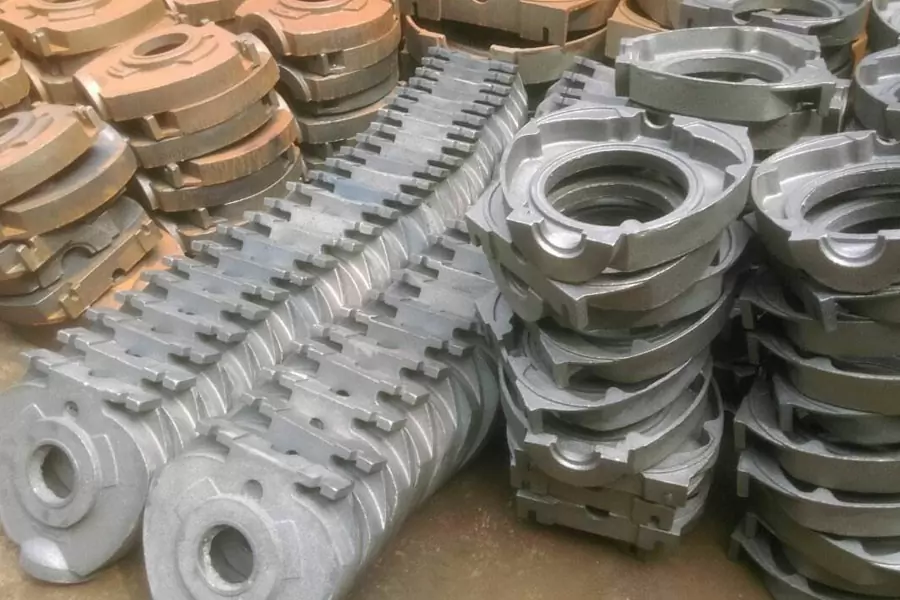
Optimizing sand casting services for complex geometries in modern manufacturing involves several key strategies and technologies. Here are some important aspects to consider:
1. Advanced Pattern Design:
- CAD and Simulation Software: Utilize advanced computer-aided design (CAD) and simulation software to design and analyze patterns for complex geometries. This helps in predicting potential issues and optimizing the design before actual sand casting services.
- 3D Printing for Patterns: Use 3D printing to create precise and intricate patterns that traditional methods might struggle with. This ensures better accuracy and complexity in the final cast parts.
2. High-Quality Sand and Binders:
- Resin-Bonded Sand: Use high-quality resin-bonded sand for improved strength and surface finish. This is particularly important for complex geometries where maintaining dimensional accuracy is crucial.
- Sand Additives: Incorporate additives in the sand to enhance its properties, such as flowability and collapsibility, which can reduce defects in complex sand casting services.
3. Optimized Mold Design:
- Modular Molds: Design modular molds that can be easily assembled and disassembled, allowing for intricate internal structures and minimizing casting defects.
- Cooling Channels: Integrate optimized cooling channels within the mold to ensure uniform cooling and reduce the likelihood of thermal stresses and deformations.
4. Simulation and Testing:
- Casting Simulation Software: Implement casting simulation software to predict potential defects such as porosity, shrinkage, and thermal stresses. This allows for adjustments in the design and process parameters before actual production.
- Virtual Prototyping: Use virtual prototyping to test and refine the sand casting services, reducing the need for physical prototypes and accelerating the development cycle.
5. Process Control and Monitoring:
- Automated Monitoring Systems: Employ automated systems for real-time monitoring of critical parameters such as temperature, pressure, and sand properties. This helps in maintaining consistency and quality in sand casting services.
- Data Analytics: Utilize data analytics to analyze historical casting data and identify patterns or trends that can lead to process improvements and defect reduction.
6. Post-Casting Treatments:
- Heat Treatment: Implement appropriate heat
treatment processes to relieve residual stresses and improve the mechanical properties of the cast parts, especially for complex geometries.
- Surface Finishing: Employ advanced surface finishing techniques such as shot blasting, machining, or polishing to achieve the desired surface quality and dimensional accuracy.
7. Quality Assurance and Inspection:
- Non-Destructive Testing (NDT): Use NDT methods such as X-ray, ultrasonic testing, and dye penetrant inspection to detect internal and surface defects without damaging the cast parts.
- Coordinate Measuring Machines (CMM): Utilize CMMs for precise measurement and verification of complex geometries to ensure they meet the required specifications.
8. Material Selection:
- Alloy Optimization: Select appropriate alloys that can accommodate the complexities of the geometry while maintaining the required mechanical properties and resistance to wear, corrosion, or other environmental factors.
- Composite Materials: Consider using composite materials where applicable to achieve a balance between weight, strength, and manufacturability.
9. Lean Manufacturing Practices:
- Waste Reduction: Implement lean manufacturing techniques to reduce waste and improve efficiency throughout the sand casting services.
- Continuous Improvement: Encourage a culture of continuous improvement where feedback from each casting run is used to make incremental improvements to the process.
10. Collaboration and Expertise:
- Cross-Functional Teams: Form cross-functional teams involving design engineers, material scientists, and manufacturing experts to collaboratively address the challenges of casting complex geometries.
- Supplier Partnerships: Partner with suppliers who specialize in high-quality sand, binders, and other materials to ensure consistent and reliable input materials for sand casting services.
By integrating these strategies, modern manufacturers can optimize their sand casting services to effectively produce complex geometries with high precision, quality, and efficiency.