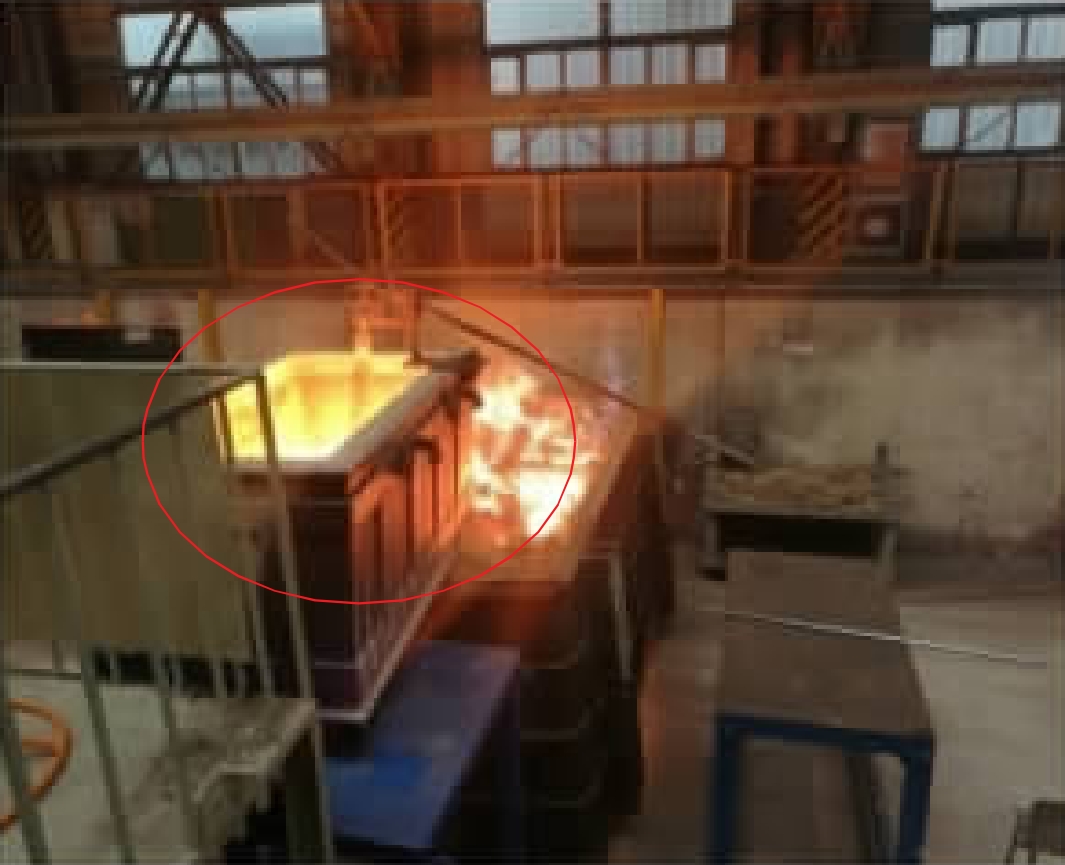